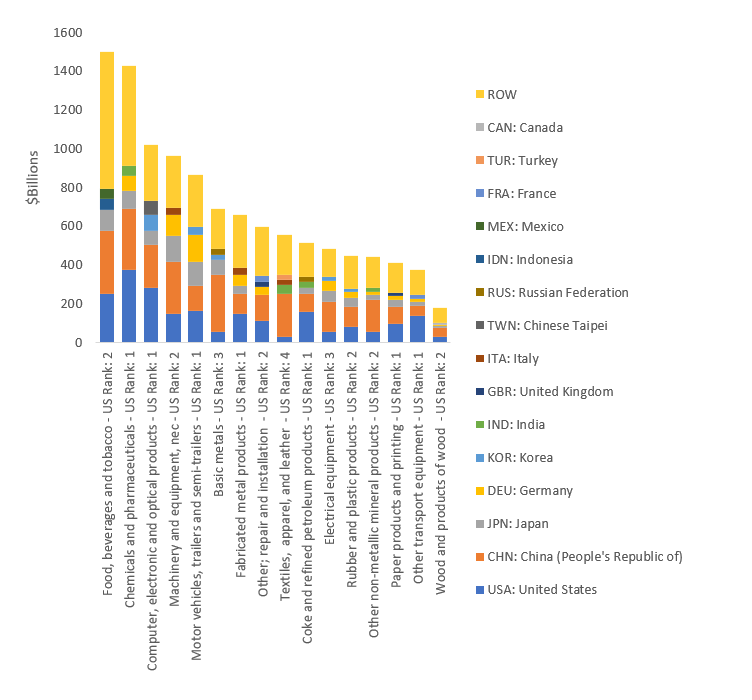
You need the right qualifications to pursue a career in maintenance engineering. Here are the certifications that you'll need and how much you can make. A maintenance engineer job is great for people who are detail-oriented. These professionals maintain the infrastructure of buildings and ensure it runs at its optimal level.
Qualifications for a career as a maintenance engineer
These are the key elements to consider if you are looking for a career as an engineer in maintenance. While a highschool diploma will provide you with the foundational skills needed, you might also be interested in taking an engineering course at college. It will be beneficial to take courses in chemistry and math. You can also gain work experience. A technical school might be an option, depending on your company's needs.
The maintenance engineer is responsible in maintaining machinery, equipment, infrastructures, and other systems. Their task is to ensure that industrial machinery runs as efficiently as possible. They are responsible for ensuring that spare parts and supplies are available. Some jobs, especially those in manufacturing, require shift work. Depending on what type of work they do, maintenance engineers could move up to management positions or seek other opportunities in related fields. After years of experience, they are able to open their own company.
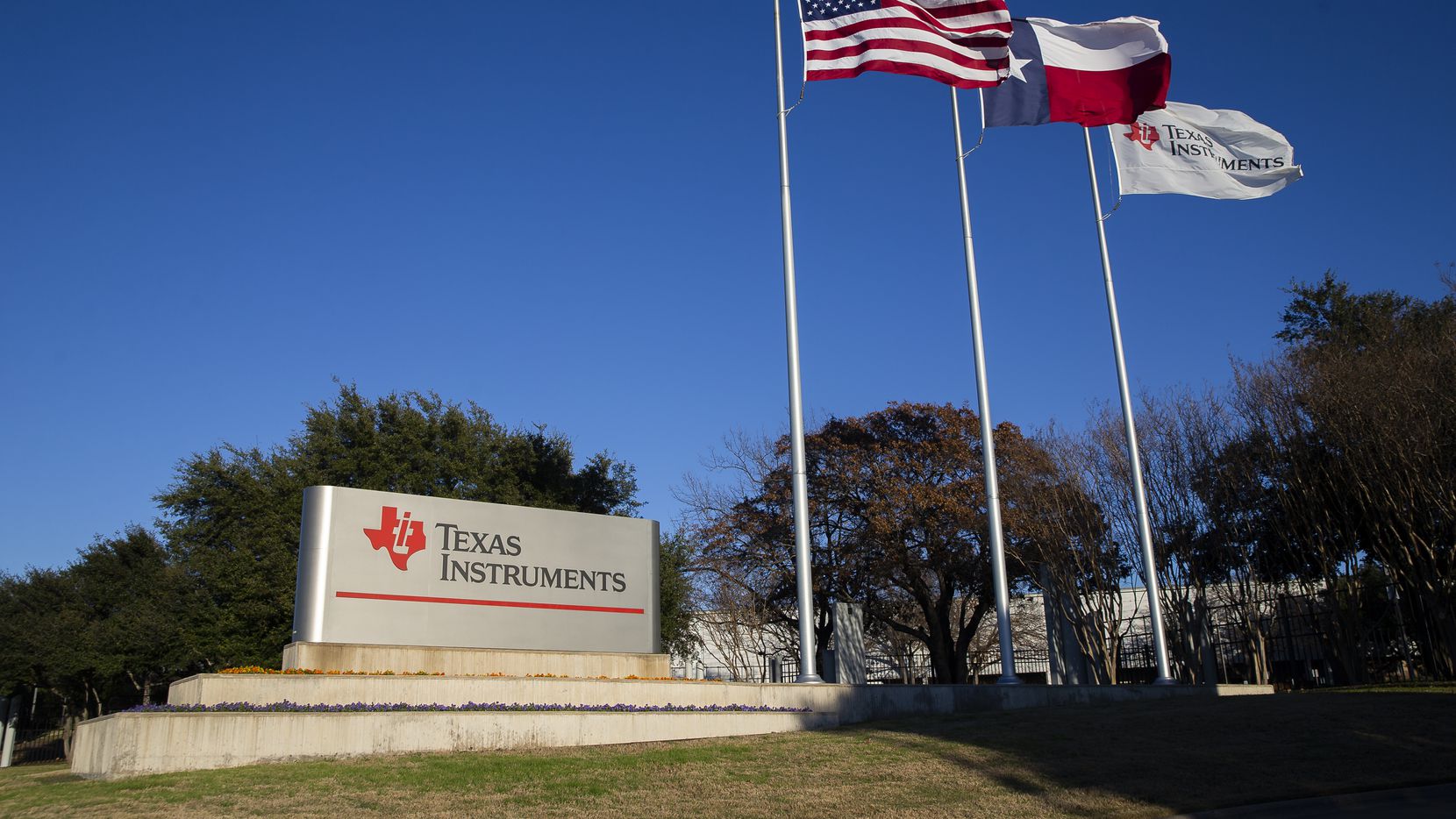
Maintenance engineers make between PS20,000 to PS25,000 an average. But salaries can vary depending on where you work, how big the company is, and what industry you are in. An engineer who is skilled in maintenance can be promoted to management positions. Career advancement may be possible with a Chartered status.
Certifications required
As a maintenance engineer, you may be required to hold several certifications. These certifications can be specific to one system or may relate to hazardous material handling. The International Maintenance Institute offers professional certification in several levels. These include certifications for Certified Technicians and Certified Maintenance Managers.
Consider your educational background before you consider becoming a maintenance technician. Although certification agencies don't require you to have any particular educational qualifications, some prefer that you have a highschool diploma or GED. Employers and recruiters typically require this minimum requirement. You can get a certification even if you don't have a degree, if you have worked in a similar field.
Although a bachelor's degree does not necessarily mean you can become a maintenance engineer or vice versa, a degree in a relevant field will make you stand out among the rest. A degree in electrical engineering, mechanical engineering, or facilities management may be useful. Even if you don't have an engineering degree, you may be able to find work as a maintenance technician or work your way up to the level of maintenance engineer with training and experience.
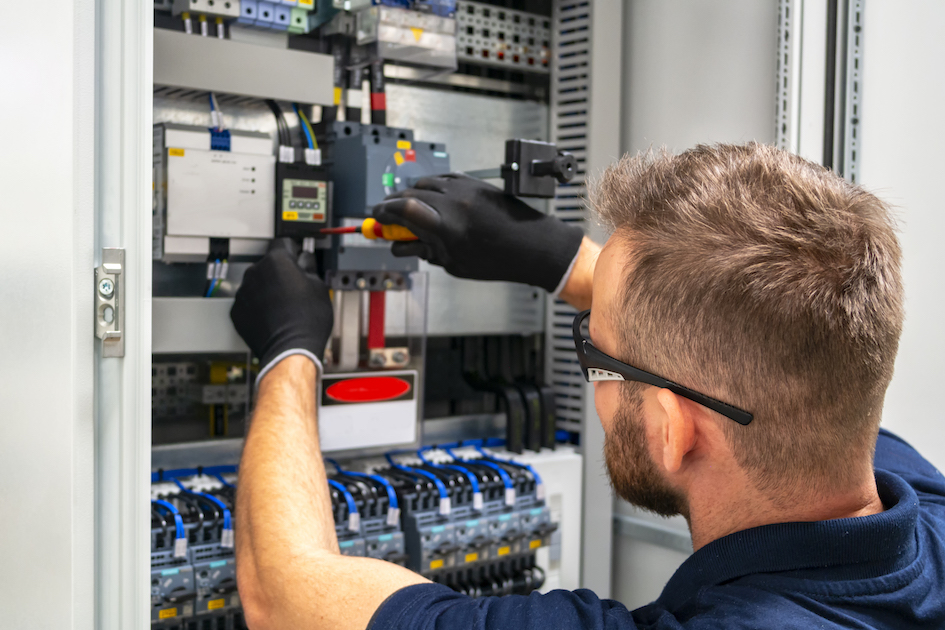
Salary
The Bureau of Labor Statistics does not monitor the salary of maintenance engineers, but job growth in related fields is projected. General maintenance workers and mechanical engineers will see a 8% increase, while construction managers could see an 11% increase in employment. Therefore, if you're considering a career as a maintenance engineer, you should focus on industries with high job growth, or look for entry-level positions within those industries.
Maintenance engineer salary: The 2008 median maintenance engineer salary was $88,570. The lowest 25% earned $48,270 while the highest 10% earned more than $110,000.
FAQ
What does manufacturing mean?
Manufacturing Industries are companies that manufacture products. These products are sold to consumers. These companies employ many processes to achieve this purpose, such as production and distribution, retailing, management and so on. They manufacture goods from raw materials using machines and other equipment. This includes all types if manufactured goods.
How does manufacturing avoid bottlenecks in production?
Avoiding production bottlenecks is as simple as keeping all processes running smoothly, from the time an order is received until the product ships.
This includes planning for capacity requirements as well as quality control measures.
This can be done by using continuous improvement techniques, such as Six Sigma.
Six Sigma can be used to improve the quality and decrease waste in all areas of your company.
It emphasizes consistency and eliminating variance in your work.
Do we need to know about Manufacturing Processes before learning about Logistics?
No. You don't have to know about manufacturing processes before learning about logistics. It is important to know about the manufacturing processes in order to understand how logistics works.
Statistics
- In 2021, an estimated 12.1 million Americans work in the manufacturing sector.6 (investopedia.com)
- It's estimated that 10.8% of the U.S. GDP in 2020 was contributed to manufacturing. (investopedia.com)
- According to a Statista study, U.S. businesses spent $1.63 trillion on logistics in 2019, moving goods from origin to end user through various supply chain network segments. (netsuite.com)
- You can multiply the result by 100 to get the total percent of monthly overhead. (investopedia.com)
- Job #1 is delivering the ordered product according to specifications: color, size, brand, and quantity. (netsuite.com)
External Links
How To
How to Use lean manufacturing in the Production of Goods
Lean manufacturing is an approach to management that aims for efficiency and waste reduction. It was developed by Taiichi Okono in Japan, during the 1970s & 1980s. TPS founder Kanji Takoda awarded him the Toyota Production System Award (TPS). Michael L. Watkins published the "The Machine That Changed the World", the first book about lean manufacturing. It was published in 1990.
Lean manufacturing can be described as a set or principles that are used to improve quality, speed and cost of products or services. It emphasizes the elimination of defects and waste throughout the value stream. Lean manufacturing is called just-in-time (JIT), zero defect, total productive maintenance (TPM), or 5S. Lean manufacturing is about eliminating activities that do not add value, such as inspection, rework, and waiting.
Lean manufacturing not only improves product quality but also reduces costs. Companies can also achieve their goals faster by reducing employee turnover. Lean Manufacturing is one of the most efficient ways to manage the entire value chains, including suppliers and customers as well distributors and retailers. Many industries worldwide use lean manufacturing. Toyota's philosophy has been a key driver of success in many industries, including automobiles and electronics.
Lean manufacturing is based on five principles:
-
Define Value - Identify the value your business adds to society and what makes you different from competitors.
-
Reduce Waste - Eliminate any activity that doesn't add value along the supply chain.
-
Create Flow - Ensure work moves smoothly through the process without interruption.
-
Standardize and simplify – Make processes as repeatable and consistent as possible.
-
Building Relationships – Establish personal relationships with both external and internal stakeholders.
Lean manufacturing isn’t new, but it has seen a renewed interest since 2008 due to the global financial crisis. Many businesses have adopted lean production techniques to make them more competitive. Some economists even believe that lean manufacturing can be a key factor in economic recovery.
Lean manufacturing, which has many benefits, is now a standard practice in the automotive industry. These include better customer satisfaction and lower inventory levels. They also result in lower operating costs.
It can be applied to any aspect of an organisation. This is because it ensures efficiency and effectiveness in all stages of the value chain.
There are three main types in lean manufacturing
-
Just-in Time Manufacturing, (JIT): This kind of lean manufacturing is also commonly known as "pull-systems." JIT is a process in which components can be assembled at the point they are needed, instead of being made ahead of time. This approach aims to reduce lead times, increase the availability of parts, and reduce inventory.
-
Zero Defects Manufacturing, (ZDM): ZDM is focused on ensuring that no defective products leave the manufacturing facility. It is better to repair a part than have it removed from the production line if it needs to be fixed. This is true even for finished products that only require minor repairs prior to shipping.
-
Continuous Improvement (CI: Continuous improvement aims to increase the efficiency of operations by constantly identifying and making improvements to reduce or eliminate waste. Continuous improvement involves continuous improvement of processes and people as well as tools.