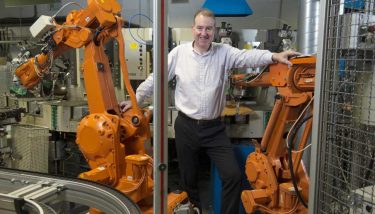
CEVA Logistics is an organization that offers logistics services. These companies offer numerous benefits to their employees, no matter if you are looking for a job or a change in your career. Here are some ways you can apply for a position in logistics at one of these companies. You can search for jobs by region.
Job description
CEVA Logistics has many job openings for people with varied education and work experiences. The company's core values are dedication to customer service and on-time delivery. The company seeks people who are passionate about logistics, and who are willing work hard. The company will consider candidates who are enthusiastic about logistics and possess a positive attitude when they apply for a job.
CEVA Logistics is seeking a Process/Industrial Engineer to design and implement new processes and improve efficiency. The ideal candidate must be self-motivated, energetic, and able work well with others. They will be responsible for managing projects, planning and implementing process designs, and using mathematical and modeling skills. They must also be familiar with robotics and other manufacturing processes to increase efficiency and quality.
Education is required
CEVA Logistics offers several career options to applicants who are interested in joining the company. They may also be eligible to become operations supervisors. These positions involve managing the day-today operations of CEVA Logistics, such as scheduling and inventory management, customer service, and customer support. These positions are often accompanied by a team. Candidates for these positions typically require a bachelor's degree in logistics, supervisory experience, and strong management and leadership skills.
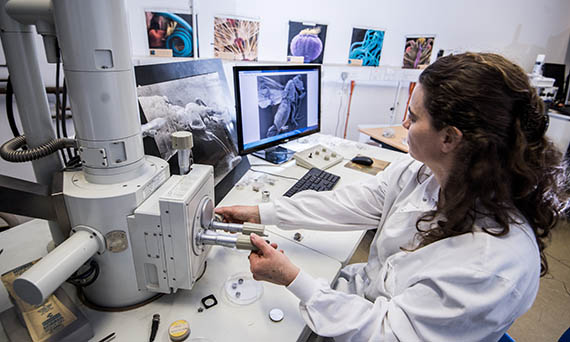
Candidates interested in applying can either apply online or through recruiters. Candidates must first create a profile on the company's career portal to apply online. You can connect to your LinkedIn account to access your profile, upload your resumes, and fill in relevant information. Once their profile has been completed, they are able to choose their preferred country and get in contact with a recruiter.
Salary range
To apply for a CEVA Logistics position, you must first create an account on the company's career portal. This allows you to connect with your LinkedIn profile and upload your resume. Additionally, you can manually input information about your experience, skills, and other relevant information. Next, you will need to choose the region or country in which you want to work. You'll then receive contact information for a recruiter in the region.
CEVA Logistics has a variety of salaries. These vary depending on your job title, work experience, and geographic location. The salary of the Vice President of CEVA Logistics is $166,000 while that of an Air Break Bulk specialist is $24,000. But, the economic climate in each region can mean that salaries may vary.
Localities
CEVA Logistics could be the right place for you if you are looking for a fulfilling career in logistics. CEVA Logistics offers a variety of positions in different locations with different responsibilities. You can apply for a job by entering the job title and location in the search box. You can search for Edison job listings. You'll need to have experience in driving, and must be able to communicate well with internal and external customers, as well as perform a variety of other tasks.
CEVA Logistics offers many career opportunities, including supervisory positions. Supervisors are responsible for the company's day to day operations. They manage inventory, coordinate schedules, and oversee the activities of employees. Operations supervisors typically have a team of employees reporting to them, and typically require a bachelor's degree or other related experience. It is also important to have strong leadership and management abilities.
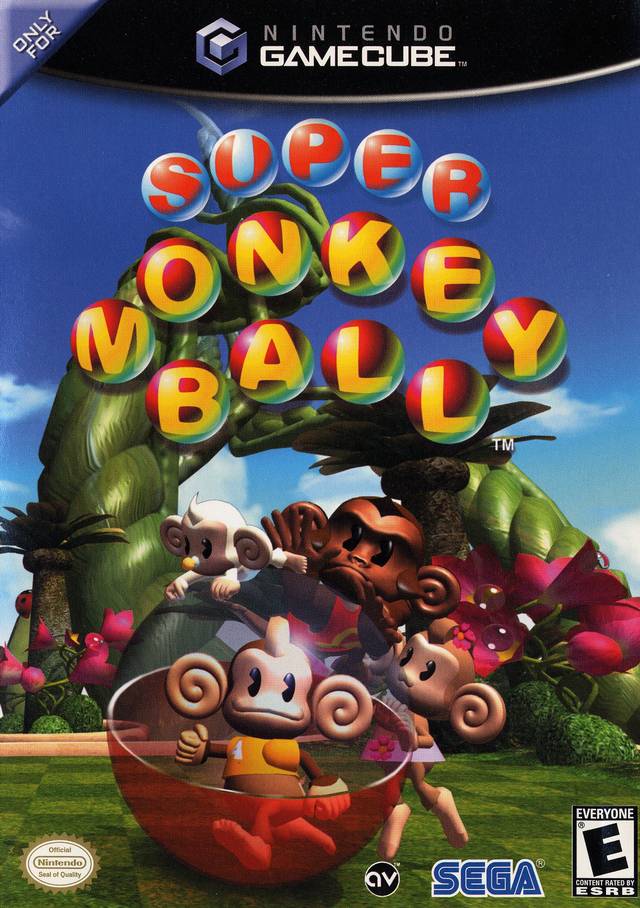
Online application
CEVA Logistics is an online job board for those looking for jobs in the logistics sector. Ceva Logistics was formed in 2006 from the merger between two Australian and Texan contract logistic companies. Its operations are now located in more than 950 countries. You can apply to full-time and part-time jobs for job seekers.
Many positions at CEVA require some work experience. However, many of the positions are entry-level. Others require minimal to moderate experience. Customer service representative, dispatcher, and admin clerk are some of the entry-level jobs.
FAQ
What are the responsibilities of a logistic manager?
Logistics managers make sure all goods are delivered on schedule and without damage. This is done through his/her expertise and knowledge about the company's product range. He/she also needs to ensure adequate stock to meet demand.
What is production planning?
Production Planning involves developing a plan for all aspects of the production, including scheduling, budgeting, casting, crew, location, equipment, props, etc. This document is designed to make sure everything is ready for when you're ready to shoot. This document should also include information on how to get the best result on set. This information includes locations, crew details and equipment requirements.
The first step in filming is to define what you want. You may already know where you want the film to be shot, or perhaps you have specific locations and sets you wish to use. Once you have determined your scenes and locations, it is time to start figuring out the elements that you will need for each scene. If you decide you need a car and don't know what model to choose, this could be an example. You could look online for cars to see what options are available, and then narrow down your choices by selecting between different makes or models.
After you have chosen the right car, you will be able to begin thinking about accessories. Do you have people who need to be seated in the front seat? Or perhaps you need someone walking around the back of the car? Perhaps you would like to change the interior colour from black to white. These questions will help you determine the exact look and feel of your car. Another thing you can do is think about what type of shots are desired. What type of shots will you choose? Maybe you want the engine or the steering wheels to be shown. These details will help identify the exact car you wish to film.
Once you've determined the above, it is time to start creating a calendar. You can use a schedule to determine when and where you need it to be shot. You will need to know when you have to be there, what time you have to leave and when your return home. This way, everyone knows what they need to do and when. It is possible to make arrangements in advance for additional staff if you are looking to hire. It is not worth hiring someone who won’t show up because you didn’t tell him.
Your schedule will also have to be adjusted to reflect the number of days required to film. Some projects take only a few days while others can last several weeks. You should consider whether you will need more than one shot per week when creating your schedule. Shooting multiple takes over the same location will increase costs and take longer to complete. You can't be certain if you will need multiple takes so it is better not to shoot too many.
Another important aspect of production planning is setting budgets. It is important to set a realistic budget so you can work within your budget. If you have to reduce your budget due to unexpected circumstances, you can always lower it later. But, don't underestimate how much money you'll spend. If you underestimate how much something costs, you'll have less money to pay for other items.
Planning production is a tedious process. Once you have a good understanding of how everything works together, planning future projects becomes easy.
How can manufacturing overproduction be reduced?
It is essential to find better ways to manage inventory to reduce overproduction. This would decrease the time that is spent on inefficient activities like purchasing, storing, or maintaining excess stock. This could help us free up our time for other productive tasks.
One way to do this is to adopt a Kanban system. A Kanban board can be used to monitor work progress. In a Kanban system, work items move through a sequence of states until they reach their final destination. Each state represents a different priority level.
To illustrate, work can move from one stage or another when it is complete enough for it to be moved to a new stage. However, if a task is still at the beginning stages, it will remain so until it reaches the end of the process.
This allows you to keep work moving along while making sure that no work gets neglected. With a Kanban board, managers can see exactly how much work is being done at any given moment. This data allows them adjust their workflow based upon real-time data.
Another way to control inventory levels is to implement lean manufacturing. Lean manufacturing emphasizes eliminating waste in all phases of production. Anything that does nothing to add value to a product is waste. Here are some examples of common types.
-
Overproduction
-
Inventory
-
Unnecessary packaging
-
Overstock materials
By implementing these ideas, manufacturers can improve efficiency and cut costs.
What are the 4 types manufacturing?
Manufacturing refers to the transformation of raw materials into useful products by using machines and processes. It can involve many activities like designing, manufacturing, testing packaging, shipping, selling and servicing.
Why automate your warehouse?
Automation has become increasingly important in modern warehousing. With the rise of ecommerce, there is a greater demand for faster delivery times as well as more efficient processes.
Warehouses need to adapt quickly to meet changing needs. To do so, they must invest heavily in technology. Automating warehouses has many benefits. Here are some benefits of investing in automation
-
Increases throughput/productivity
-
Reduces errors
-
Improves accuracy
-
Safety Boosts
-
Eliminates bottlenecks
-
Companies can scale more easily
-
This makes workers more productive
-
This gives you visibility into what happens in the warehouse
-
Enhances customer experience
-
Improves employee satisfaction
-
Reducing downtime and increasing uptime
-
Quality products delivered on time
-
Human error can be eliminated
-
This helps to ensure compliance with regulations
Is there anything we should know about Manufacturing Processes prior to learning about Logistics.
No. No. However, knowing about manufacturing processes will definitely give you a better understanding of how logistics works.
Can some manufacturing processes be automated?
Yes! Yes! Automation has existed since ancient times. The Egyptians discovered the wheel thousands and years ago. We now use robots to help us with assembly lines.
There are many uses of robotics today in manufacturing. These include:
-
Robots for assembly line
-
Robot welding
-
Robot painting
-
Robotics inspection
-
Robots that create products
Manufacturing can also be automated in many other ways. For example, 3D printing allows us to make custom products without having to wait for weeks or months to get them manufactured.
Statistics
- (2:04) MTO is a production technique wherein products are customized according to customer specifications, and production only starts after an order is received. (oracle.com)
- [54][55] These are the top 50 countries by the total value of manufacturing output in US dollars for its noted year according to World Bank.[56] (en.wikipedia.org)
- Many factories witnessed a 30% increase in output due to the shift to electric motors. (en.wikipedia.org)
- According to a Statista study, U.S. businesses spent $1.63 trillion on logistics in 2019, moving goods from origin to end user through various supply chain network segments. (netsuite.com)
- In 2021, an estimated 12.1 million Americans work in the manufacturing sector.6 (investopedia.com)
External Links
How To
How to Use Lean Manufacturing for the Production of Goods
Lean manufacturing is a management style that aims to increase efficiency and reduce waste through continuous improvement. It was developed by Taiichi Okono in Japan, during the 1970s & 1980s. TPS founder Kanji Takoda awarded him the Toyota Production System Award (TPS). The first book published on lean manufacturing was titled "The Machine That Changed the World" written by Michael L. Watkins and published in 1990.
Lean manufacturing, often described as a set and practice of principles, is aimed at improving the quality, speed, cost, and efficiency of products, services, and other activities. It emphasizes eliminating waste and defects throughout the value stream. The five-steps of Lean Manufacturing are just-in time (JIT), zero defect and total productive maintenance (TPM), as well as 5S. Lean manufacturing focuses on eliminating non-value-added activities such as rework, inspection, and waiting.
Lean manufacturing is a way for companies to achieve their goals faster, improve product quality, and lower costs. Lean manufacturing is considered one of the most effective ways to manage the entire value chain, including suppliers, customers, distributors, retailers, and employees. Many industries worldwide use lean manufacturing. Toyota's philosophy is the foundation of its success in automotives, electronics and appliances, healthcare, chemical engineers, aerospace, paper and food, among other industries.
Five fundamental principles underlie lean manufacturing.
-
Define Value - Identify the value your business adds to society and what makes you different from competitors.
-
Reduce waste - Stop any activity that isn't adding value to the supply chains.
-
Create Flow – Ensure that work flows smoothly throughout the process.
-
Standardize & simplify - Make processes consistent and repeatable.
-
Build Relationships - Establish personal relationships with both internal and external stakeholders.
Although lean manufacturing isn't a new concept in business, it has gained popularity due to renewed interest in the economy after the 2008 global financial crisis. To increase their competitiveness, many businesses have turned to lean manufacturing. In fact, some economists believe that lean manufacturing will be an important factor in economic recovery.
Lean manufacturing is now becoming a common practice in the automotive industry, with many benefits. These benefits include increased customer satisfaction, reduced inventory levels and lower operating costs.
You can apply Lean Manufacturing to virtually any aspect of your organization. However, it is particularly useful when applied to the production side of an organization because it ensures that all steps in the value chain are efficient and effective.
There are three main types in lean manufacturing
-
Just-in-Time Manufacturing (JIT): This type of lean manufacturing is commonly referred to as "pull systems." JIT means that components are assembled at the time of use and not manufactured in advance. This approach aims to reduce lead times, increase the availability of parts, and reduce inventory.
-
Zero Defects Manufacturing (ZDM),: ZDM is a system that ensures no defective units are left the manufacturing facility. Repairing a part that is damaged during assembly should be done, not scrapping. This applies to finished goods that may require minor repairs before shipment.
-
Continuous Improvement (CI),: Continuous improvement aims improve the efficiency and effectiveness of operations by continuously identifying issues and making changes to reduce waste. Continuous Improvement involves continuous improvement of processes.