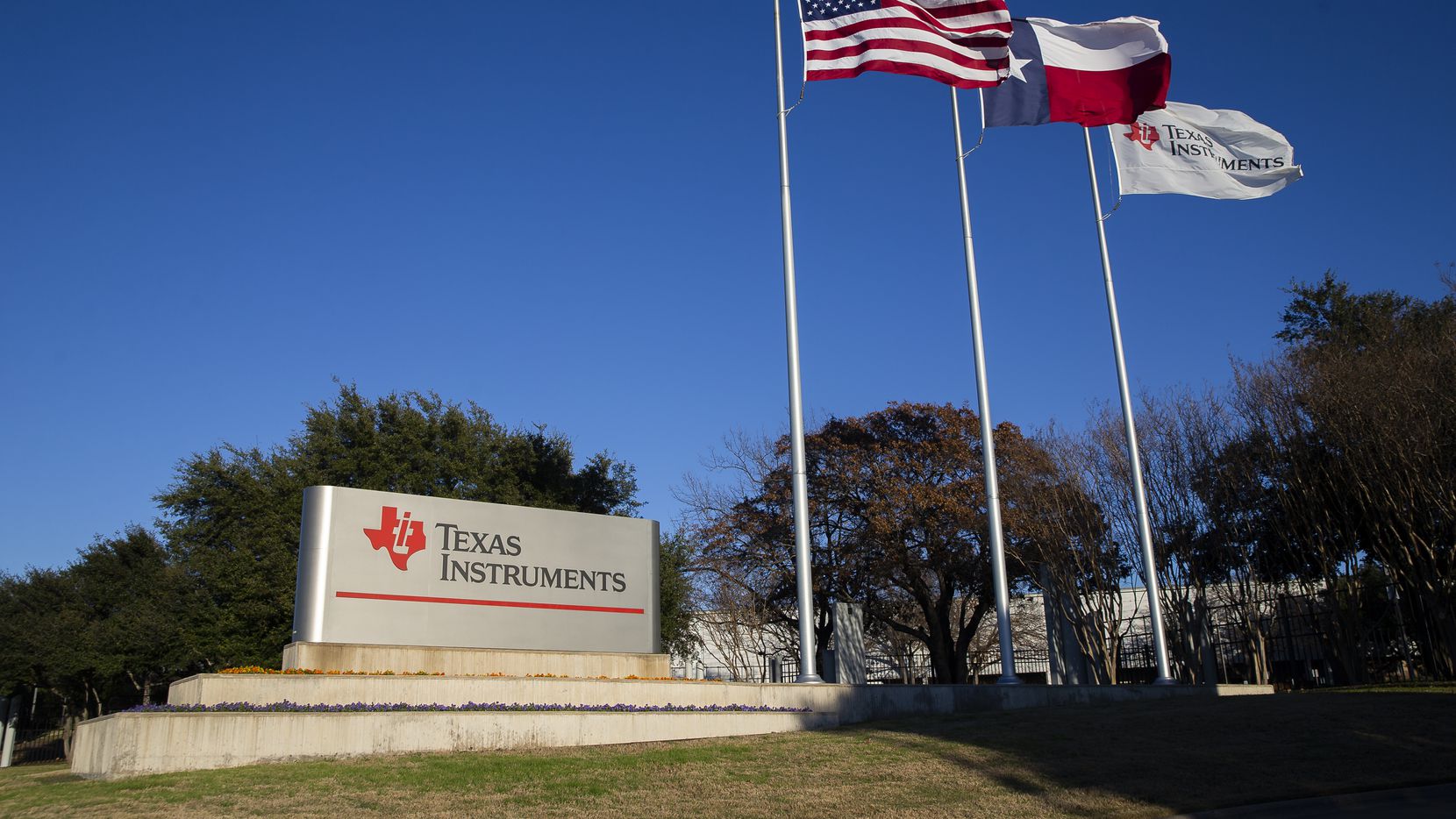
Companies that use advanced manufacturing technology to improve their products and processes often incorporate new technologies. These technologies are referred to as advanced, cutting edge, and innovative. More companies are integrating these technologies into their operations. Some of these technologies are: Robotics, Material deposition, and Additive manufacturing. Find out more about these technologies.
Additive manufacturing
Additive manufacturing is the future in manufacturing. This type involves additive manufacturing technologies also known as 3D printers. Several advantages of this type of manufacturing include increased flexibility and decreased inventory costs. It also reduces the need to import labor-intensive components and parts.
Innovations in additive manufacturing technology have greatly increased the speed of manufacturing. They allow businesses to respond quickly to supply-chain disruptions. They can manufacture custom parts in as little as a few hours, sometimes even in days. This process is particularly useful in industries that suffer from supply-chain bottlenecks. Advanced manufacturing is capable of producing parts with complex geometries.
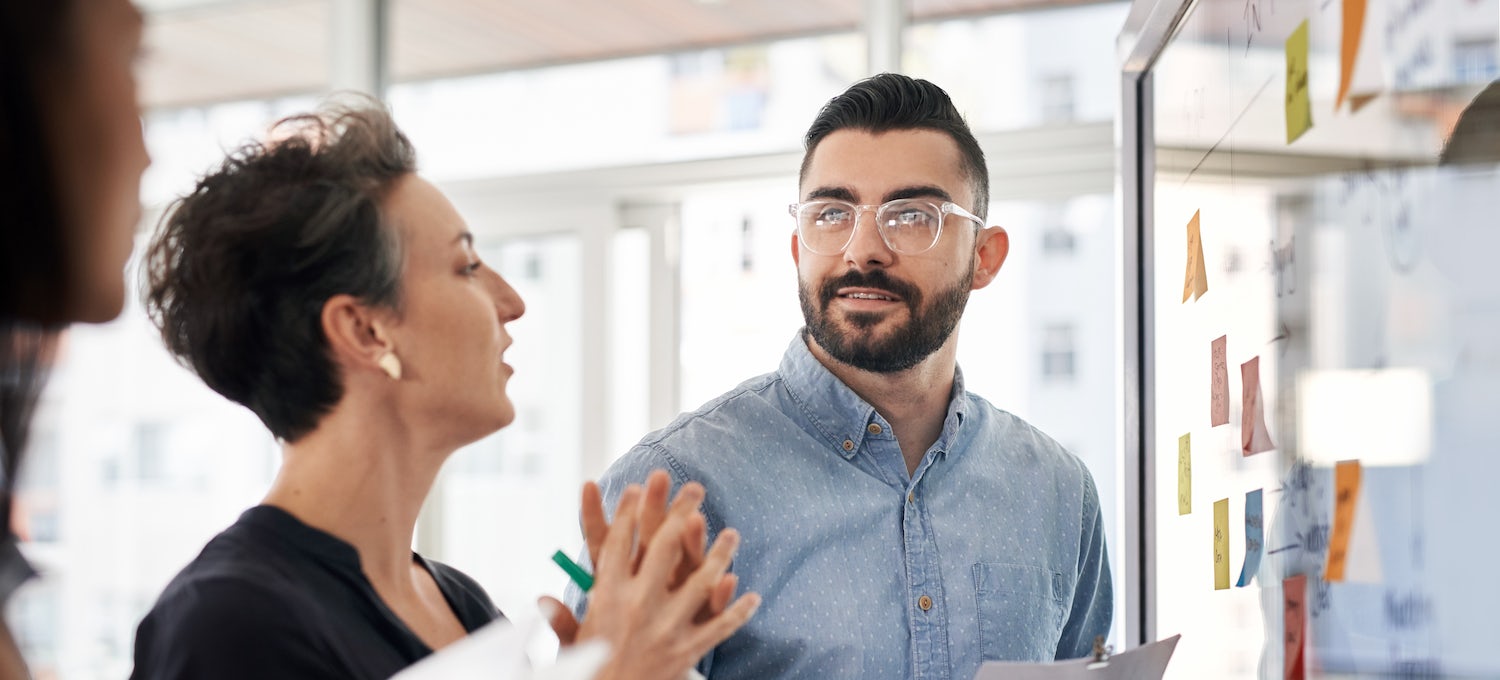
A manufacturer can also make very small quantities. You can use additive manufacturing to make custom dental appliances. This process allows the creation of complex structures like internal heat channels. Advanced manufacturing by additive manufacturing can also be used to reduce inventory and create specialized parts. It can reduce materials costs by ninety-five percent and energy consumption by half.
Robotics
Most industrial producers are keen to use advanced robotics in their manufacturing processes. They aren't satisfied with the current performance and progress made in their implementation. They cite high technology's limitations and high costs as obstacles to wider deployment. They lack key enablers that will allow them to fully deploy advanced robots in their factories.
In order to successfully integrate advanced robots, manufacturers must examine their system architecture. These systems must contain infrastructure, analytics, data, and workflow management. When these capabilities are in place companies can begin to look for strategic robotics partners. These partners will be able to help the company choose which processes and technologies are most suitable for their business. In the case of robotics, this can be accomplished with the use of simulation models.
The use of advanced robotics is rapidly evolving across numerous industries. Currently, robotic automation is being applied to areas as diverse as aerospace, medical, and automotive manufacturing. This technology has helped revolutionize the manufacturing industry. This technology not only lowers human labor costs but also saves money by running 24 hours a night and not requiring lights.
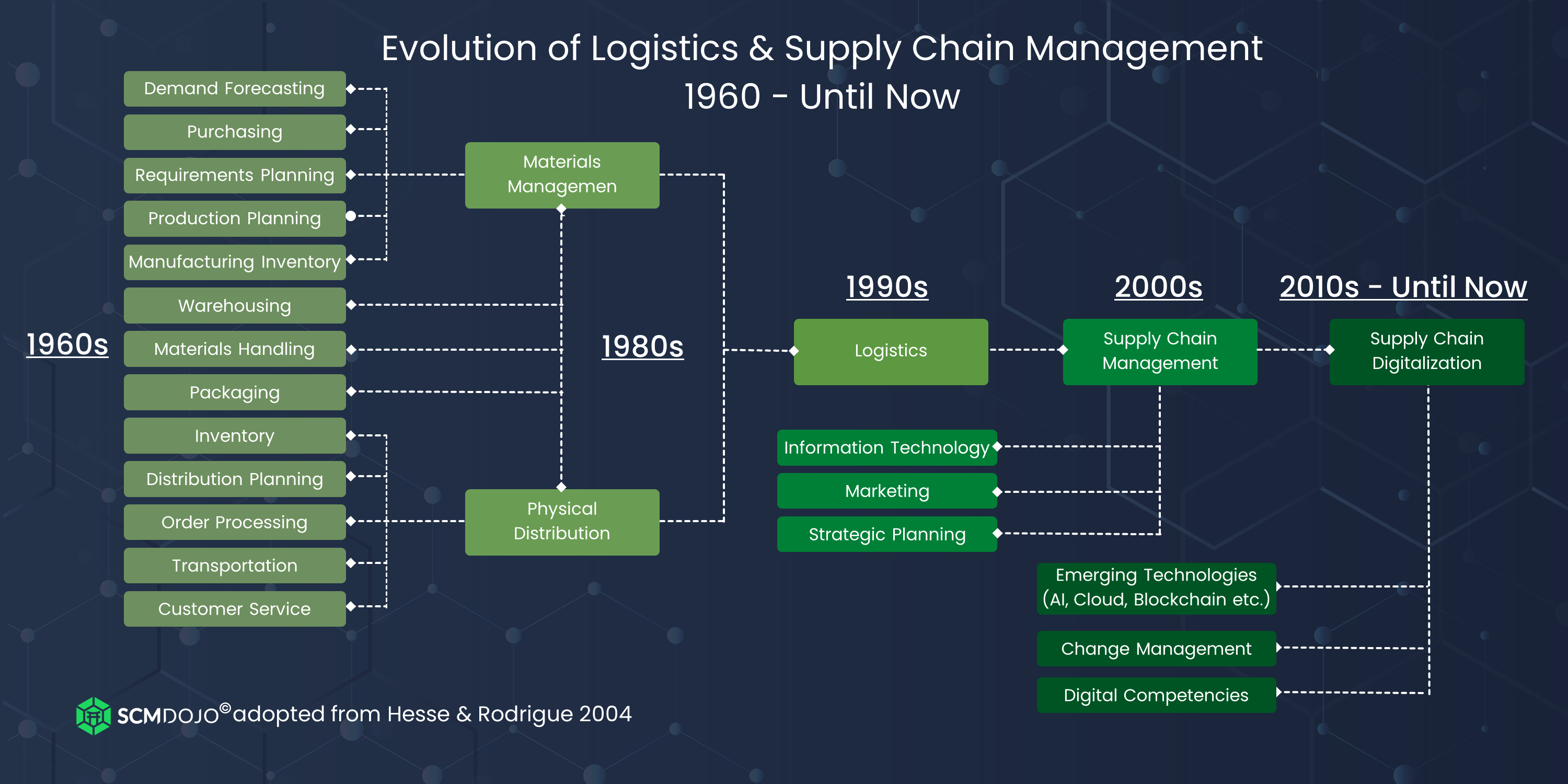
Material deposition
Material deposition is an important technique in advanced manufacturing. The process involves using a combination of laser beams and arc plasma energies to deposit thin films of a material on a target. A substrate is usually made up of wire or powder. The deposition takes place in an inert or vacuum. You can also find other sources of energy.
Plasma metal deposition is one of the most promising direct energy deposition techniques. It uses a plasma source for metals to be deposited. This process can be used to create large, complex parts from wire, powder or both. This process has many benefits, including a reduced amount of machining and a shorter lead-time.
This process can also be used to create ceramics, polymers and metals. Generally, metals are used in wire or powder form.
FAQ
What does manufacturing industry mean?
Manufacturing Industries are businesses that produce products for sale. Consumers are the people who purchase these products. These companies employ many processes to achieve this purpose, such as production and distribution, retailing, management and so on. They create goods from raw materials, using machines and various other equipment. This includes all types manufactured goods such as clothing, building materials, furniture, electronics, tools and machinery.
What does it take to run a logistics business?
To be a successful businessman in logistics, you will need many skills and knowledge. Effective communication skills are necessary to work with suppliers and clients. You will need to know how to interpret data and draw conclusions. You must be able and able to handle stress situations and work under pressure. You need to be innovative and creative to come up with new ways to increase efficiency. You will need strong leadership skills to motivate and direct your team members towards achieving their organizational goals.
It is also important to be efficient and well organized in order meet deadlines.
What is manufacturing and logistics?
Manufacturing refers to the process of making goods using raw materials and machines. Logistics is the management of all aspects of supply chain activities, including procurement, production planning, distribution, warehousing, inventory control, transportation, and customer service. Manufacturing and logistics are often considered together as a broader term that encompasses both the process of creating products and delivering them to customers.
What can I do to learn more about manufacturing?
Practical experience is the best way of learning about manufacturing. You can also read educational videos or take classes if this isn't possible.
How can excess manufacturing production be reduced?
Improved inventory management is the key to reducing overproduction. This would reduce the time spent on unproductive activities like purchasing, storing and maintaining excess stock. This will allow us to free up resources for more productive tasks.
Kanban systems are one way to achieve this. A Kanban board is a visual display used to track work in progress. Kanban systems allow work items to move through different states until they reach their final destination. Each state is assigned a different priority.
When work is completed, it can be transferred to the next stage. If a task is still in its beginning stages, it will continue to be so until it reaches the end.
This allows work to move forward and ensures that no work is missed. With a Kanban board, managers can see exactly how much work is being done at any given moment. This information allows managers to adjust their workflow based off real-time data.
Lean manufacturing, another method to control inventory levels, is also an option. Lean manufacturing works to eliminate waste throughout every stage of the production chain. Waste includes anything that does not add value to the product. Here are some examples of common types.
-
Overproduction
-
Inventory
-
Unnecessary packaging
-
Excess materials
These ideas will help manufacturers increase efficiency and lower costs.
Is automation necessary in manufacturing?
Not only are service providers and manufacturers important, but so is automation. They can provide services more quickly and efficiently thanks to automation. In addition, it helps them reduce costs by reducing human errors and improving productivity.
Why automate your warehouse
Modern warehousing has seen automation take center stage. With the rise of ecommerce, there is a greater demand for faster delivery times as well as more efficient processes.
Warehouses should be able adapt quickly to new needs. Technology is essential for warehouses to be able to adapt quickly to changing needs. Automating warehouses has many benefits. These are some of the benefits that automation can bring to warehouses:
-
Increases throughput/productivity
-
Reduces errors
-
Accuracy is improved
-
Safety enhancements
-
Eliminates bottlenecks
-
Companies can scale more easily
-
Increases efficiency of workers
-
This gives you visibility into what happens in the warehouse
-
Enhances customer experience
-
Improves employee satisfaction
-
Reducing downtime and increasing uptime
-
You can be sure that high-quality products will arrive on time
-
Human error can be eliminated
-
This helps to ensure compliance with regulations
Statistics
- According to the United Nations Industrial Development Organization (UNIDO), China is the top manufacturer worldwide by 2019 output, producing 28.7% of the total global manufacturing output, followed by the United States, Japan, Germany, and India.[52][53] (en.wikipedia.org)
- Many factories witnessed a 30% increase in output due to the shift to electric motors. (en.wikipedia.org)
- In the United States, for example, manufacturing makes up 15% of the economic output. (twi-global.com)
- (2:04) MTO is a production technique wherein products are customized according to customer specifications, and production only starts after an order is received. (oracle.com)
- Job #1 is delivering the ordered product according to specifications: color, size, brand, and quantity. (netsuite.com)
External Links
How To
How to Use the Just-In-Time Method in Production
Just-in-time (JIT) is a method that is used to reduce costs and maximize efficiency in business processes. It allows you to get the right amount resources at the right time. This means you only pay what you use. Frederick Taylor was the first to coin this term. He developed it while working as a foreman during the early 1900s. He noticed that workers were often paid overtime when they had to work late. He realized that workers should have enough time to complete their jobs before they begin work. This would help increase productivity.
JIT is an acronym that means you need to plan ahead so you don’t waste your money. Look at your entire project, from start to end. Make sure you have enough resources in place to deal with any unexpected problems. You will have the resources and people to solve any problems you anticipate. This will prevent you from spending extra money on unnecessary things.
There are several types of JIT techniques:
-
Demand-driven: This type of JIT allows you to order the parts/materials required for your project on a regular basis. This will enable you to keep track of how much material is left after you use it. This will let you know how long it will be to produce more.
-
Inventory-based: This is a type where you stock the materials required for your projects in advance. This allows one to predict how much they will sell.
-
Project-driven: This method allows you to set aside enough funds for your project. Knowing how much money you have available will help you purchase the correct amount of materials.
-
Resource-based JIT: This is the most popular form of JIT. Here you can allocate certain resources based purely on demand. If you have many orders, you will assign more people to manage them. If you don’t have many orders you will assign less people to the work.
-
Cost-based: This is a similar approach to resource-based but you are not only concerned with how many people you have, but also how much each one costs.
-
Price-based: This is similar to cost-based but instead of looking at individual workers' salaries, you look at the total company price.
-
Material-based: This approach is similar to cost-based. However, instead of looking at the total cost for the company, you look at how much you spend on average on raw materials.
-
Time-based: Another variation of resource-based JIT. Instead of focusing solely on the amount each employee costs, focus on how long it takes for the project to be completed.
-
Quality-based JIT: This is another variation of resource based JIT. Instead of focusing on the cost of each worker or how long it takes, think about how high quality your product is.
-
Value-based: This is one of the newest forms of JIT. This is where you don't care about how the products perform or whether they meet customers' expectations. Instead, you focus on the added value that you provide to your market.
-
Stock-based. This method is inventory-based and focuses only on the actual production at any given point. It is used when production goals are met while inventory is kept to a minimum.
-
Just-in-time (JIT) planning: This is a combination of JIT and supply chain management. This refers to the scheduling of the delivery of components as soon after they are ordered. It is essential because it reduces lead-times and increases throughput.