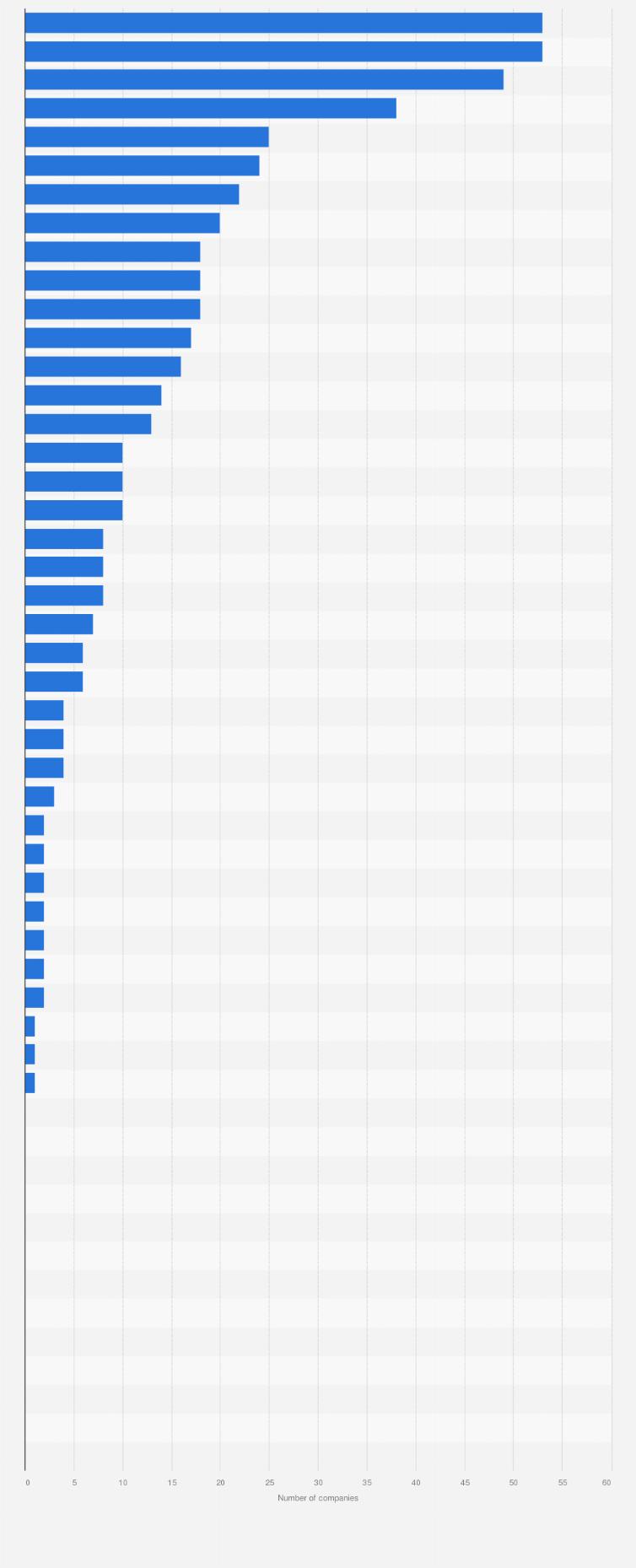
Lean manufacturing is applied to service sectors using lean services. The US Health Care providers and HMRC in Britain are two examples of companies that have adopted this method to improve their production processes. Lean services are designed to reduce waste, improve customer satisfaction, and decrease costs. Whether you're a small startup or a global giant, lean services can improve your business.
Lean manufacturing
Lean manufacturing is a process that is based on eliminating waste. The process helps businesses increase their overall productivity, reduce operating costs, and increase employee satisfaction. It can help increase profits. It can help increase profits and speed up product development. With lean manufacturing services, companies can expand their customer base as well as increase their revenue streams.
Lean manufacturing requires a team approach and a lot of talent. It is essential that all members of the team are familiar with the process and how they work. Additionally, they must be able adapt the practices to suit the company's needs. For example, the first step in lean manufacturing is to simplify the manufacturing processes. Complex manufacturing processes can make it difficult for people to spot inefficiencies and waste. Simplicity also helps improve visibility and creates a culture that encourages continuous improvement. This will empower your employees and allow them to identify inefficiencies.
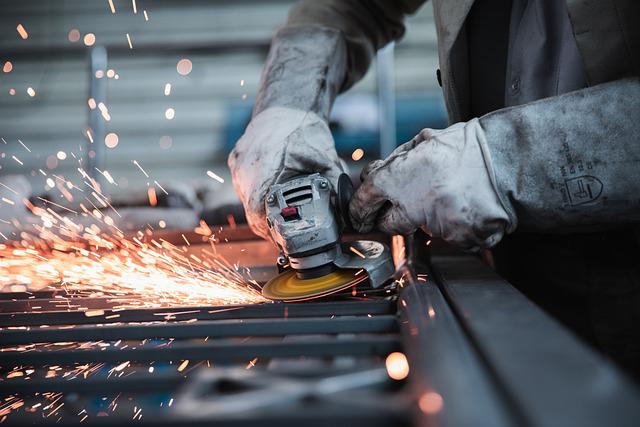
Lean manufacturing is a way for companies to increase efficiency and reduce lead times. MXGlobal, a company that offers lean implementation, has successfully consulted Japanese companies having a U.S. location. Lean manufacturing services offered by the firm are designed to help businesses expand internationally and reach their business goals.
Lean manufacturing helps businesses create an environment conducive to maximum profits. They are focused on improving productivity and reducing waste. There are eight types. They include excess production, inventory, and transport. These wastes may increase customer satisfaction and cost more.
Lean operations management
In order to implement lean operation management for lean service, organizations need to first understand what they are trying accomplish. This is a method that creates value for the customer. Value is what drives sales, and is what consumers expect from a product or service. Start by mapping the various steps involved in the creation of a product/service and asking, "What adds to the customer?"
Lean management systems aim to continuously improve their processes. Continuous improvement is the core of this approach. This ensures your team delivers work assignments consistently in a shorter amount of time and with less effort. In addition, this method reduces waste from production processes, and optimizes overhead and storage costs. The four principles of Lean Management include continuous improvement and minimization, minimizing waste, reducing cycles time, and ensuring continuous workflows.
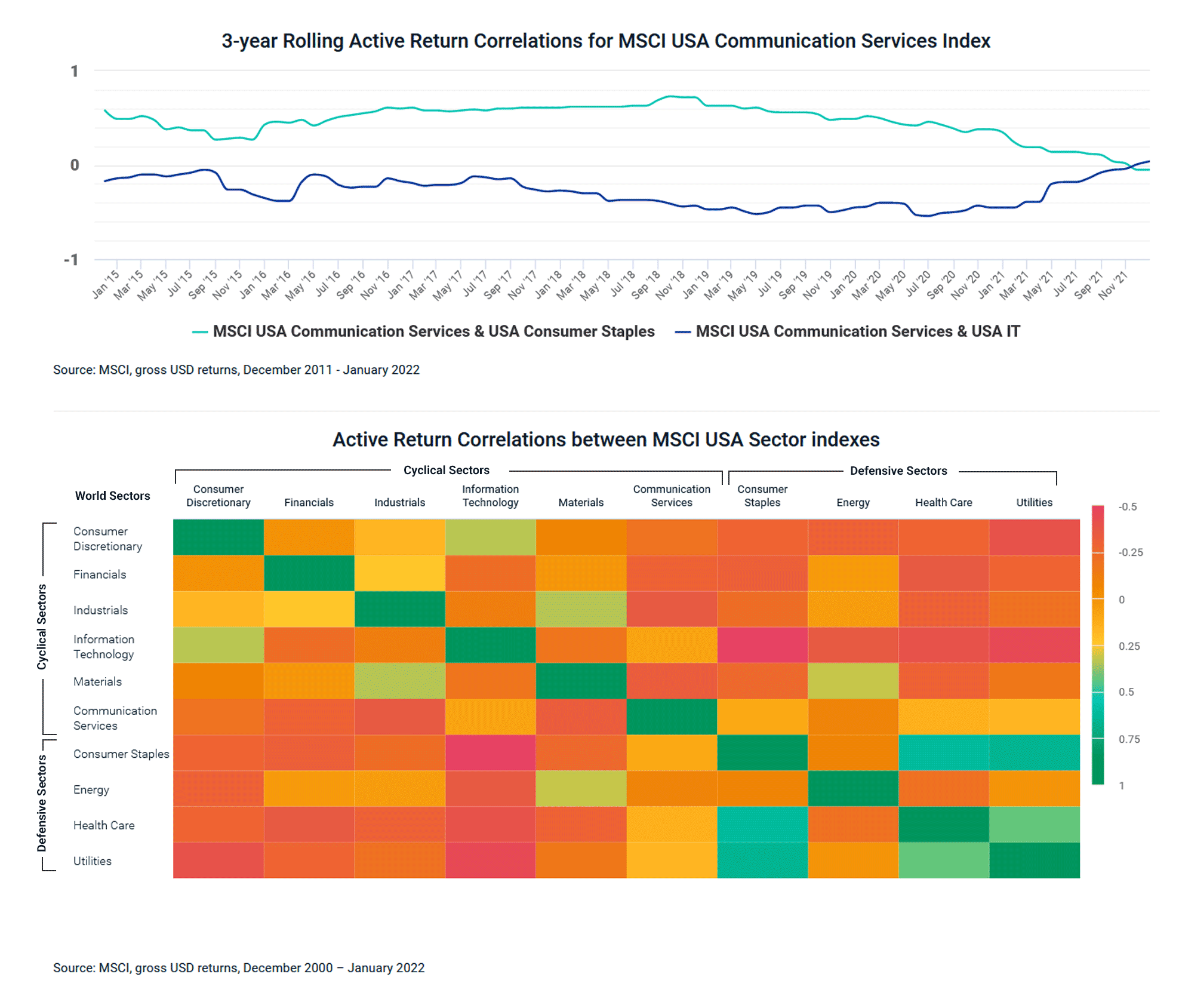
Lean operations management - lean services, focuses on creating greater value for customers by using fewer resources. It is more difficult to identify intangible wastes in a service environment. But lean principles aim to reduce and eliminate them. Businesses can maximise profits and create value by eliminating waste.
FAQ
What is meant by manufacturing industries?
Manufacturing Industries is a group of businesses that produce goods for sale. Consumers are people who purchase these goods. These companies employ many processes to achieve this purpose, such as production and distribution, retailing, management and so on. They manufacture goods from raw materials using machines and other equipment. This includes all types if manufactured goods.
How important is automation in manufacturing?
Automating is not just important for manufacturers, but also for service providers. They can provide services more quickly and efficiently thanks to automation. In addition, it helps them reduce costs by reducing human errors and improving productivity.
How can manufacturing avoid production bottlenecks
The key to avoiding bottlenecks in production is to keep all processes running smoothly throughout the entire production cycle, from the time you receive an order until the time when the product ships.
This includes planning to meet capacity requirements and quality control.
Continuous improvement techniques such Six Sigma can help you achieve this.
Six Sigma management is a system that improves quality and reduces waste within your organization.
It is focused on creating consistency and eliminating variation in your work.
How can we increase manufacturing efficiency?
First, identify the factors that affect production time. We must then find ways that we can improve these factors. If you don't know where to start, then think about which factor(s) have the biggest impact on production time. Once you have identified the factors, then try to find solutions.
What are the 4 types manufacturing?
Manufacturing is the process by which raw materials are transformed into useful products through machines and processes. It can involve many activities like designing, manufacturing, testing packaging, shipping, selling and servicing.
What are manufacturing and logistics?
Manufacturing is the process of creating goods from raw materials by using machines and processes. Logistics manages all aspects of the supply chain, including procurement, production planning and distribution, inventory control, transportation, customer service, and transport. Logistics and manufacturing are often referred to as one thing. It encompasses both the creation of products and their delivery to customers.
What are the 7 Rs of logistics management?
The acronym 7R's of Logistic is an acronym that stands for seven fundamental principles of logistics management. It was developed and published by the International Association of Business Logisticians in 2004 as part of the "Seven Principles of Logistics Management".
The acronym is made up of the following letters:
-
Responsible - to ensure that all actions are within the legal requirements and are not detrimental to others.
-
Reliable - You can have confidence that you will fulfill your promises.
-
Use resources effectively and sparingly.
-
Realistic - Consider all aspects of operations, including environmental impact and cost effectiveness.
-
Respectful - show respect and treat others fairly and fairly
-
Responsive - Look for ways to save time and increase productivity.
-
Recognizable is a company that provides customers with value-added solutions.
Statistics
- According to a Statista study, U.S. businesses spent $1.63 trillion on logistics in 2019, moving goods from origin to end user through various supply chain network segments. (netsuite.com)
- (2:04) MTO is a production technique wherein products are customized according to customer specifications, and production only starts after an order is received. (oracle.com)
- Many factories witnessed a 30% increase in output due to the shift to electric motors. (en.wikipedia.org)
- You can multiply the result by 100 to get the total percent of monthly overhead. (investopedia.com)
- It's estimated that 10.8% of the U.S. GDP in 2020 was contributed to manufacturing. (investopedia.com)
External Links
How To
How to Use Lean Manufacturing for the Production of Goods
Lean manufacturing is a management style that aims to increase efficiency and reduce waste through continuous improvement. It was created in Japan by Taiichi Ohno during the 1970s and 80s. He received the Toyota Production System award (TPS), from Kanji Toyoda, founder of TPS. The first book published on lean manufacturing was titled "The Machine That Changed the World" written by Michael L. Watkins and published in 1990.
Lean manufacturing, often described as a set and practice of principles, is aimed at improving the quality, speed, cost, and efficiency of products, services, and other activities. It emphasizes reducing defects and eliminating waste throughout the value chain. Lean manufacturing is called just-in-time (JIT), zero defect, total productive maintenance (TPM), or 5S. Lean manufacturing seeks to eliminate non-value added activities, such as inspection, work, waiting, and rework.
In addition to improving product quality and reducing costs, lean manufacturing helps companies achieve their goals faster and reduces employee turnover. Lean Manufacturing is one of the most efficient ways to manage the entire value chains, including suppliers and customers as well distributors and retailers. Lean manufacturing can be found in many industries. Toyota's philosophy, for example, is what has enabled it to be successful in electronics, automobiles, medical devices, healthcare and chemical engineering as well as paper and food.
Five fundamental principles underlie lean manufacturing.
-
Define Value - Determine the value that your business brings to society. Also, identify what sets you apart from your competitors.
-
Reduce waste - Get rid of any activity that does not add value to the supply chain.
-
Create Flow. Ensure that your work is uninterrupted and flows seamlessly.
-
Standardize and Simplify – Make processes as consistent, repeatable, and as simple as possible.
-
Building Relationships – Establish personal relationships with both external and internal stakeholders.
Lean manufacturing, although not new, has seen renewed interest in the economic sector since 2008. To increase their competitiveness, many businesses have turned to lean manufacturing. Economists think that lean manufacturing is a crucial factor in economic recovery.
Lean manufacturing is becoming a popular practice in automotive. It has many advantages. These include better customer satisfaction and lower inventory levels. They also result in lower operating costs.
Any aspect of an enterprise can benefit from Lean manufacturing. It is especially useful for the production aspect of an organization, as it ensures that every step in the value chain is efficient and effective.
There are three types of lean manufacturing.
-
Just-in Time Manufacturing (JIT), also known as "pull system": This form of lean manufacturing is often referred to simply as "pull". JIT refers to a system in which components are assembled at the point of use instead of being produced ahead of time. This approach reduces lead time, increases availability and reduces inventory.
-
Zero Defects Manufacturing (ZDM): ZDM focuses on ensuring that no defective units leave the manufacturing facility. It is better to repair a part than have it removed from the production line if it needs to be fixed. This applies to finished goods that may require minor repairs before shipment.
-
Continuous Improvement (CI): CI aims to improve the efficiency of operations by continuously identifying problems and making changes in order to eliminate or minimize waste. Continuous improvement refers to continuous improvement of processes as well people and tools.