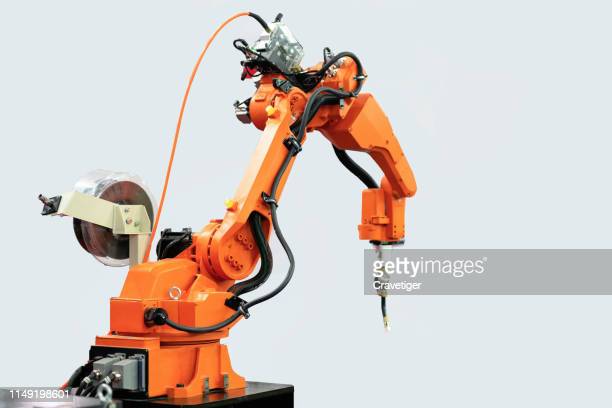
The best books in lean manufacturing provide industry managers with essential guidance. The bestselling book covers a range of concepts including how to improve business processes, reduce expenses and improve quality. Easy implementation is made possible by detailed drawings and stepby-step instructions. Information about lean manufacturing tools is also included in the book.
The book also provides an overview of the Toyota production system and Toyota's global success. It also explains Toyota's motivation, problem-solving and management style. It also explains Toyota's Lean strategy, and the 14 management principles which are the core of its business practices. The book also has a chapter on Toyota's automotive industry. It includes a section that explains how Toyota uses lean principles in the sector.
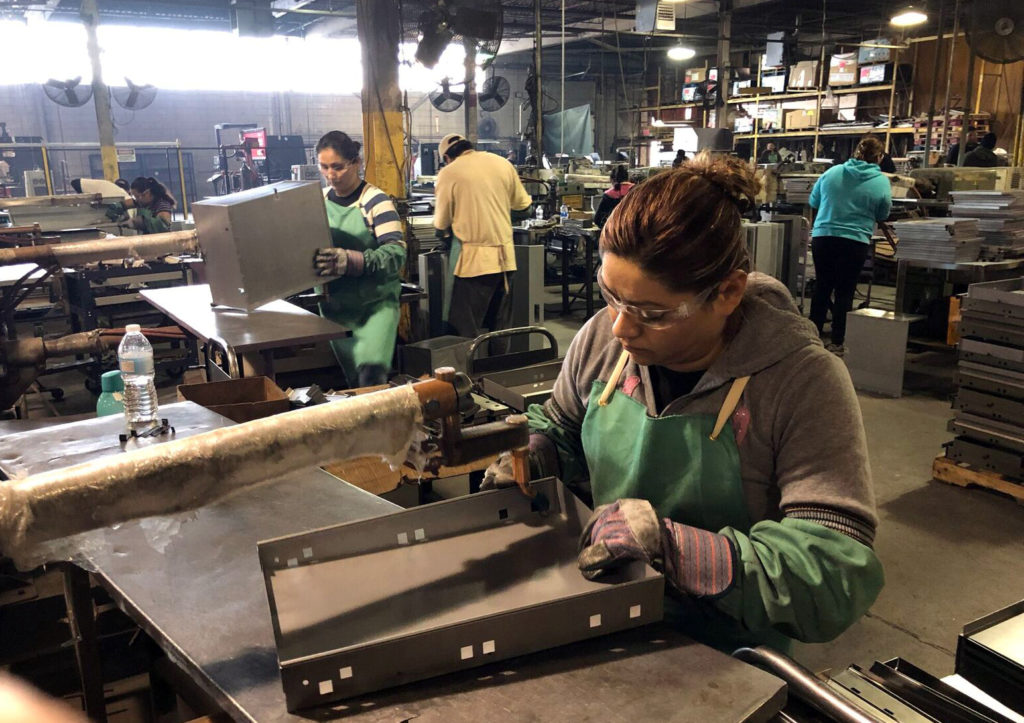
Lean manufacturing is a process of manufacturing that strives to improve the quality and efficiency of the products and services a company produces. This process eliminates waste and makes the process more efficient. Highly skilled machines and people are the key to manufacturing success. These interactions make up the bulk of manufacturing company's overall costs.
The best books on lean manufacturing include the Lean Manufacturing Tool Book, The Toyota Way: 14 Management Principles for Improving Quality and Productivity, and The Machine that Changed the World: How Toyota Built a Competitive Advantage. These books offer a thorough explanation of Toyota's manufacturing system as well as practical tips, and detailed instructions for how to apply Lean techniques to any type of manufacturing environment. Lean Manufacturing Tool Book contains all of the necessary tools for Lean manufacturing. The book provides expert advice to help you choose the right tool and lists the available tools. The book also describes Lean manufacturing concepts and Six Sigma.
The Toyota Way is the first book to introduce Lean manufacturing. It focuses on Toyota's management principles and discusses how to implement them within your own organization. It also features company profiles and the principles that have made Toyota's success possible. It also includes a new afterword that discusses the impact of Lean on the manufacturing industry since the publication of the book. It also contains updated frameworks that can be used to improve production, reduce costs, and improve quality.
The Machine that Changed the World, How Lean Changed the World, was the first book that explained the Toyota Production System and its effect on the manufacturing industries. This book was published in 1990. It provides an overview of the system and gives the reader an important context for the role of Lean in the manufacturing industry since the book's publication. It includes a new afterword and a revised foreword that provide a better understanding of the Toyota Production System and its impact on the global manufacturing industry. It also discusses the principles that underlie all Lean practices.
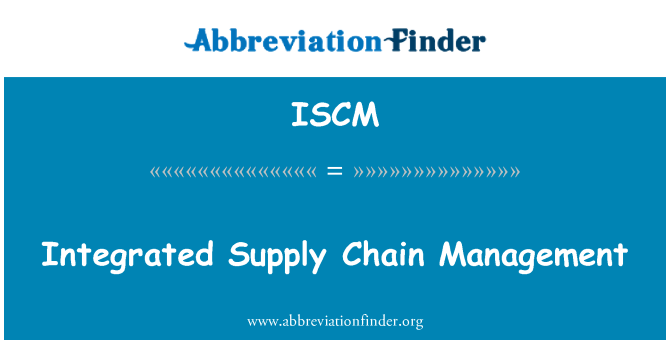
Another book worth reading is The Toyota Kata Flow Focused Manufacturing Methodology. It explains how Toyota works together with their customers to offer quality products. It explains Toyota's commitment towards quality, problem-solving, speeding up business operations and ensuring customer satisfaction. It also explains how Toyota selects and hires employees and how they are motivated to deliver high quality products and services.
FAQ
What is the role of a logistics manager
Logistics managers are responsible for ensuring that all goods arrive in perfect condition and on time. This is done using his/her knowledge of the company's products. He/she should also ensure enough stock is available to meet demand.
Why is logistics so important in manufacturing?
Logistics is an integral part of every business. They help you achieve great results by helping you manage all aspects of product flow, from raw materials to finished goods.
Logistics also play a major role in reducing costs and increasing efficiency.
What is the role and responsibility of a Production Planner?
Production planners ensure all aspects of the project are delivered within time and budget. They make sure that the product and services meet client expectations.
Statistics
- It's estimated that 10.8% of the U.S. GDP in 2020 was contributed to manufacturing. (investopedia.com)
- [54][55] These are the top 50 countries by the total value of manufacturing output in US dollars for its noted year according to World Bank.[56] (en.wikipedia.org)
- According to a Statista study, U.S. businesses spent $1.63 trillion on logistics in 2019, moving goods from origin to end user through various supply chain network segments. (netsuite.com)
- (2:04) MTO is a production technique wherein products are customized according to customer specifications, and production only starts after an order is received. (oracle.com)
- According to the United Nations Industrial Development Organization (UNIDO), China is the top manufacturer worldwide by 2019 output, producing 28.7% of the total global manufacturing output, followed by the United States, Japan, Germany, and India.[52][53] (en.wikipedia.org)
External Links
How To
How to Use the Just-In-Time Method in Production
Just-in-time is a way to cut costs and increase efficiency in business processes. It is a process where you get the right amount of resources at the right moment when they are needed. This means that only what you use is charged to your account. Frederick Taylor first coined this term while working in the early 1900s as a foreman. Taylor observed that overtime was paid to workers if they were late in working. He decided to ensure workers have enough time to do their jobs before starting work to improve productivity.
JIT is an acronym that means you need to plan ahead so you don’t waste your money. It is important to look at your entire project from beginning to end and ensure that you have enough resources to handle any issues that may arise. If you anticipate that there might be problems, you'll have enough people and equipment to fix them. You won't have to pay more for unnecessary items.
There are many JIT methods.
-
Demand-driven: This type of JIT allows you to order the parts/materials required for your project on a regular basis. This will allow for you to track the material that you have left after using it. It will also allow you to predict how long it takes to produce more.
-
Inventory-based: This type allows you to stock the materials needed for your projects ahead of time. This allows you predict the amount you can expect to sell.
-
Project-driven: This is an approach where you set aside enough funds to cover the cost of your project. If you know the amount you require, you can buy the materials you need.
-
Resource-based JIT: This is the most popular form of JIT. You allocate resources based on the demand. You might assign more people to help with orders if there are many. If there aren't many orders, you will assign fewer people.
-
Cost-based : This is similar in concept to resource-based. But here, you aren't concerned about how many people your company has but how much each individual costs.
-
Price-based: This is very similar to cost-based, except that instead of looking at how much each individual worker costs, you look at the overall price of the company.
-
Material-based: This is very similar to cost-based but instead of looking at total costs of the company you are concerned with how many raw materials you use on an average.
-
Time-based: Another variation of resource-based JIT. Instead of focusing on how much each employee costs, you focus on how long it takes to complete the project.
-
Quality-based JIT: Another variation on resource-based JIT. Instead of worrying about the costs of each employee or how long it takes for something to be made, you should think about how quality your product is.
-
Value-based JIT is the newest form of JIT. In this instance, you are not concerned about the product's performance or meeting customer expectations. Instead, you're focused on how much value you add to the market.
-
Stock-based is an inventory-based system that measures the number of items produced at any given moment. This is used to increase production and minimize inventory.
-
Just-in-time (JIT) planning: This is a combination of JIT and supply chain management. It is the process that schedules the delivery of components within a short time of their order. It's important because it reduces lead times and increases throughput.