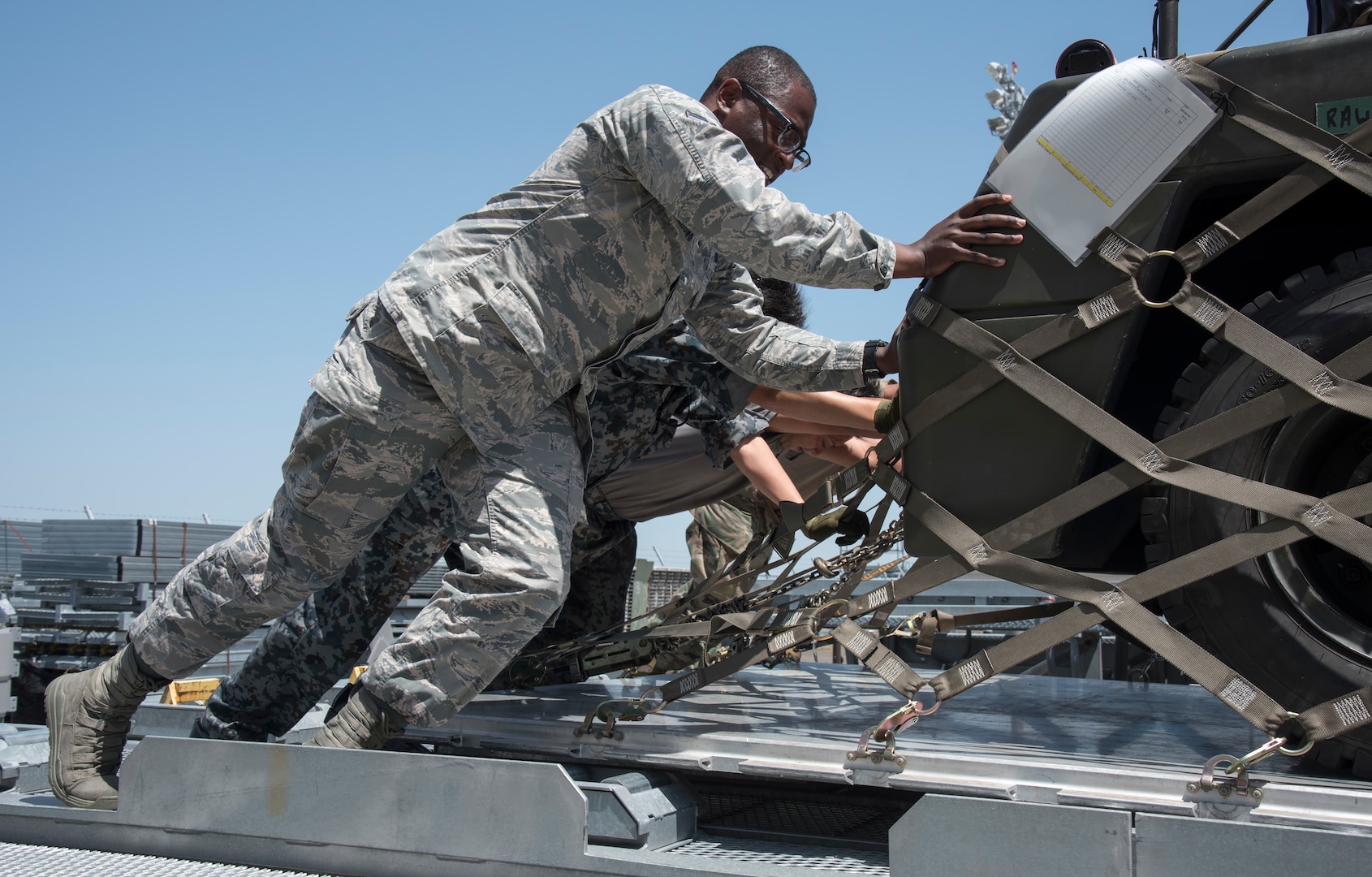
Flow describes the state of being in which all steps of a manufacturing process flow seamlessly without interruption. Each step adds value and the goods flow freely through the production process. A lot of companies plan the production of a particular quantity of stock so that production orders can easily be fulfilled. This is Lean Manufacturing's term for "push" production. These are the main elements of flow:
Just-in-time manufacturing
When lean manufacturing was first introduced to the U.S. in the late 1970s, "just-in-time" manufacturing was the dominant paradigm. Although it offers many benefits, it is not the best method to manage a company. Many new skills and mindsets are required to lower costs and improve efficiency. It is worth the effort if you are to reap all of its benefits.
Standardization and the ability to work with smaller lots are some of the key elements of just-in–time manufacturing. It is crucial to have a well-planned facility layout in order to promote a just-in time mindset. Cellular manufacturing, by example, can improve production flow. Workstations and parts bins can be organized in cells that ensure smoother flow of materials. Just-in-time producers should avoid lengthy changeovers.
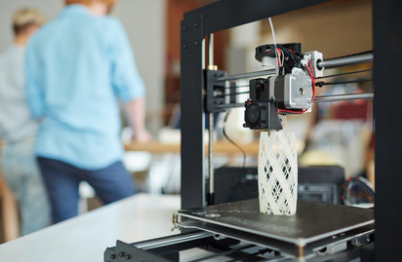
Standardized work
First, you have to create standardized work before applying lean manufacturing in manufacturing processes. This system of work focuses on the workers and what they must do to create a product or service. This refers to the ongoing improvement of the system through kaizen. The cell leader is responsible for standardizing work documents and they are automatically updated as takt times change. Standardized work documentation provides a base for improvement activities, including kaizen and improvement activities.
Standardized work processes help improve service quality and productivity. They reduce product development time and reduce human error. Because people are more familiar with the process, it allows the organization to solve problems quicker. This allows the organization to increase customer satisfaction and continuous improvement. These processes are easy to implement in a company once they have been established. A mission statement is a great idea.
Continuous improvement
Lean principles foster continuous improvement which leads to many benefits. These benefits are usually additive, but one thread links them all: increased productivity, lower costs, and shorter lead times. Lean continuous improvement is about increasing value creation. How does continuous improvement work? This article will show you some of the benefits of continuous improvement. It's simple: Continuous Improvement helps companies save money.
In continuous improvement, a company focuses on incremental improvements rather than sweeping changes. Although individual improvements are small and seem insignificant, the total improvement is substantial. This slow process is more about small steps than making huge leaps. Continuous improvement in lean manufacturing environments focuses on aligning goals. This helps the business achieve maximum productivity and profitability. Continuous improvement methods allow for a simplified production process, so that all processes work together in order to achieve a common goal.
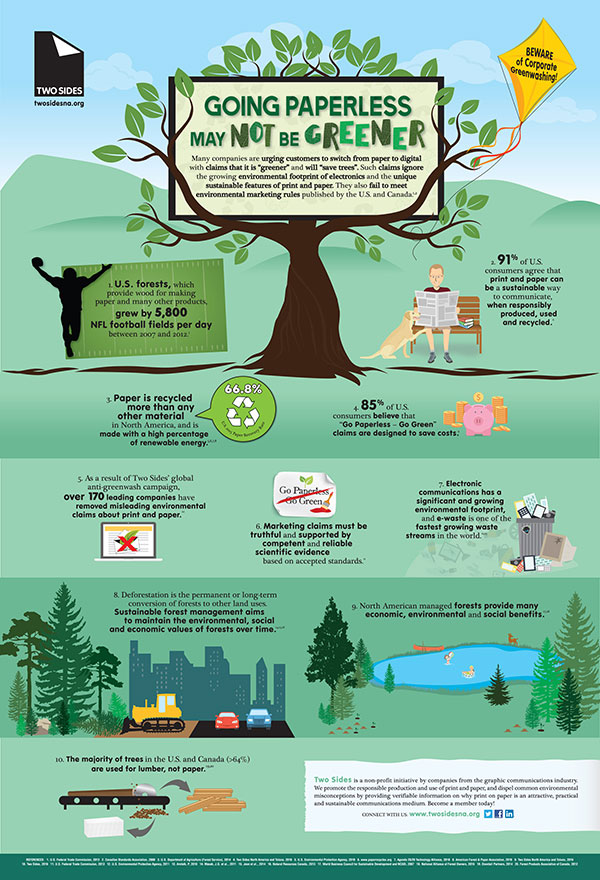
Kaizen
Kaizen in lean manufacturing is about reducing waste. Sometimes it can improve production yield, decrease lead times, and improve quality. A team of employees is assigned a specific role to study the problem and propose solutions. The process of creating a value stream map for kaizen usually begins with the creation. Next, the team conducts time analyses of all relevant operations. The process continues until each step is improved, and the overall process becomes more efficient.
A manufacturing plant might purchase a new forklift after identifying inefficiencies. Its operator could move inventory around to make loading/unloading more efficient. Similar to the value stream it's a map showing all the processes that go into creating products and services. During the mapping process, five different S's are used to increase employee productivity and workplace practices. There are seven types. Each type focuses upon a different aspect in a manufacturing process.
FAQ
What jobs are available in logistics?
There are different kinds of jobs available in logistics. These are some of the jobs available in logistics:
-
Warehouse workers - They load trucks and pallets.
-
Transport drivers - These are people who drive trucks and trailers to transport goods or perform pick-ups.
-
Freight handlers are people who sort and pack freight into warehouses.
-
Inventory managers – These people oversee inventory at warehouses.
-
Sales representatives - They sell products to customers.
-
Logistics coordinators: They plan and manage logistics operations.
-
Purchasing agents - They purchase goods and services needed for company operations.
-
Customer service representatives - Answer calls and email from customers.
-
Shipping clerks – They process shipping orders, and issue bills.
-
Order fillers: They fill orders based off what has been ordered and shipped.
-
Quality control inspectors (QCI) - They inspect all incoming and departing products for potential defects.
-
Others - There is a variety of other jobs in logistics. These include transportation supervisors and cargo specialists.
What are the responsibilities of a logistic manager?
Logistics managers make sure all goods are delivered on schedule and without damage. This is done by using his/her experience and knowledge of the company's products. He/she should ensure that sufficient stock is available in order to meet customer demand.
What are the responsibilities for a manufacturing manager
A manufacturing manager must ensure that all manufacturing processes are efficient and effective. They should also be aware and responsive to any company problems.
They should also know how to communicate with other departments such as sales and marketing.
They should be up to date on the latest trends and be able apply this knowledge to increase productivity and efficiency.
Statistics
- You can multiply the result by 100 to get the total percent of monthly overhead. (investopedia.com)
- It's estimated that 10.8% of the U.S. GDP in 2020 was contributed to manufacturing. (investopedia.com)
- [54][55] These are the top 50 countries by the total value of manufacturing output in US dollars for its noted year according to World Bank.[56] (en.wikipedia.org)
- In the United States, for example, manufacturing makes up 15% of the economic output. (twi-global.com)
- (2:04) MTO is a production technique wherein products are customized according to customer specifications, and production only starts after an order is received. (oracle.com)
External Links
How To
How to Use the Just In Time Method in Production
Just-in-time (JIT) is a method that is used to reduce costs and maximize efficiency in business processes. This is where you have the right resources at the right time. This means you only pay what you use. Frederick Taylor developed the concept while working as foreman in early 1900s. He observed how workers were paid overtime if there were delays in their work. He decided to ensure workers have enough time to do their jobs before starting work to improve productivity.
JIT is about planning ahead. You should have all the necessary resources ready to go so that you don’t waste money. Look at your entire project, from start to end. Make sure you have enough resources in place to deal with any unexpected problems. If you anticipate that there might be problems, you'll have enough people and equipment to fix them. This way you won't be spending more on things that aren’t really needed.
There are many JIT methods.
-
Demand-driven: This JIT is where you place regular orders for the parts/materials that are needed for your project. This will allow to track how much material has been used up. This will allow to you estimate the time it will take for more to be produced.
-
Inventory-based: This is a type where you stock the materials required for your projects in advance. This allows for you to anticipate how much you can sell.
-
Project-driven: This approach involves setting aside sufficient funds to cover your project's costs. You will be able to purchase the right amount of materials if you know what you need.
-
Resource-based JIT: This type of JIT is most commonly used. You assign certain resources based off demand. For instance, if you have a lot of orders coming in, you'll assign more people to handle them. If you don’t have many orders you will assign less people to the work.
-
Cost-based: This is similar to resource-based, except that here you're not just concerned about how many people you have but how much each person costs.
-
Price-based: This is similar to cost-based but instead of looking at individual workers' salaries, you look at the total company price.
-
Material-based: This approach is similar to cost-based. However, instead of looking at the total cost for the company, you look at how much you spend on average on raw materials.
-
Time-based JIT is another form of resource-based JIT. Instead of focusing only on how much each employee is costing, you should focus on how long it takes to complete your project.
-
Quality-based JIT: Another variation on resource-based JIT. Instead of looking at the labor costs and time it takes to make a product, think about its quality.
-
Value-based: This is one of the newest forms of JIT. In this scenario, you're not concerned about how products perform or whether customers expect them to meet their expectations. Instead, you focus on the added value that you provide to your market.
-
Stock-based: This inventory-based approach focuses on how many items are being produced at any one time. It is used when production goals are met while inventory is kept to a minimum.
-
Just-in time (JIT), planning: This is a combination JIT/supply chain management. It is the process that schedules the delivery of components within a short time of their order. It reduces lead times and improves throughput.