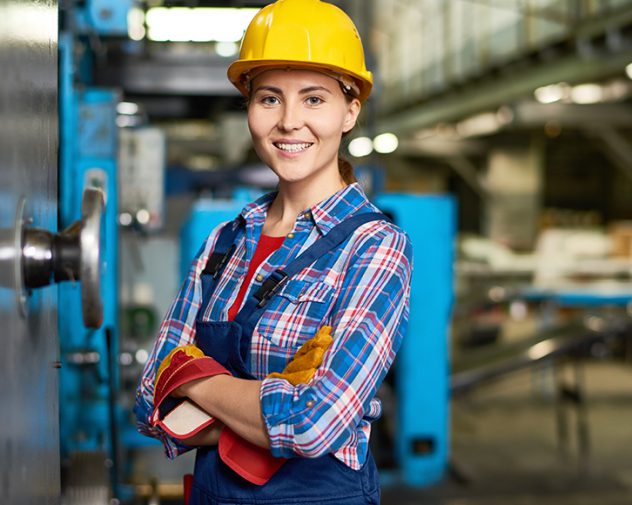
Structural engineers have one of the highest salaries, compared to other professions. The demand for structural engineers affects their salary. A typical requirement for structural engineers is a minimum of a bachelor's level. They should also have at least one year of experience in this field. They could be employed in a construction company or utility company. Some structural engineers may start their own firm.
Structural engineers create structures that can withstand stress. They need to be familiar with the properties and limitations of various materials. They might also be required to work on bid projects. They need to have project management and communication skills. They need to be proficient with computer software. To meet deadlines, they might have to work overtime. They can also travel for client projects outside their city.
Many structures engineers work full-time. But they can also work nights and weekends. They can use the company car and receive extended health benefits if they work for a company. They may be eligible for employee share ownership plans. A structural engineer can also increase his or her salary by changing employers or gaining an advanced degree. The annual salary for structural engineer can be anywhere from $59,000 to $118,000.
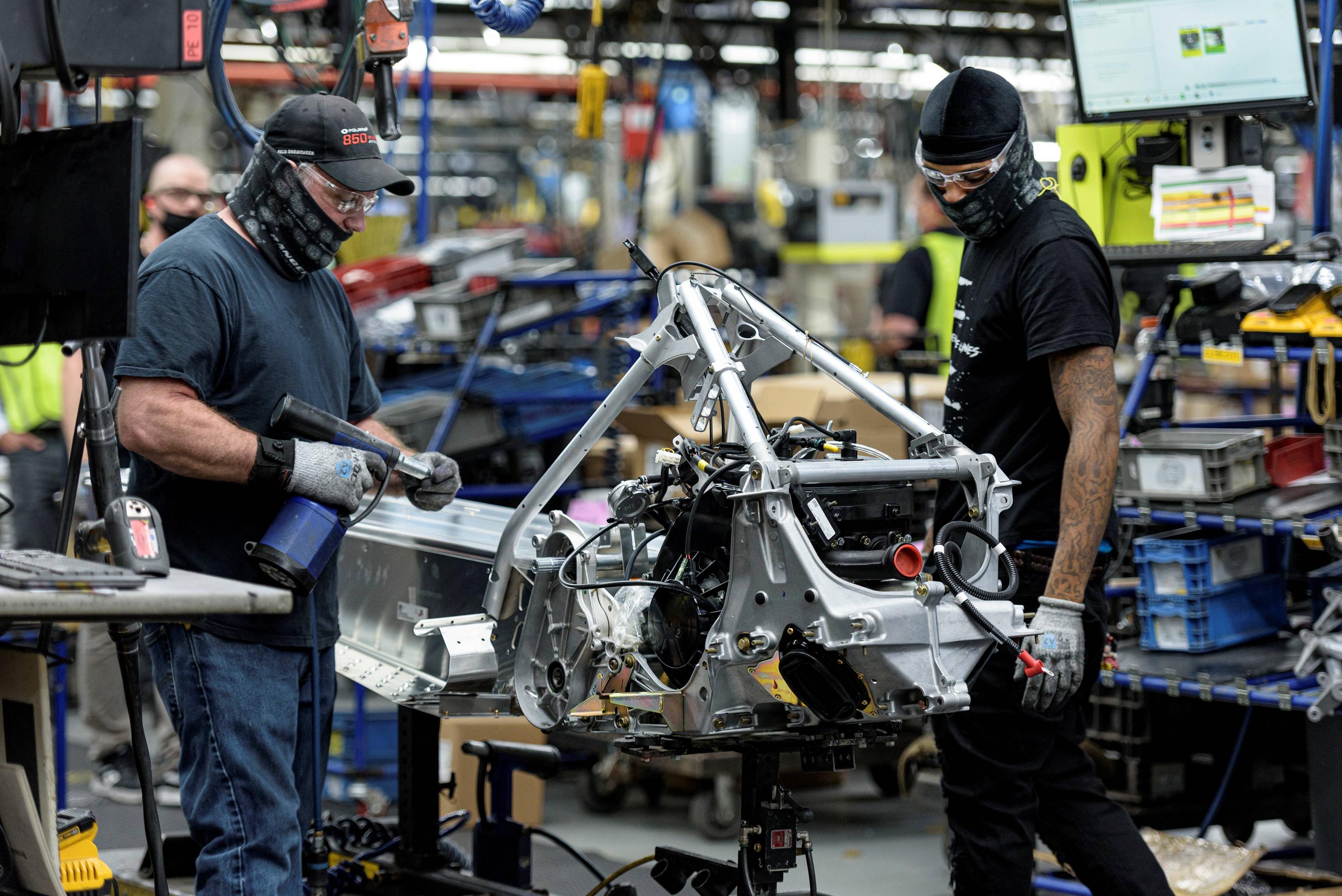
The salaries for structural engineers vary across the United States. San Francisco structural engineers earn an average of $147.822 per year. District of Columbia earns the second-highest salary, with an average of $146.683. The third highest salary is in Deer Park, CA, where the average salary is $111,562.
In Oslo, Norway, the average salary for structures engineer is kr 765 026 a year. The average Norwegian salary for structural engineers is kr 765 026 per year. The salary of structural engineers is also correlated with the cost of living.
Most structural engineers work Monday through Friday from 9:00 AM to 5:00 PM. They can also work weekends, nights, and holidays. They might visit construction sites occasionally to check on work. They must be able communicate with their clients their designs. They will also need to know how to use computer-aided modeling (CAD) software to visualize the final parts.
An experienced structural engineer can also be an assistant. They will need to go through supervised training before being able to work independently. You can also get certified as a structural engineer through an apprenticeship program. They must have at minimum four years experience in the field. Once they have sufficient experience, they may apply directly to employers.
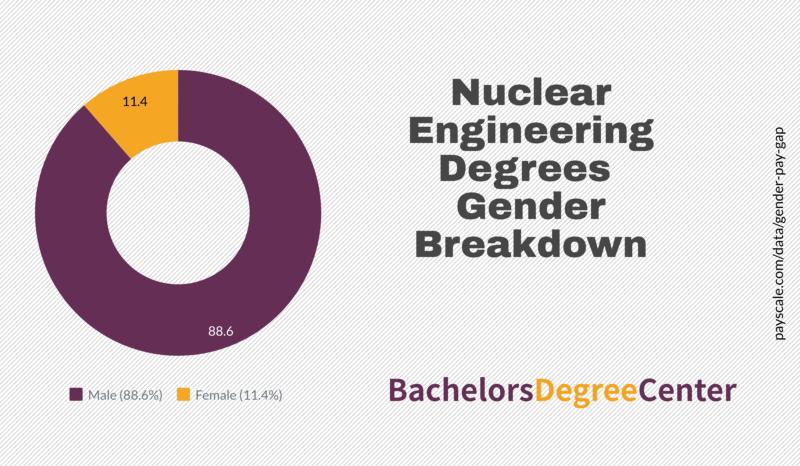
A typical hourly wage for structural engineers is $42 As a structural engineer your salary may increase if the work you do is hard and you get more experience. The best salaries are earned by senior structural engineers. You can also join the Institution of StructE which recognizes excellence within the field.
A structural engineer's total compensation includes salary, bonus and profit sharing. The average bonus is $3179
FAQ
What does it take to run a logistics business?
To be a successful businessman in logistics, you will need many skills and knowledge. Effective communication skills are necessary to work with suppliers and clients. It is important to be able to analyse data and draw conclusions. You must be able and able to handle stress situations and work under pressure. You must be creative and innovative to develop new ideas to improve efficiency. You need to have strong leadership qualities to motivate team members and direct them towards achieving organizational goals.
It is important to be organized and efficient in order to meet tight deadlines.
What are manufacturing and logistics?
Manufacturing refers to the process of making goods using raw materials and machines. Logistics includes all aspects related to supply chain management, such as procurement, distribution planning, inventory control and transportation. Manufacturing and logistics are often considered together as a broader term that encompasses both the process of creating products and delivering them to customers.
What are the four types of manufacturing?
Manufacturing is the process of transforming raw materials into useful products using machines and processes. Manufacturing involves many activities, including designing, building, testing and packaging, shipping, selling, service, and so on.
Are there any Manufacturing Processes that we should know before we can learn about Logistics?
No. No. Knowing about manufacturing processes will help you understand how logistics works.
What does warehouse mean?
Warehouses and storage facilities are where goods are kept before being sold. It can be an indoor space or an outdoor area. Sometimes, it can be both an indoor and outdoor space.
What kind of jobs are there in logistics?
There are many jobs available in logistics. Some examples are:
-
Warehouse workers – They load, unload and transport pallets and trucks.
-
Transportation drivers – These drivers drive trucks and wagons to transport goods and pick up the goods.
-
Freight handlers are people who sort and pack freight into warehouses.
-
Inventory managers - These are responsible for overseeing the stock of goods in warehouses.
-
Sales reps - They sell products and services to customers.
-
Logistics coordinators are responsible for organizing and planning logistics operations.
-
Purchasing agents - They buy goods and services that are necessary for company operations.
-
Customer service representatives are available to answer customer calls and emails.
-
Shipping clerks - They process shipping orders and issue bills.
-
Order fillers – They fill orders based upon what was ordered and shipped.
-
Quality control inspectors – They inspect incoming and outgoing products to ensure that there are no defects.
-
Other - Logistics has many other job opportunities, including transportation supervisors, logistics specialists, and cargo specialists.
How can manufacturing prevent production bottlenecks?
Production bottlenecks can be avoided by ensuring that processes are running smoothly during the entire production process, starting with the receipt of an order and ending when the product ships.
This includes both quality control and capacity planning.
This can be done by using continuous improvement techniques, such as Six Sigma.
Six Sigma Management System is a method to increase quality and reduce waste throughout your organization.
It emphasizes consistency and eliminating variance in your work.
Statistics
- In 2021, an estimated 12.1 million Americans work in the manufacturing sector.6 (investopedia.com)
- [54][55] These are the top 50 countries by the total value of manufacturing output in US dollars for its noted year according to World Bank.[56] (en.wikipedia.org)
- (2:04) MTO is a production technique wherein products are customized according to customer specifications, and production only starts after an order is received. (oracle.com)
- In the United States, for example, manufacturing makes up 15% of the economic output. (twi-global.com)
- According to a Statista study, U.S. businesses spent $1.63 trillion on logistics in 2019, moving goods from origin to end user through various supply chain network segments. (netsuite.com)
External Links
How To
How to Use the Just-In-Time Method in Production
Just-intime (JIT), which is a method to minimize costs and maximize efficiency in business process, is one way. It's a way to ensure that you get the right resources at just the right time. This means that your only pay for the resources you actually use. Frederick Taylor was the first to coin this term. He developed it while working as a foreman during the early 1900s. He saw how overtime was paid to workers for work that was delayed. He concluded that if workers were given enough time before they start work, productivity would increase.
JIT is an acronym that means you need to plan ahead so you don’t waste your money. The entire project should be looked at from start to finish. You need to ensure you have enough resources to tackle any issues that might arise. You can anticipate problems and have enough equipment and people available to fix them. This way, you won't end up paying extra money for things that weren't really necessary.
There are many types of JIT methods.
-
Demand-driven JIT: This is a JIT that allows you to regularly order the parts/materials necessary for your project. This will enable you to keep track of how much material is left after you use it. This will allow to you estimate the time it will take for more to be produced.
-
Inventory-based: You stock materials in advance to make your projects easier. This allows one to predict how much they will sell.
-
Project-driven: This method allows you to set aside enough funds for your project. Knowing how much money you have available will help you purchase the correct amount of materials.
-
Resource-based JIT: This type of JIT is most commonly used. Here, you allocate certain resources based on demand. For example, if there is a lot of work coming in, you will have more people assigned to them. If you don't have many orders, you'll assign fewer people to handle the workload.
-
Cost-based: This approach is very similar to resource-based. However, you don't just care about the number of people you have; you also need to consider how much each person will cost.
-
Price-based pricing: This is similar in concept to cost-based but instead you look at how much each worker costs, it looks at the overall company's price.
-
Material-based is an alternative to cost-based. Instead of looking at the total cost in the company, this method focuses on the average amount of raw materials that you consume.
-
Time-based JIT: A variation on resource-based JIT. Instead of worrying about how much each worker costs, you can focus on how long the project takes.
-
Quality-based JIT: Another variation on resource-based JIT. Instead of thinking about the cost of each employee or the time it takes to produce something, you focus on how good your product quality.
-
Value-based JIT is the newest form of JIT. In this instance, you are not concerned about the product's performance or meeting customer expectations. Instead, you focus on the added value that you provide to your market.
-
Stock-based. This method is inventory-based and focuses only on the actual production at any given point. It's useful when you want maximum production and minimal inventory.
-
Just-in time (JIT), planning: This is a combination JIT/supply chain management. It is the process of scheduling components' delivery as soon as they have been ordered. This is important as it reduces lead time and increases throughput.