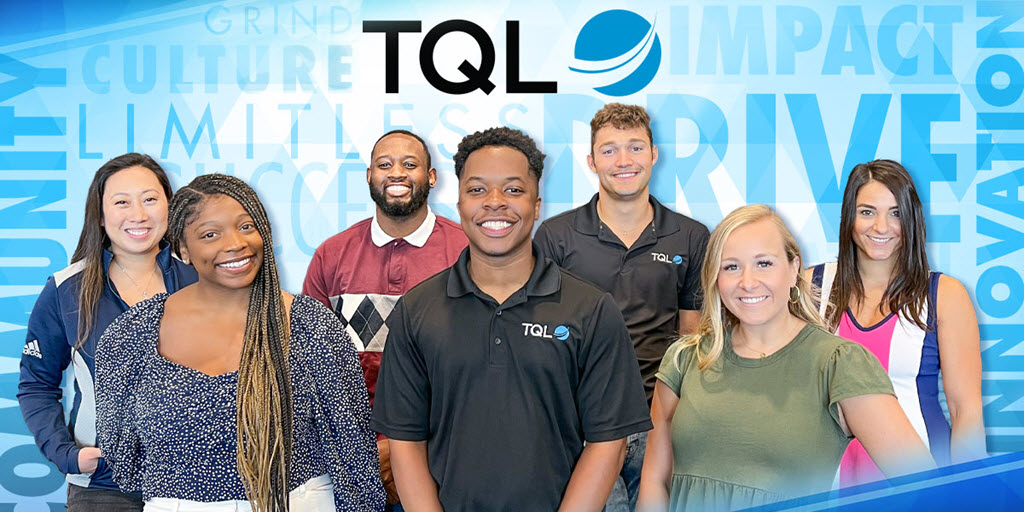
Logistics is an essential component of any supply-chain. Products must be transported from one place to another, starting at the beginning. In today's fast-paced world, logistics is an essential component of every company's operations. Effective logistics requires a well-trained workforce. In addition, a logistic supply chain involves the efficient and timely movement of goods, information, and resources. But what exactly does logistics mean? This article will explore some important aspects in logistic supply chain.
Logistics is the movement and storage of products from one point to another.
Logistics is the act of moving goods from A to B. Logistics managers oversee these processes. They are responsible for coordinating all aspects of moving products from one destination to the other. They need to determine the best shipping method for a product, take into account its weight, recyclability and ensure the final cost is equal to the total load. Customers satisfaction and warehousing requirements are also important factors in shipping costs.
It is an integral part of a supply-chain
The logistics process includes identifying problems within the supply chain and finding solutions. These problems are often associated with high costs and waste. You might order a large quantity of a product, but it may sit on a shelf in the warehouse for several days. High transportation costs are another cost. Problems can also arise from overproduction, when companies produce more product than they actually need. This causes wasted resources and can impact the market's pricing.
It takes a skilled workforce.
For a logistics supply chain, it is essential to have a qualified workforce. A skilled workforce will give a company a competitive advantage and will ensure the logistics facility runs smoothly. If the workforce exceeds expectations, they should be rewarded. Total Logistics Solutions consultants can be found in warehouses to gain a better understanding of the process. It also helps to know your competition well. A Total Logistics Solutions consultant can help you achieve this.
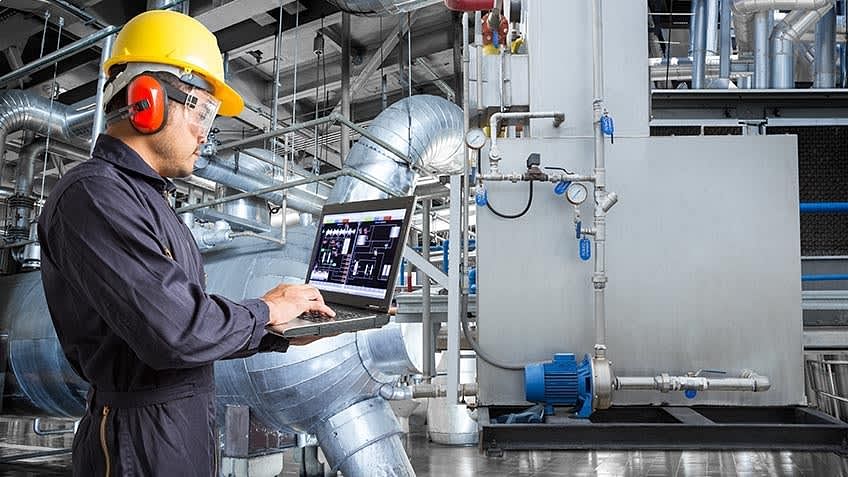
It requires technology
To be competitive, the logistics industry is facing technological advances that are not only changing the industry's landscape, but also the way it works. The logistics industry is changing with the advent of advanced analytics, additive manufacturing, automation, and other technological advances. This will lead to an increase in autonomous vehicles within warehouses and dramatic changes in inventory management and warehousing. Ultimately, these advancements will make logistics more efficient and more cost-effective for businesses.
FAQ
How can we improve manufacturing efficiency?
First, we need to identify which factors are most critical in affecting production times. We then need to figure out how to improve these variables. You can start by identifying the most important factors that impact production time. Once you've identified them all, find solutions to each one.
How important is automation in manufacturing?
Automating is not just important for manufacturers, but also for service providers. They can provide services more quickly and efficiently thanks to automation. It reduces human errors and improves productivity, which in turn helps them lower their costs.
What is the job of a logistics manger?
Logistics managers ensure that goods arrive on time and are unharmed. This is achieved by using their knowledge and experience with the products of the company. He/she also needs to ensure adequate stock to meet demand.
What do we need to know about Manufacturing Processes in order to learn more about Logistics?
No. No. It is important to know about the manufacturing processes in order to understand how logistics works.
What skills are required to be a production manager?
A production planner must be organized, flexible, and able multitask to succeed. Effective communication with clients and colleagues is essential.
Statistics
- In the United States, for example, manufacturing makes up 15% of the economic output. (twi-global.com)
- [54][55] These are the top 50 countries by the total value of manufacturing output in US dollars for its noted year according to World Bank.[56] (en.wikipedia.org)
- Job #1 is delivering the ordered product according to specifications: color, size, brand, and quantity. (netsuite.com)
- According to a Statista study, U.S. businesses spent $1.63 trillion on logistics in 2019, moving goods from origin to end user through various supply chain network segments. (netsuite.com)
- (2:04) MTO is a production technique wherein products are customized according to customer specifications, and production only starts after an order is received. (oracle.com)
External Links
How To
How to use lean manufacturing in the production of goods
Lean manufacturing is a management system that aims at increasing efficiency and reducing waste. It was developed in Japan during the 1970s and 1980s by Taiichi Ohno, who received the Toyota Production System (TPS) award from TPS founder Kanji Toyoda. The first book published on lean manufacturing was titled "The Machine That Changed the World" written by Michael L. Watkins and published in 1990.
Lean manufacturing is often defined as a set of principles used to improve the quality, speed, and cost of products and services. It emphasizes reducing defects and eliminating waste throughout the value chain. Just-in-time (JIT), zero defect (TPM), and 5S are all examples of lean manufacturing. Lean manufacturing is about eliminating activities that do not add value, such as inspection, rework, and waiting.
Lean manufacturing improves product quality and costs. It also helps companies reach their goals quicker and decreases employee turnover. Lean manufacturing has been deemed one of the best ways to manage the entire value-chain, including customers, distributors as well retailers and employees. Lean manufacturing is widely used in many industries. Toyota's philosophy is the foundation of its success in automotives, electronics and appliances, healthcare, chemical engineers, aerospace, paper and food, among other industries.
Five basic principles of Lean Manufacturing are included in lean manufacturing
-
Define value - Find out what your business contributes to society, and what makes it different from other competitors.
-
Reduce waste - Stop any activity that isn't adding value to the supply chains.
-
Create Flow – Ensure that work flows smoothly throughout the process.
-
Standardize and simplify - Make your processes as consistent as possible.
-
Build Relationships - Establish personal relationships with both internal and external stakeholders.
Lean manufacturing, although not new, has seen renewed interest in the economic sector since 2008. Many businesses are now using lean manufacturing to improve their competitiveness. Many economists believe lean manufacturing will play a major role in economic recovery.
Lean manufacturing is becoming a popular practice in automotive. It has many advantages. These include higher customer satisfaction, lower inventory levels, lower operating expenses, greater productivity, and improved overall safety.
Lean manufacturing can be applied to almost every aspect of an organization. Because it makes sure that all value chains are efficient and effectively managed, Lean Manufacturing is particularly helpful for organizations.
There are three types of lean manufacturing.
-
Just-in-Time Manufacturing: Also known as "pull systems", this type of lean manufacturing uses just-in-time manufacturing (JIT). JIT means that components are assembled at the time of use and not manufactured in advance. This strategy aims to decrease lead times, increase availability of parts and reduce inventory.
-
Zero Defects Manufacturing, (ZDM): ZDM is focused on ensuring that no defective products leave the manufacturing facility. If a part is required to be repaired on the assembly line, it should not be scrapped. This applies to finished products, which may need minor repairs before they are shipped.
-
Continuous Improvement: Continuous Improvement aims to improve efficiency by continually identifying problems and making adjustments to eliminate or minimize waste. It involves continuous improvement of processes, people, and tools.