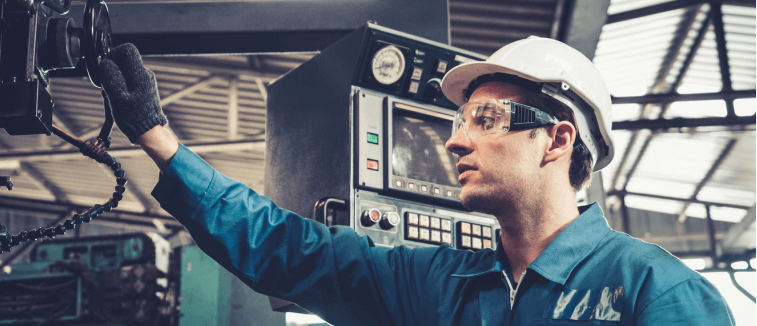
A degree in either architecture or engineering is required to be an engineer or architect manager. Although many of these professionals work in an office, others work on construction sites. The majority hold a bachelor’s degree in either architecture or engineering as well as extensive industry experience. A few choose to obtain a master's degree in business administration as an addition to their education. There are many options for advancement within this profession. Consider a MBA to help you get a job as an architect or engineer manager.
Perspective for engineers and architects
It is a good time to be an engineer or architect manager. The number of available jobs is expected to rise by two percent in the next ten years. This increase will reflect the growth of various industries. However, the competition for available jobs is fierce. For more information on the career outlook for this field, see the O*NET website.
Managers in engineering and architecture plan and direct the activities of an engineering or architect company. They use their architectural knowledge to plan, design the construction and manage many activities. These activities could include the design, building, maintenance and repair of large buildings, engineering research sites, or manufacturing facilities. They are also responsible in the conceptual design of new products. This requires them to identify the desired technical goals and create detailed plans that will help the company meet these goals.
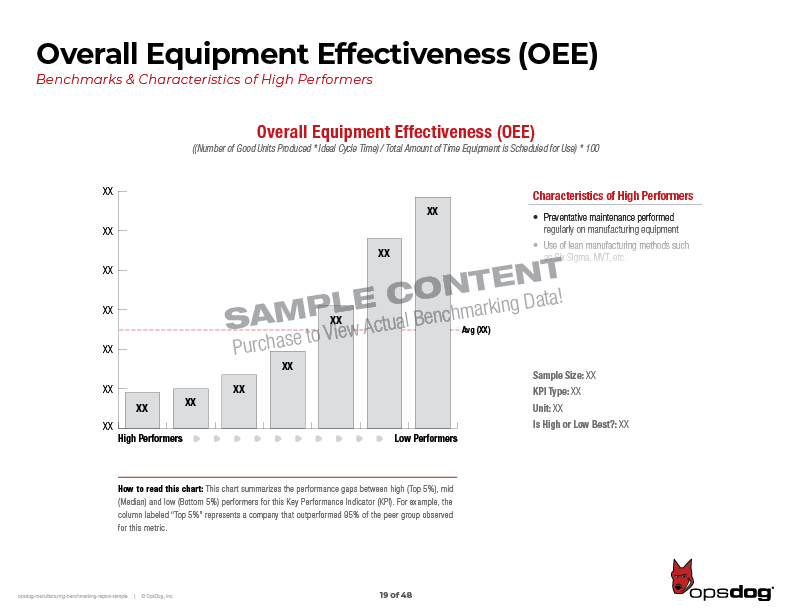
Most applicants for this job require at least a master’s degree in management. The best graduate-level program depends on the type of management position you want. A master's in engineering can prepare you to work as a manager, while a masters in business administration will help you develop more managerial skills. Both types of graduate programs take at least one year to complete.
Education is required
Engineer and architectural managers need to have a solid education. They are responsible for supervising the day to day operations of engineering teams. They also provide oversight and training to staff. They are also responsible for recommending budgets and acting as mentors to other employees. If you are interested in a career in this area, you might consider a bachelor's in the field.
Most of these managers have a bachelor’s degree either in architecture or engineering. However, many have advanced degrees or certificates in technology or business administration. A master's degree in engineering management, or technology management, also known as MsEM will provide you with the necessary managerial skills. Strong communication and analytical skills are essential.
The responsibility of architects and engineers managers is to implement new projects while maintaining high quality end products. They take into account the effects on the environment as well as the needs of the users. They prepare budgets and plans based on technical specifications. They supervise teams and engineers to ensure the success of projects.
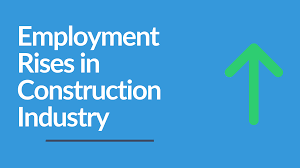
Earning potential
Over the next decade there is an expected 13 percent increase in earning potential for architects and engineers managers. This industry is expected to see an increase of jobs. Despite the fact that the number of jobs in this industry is expected to increase, competition will remain intense. However, the growth rate in the industry will not be as high as the average for all occupations.
The range of salaries for this occupation depends on your education, experience and geographical location. An entry-level position in this field will earn a salary of $75,190. Those with four to five years of experience can expect to make at least $104,800. For those with a minimum of ten years experience, they can make approximately $156,620 annually.
FAQ
What does it take to run a logistics business?
A successful logistics business requires a lot more than just knowledge. For clients and suppliers to be successful, you need to have excellent communication skills. You must be able analyze data and draw out conclusions. You will need to be able handle pressure well and work in stressful situations. In order to innovate and create new ways to improve efficiency, creativity is essential. Strong leadership qualities are essential to motivate your team and help them achieve their organizational goals.
It is also important to be efficient and well organized in order meet deadlines.
What are the responsibilities of a production planner
Production planners ensure all aspects of the project are delivered within time and budget. They also ensure that the product/service meets the client’s needs.
What does warehouse refer to?
Warehouses and storage facilities are where goods are kept before being sold. It can be either an indoor or outdoor space. It could be one or both.
Are there any Manufacturing Processes that we should know before we can learn about Logistics?
No. You don't have to know about manufacturing processes before learning about logistics. It is important to know about the manufacturing processes in order to understand how logistics works.
What is manufacturing and logistics?
Manufacturing refers to the process of making goods using raw materials and machines. Logistics covers all aspects involved in managing supply chains, including procurement and production planning. As a broad term, manufacturing and logistics often refer to both the creation and delivery of products.
Is automation necessary in manufacturing?
Automation is important not only for manufacturers but also for service providers. It allows them provide faster and more efficient services. It reduces human errors and improves productivity, which in turn helps them lower their costs.
How does a Production Planner differ from a Project Manager?
The primary difference between a producer planner and a manager of a project is that the manager usually plans and organizes the whole project, while a production planner is only involved in the planning stage.
Statistics
- [54][55] These are the top 50 countries by the total value of manufacturing output in US dollars for its noted year according to World Bank.[56] (en.wikipedia.org)
- According to the United Nations Industrial Development Organization (UNIDO), China is the top manufacturer worldwide by 2019 output, producing 28.7% of the total global manufacturing output, followed by the United States, Japan, Germany, and India.[52][53] (en.wikipedia.org)
- It's estimated that 10.8% of the U.S. GDP in 2020 was contributed to manufacturing. (investopedia.com)
- Job #1 is delivering the ordered product according to specifications: color, size, brand, and quantity. (netsuite.com)
- In the United States, for example, manufacturing makes up 15% of the economic output. (twi-global.com)
External Links
How To
How to Use Lean Manufacturing in the Production of Goods
Lean manufacturing is a management style that aims to increase efficiency and reduce waste through continuous improvement. It was first developed in Japan in the 1970s/80s by Taiichi Ahno, who was awarded the Toyota Production System (TPS), award from KanjiToyoda, the founder of TPS. Michael L. Watkins published the "The Machine That Changed the World", the first book about lean manufacturing. It was published in 1990.
Lean manufacturing refers to a set of principles that improve the quality, speed and costs of products and services. It emphasizes reducing defects and eliminating waste throughout the value chain. Just-in-time (JIT), zero defect (TPM), and 5S are all examples of lean manufacturing. Lean manufacturing eliminates non-value-added tasks like inspection, rework, waiting.
Lean manufacturing not only improves product quality but also reduces costs. Companies can also achieve their goals faster by reducing employee turnover. Lean Manufacturing is one of the most efficient ways to manage the entire value chains, including suppliers and customers as well distributors and retailers. Lean manufacturing is widely practiced in many industries around the world. Toyota's philosophy is a great example of this. It has helped to create success in automobiles as well electronics, appliances and healthcare.
Lean manufacturing includes five basic principles:
-
Define Value: Identify the social value of your business and what sets you apart.
-
Reduce waste - Stop any activity that isn't adding value to the supply chains.
-
Create Flow - Ensure work moves smoothly through the process without interruption.
-
Standardize and simplify - Make your processes as consistent as possible.
-
Build Relationships - Establish personal relationships with both internal and external stakeholders.
Lean manufacturing is not a new concept, but it has been gaining popularity over the last few years due to a renewed interest in the economy following the global financial crisis of 2008. To increase their competitiveness, many businesses have turned to lean manufacturing. In fact, some economists believe that lean manufacturing will be an important factor in economic recovery.
Lean manufacturing has many benefits in the automotive sector. These benefits include increased customer satisfaction, reduced inventory levels and lower operating costs.
Any aspect of an enterprise can benefit from Lean manufacturing. It is especially useful for the production aspect of an organization, as it ensures that every step in the value chain is efficient and effective.
There are three types principally of lean manufacturing:
-
Just-in Time Manufacturing (JIT), also known as "pull system": This form of lean manufacturing is often referred to simply as "pull". JIT is a process in which components can be assembled at the point they are needed, instead of being made ahead of time. This strategy aims to decrease lead times, increase availability of parts and reduce inventory.
-
Zero Defects Manufacturing, (ZDM): ZDM is focused on ensuring that no defective products leave the manufacturing facility. If a part needs to be fixed during the assembly line, it should be repaired rather than scrapped. This applies to finished goods that may require minor repairs before shipment.
-
Continuous Improvement: Continuous Improvement aims to improve efficiency by continually identifying problems and making adjustments to eliminate or minimize waste. Continuous improvement involves continuous improvement of processes and people as well as tools.