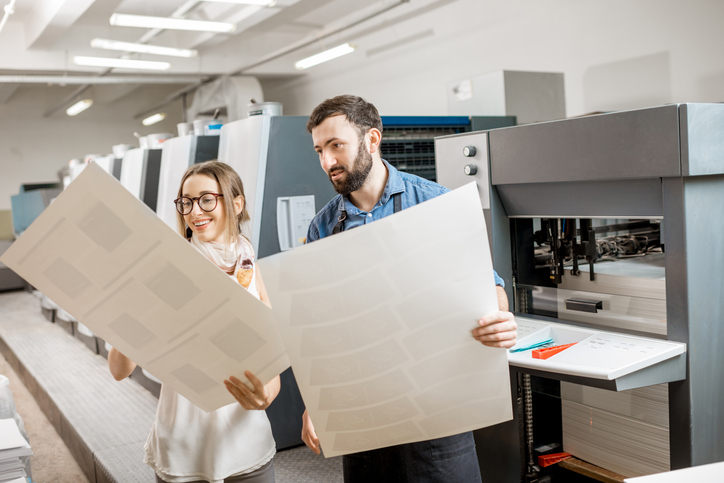
Your location and your specialization will affect the salary of a material engineering engineer. Some of the highest paying companies include Apple, ConocoPhillips, Meta and Western Digital. You might also find great opportunities at FedEx and Motorola Solutions for material engineers.
Materials engineers need knowledge of the relationship between materials, and their processing methods. They need to be able pinpoint the reasons for failures. Additionally, they should be able explain engineering concepts to non engineers. They are responsible for developing and implementing cost-efficient operations strategies. They may also need to communicate with suppliers and other professionals. They might also need to travel to different countries to collect samples. In some cases they may have to work for more than 40 hours per week.
Materials engineers could also obtain advanced degrees. They may be eligible for a PhD. They might also be eligible to teach or do research. Senior material engineers can assume more management responsibilities. They might also have the opportunity for innovative research.
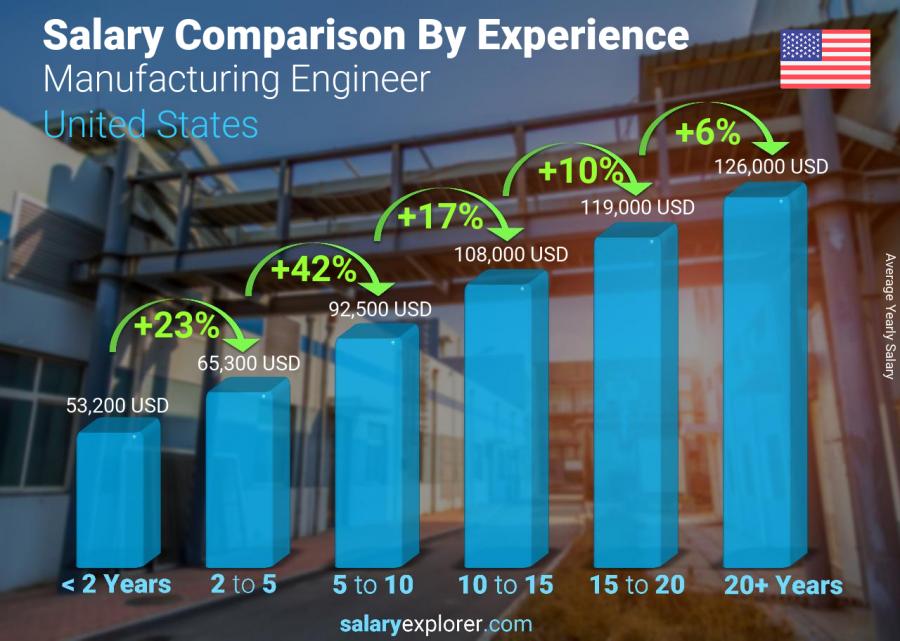
Materials engineers could work in factories or offices. They might also travel to other sites to collect samples to test. The field is also very competitive, so it is important to stay on top of industry trends and innovations. They may also need to establish relationships with clients. They can assist product engineers in implementing green practices and improving their products. They may also be able build a strong reputation within their field.
Materials engineers could also work in laboratories. For troubleshooting and design, they may be proficient in advanced math topics. They may also need the ability to clearly communicate engineering concepts. They may also be required to travel to other countries to collect samples, or to observe the use of materials in a manufacturing plant.
Technology companies such as FedEx and Apple often hire materials engineers. Raytheon Technologies, which manufactures metals and other material, may employ them. This field is very competitive, so it may be difficult to land a job with these companies. It is also possible to become a material engineer through engineering consulting firms. You may also have the opportunity to start your own business, which will allow you to stay at the forefront of your industry.
Long hours may be required for materials engineers. They might be required to travel long distances to obtain samples for testing or to observe the process of manufacturing materials. If they work as material engineers in factories, they might be required to work longer hours. Because of this, they will need to be able to work hard.
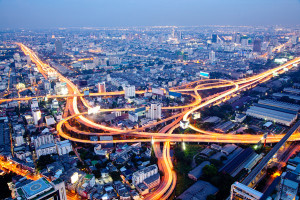
Material engineers will often need to work together as part of a team. They may be required to communicate with suppliers, clients, and other professionals. They could also be responsible to make sure deadlines are met and budgets are met.
FAQ
How can manufacturing reduce production bottlenecks?
Avoiding production bottlenecks is as simple as keeping all processes running smoothly, from the time an order is received until the product ships.
This includes planning for both capacity requirements and quality control measures.
Continuous improvement techniques like Six Sigma are the best way to achieve this.
Six Sigma is a management method that helps to improve quality and reduce waste.
It's all about eliminating variation and creating consistency in work.
How can manufacturing excess production be decreased?
Improved inventory management is the key to reducing overproduction. This would reduce the time needed to manage inventory. We could use these resources to do other productive tasks.
One way to do this is to adopt a Kanban system. A Kanban Board is a visual display that tracks work progress. Work items are moved through various states to reach their destination in a Kanban system. Each state represents a different priority level.
If work is moving from one stage to the other, then the current task can be completed and moved on to the next. It is possible to keep a task in the beginning stages until it gets to the end.
This allows work to move forward and ensures that no work is missed. Managers can see how much work has been done and the status of each task at any time with a Kanban Board. This information allows them to adjust their workflow based on real-time data.
Lean manufacturing is another way to manage inventory levels. Lean manufacturing seeks to eliminate waste from every step of the production cycle. Anything that doesn't add value to the product is considered waste. The following are examples of common waste types:
-
Overproduction
-
Inventory
-
Packaging not required
-
Exceed materials
Manufacturers can reduce their costs and improve their efficiency by using these ideas.
What is production plan?
Production planning is the process of creating a plan that covers all aspects of production. This includes scheduling, budgeting and crew, location, equipment, props, and more. This document aims to ensure that everything is planned and ready when you are ready to shoot. This document should also include information on how to get the best result on set. This information includes locations, crew details and equipment requirements.
The first step in filming is to define what you want. You may have decided where to shoot or even specific locations you want to use. Once you've identified the locations and scenes you want to use, you can begin to plan what elements you need for each scene. One example is if you are unsure of the exact model you want but decide that you require a car. This is where you can look up car models online and narrow down your options by choosing from different makes and models.
Once you have found the right car, you can start thinking about extras. You might need to have people in the front seats. Perhaps you have someone who needs to be able to walk around the back of your car. You might want to change your interior color from black and white. These questions will help to determine the style and feel of your car. Also, think about what kind of shots you would like to capture. Will you be filming close-ups or wide angles? Maybe you want to show your engine or the steering wheel. This will allow you to determine the type of car you want.
Once you have determined all of the above, you can move on to creating a schedule. The schedule will show you when to begin shooting and when to stop. The schedule will show you when to get there, what time to leave, and when to return home. It will help everyone know exactly what they have to do and when. If you need to hire extra staff, you can make sure you book them in advance. It's not worth paying someone to show up if you haven't told him.
Your schedule will also have to be adjusted to reflect the number of days required to film. Some projects can be completed in a matter of days or weeks. Others may take several days. You should consider whether you will need more than one shot per week when creating your schedule. Multiplying takes in the same area will result both in increased costs and a longer time. If you are unsure if you need multiple takes, it is better to err on the side of caution and shoot fewer takes rather than risk wasting money.
Budget setting is an important part of production planning. A realistic budget will help you work within your means. You can always lower the budget if you encounter unexpected problems. However, you shouldn't overestimate the amount of money you will spend. If you underestimate the cost of something, you will have less money left after paying for other items.
Production planning is a very detailed process, but once you understand how everything works together, it becomes easier to plan future projects.
What does warehouse mean?
A warehouse or storage facility is where goods are stored before they are sold. You can have it indoors or outdoors. In some cases it could be both indoors and outdoors.
Why automate your warehouse
Modern warehousing is becoming more automated. E-commerce has brought increased demand for more efficient and quicker delivery times.
Warehouses need to adapt quickly to meet changing needs. To do so, they must invest heavily in technology. The benefits of automating warehouses are numerous. Here are some benefits of investing in automation
-
Increases throughput/productivity
-
Reduces errors
-
Increases accuracy
-
Boosts safety
-
Eliminates bottlenecks
-
This allows companies to scale easily
-
This makes workers more productive
-
Provides visibility into everything that happens in the warehouse
-
Enhances customer experience
-
Improves employee satisfaction
-
Reduces downtime and improves uptime
-
Quality products delivered on time
-
Human error can be eliminated
-
Assure compliance with regulations
What are the 4 types of manufacturing?
Manufacturing is the process by which raw materials are transformed into useful products through machines and processes. It can involve many activities like designing, manufacturing, testing packaging, shipping, selling and servicing.
Statistics
- Job #1 is delivering the ordered product according to specifications: color, size, brand, and quantity. (netsuite.com)
- It's estimated that 10.8% of the U.S. GDP in 2020 was contributed to manufacturing. (investopedia.com)
- In the United States, for example, manufacturing makes up 15% of the economic output. (twi-global.com)
- [54][55] These are the top 50 countries by the total value of manufacturing output in US dollars for its noted year according to World Bank.[56] (en.wikipedia.org)
- According to the United Nations Industrial Development Organization (UNIDO), China is the top manufacturer worldwide by 2019 output, producing 28.7% of the total global manufacturing output, followed by the United States, Japan, Germany, and India.[52][53] (en.wikipedia.org)
External Links
How To
Six Sigma and Manufacturing
Six Sigma is defined as "the application of statistical process control (SPC) techniques to achieve continuous improvement." Motorola's Quality Improvement Department, Tokyo, Japan, developed it in 1986. The basic idea behind Six Sigma is to improve quality by improving processes through standardization and eliminating defects. In recent years, many companies have adopted this method because they believe there is no such thing as perfect products or services. Six Sigma's main objective is to reduce variations from the production average. You can calculate the percentage of deviation from the norm by taking a sample of your product and comparing it to the average. If it is too large, it means that there are problems.
Understanding the dynamics of variability within your business is the first step in Six Sigma. Once you have a good understanding of the basics, you can identify potential sources of variation. Also, you will need to identify the sources of variation. Random variations are caused by human errors. Systematic variations can be caused by outside factors. Random variations would include, for example, the failure of some widgets to fall from the assembly line. But if you notice that every widget you make falls apart at the exact same place each time, this would indicate that there is a problem.
Once you identify the problem areas, it is time to create solutions. It might mean changing the way you do business or redesigning it entirely. Test them again once you've implemented the changes. If they don't work you need to rework them and come up a better plan.