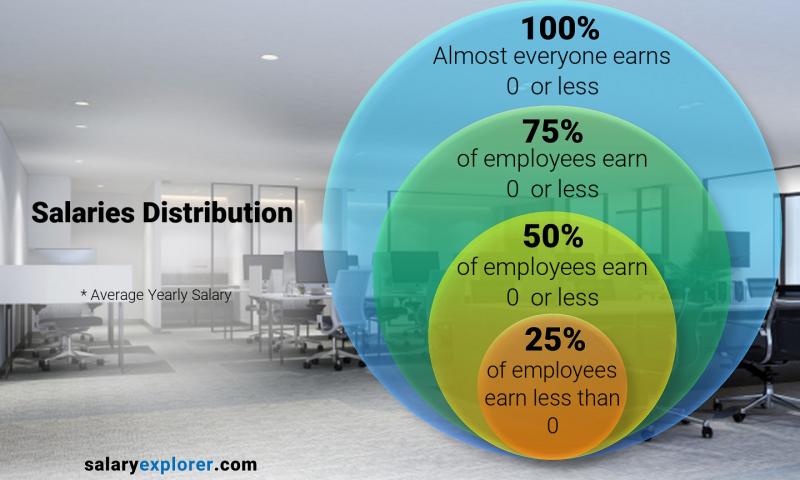
An accurate cost estimate is necessary for nearly every task a company undertakes. Cost estimators are responsible for this. They aid companies to determine the costs involved in manufacturing or developing new products. They must also evaluate the costs of building a new structure. This includes analyzing the costs of materials and labor.
Construction companies employ most cost estimaters. They are expected to be well-versed in construction processes and methods. They will also need to be familiarized with computer-aided planning (CAD). This software helps to improve efficiency in design and manufacturing. Cost estimators also need to be able to read data from databases. They can also make use of other software like Microsoft Excel.
To make accurate cost estimates, cost estimators collaborate with other professionals. To determine the cost of each component, they evaluate the site conditions and project blueprints. They may also consult engineers to determine the necessary machining operations and gauges.
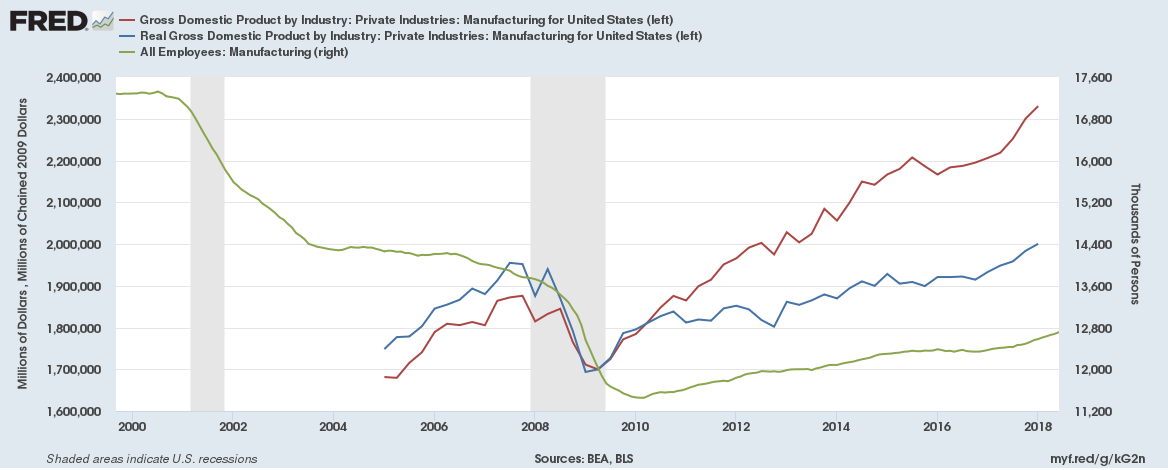
Cost estimators must be meticulous, assertive, and reliable. They must be capable of interpreting difficult information. They must be able to communicate clearly and accurately their findings. Aside from that, they should be able work with professionals as well as clients.
Cost estimators typically work in the engineering or cost divisions of a company. They should have a solid knowledge of science and math. They must also have a strong knowledge of computer software including BIM, CAD, and commercial. They might be required to attend a certification program. Certified Cost Estimator/Analyst(CCEA), Professional cost estimator/Analyst and Certified Professional Estimator are some examples of certifications.
Cost estimators might be experts in particular services or industries. Some specialize in construction or building costs while others concentrate on software development. Cost estimators could also be employed in other areas like automotive repair and management, building construction, or specialty trade contractors.
These individuals communicate with suppliers, clients, and engineers. They are also proficient in industry terminology. They also build up a vast knowledge base before preparing costs estimates. This occupation is not only responsible for preparing cost estimates but also conducts studies to study the impact of various processes on costs and to find ways to decrease costs.
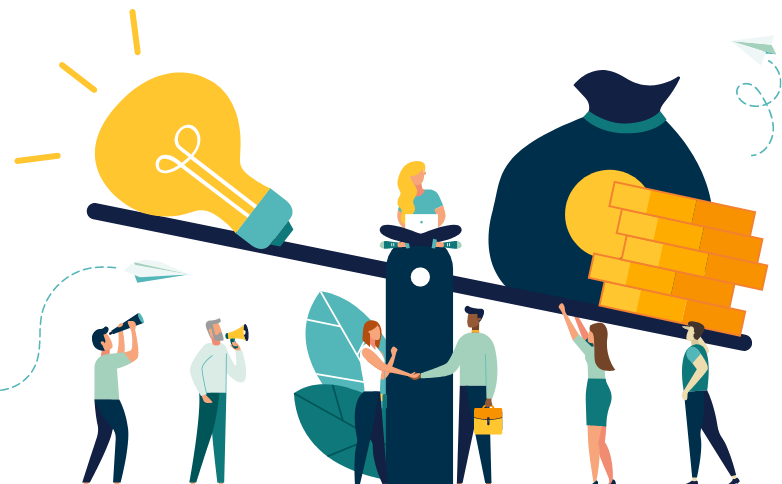
The industry may require job applicants to have a bachelor’s degree. An internship may be required. They may also benefit from cooperative education programs. A degree in building construction, or construction management is also an advantage for construction companies.
They work in construction and other manufacturing companies. They provide accurate estimates to companies that enable them to make profitable bids. They can also analyze data regarding the supply chain, and other factors that influence costs. They can also be cost estimators for government programs. They may also be asked to redesign products or services.
Cost estimators must have a strong understanding of computer-aided design (CAD) software. They can also be trained in the use of automatic cost estimation software.
FAQ
What is the job of a logistics manger?
Logistics managers ensure that goods arrive on time and are unharmed. This is accomplished by using the experience and knowledge gained from working with company products. He/she should also ensure enough stock is available to meet demand.
What does warehouse refer to?
A warehouse is a place where goods are stored until they are sold. It can be either an indoor or outdoor space. It could be one or both.
How does manufacturing avoid bottlenecks in production?
Avoiding production bottlenecks is as simple as keeping all processes running smoothly, from the time an order is received until the product ships.
This includes planning for both capacity requirements and quality control measures.
This can be done by using continuous improvement techniques, such as Six Sigma.
Six Sigma Management System is a method to increase quality and reduce waste throughout your organization.
It is focused on creating consistency and eliminating variation in your work.
Why automate your factory?
Modern warehouses are increasingly dependent on automation. The rise of e-commerce has led to increased demand for faster delivery times and more efficient processes.
Warehouses should be able adapt quickly to new needs. They must invest heavily in technology to do this. Automation warehouses can bring many benefits. These are just a few reasons to invest in automation.
-
Increases throughput/productivity
-
Reduces errors
-
Accuracy is improved
-
Safety enhancements
-
Eliminates bottlenecks
-
Companies can scale up more easily
-
Makes workers more efficient
-
Gives you visibility into all that is happening in your warehouse
-
Enhances customer experience
-
Improves employee satisfaction
-
Reducing downtime and increasing uptime
-
You can be sure that high-quality products will arrive on time
-
Eliminates human error
-
It helps ensure compliance with regulations
What are the 7 R's of logistics?
The acronym 7R's for Logistics stands to represent the seven basic principles in logistics management. It was developed by the International Association of Business Logisticians (IABL) and published in 2004 as part of its "Seven Principles of Logistics Management" series.
The acronym is composed of the following letters.
-
Responsible - ensure that all actions taken are within legal requirements and are not harmful to others.
-
Reliable - Have confidence in your ability to fulfill all of your commitments.
-
It is reasonable to use resources efficiently and not waste them.
-
Realistic - Consider all aspects of operations, including environmental impact and cost effectiveness.
-
Respectful - Treat people fairly and equitably
-
Reliable - Find ways to save money and increase your productivity.
-
Recognizable - provide customers with value-added services.
Statistics
- (2:04) MTO is a production technique wherein products are customized according to customer specifications, and production only starts after an order is received. (oracle.com)
- According to a Statista study, U.S. businesses spent $1.63 trillion on logistics in 2019, moving goods from origin to end user through various supply chain network segments. (netsuite.com)
- Many factories witnessed a 30% increase in output due to the shift to electric motors. (en.wikipedia.org)
- It's estimated that 10.8% of the U.S. GDP in 2020 was contributed to manufacturing. (investopedia.com)
- [54][55] These are the top 50 countries by the total value of manufacturing output in US dollars for its noted year according to World Bank.[56] (en.wikipedia.org)
External Links
How To
How to Use Six Sigma in Manufacturing
Six Sigma is "the application statistical process control (SPC), techniques for continuous improvement." Motorola's Quality Improvement Department created Six Sigma at their Tokyo plant, Japan in 1986. Six Sigma's main goal is to improve process quality by standardizing processes and eliminating defects. Many companies have adopted Six Sigma in recent years because they believe that there are no perfect products and services. Six Sigma's primary goal is to reduce variation from the average value of production. If you take a sample and compare it with the average, you will be able to determine how much of the production process is different from the norm. If there is a significant deviation from the norm, you will know that something needs to change.
The first step toward implementing Six Sigma is understanding how variability works in your business. Once you have a good understanding of the basics, you can identify potential sources of variation. This will allow you to decide if these variations are random and systematic. Random variations occur when people make mistakes; systematic ones are caused by factors outside the process itself. You could consider random variations if some widgets fall off the assembly lines. It would be considered a systematic problem if every widget that you build falls apart at the same location each time.
Once you've identified the problem areas you need to find solutions. This could mean changing your approach or redesigning the entire process. Test them again once you've implemented the changes. If they didn't work, then you'll need to go back to the drawing board and come up with another plan.