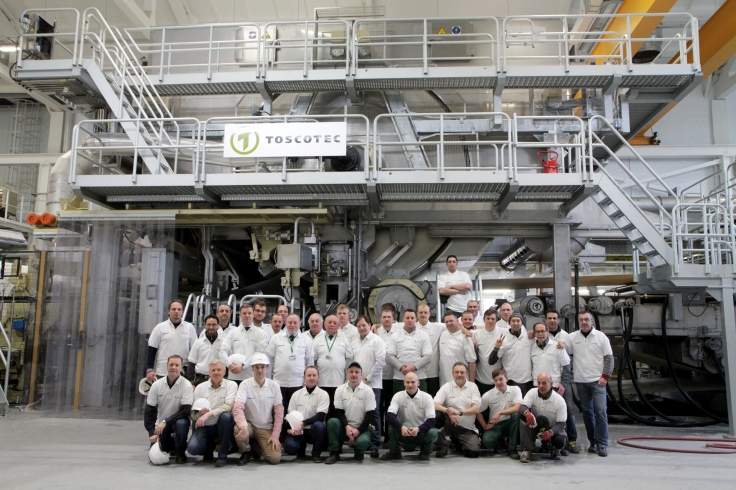
Historically, manufacturing has been driven by consumer demand. But this is changing. Technology is also transforming the manufacturing industry. Predictive analytics has allowed manufacturers to bring production closer to customers. Despite these advances, manufacturing faces many risks, including shortages and high demand. Manufacturers may lose customers if they do not meet consumers' demand. They could also lose customers if they produce excessively. To preserve their brand image manufacturers must comply with quality control standards.
Manufacturers can use a variety of manufacturing methods, but they all have similar characteristics. Repetitive manufacturing, batch manufacturing and process manufacturing are the most popular. These processes allow manufacturers to produce large quantities of products on large scales.
Repetitive manufacturing is the use of dedicated production lines to produce identical or similar products all year. Repetitive manufacturing production lines require little setup and changeover, making them ideal for production runs with limited capital investment. They can run 24-hours per day.
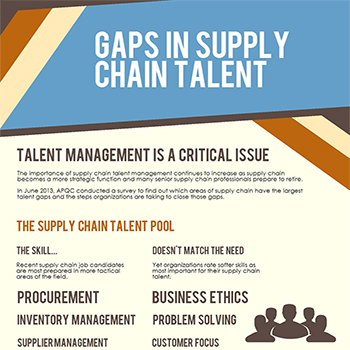
Batch manufacturing is similar but can only be done in small, discrete batches. This process is typically faster and requires less automation. This process is not ideal for all production types. This is an excellent option for products which require frequent changeovers. It can also be used for custom-made products. It is ideal for making goods from materials that don't easily degrade.
Discrete manufacturing is the other side of process manufacturing. It involves using a bill and instructions to make finished goods. It can also include toys and automobiles. It can also involve the use of software and computers. The main difference is that process manufacturing requires fewer interruptions and higher quality control.
The most common process for mass manufacturing of plastic parts is injection molding. These small plastic pellets can be melted and then injected into molds. The mold is then cooled, and mechanically ejected. To ensure uniform coating, molds are heated and rotated. This technique can be used to make many products, including pipes and straws.
Atomic manufacturing is the third type. This is also called "bottom-up" or "bottom-up" production. This is where components can interact naturally. Also, this method allows for the production of products made from biological materials. You can add parts manually or automatically in certain cases.
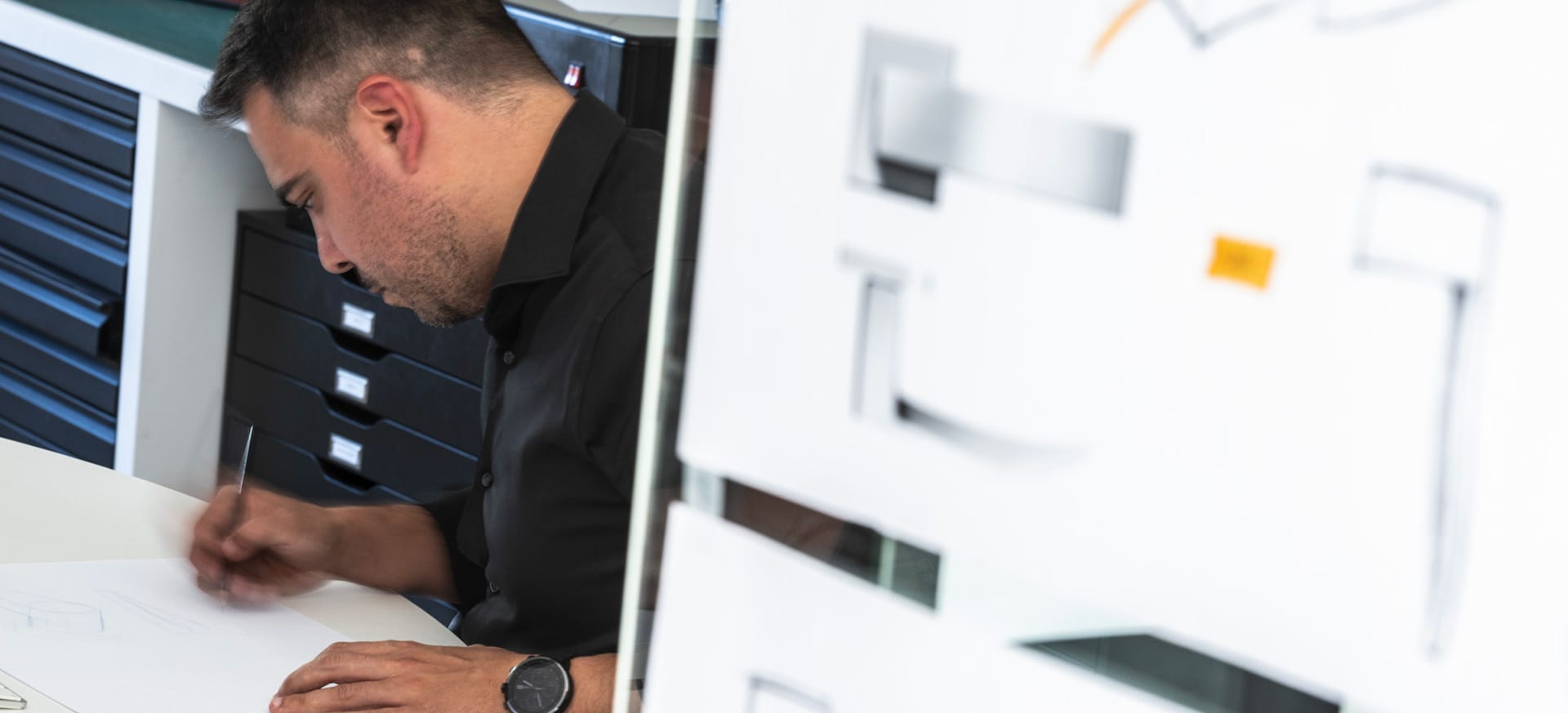
Another form of process manufacturing is intermittent manufacturing. This method produces multiple identical items at once, which is especially beneficial for low-volume production runs. It is however difficult to customize and is not appropriate for all products.
Process manufacturing also includes the production of items that cannot be broken down, such as ceramics or glass. The main advantage of process manufacturing is the ability to produce a variety of products, while maintaining a high quality of production. Additionally, process manufacturing is less prone to defects and has fewer interruptions.
FAQ
What skills is required for a production planner?
Production planners must be flexible, organized, and able handle multiple tasks. Effective communication with clients and colleagues is essential.
What is the best way to learn about manufacturing?
You can learn the most about manufacturing by getting involved in it. If that is not possible, you could always read books or view educational videos.
How can manufacturing efficiency be improved?
First, we need to identify which factors are most critical in affecting production times. We must then find ways that we can improve these factors. If you don’t know how to start, look at which factors have the greatest impact upon production time. Once you have identified the factors, then try to find solutions.
Statistics
- It's estimated that 10.8% of the U.S. GDP in 2020 was contributed to manufacturing. (investopedia.com)
- [54][55] These are the top 50 countries by the total value of manufacturing output in US dollars for its noted year according to World Bank.[56] (en.wikipedia.org)
- Job #1 is delivering the ordered product according to specifications: color, size, brand, and quantity. (netsuite.com)
- You can multiply the result by 100 to get the total percent of monthly overhead. (investopedia.com)
- Many factories witnessed a 30% increase in output due to the shift to electric motors. (en.wikipedia.org)
External Links
How To
How to Use 5S to Increase Productivity in Manufacturing
5S stands in for "Sort", the "Set In Order", "Standardize", or "Separate". Toyota Motor Corporation invented the 5S strategy in 1954. It allows companies to improve their work environment, thereby achieving greater efficiency.
The basic idea behind this method is to standardize production processes, so they become repeatable, measurable, and predictable. This means that daily tasks such as cleaning and sorting, storage, packing, labeling, and packaging are possible. Workers can be more productive by knowing what to expect.
There are five steps that you need to follow in order to implement 5S. Each step is a different action that leads to greater efficiency. For example, when you sort things, you make them easy to find later. When you arrange items, you place them together. You then organize your inventory in groups. You can also label your containers to ensure everything is properly labeled.
Employees will need to be more critical about their work. Employees need to understand the reasons they do certain jobs and determine if there is a better way. In order to use the 5S system effectively, they must be able to learn new skills.
In addition to improving efficiency, the 5S system also increases morale and teamwork among employees. As they begin to see improvements, they feel motivated to continue working towards the goal of achieving higher levels of efficiency.