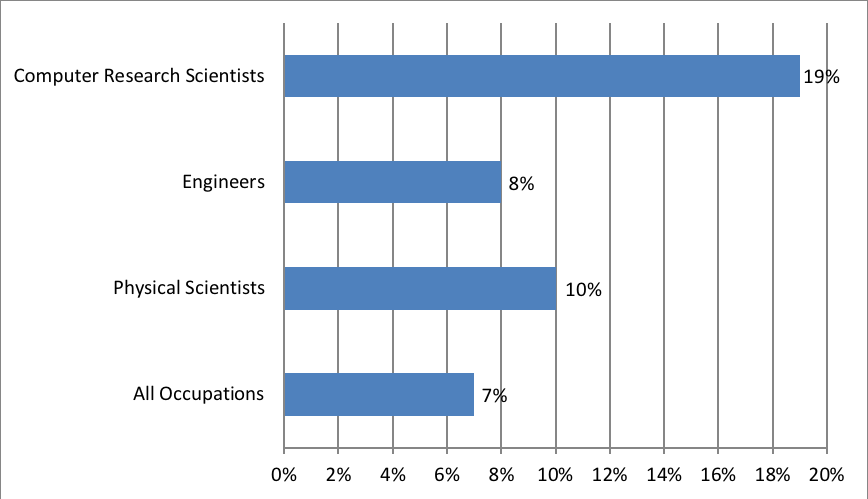
The United States is the third largest manufacturer in the world, and its manufacturing output hit a record high in Q1 2018 at $2.00 trillion, nearly double the amount before the Great Recession. However, despite a strong domestic economy, the United States manufacturing industry is taking a shotgun approach to its current challenges. We need to be more aggressive in addressing the industry's challenges, regardless of whether this is due to a lack or skilled labor.
Since 2000, jobs have dropped by 5 million
Since 2000, the US has lost five millions manufacturing jobs. While some people believe trade with China is the reason, it only accounts for a fourth to four percent of the decline in manufacturing job opportunities. Manufacturing jobs were also lost in countries that couldn't compete with Chinese imports. But there are many factors that contributed to the decline of manufacturing jobs. The following are some of the reasons:
Over the past two decades, almost a third have been lost in US manufacturing. It was 17,000,000 in 1965. It dropped to just 12,000,000 in 2010. While the decline in manufacturing jobs is not the fault of trade, it has been the result of structural problems - a decline in capital investment, output, productivity, and trade deficits - which are not sustainable. Although productivity gains had a large role in the decline in manufacturing jobs, they weren't enough. The problem is automation, not productivity gains.
Strong demand is for manufactured products
In the United States, the demand for manufactured goods remains strong despite the fact that the share of consumer spending on these items has decreased over the past few decades. In 1945, personal spending on durable goods made up 58% of total expenditures, compared with 28% today. This is because both the manufacturing cost and the sale price have declined, but the content has increased. As a result, the cost of computers, televisions, and sound equipment has fallen significantly.
The US has experienced a rebound in manufacturing activity which has helped boost the production of manufactured products. According to the Fifth District Manufacturing Activity Survey, demand is high for manufactured goods and production is increasing. However, supply chain bottlenecks are limiting output. The increased production has stressed supply chains. Respondents report that they have experienced supply chain disruptions that impact their ability keep adequate inventories. Backlogs and lead times for vendors have increased.
The trade deficit in manufacturable goods has more or less doubled over the past decade
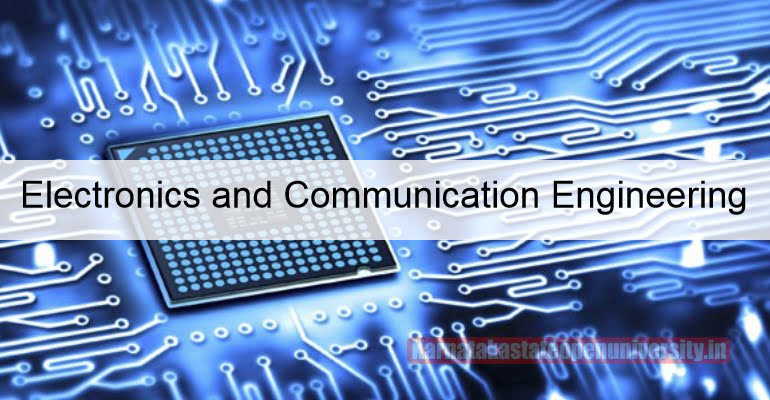
Some economists worry that the U.S.'s trade surplus will lower global growth and create more instability among its trading partners. Other economists point out that US imports are not always a good thing for the economy. They are essential to maintaining global stability. The trade deficit may even be a necessary evil, since the U.S. relies heavily on foreign markets to generate its economic output, while high levels of foreign demand may make it difficult to achieve full employment.
Since 2000, nearly two-thirds of the U.S. manufacturing goods trade deficit has increased. The increase in Chinese imports is partially responsible for the growing US deficit. The bigger problem is that the imbalance is concentrated within the manufacturing sector where wages and employment have declined since the 1990s. As a result, US manufacturing employment has fallen dramatically from 26 percent in 1970 to 8.5 percent in 2016. Some economists attribute the decline in manufacturing employment to China's increased level of competition. However, most economists attribute the decline primarily to automation, productivity growth, and shifting demand from goods towards services.
Industry uses a shotgun approach
The US has a variety of advanced manufacturing initiatives. It is also well-established in this area. But some countries are attempting to introduce the internet of things to manufacturing. The US, on the other hand, focuses on diverse technologies and combines Internet advertising with traditional mass media. The result is a shotgun approach, where companies focus on many different technologies and aim for a broad customer base.
FAQ
What is it like to manage a logistics company?
You need to have a lot of knowledge and skills to manage a successful logistic business. You must have good communication skills to interact effectively with your clients and suppliers. You must be able analyze data and draw out conclusions. You will need to be able handle pressure well and work in stressful situations. You need to be innovative and creative to come up with new ways to increase efficiency. You need to have strong leadership qualities to motivate team members and direct them towards achieving organizational goals.
You must be organized to meet tight deadlines.
What is the role and responsibility of a Production Planner?
Production planners make sure that every aspect of the project is delivered on-time, within budget, and within schedule. They also ensure the quality of the product and service meets the client's requirements.
What is the distinction between Production Planning or Scheduling?
Production Planning (PP), is the process of deciding what production needs to take place at any given time. This can be done by forecasting demand and identifying production capabilities.
Scheduling refers the process by which tasks are assigned dates so that they can all be completed within the given timeframe.
Do we need to know about Manufacturing Processes before learning about Logistics?
No. No. Understanding the manufacturing process will allow you to better understand logistics.
What makes a production planner different from a project manger?
The difference between a product planner and project manager is that a planer is typically the one who organizes and plans the entire project. A production planner, however, is mostly involved in the planning stages.
What is the difference between manufacturing and logistics
Manufacturing refers to the process of making goods using raw materials and machines. Logistics includes all aspects related to supply chain management, such as procurement, distribution planning, inventory control and transportation. Sometimes manufacturing and logistics are combined to refer to a wider term that includes both the process of creating products as well as their delivery to customers.
What skills is required for a production planner?
To become a successful production planner, you need to be organized, flexible, and able to multitask. Also, you must be able and willing to communicate with clients and coworkers.
Statistics
- In 2021, an estimated 12.1 million Americans work in the manufacturing sector.6 (investopedia.com)
- [54][55] These are the top 50 countries by the total value of manufacturing output in US dollars for its noted year according to World Bank.[56] (en.wikipedia.org)
- Many factories witnessed a 30% increase in output due to the shift to electric motors. (en.wikipedia.org)
- (2:04) MTO is a production technique wherein products are customized according to customer specifications, and production only starts after an order is received. (oracle.com)
- It's estimated that 10.8% of the U.S. GDP in 2020 was contributed to manufacturing. (investopedia.com)
External Links
How To
Six Sigma: How to Use it in Manufacturing
Six Sigma is "the application statistical process control (SPC), techniques for continuous improvement." Motorola's Quality Improvement Department in Tokyo, Japan developed Six Sigma in 1986. Six Sigma's core idea is to improve the quality of processes by standardizing and eliminating defects. Many companies have adopted Six Sigma in recent years because they believe that there are no perfect products and services. Six Sigma aims to reduce variation in the production's mean value. You can calculate the percentage of deviation from the norm by taking a sample of your product and comparing it to the average. If this deviation is too big, you know something needs fixing.
Understanding how variability works in your company is the first step to Six Sigma. Once you understand this, you can then identify the causes of variation. This will allow you to decide if these variations are random and systematic. Random variations happen when people make errors; systematic variations are caused externally. Random variations would include, for example, the failure of some widgets to fall from the assembly line. If however, you notice that each time you assemble a widget it falls apart in exactly the same spot, that is a problem.
After identifying the problem areas, you will need to devise solutions. You might need to change the way you work or completely redesign the process. Once you have implemented the changes, it is important to test them again to ensure they work. If they don’t work, you’ll need to go back and rework the plan.