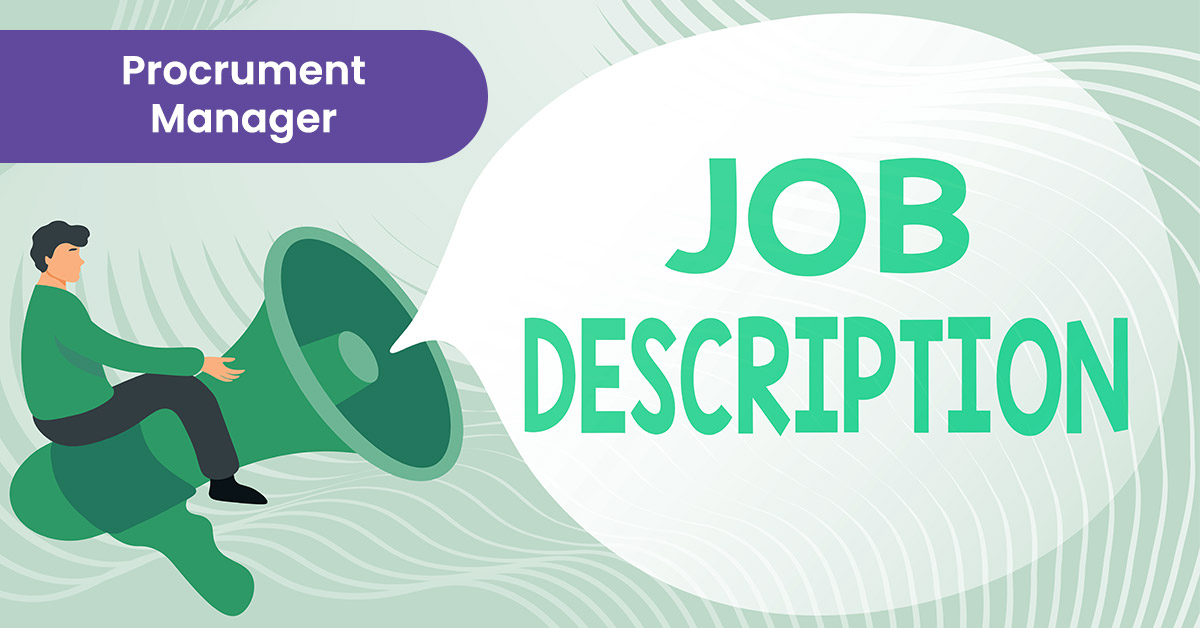
For industrial engineers, you will need strong math skills, knowledge of physical science and the ability to solve problems. These individuals can work in different sectors, including manufacturing, construction, and health care. They could work in an office or on the factory floor.
Industrial engineers analyze production processes, develop manufacturing techniques, and improve efficiency. They can also design quality control procedures. They may also be responsible for creating manufacturing standards and training staff. Individuals who are interested to become industrial engineers must be willing and able to collaborate with others. They must also be motivated to increase efficiency and streamline processes. They should have strong leadership and communication skills. They should also be adept at problem solving.
Industrial engineers can create cost analysis tools and help robots run more efficiently. They also use data analysis to determine if processes have been optimized. They could also be responsible for developing manufacturing standards and design guidelines. They will develop procedures for equipment, inventory control, and create documentation. They can also present their plans orally or in written reports.
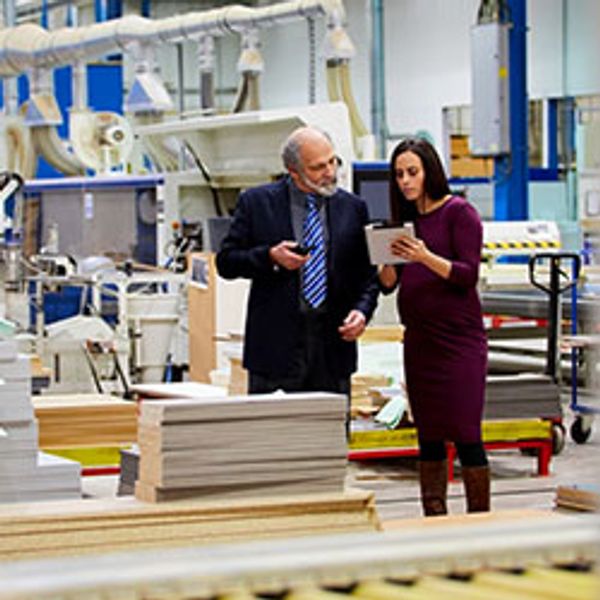
Industrial engineers are employed in offices, warehouses, manufacturing plants and may travel to client sites. They might work in noisy or cramped environments. They may need to wear protective safety clothes. Sometimes they will need to work more than normal in order to meet production deadlines.
The industrial engineer is responsible for the design and implementation process, assuring that it runs efficiently and producing high-quality products. They may also be responsible for solving production problems. Some industrial engineers can also start manufacturing businesses. They may also have to train new employees and make sure they understand how to work properly. They may also have to make sure that raw materials meet quality standards before they are used in manufacturing.
The industrial engineer works with other departments to develop integrated systems that manage industrial production. They may be specialists in one engineering field. They may be required to work in an unorganized or noisy environment. They may need to travel to warehouses or construction sites to gather data, and they may have to work with other professionals to find solutions to manufacturing problems.
An education or work experience can help industrial engineers move up to managerial positions. They might open their own consultancy firms or become technical specialists in a particular field. They might also be skilled in facility planning or quality control. They could also be responsible in designing production layouts. They could also be responsible in developing wage and pay administration systems. They may also be responsible scheduling deliveries based in production forecasts, storage, handling, and maintenance requirements. They may also travel to perform administrative tasks. They may also supervise technicians.
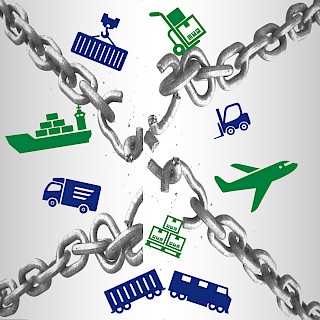
Industrial engineers might work for a company or as consultants. They may work a standard 40-hour work week or more, depending on the company's needs. If they are providing technical support to businesses, they might work up to 40 hours per week in a consulting company.
FAQ
What is the responsibility of a production planner?
Production planners make sure that every aspect of the project is delivered on-time, within budget, and within schedule. They ensure that the product or service is of high quality and meets client requirements.
What is the difference between Production Planning, Scheduling and Production Planning?
Production Planning (PP) refers to the process of determining how much production is needed at any given moment. This is accomplished by forecasting the demand and identifying production resources.
Scheduling is the process of assigning specific dates to tasks so they can be completed within the specified timeframe.
How can manufacturing overproduction be reduced?
It is essential to find better ways to manage inventory to reduce overproduction. This would reduce the time needed to manage inventory. We could use these resources to do other productive tasks.
One way to do this is to adopt a Kanban system. A Kanban board is a visual display used to track work in progress. A Kanban system allows work items to move through several states before reaching their final destination. Each state is assigned a different priority.
To illustrate, work can move from one stage or another when it is complete enough for it to be moved to a new stage. If a task is still in its beginning stages, it will continue to be so until it reaches the end.
This allows for work to continue moving forward, while also ensuring that there is no work left behind. A Kanban board allows managers to monitor how much work is being completed at any given moment. This information allows managers to adjust their workflow based off real-time data.
Lean manufacturing can also be used to reduce inventory levels. Lean manufacturing seeks to eliminate waste from every step of the production cycle. Anything that doesn't add value to the product is considered waste. These are some of the most common types.
-
Overproduction
-
Inventory
-
Unnecessary packaging
-
Overstock materials
These ideas will help manufacturers increase efficiency and lower costs.
Is automation necessary in manufacturing?
Automation is important not only for manufacturers but also for service providers. Automation allows them to deliver services quicker and more efficiently. They can also reduce their costs by reducing human error and improving productivity.
What is production planning?
Production Planning is the creation of a plan to cover all aspects, such as scheduling, budgeting. Location, crew, equipment, props and other details. This document is designed to make sure everything is ready for when you're ready to shoot. This document should include information about how to achieve the best results on-set. This information includes locations, crew details and equipment requirements.
The first step is to decide what you want. You may have already chosen the location you want, or there are locations or sets you prefer. Once you have identified your locations and scenes, you can start working out which elements you require for each scene. For example, you might decide that you need a car but don't know exactly what model you want. To narrow your options, you can search online for available models.
Once you have found the right car, you can start thinking about extras. Do you need people sitting in the front seats? Maybe you need someone to move around in the back. Maybe you'd like to change the interior from black to a white color. These questions can help you decide the right look for your car. It is also worth considering the types of shots that you wish to take. What type of shots will you choose? Maybe you want the engine or the steering wheels to be shown. These factors will help you determine which car style you want to film.
Once you've determined the above, it is time to start creating a calendar. You can use a schedule to determine when and where you need it to be shot. The schedule will show you when to get there, what time to leave, and when to return home. Everyone knows exactly what they should do and when. You can also make sure to book extra staff in advance if you have to hire them. There is no point in hiring someone who won't turn up because you didn't let him know.
You will need to factor in the days that you have to film when creating your schedule. Some projects may only take a couple of days, while others could last for weeks. While creating your schedule, it is important to remember whether you will require more than one shot per day. Multiple takes of the same location will lead to higher costs and take more time. It is better to be cautious and take fewer shots than you risk losing money if you are not sure if multiple takes are necessary.
Another important aspect of production planning is setting budgets. You will be able to manage your resources if you have a realistic budget. If you have to reduce your budget due to unexpected circumstances, you can always lower it later. However, you shouldn't overestimate the amount of money you will spend. You'll end up with less money after paying for other things if the cost is underestimated.
Planning production is a tedious process. Once you have a good understanding of how everything works together, planning future projects becomes easy.
What are the 4 types manufacturing?
Manufacturing is the process of transforming raw materials into useful products using machines and processes. It includes many different activities like designing, building and testing, packaging, shipping and selling, as well as servicing.
Statistics
- According to a Statista study, U.S. businesses spent $1.63 trillion on logistics in 2019, moving goods from origin to end user through various supply chain network segments. (netsuite.com)
- Job #1 is delivering the ordered product according to specifications: color, size, brand, and quantity. (netsuite.com)
- It's estimated that 10.8% of the U.S. GDP in 2020 was contributed to manufacturing. (investopedia.com)
- Many factories witnessed a 30% increase in output due to the shift to electric motors. (en.wikipedia.org)
- (2:04) MTO is a production technique wherein products are customized according to customer specifications, and production only starts after an order is received. (oracle.com)
External Links
How To
Six Sigma in Manufacturing
Six Sigma can be described as "the use of statistical process control (SPC), techniques to achieve continuous improvement." Motorola's Quality Improvement Department created Six Sigma at their Tokyo plant, Japan in 1986. Six Sigma's core idea is to improve the quality of processes by standardizing and eliminating defects. Since there are no perfect products, or services, this approach has been adopted by many companies over the years. Six Sigma's main objective is to reduce variations from the production average. It is possible to measure the performance of your product against an average and find the percentage of time that it differs from the norm. If this deviation is too big, you know something needs fixing.
The first step toward implementing Six Sigma is understanding how variability works in your business. Once you have a good understanding of the basics, you can identify potential sources of variation. Also, you will need to identify the sources of variation. Random variations are caused by human errors. Systematic variations can be caused by outside factors. For example, if you're making widgets, and some of them fall off the assembly line, those would be considered random variations. It would be considered a systematic problem if every widget that you build falls apart at the same location each time.
Once you identify the problem areas, it is time to create solutions. This could mean changing your approach or redesigning the entire process. Test them again once you've implemented the changes. If they don't work, you will need to go back to the drawing boards and create a new plan.