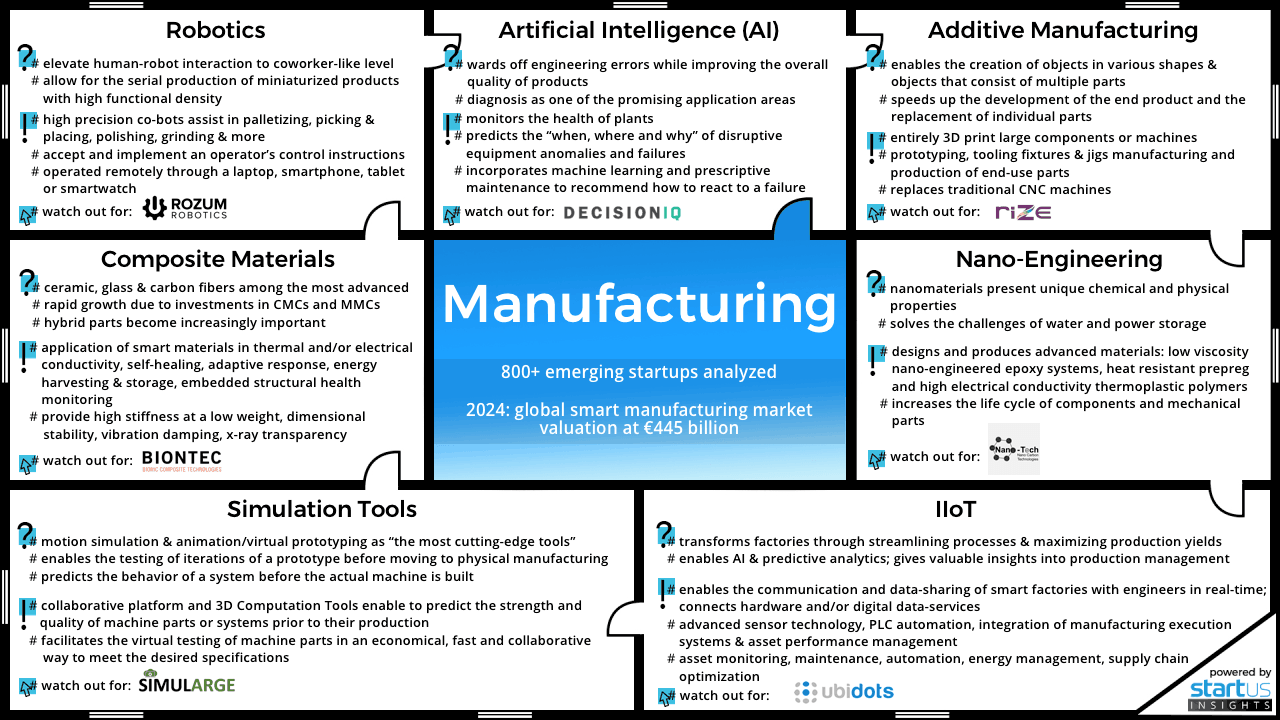
During the Great Recession, Ohio manufacturers lost a total of 166,000 manufacturing jobs. While the manufacturing sector in Ohio has rebounded, it has been slower than other states. Ohio's manufacturing jobs are still below the level they were before the recession.
Ohio's drop in manufacturing jobs is due largely to the rise of European and Japanese manufacturing competition. Manufacturers have had the opportunity to become more technologically sophisticated and to reduce labor costs. Global economic conditions have been difficult, leading to job losses.
Ohio's workforce shortage is one the biggest challenges facing its manufacturers. However, the state has many programs to address the shortage of skilled labor. These initiatives are scattered and isolated and do not address the entire workforce problems facing manufacturers. The Ohio Governor's Office of Workforce Transformation released a special report about the workforce shortage. It recommended greater collaboration between businesses and educators. However, the report discovered a gap between business and school needs.
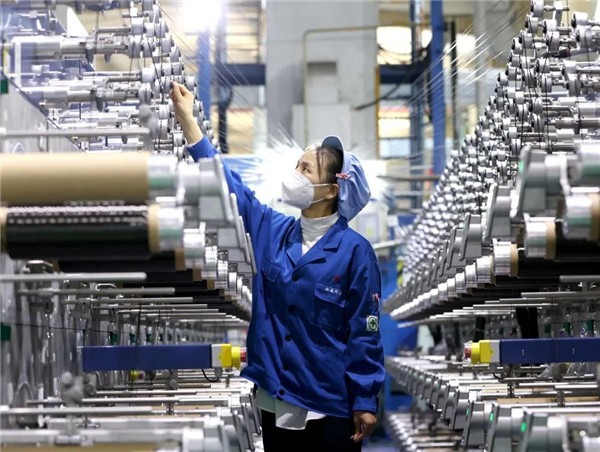
Ohio's workforce is multifaceted, complex and diverse. Manufacturing workers are less likely to be represented by a union than workers in other industries in the state. However, unionized manufacturing jobs offer solid benefits and livable wages.
Ohio's manufacturing sector contributes significantly to its economy. Utilizing interstate highways and railways as well as inland waterways, manufacturers can distribute their goods at a competitive price. The state is also a leading exporter. Private investors will also be attracted by the state's natural-gas production.
While the state has gained 50,000 manufacturing job opportunities over the past four years of his administration, Kasich's tenure in office has seen slow job gains. In Kasich's first three terms, the average manufacturing job gain was 7 percent. Manufacturing jobs have decreased by 1,771 jobs over the past two-years. These losses are caused by the slowing economy, the automobile industry, and lukewarm global demands.
Ohio is a prominent exporter. Its top export markets include the U.S.A. Canada, Mexico, Mexico, and the U.K. But, Ohio's exports have dropped by $1.4B in the past one year. Trade policy continues to be a key issue for manufacturers in Ohio. While trade policy changes might be beneficial for certain industries, it will not solve all of the problems.
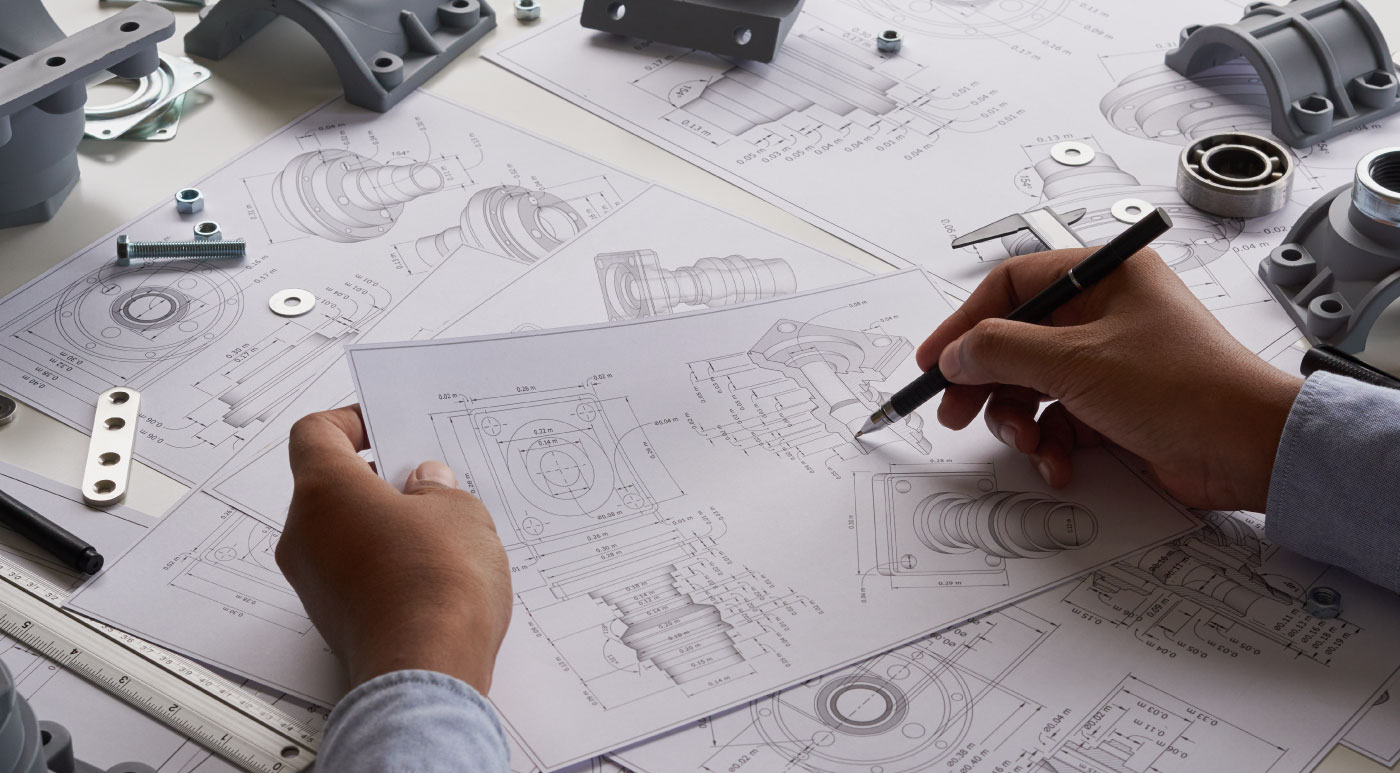
Ohio's manufacturing sector is still one of the most important. Manufacturing jobs are some of the highest paying jobs for semi-skilled workers without post-secondary education. Wages have not kept up to the pace of Ohio's production. Manufacturing jobs pay more in Ohio than any other industry, but they are not sufficient for middle-class lifestyles.
Ohio's manufacturing workforce consists of a diverse group of workers. In order to keep up with the rest, the state's manufacturing sectors have been diversifying. Ohio has become more service-oriented and manufacturing is no longer Ohio’s main employer. Manufacturers are increasingly focusing on international exposure and future-generation skills.
FAQ
What are manufacturing and logistics?
Manufacturing is the process of creating goods from raw materials by using machines and processes. Logistics covers all aspects involved in managing supply chains, including procurement and production planning. As a broad term, manufacturing and logistics often refer to both the creation and delivery of products.
Is automation important for manufacturing?
Automating is not just important for manufacturers, but also for service providers. They can provide services more quickly and efficiently thanks to automation. In addition, it helps them reduce costs by reducing human errors and improving productivity.
What are the 7 Rs of logistics management?
The 7R's of Logistics is an acronym for the seven basic principles of logistics management. It was developed and published by the International Association of Business Logisticians in 2004 as part of the "Seven Principles of Logistics Management".
The acronym is composed of the following letters.
-
Responsible - to ensure that all actions are within the legal requirements and are not detrimental to others.
-
Reliable - Have confidence in your ability to fulfill all of your commitments.
-
Use resources effectively and sparingly.
-
Realistic – Consider all aspects, including cost-effectiveness as well as environmental impact.
-
Respectful - Treat people fairly and equitably
-
Resourceful - look for opportunities to save money and increase productivity.
-
Recognizable: Provide customers with value-added service
What is meant by manufacturing industries?
Manufacturing Industries are companies that manufacture products. Consumers are people who purchase these goods. These companies use a variety processes such as distribution, retailing and management to accomplish their purpose. They make goods from raw materials with machines and other equipment. This includes all types and varieties of manufactured goods, such as food items, clothings, building supplies, furnitures, toys, electronics tools, machinery vehicles, pharmaceuticals medical devices, chemicals, among others.
What skills should a production planner have?
Production planners must be flexible, organized, and able handle multiple tasks. Effective communication with clients and colleagues is essential.
What is the role of a manager in manufacturing?
A manufacturing manager must ensure that all manufacturing processes are efficient and effective. They should be aware of any issues within the company and respond accordingly.
They should also be able communicate with other departments, such as sales or marketing.
They should also be aware of the latest trends in their industry and be able to use this information to help improve productivity and efficiency.
How does a Production Planner differ from a Project Manager?
A production planner is more involved in the planning phase of the project than a project manger.
Statistics
- Many factories witnessed a 30% increase in output due to the shift to electric motors. (en.wikipedia.org)
- In 2021, an estimated 12.1 million Americans work in the manufacturing sector.6 (investopedia.com)
- According to the United Nations Industrial Development Organization (UNIDO), China is the top manufacturer worldwide by 2019 output, producing 28.7% of the total global manufacturing output, followed by the United States, Japan, Germany, and India.[52][53] (en.wikipedia.org)
- (2:04) MTO is a production technique wherein products are customized according to customer specifications, and production only starts after an order is received. (oracle.com)
- Job #1 is delivering the ordered product according to specifications: color, size, brand, and quantity. (netsuite.com)
External Links
How To
How to Use the 5S to Increase Productivity In Manufacturing
5S stands to stand for "Sort", “Set In Order", “Standardize", and "Store". Toyota Motor Corporation developed the 5S method in 1954. It improves the work environment and helps companies to achieve greater efficiency.
This method aims to standardize production processes so that they are repeatable, measurable and predictable. This means that every day tasks such cleaning, sorting/storing, packing, and labeling can be performed. This knowledge allows workers to be more efficient in their work because they are aware of what to expect.
There are five steps to implementing 5S, including Sort, Set In Order, Standardize, Separate and Store. Each step requires a different action to increase efficiency. If you sort items, it makes them easier to find later. When you arrange items, you place them together. Once you have separated your inventory into groups and organized them, you will store these groups in easily accessible containers. Finally, when you label your containers, you ensure everything is labeled correctly.
Employees need to reflect on how they do their jobs. Employees must be able to see why they do what they do and find a way to achieve them without having to rely on their old methods. They must learn new skills and techniques in order to implement the 5S system.
The 5S method increases efficiency and morale among employees. As they begin to see improvements, they feel motivated to continue working towards the goal of achieving higher levels of efficiency.