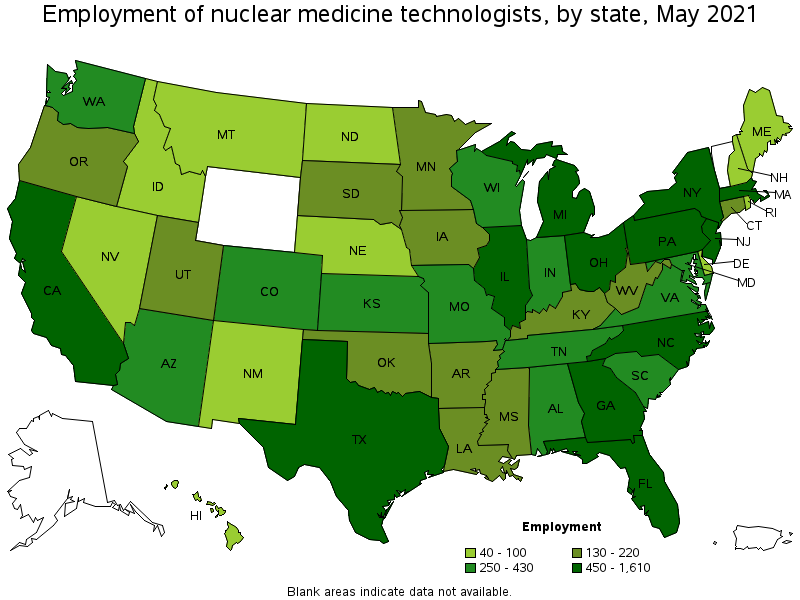
The United States is the third largest country manufacturer in the entire world. Its manufacturing output was almost double that of the Great Recession. The United States' manufacturing sector is not taking the right approach to its challenges despite a strong economy. This could be due to a shortage of skilled labor or investment, but we must be more aggressive in dealing with the problems facing our industry.
Jobs have declined by 5 million since 2000
Five million US manufacturing jobs have been lost since 2000. Some claim that the rise of trade with China is to blame. However, only about a quarter the decline in manufacturing jobs can be attributed to this. Other than trade with China and the loss of manufacturing jobs in local markets, which aren't able to compete with Chinese imports, But there are many factors that contributed to the decline of manufacturing jobs. The following are some of the reasons:
Over the past two decades, almost a third have been lost in US manufacturing. It was 17,000,000 in 1965. It dropped to just 12,000,000 in 2010. While the decline in manufacturing jobs is not the fault of trade, it has been the result of structural problems - a decline in capital investment, output, productivity, and trade deficits - which are not sustainable. Although productivity gains had a large role in the decline in manufacturing jobs, they weren't enough. Not productivity gains, but automation is the problem.
Strong demand is for manufactured products
The United States has a strong demand for manufactured products despite the fact that consumer spending on these goods has fallen over the past several decades. In 1945, personal consumption of durable goods accounted to 58%, compared today to 28%. This is because the cost of manufacturing and sale of these goods has dropped while the content has increased. The result is that computers, televisions and sound equipment have fallen in price.
The US has seen a rise in manufacturing activity, which has led to an increase in production. According to the Fifth District Manufacturing Activity Survey, demand is high for manufactured goods and production is increasing. However, supply chain bottlenecks are limiting output. Increased production has put pressure on supply chains. Many respondents reported experiencing supply chain disruptions that have affected their ability to keep necessary inventories. Backlogs have increased as well, and vendors lead times have been longer.
Trade deficit in manufactured goods has more than doubled in the past decade
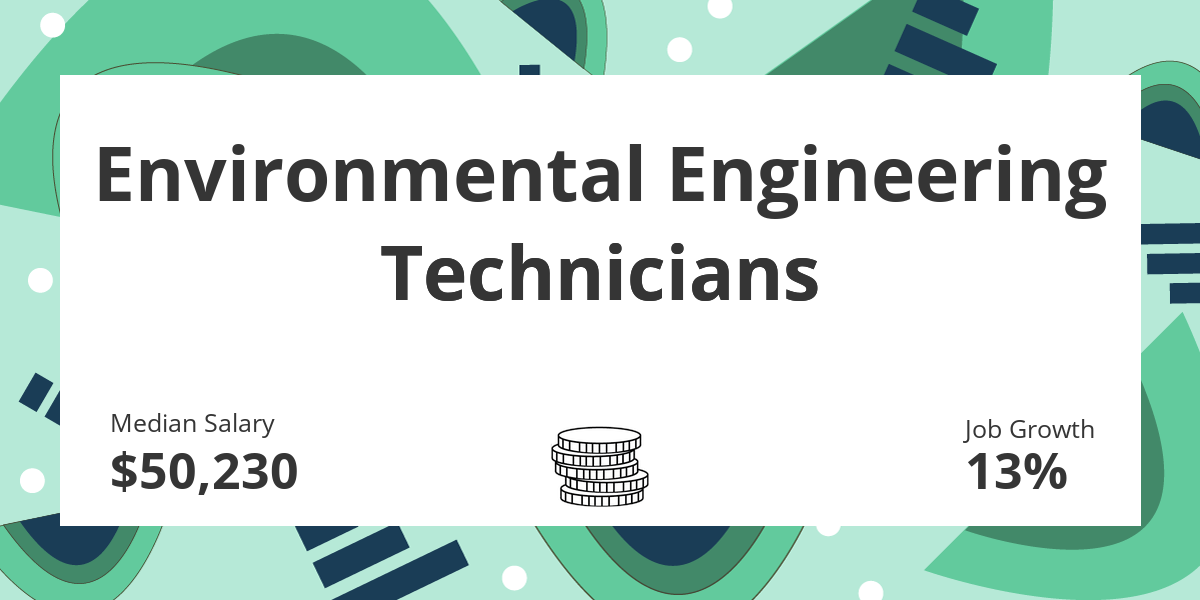
Economists worry that the U.S. will have a lower level of global growth and cause more instability among its trading counterparts. However, high imports from the USA of manufactured goods is not necessarily a problem for the U.S. economy. It is crucial to maintaining economic stability worldwide. A trade deficit might even be necessary, as the U.S. heavily relies on foreign markets for its economic output. However, high levels of foreign demand could make it more difficult to reach full employment.
Since 2000, the U.S. manufactured goods trade deficit has almost doubled. The US deficit has been growing partly because of the increase in Chinese imports. But the larger problem is that this imbalance is concentrated in the manufacturing sector, where wages and employment have decreased since the 1990s. The result is that US manufacturing employment has dropped dramatically from 26 percent of 1970 to 8.5% in 2016. Some economists attribute the decline in manufacturing employment to China's increased level of competition. However, most economists attribute the decline primarily to automation, productivity growth, and shifting demand from goods towards services.
Industry adopts a shotgun approach
The US manufacturing industry is well-respected for its advanced manufacturing efforts and has many other initiatives. However, some countries have chosen to bring the internet of everything into manufacturing. The US, on other hand, is focused on different technologies and blends traditional mass media with Internet advertisement. The result is a shotgun approach, where companies focus on many different technologies and aim for a broad customer base.
FAQ
How can overproduction in manufacturing be reduced?
The key to reducing overproduction lies in developing better ways to manage inventory. This would reduce time spent on activities such as purchasing, stocking, and maintaining excess stock. We could use these resources to do other productive tasks.
A Kanban system is one way to achieve this. A Kanban Board is a visual display that tracks work progress. In a Kanban system, work items move through a sequence of states until they reach their final destination. Each state is assigned a different priority.
To illustrate, work can move from one stage or another when it is complete enough for it to be moved to a new stage. However, if a task is still at the beginning stages, it will remain so until it reaches the end of the process.
This allows you to keep work moving along while making sure that no work gets neglected. Managers can view the Kanban board to see how much work they have done. This data allows them adjust their workflow based upon real-time data.
Lean manufacturing can also be used to reduce inventory levels. Lean manufacturing seeks to eliminate waste from every step of the production cycle. Anything that does not contribute to the product's value is considered waste. The following are examples of common waste types:
-
Overproduction
-
Inventory
-
Unnecessary packaging
-
Exceed materials
By implementing these ideas, manufacturers can improve efficiency and cut costs.
What is the distinction between Production Planning or Scheduling?
Production Planning (PP), is the process of deciding what production needs to take place at any given time. This is accomplished by forecasting the demand and identifying production resources.
Scheduling refers the process by which tasks are assigned dates so that they can all be completed within the given timeframe.
What are the 4 types manufacturing?
Manufacturing is the process that transforms raw materials into useful products. Manufacturing can include many activities such as designing and building, testing, packaging shipping, selling, servicing, and other related activities.
What does warehouse mean?
A warehouse or storage facility is where goods are stored before they are sold. You can have it indoors or outdoors. In some cases, it may be a combination of both.
Is it possible to automate certain parts of manufacturing
Yes! Yes. Automation has been around since ancient time. The Egyptians invent the wheel thousands of year ago. To help us build assembly lines, we now have robots.
There are many applications for robotics in manufacturing today. These include:
-
Robots for assembly line
-
Robot welding
-
Robot painting
-
Robotics inspection
-
Robots that create products
Manufacturing could also benefit from automation in other ways. For instance, 3D printing allows us make custom products and not have to wait for months or even weeks to get them made.
What is the role of a manager in manufacturing?
A manufacturing manager must make sure that all manufacturing processes run smoothly and effectively. They should also be aware of any problems within the company and act accordingly.
They should also be able and comfortable communicating with other departments like sales and marketing.
They should be up to date on the latest trends and be able apply this knowledge to increase productivity and efficiency.
Statistics
- Many factories witnessed a 30% increase in output due to the shift to electric motors. (en.wikipedia.org)
- [54][55] These are the top 50 countries by the total value of manufacturing output in US dollars for its noted year according to World Bank.[56] (en.wikipedia.org)
- According to the United Nations Industrial Development Organization (UNIDO), China is the top manufacturer worldwide by 2019 output, producing 28.7% of the total global manufacturing output, followed by the United States, Japan, Germany, and India.[52][53] (en.wikipedia.org)
- You can multiply the result by 100 to get the total percent of monthly overhead. (investopedia.com)
- (2:04) MTO is a production technique wherein products are customized according to customer specifications, and production only starts after an order is received. (oracle.com)
External Links
How To
How to Use Just-In-Time Production
Just-intime (JIT), a method used to lower costs and improve efficiency in business processes, is called just-in-time. It allows you to get the right amount resources at the right time. This means that your only pay for the resources you actually use. Frederick Taylor developed the concept while working as foreman in early 1900s. He saw how overtime was paid to workers for work that was delayed. He decided to ensure workers have enough time to do their jobs before starting work to improve productivity.
The idea behind JIT is that you should plan ahead and have everything ready so you don't waste money. Also, you should look at the whole project from start-to-finish and make sure you have the resources necessary to address any issues. You'll be prepared to handle any potential problems if you know in advance. You won't have to pay more for unnecessary items.
There are many JIT methods.
-
Demand-driven JIT: This is a JIT that allows you to regularly order the parts/materials necessary for your project. This will allow to track how much material has been used up. This will let you know how long it will be to produce more.
-
Inventory-based: This type allows you to stock the materials needed for your projects ahead of time. This allows one to predict how much they will sell.
-
Project-driven : This is a method where you make sure that enough money is set aside to pay the project's cost. If you know the amount you require, you can buy the materials you need.
-
Resource-based JIT is the most widespread form. You allocate resources based on the demand. For instance, if you have a lot of orders coming in, you'll assign more people to handle them. You'll have fewer orders if you have fewer.
-
Cost-based: This is the same as resource-based except that you don't care how many people there are but how much each one of them costs.
-
Price-based: This is similar to cost-based but instead of looking at individual workers' salaries, you look at the total company price.
-
Material-based: This approach is similar to cost-based. However, instead of looking at the total cost for the company, you look at how much you spend on average on raw materials.
-
Time-based JIT: This is another variant of resource-based JIT. Instead of focusing on how much each employee costs, you focus on how long it takes to complete the project.
-
Quality-based JIT - This is another form of resource-based JIT. Instead of looking at the labor costs and time it takes to make a product, think about its quality.
-
Value-based: This is one of the newest forms of JIT. This is where you don't care about how the products perform or whether they meet customers' expectations. Instead, you're focused on how much value you add to the market.
-
Stock-based: This inventory-based approach focuses on how many items are being produced at any one time. It is used when production goals are met while inventory is kept to a minimum.
-
Just-in-time planning (JIT): This is a combination JIT and supply-chain management. It is the process that schedules the delivery of components within a short time of their order. It reduces lead times and improves throughput.