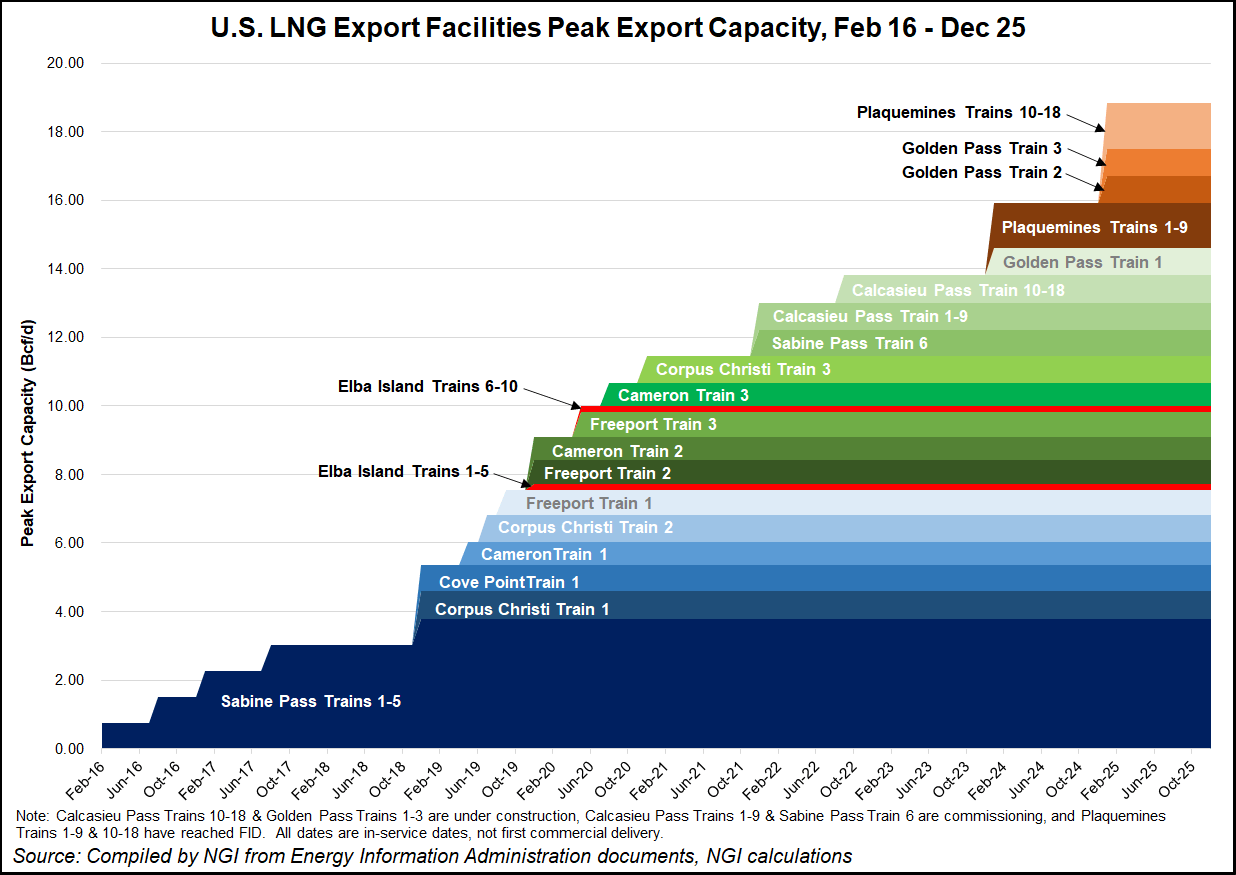
DFSS is a design technique that uses a variety to design a product. Its purpose is to reduce waste and improve quality while increasing market share. This is a proven method to improve your products or services.
DFSS is a process where customer needs are considered throughout the design process. This ensures the product or service that you design meets your customer's requirements. It ensures that your product meets high standards when it is launched to the marketplace. DFSS is used often to design a product/service from scratch. You can also use it to create products and services to replace existing products.
In the first phase, the DFSS team determines what the customer needs and wants. This can include gathering information on existing processes, interviewing customers, and surveying customers. The design team then evaluates alternative products and designs to find the best fit. This includes the development or modification of substitute ideas and defining functional requirements. Depending on the complexity of the project, the phase may include additional steps.
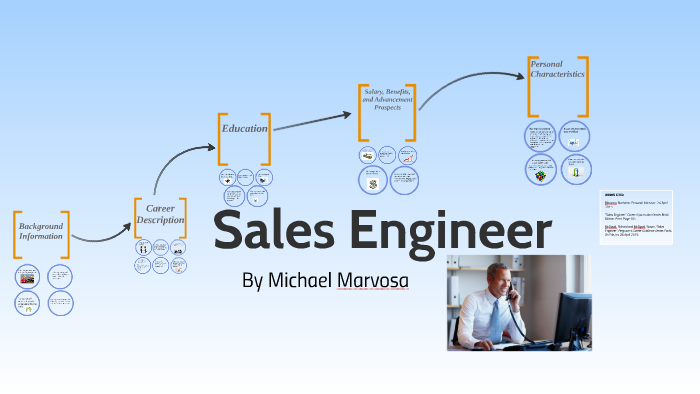
DFSS, a design methodology, is used to help companies design products or services efficiently and effectively. It's also used to identify potential problems and prevent them from becoming serious issues. It will also reduce waste and increase your company's profitability. Its aim is to increase the effectiveness of a product or service by identifying process parameters that make it more effective.
There are different methodologies for implementing DFSS. DMADV is one of the most widely used methods. This involves a five step process. It starts with defining the customer, identifying their needs, and developing a design concept. This method is based on solid engineering principles and is used often to develop completely new products or services. It also includes a measurement-and-analysis phase to assess the product’s performance.
Optimization is the next phase. This involves evaluating the product's performance at multiple levels. This step is crucial for the development of new business procedures. This stage has two goals: to reduce variability, and to ensure the product is stable over time.
The final stage of the verification process is where the product is verified to be stable. This stage also validates that the product is capable of performing over time. This process also includes validation testing. After the design is validated, validation testing is often completed.
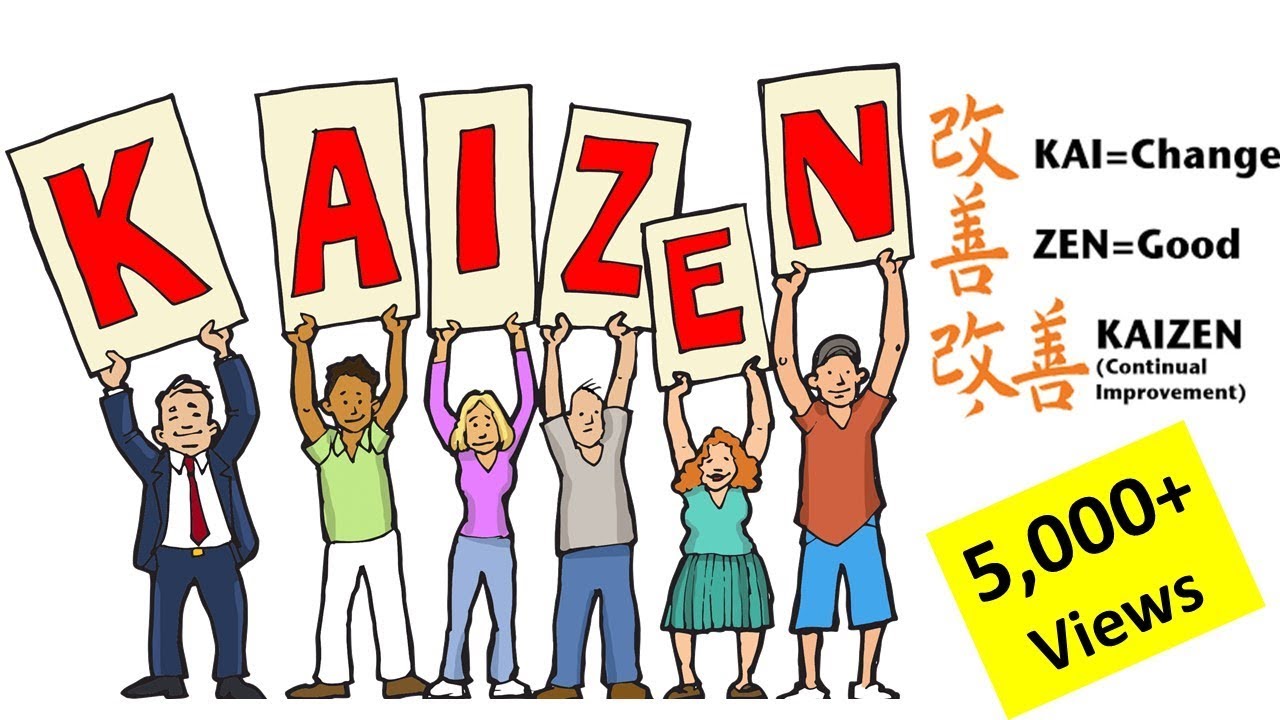
In order to successfully implement DFSS, you need to have a detailed process map that shows the different workflows involved in the design process. A detailed process map should contain information about resources, timeframes, milestones, as well as details about the budget. You should also be able to identify any external involvement that may be required. A prototype may be needed to verify that the product meets the customer's requirements. It is also beneficial to implement DFSS within an environment that offers clear rewards for achieving the goals of your project.
FAQ
Is it necessary to be familiar with Manufacturing Processes before we learn about Logistics.
No. It doesn't matter if you don't know anything about manufacturing before you learn about logistics. Knowing about manufacturing processes will help you understand how logistics works.
How can I learn about manufacturing?
Hands-on experience is the best way to learn more about manufacturing. You can also read educational videos or take classes if this isn't possible.
What is the job of a production plan?
Production planners ensure all aspects of the project are delivered within time and budget. They ensure that the product or service is of high quality and meets client requirements.
Statistics
- (2:04) MTO is a production technique wherein products are customized according to customer specifications, and production only starts after an order is received. (oracle.com)
- Job #1 is delivering the ordered product according to specifications: color, size, brand, and quantity. (netsuite.com)
- In the United States, for example, manufacturing makes up 15% of the economic output. (twi-global.com)
- [54][55] These are the top 50 countries by the total value of manufacturing output in US dollars for its noted year according to World Bank.[56] (en.wikipedia.org)
- According to a Statista study, U.S. businesses spent $1.63 trillion on logistics in 2019, moving goods from origin to end user through various supply chain network segments. (netsuite.com)
External Links
How To
How to Use 5S for Increasing Productivity in Manufacturing
5S stands in for "Sort", the "Set In Order", "Standardize", or "Separate". The 5S methodology was developed at Toyota Motor Corporation in 1954. It helps companies achieve higher levels of efficiency by improving their work environment.
This approach aims to standardize production procedures, making them predictable, repeatable, and easily measurable. This means that daily tasks such as cleaning and sorting, storage, packing, labeling, and packaging are possible. Because workers know what they can expect, this helps them perform their jobs more efficiently.
Implementing 5S involves five steps: Sort, Set in Order, Standardize Separate, Store, and Each step requires a different action, which increases efficiency. For example, when you sort things, you make them easy to find later. Once you have placed items in an ordered fashion, you will put them together. You then organize your inventory in groups. Labeling your containers will ensure that everything is correctly labeled.
Employees must be able to critically examine their work practices. Employees need to be able understand their motivations and discover alternative ways to do them. They will need to develop new skills and techniques in order for the 5S system to be implemented.
The 5S method not only increases efficiency but also boosts morale and teamwork. They feel more motivated to work towards achieving greater efficiency as they see the results.