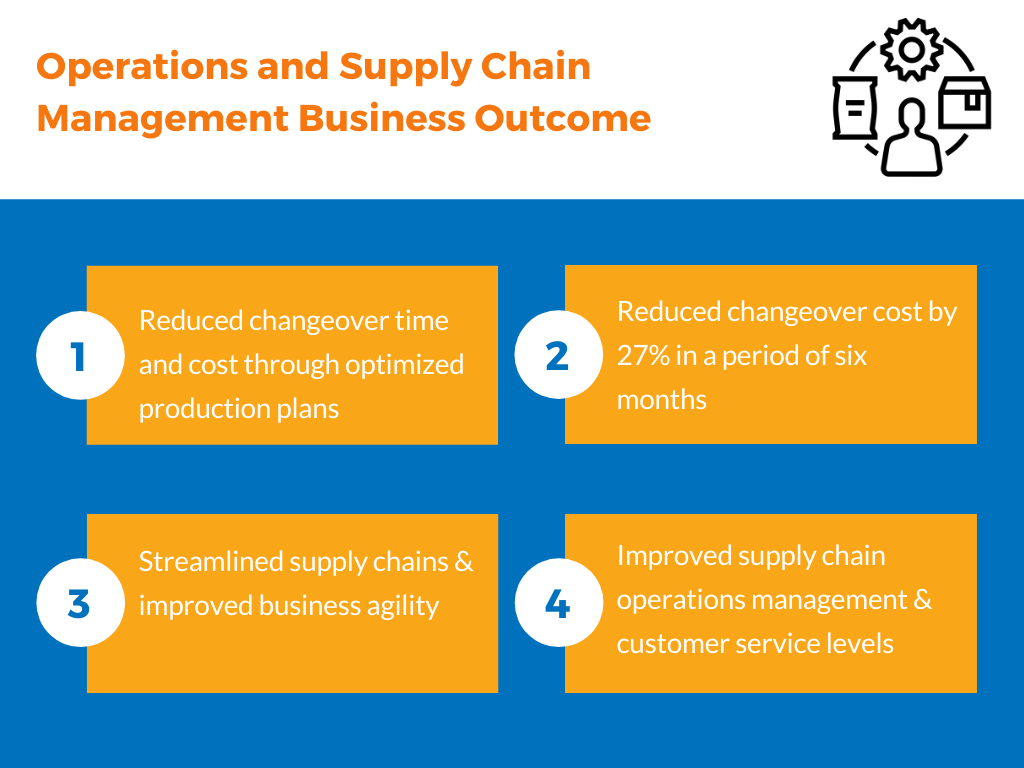
While value stream mapping is a way to improve your manufacturing process, it's not always easy. It involves mapping product family and products. It requires training for your team, and maybe even a value stream manager. Leadership should also support the implementation of your strategy. Larger companies have value stream managers who are responsible for the mapping process. Although smaller companies may be able to do without a VSM manager it is beneficial to communicate with the leadership about the potential improvements.
Lean Six Sigma
Value Stream Mapping in Lean Six Sigma will allow you to document the flow information from customers to suppliers. Your customer is the first thing you should put on your value streammap. If you're in the shipping area, start there and work upstream. Include a box with customer data. This will let you know how often products must be produced to meet demand. It is also important to determine the Takt time, which is the time taken to produce a product and how it compares to its cycle time. If Takt is longer than the cycle times, it means that there is a bottleneck.
Value stream maps can be used to help companies identify and eliminate waste in every stage of their business processes. Value stream mapping is a way to identify non-value-added activities, analyze the flow of information and identify threats and opportunities in your business. It's also a useful tool to identify bottlenecks, and where improvements can be made in order to make the process more efficient. The benefits of using Value Stream Mapping in Lean Six Sigma go beyond simply improving the flow of information - a Value Stream Map can be a valuable tool in helping you implement Lean Six Sigma and improve your bottom line.
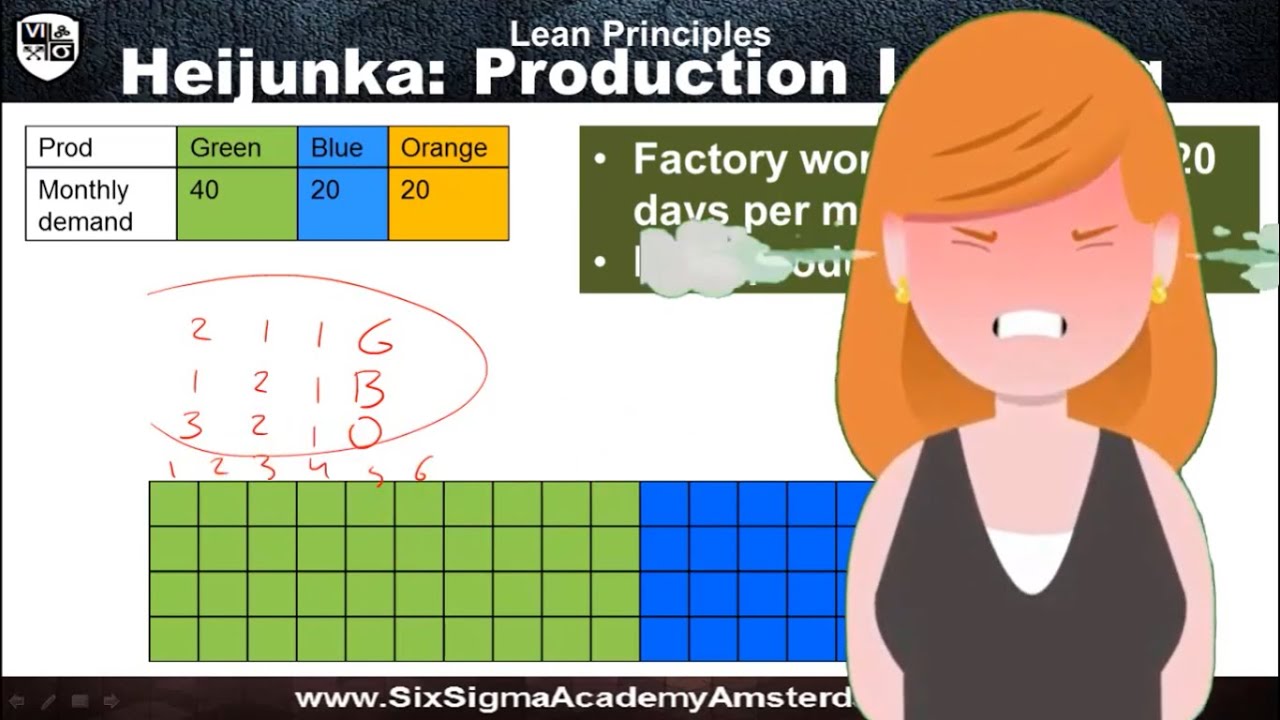
Lean Healthcare
Value stream mapping allows for better synchronization in the medical industry. It helps identify areas that need improvement and recommends ways to implement them. A map could show a patient's flow, from their arrival at the hospital to when they leave after treatment. These flow paths can be used to visualize the entire process and help identify value-added and waste-generating actions.
In order to make VSM in Lean Healthcare more effective, the authors recommend setting up clear definitions of the terms used in the process. They also recommend establishing appropriate indicators and sharing examples of success and failure. This allows the results to be repeated and can be adapted for different situations. Lean methodologies in the healthcare sector are more likely to produce positive outcomes. To ensure that the benefits of this methodology are felt throughout the health care system, the authors suggest establishing a common definition of value stream mapping in the healthcare industry.
Lean Manufacturing
It is crucial to get input from all stakeholders involved in a value stream mapping process before you can begin. This team should include the people responsible for fulfilling customer needs. They should also include people who perform critical tasks and activities to ensure the flow of information. By gathering input from these key stakeholders, value stream mapping can help identify waste, and ultimately improve efficiency. Define the scope of the value-stream mapping process.
Next, pick the product or the process that you want to improve. Finally, teach the team about value stream mapping. The mapping process starts with the customer's needs and covers all aspects of the decision-making, communication and communications processes. Value stream mapping helps to reduce waste and improve customer satisfaction. By identifying the elements that contribute to customer satisfaction and removing them, lean manufacturing can become a viable, sustainable solution for the challenges facing any company.
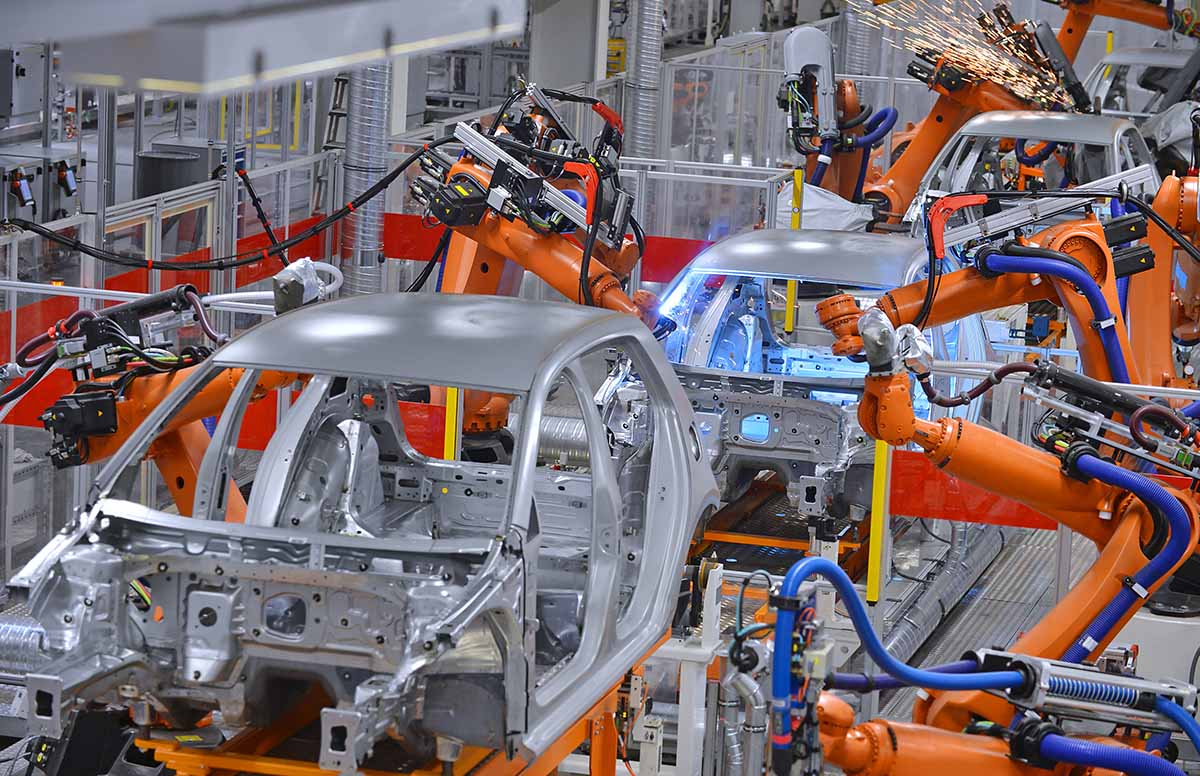
Future state value stream mapping
Future state value streaming mapping is an excellent tool to identify waste. This mapping has two goals: to identify and eliminate the causes of waste. Future state ideas are marked using the same symbols that current state mapping. Takt Time is a key concept in future state value stream mapping. It allows you to efficiently allocate resources and to identify waste areas. A future state value stream chart can be an effective tool for your company.
Once you have determined the root causes of the problems, and the relationship with the future state, you can map the steps required to get there. A future state map can be a constant point of reference for teams to reference as they complete projects and reach the target value. It is important to update your future stream mapping of state value every six to twelve mois to ensure that you are able to monitor your progress. You should update your future state map as new projects are launched and modifications made.
FAQ
Is automation necessary in manufacturing?
Automating is not just important for manufacturers, but also for service providers. It enables them to provide services faster and more efficiently. It also helps to reduce costs and improve productivity.
What is the job of a logistics manger?
A logistics manager ensures that all goods are delivered on time and without damage. This is done by using his/her experience and knowledge of the company's products. He/she also needs to ensure adequate stock to meet demand.
What do you mean by warehouse?
A warehouse, or storage facility, is where goods are stored prior to being sold. It can be an outdoor or indoor area. It may also be an indoor space or an outdoor area.
How can manufacturing efficiency improved?
The first step is to determine the key factors that impact production time. We must then find ways that we can improve these factors. If you don’t know how to start, look at which factors have the greatest impact upon production time. Once you've identified them, try to find solutions for each of those factors.
Why automate your warehouse
Modern warehouses are increasingly dependent on automation. E-commerce has brought increased demand for more efficient and quicker delivery times.
Warehouses must adapt quickly to meet changing customer needs. Technology investment is necessary to enable warehouses to respond quickly to changing demands. The benefits of automating warehouses are numerous. Here are some reasons why it's worth investing in automation:
-
Increases throughput/productivity
-
Reduces errors
-
Increases accuracy
-
Safety increases
-
Eliminates bottlenecks
-
This allows companies to scale easily
-
This makes workers more productive
-
Provides visibility into everything that happens in the warehouse
-
Enhances customer experience
-
Improves employee satisfaction
-
This reduces downtime while increasing uptime
-
This ensures that quality products are delivered promptly
-
Eliminates human error
-
It ensures compliance with regulations
What are the 7 R's of logistics?
The acronym "7R's" of Logistics stands for seven principles that underpin logistics management. It was developed and published by the International Association of Business Logisticians in 2004 as part of the "Seven Principles of Logistics Management".
The following letters make up the acronym:
-
Responsible - to ensure that all actions are within the legal requirements and are not detrimental to others.
-
Reliable - Have confidence in your ability to fulfill all of your commitments.
-
Be responsible - Use resources efficiently and avoid wasting them.
-
Realistic – consider all aspects of operations, from cost-effectiveness to environmental impact.
-
Respectful - Treat people fairly and equitably
-
Responsive - Look for ways to save time and increase productivity.
-
Recognizable provides value-added products and services to customers
Statistics
- According to the United Nations Industrial Development Organization (UNIDO), China is the top manufacturer worldwide by 2019 output, producing 28.7% of the total global manufacturing output, followed by the United States, Japan, Germany, and India.[52][53] (en.wikipedia.org)
- (2:04) MTO is a production technique wherein products are customized according to customer specifications, and production only starts after an order is received. (oracle.com)
- In the United States, for example, manufacturing makes up 15% of the economic output. (twi-global.com)
- Job #1 is delivering the ordered product according to specifications: color, size, brand, and quantity. (netsuite.com)
- You can multiply the result by 100 to get the total percent of monthly overhead. (investopedia.com)
External Links
How To
How to Use 5S to Increase Productivity in Manufacturing
5S stands for "Sort", "Set In Order", "Standardize", "Separate" and "Store". Toyota Motor Corporation developed the 5S method in 1954. It improves the work environment and helps companies to achieve greater efficiency.
This method has the basic goal of standardizing production processes to make them repeatable. It means tasks like cleaning, sorting or packing, labeling, and storing are done every day. This knowledge allows workers to be more efficient in their work because they are aware of what to expect.
There are five steps to implementing 5S, including Sort, Set In Order, Standardize, Separate and Store. Each step requires a different action, which increases efficiency. If you sort items, it makes them easier to find later. You arrange items by placing them in an order. Then, after you separate your inventory into groups, you store those groups in containers that are easy to access. Make sure everything is correctly labeled when you label your containers.
Employees need to reflect on how they do their jobs. Employees must be able to see why they do what they do and find a way to achieve them without having to rely on their old methods. They must learn new skills and techniques in order to implement the 5S system.
The 5S method not only increases efficiency but also boosts morale and teamwork. They will feel motivated to strive for higher levels of efficiency once they start to see results.