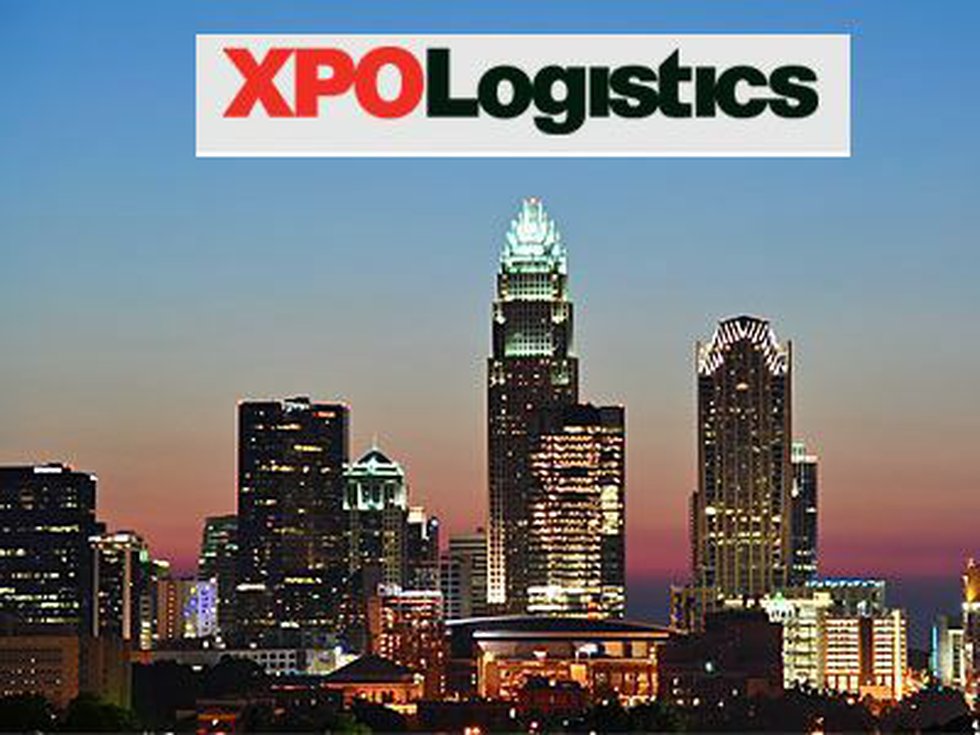
The SCOR model was developed by Supply Chain Council. It is used widely in the industry. It helps businesses better understand business processes, operational performance and goals. It also helps identify areas for improvement.
The model is broken down into three segments: performance measurements, supply chain best practice and process modeling. The model's first segment, process modeling, is a focus on planning, sourcing for, manufacturing and delivering products. Also included are market interactions, product return management and interaction with customers.
This segment of the model also provides more than 150 key performance indicators (KPIs) that you can use to measure the success of your operations. For instance, you can assess the performance of your suppliers in terms of delivery and determine if their products are high-quality at a reasonable price.
You can analyze your costs by analyzing customer returns. If you reduce the return rate of your suppliers by 20 per cent, then you will be able to save money. This can help you identify areas that you may be able save money on by improving your process.
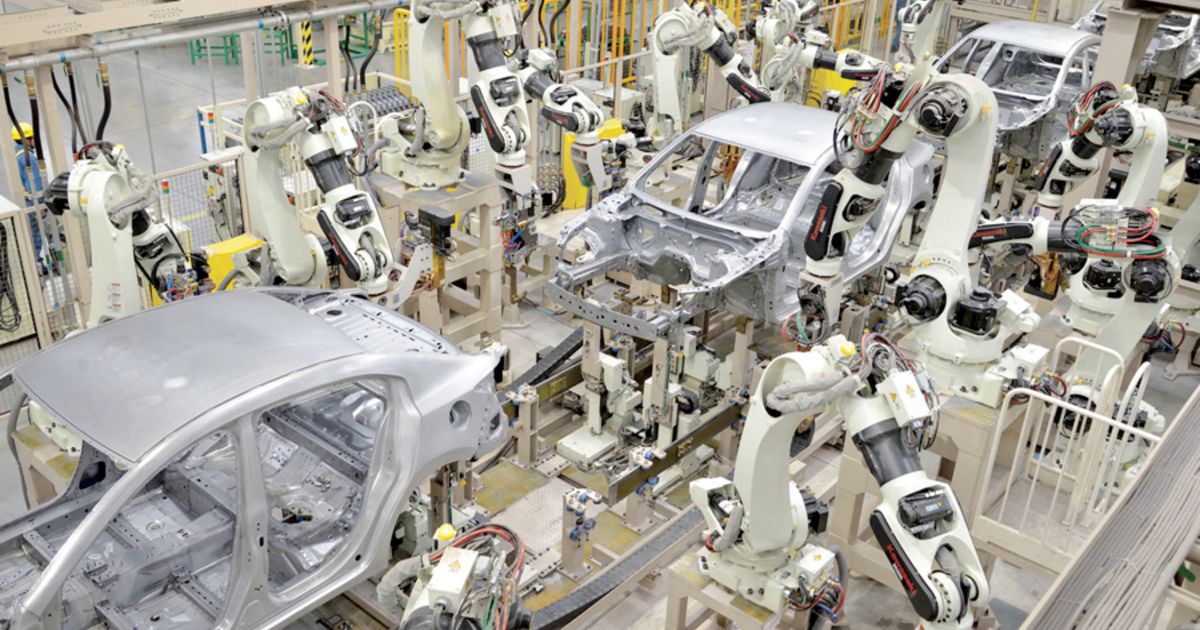
You may be confused by the SCOR model if you are new to it. The main goal of the SCOR model to help create an efficient, standardized supply chain management system.
It breaks up the supply chain in ideal business processes. Each process is then categorized based on its value to your company. It is easy to compare different supply chain activities in your company as well as across industries.
The second segment in the model is called performance measurements. This is a set of metrics you can utilize to evaluate the success of your overall supply chain operations. These metrics can help you evaluate different performance areas such as inventory management, transportation cost, supplier quality and customer service.
The data from the performance measurement can be used to determine how well your company performs in each of these areas, and then set up action items for improving your operations. You should be aware that these metrics are only valuable if they are used.
One of the first things you will need to do is create a list of current KPIs that you can monitor. Then, you can start to review each of these metrics monthly to see how your company is doing in each area.
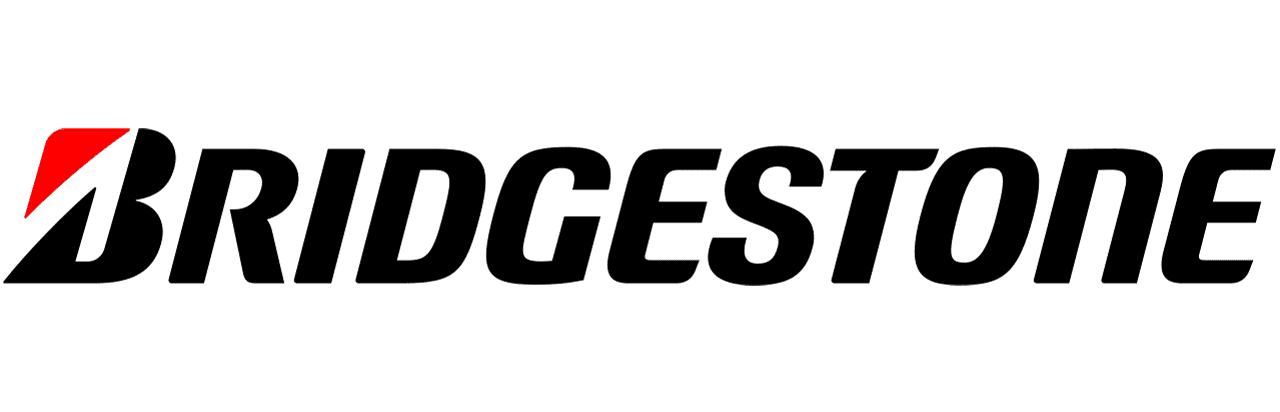
It's a great time to start thinking of new ways your company can implement business processes. This will help you improve operations and increase profits. Compare the new processes you have implemented with your existing ones to determine if they are effective.
This is an excellent way to get you and your team started in improving the supply chain operation of your company. SCOR provides companies with an opportunity to collaborate with suppliers and customers, by providing a common language and framework that can be used for measuring and analyzing the performance of supply chains.
FAQ
How is a production manager different from a producer planner?
A production planner is more involved in the planning phase of the project than a project manger.
What is the difference between Production Planning and Scheduling?
Production Planning (PP), or production planning, is the process by which you determine what products are needed at any given time. This can be done by forecasting demand and identifying production capabilities.
Scheduling is the process that assigns dates to tasks so they can get completed within a given timeframe.
What types of jobs can you find in logistics
There are many jobs available in logistics. Some examples are:
-
Warehouse workers - They load trucks and pallets.
-
Transportation drivers – They drive trucks or trailers to transport goods and perform pick-ups.
-
Freight handlers are people who sort and pack freight into warehouses.
-
Inventory managers – These people oversee inventory at warehouses.
-
Sales representatives - They sell products to customers.
-
Logistics coordinators - They organize and plan logistics operations.
-
Purchasing agents - They buy goods and services that are necessary for company operations.
-
Customer service representatives - Answer calls and email from customers.
-
Shipping clerks – They process shipping orders, and issue bills.
-
Order fillers: They fill orders based off what has been ordered and shipped.
-
Quality control inspectors (QCI) - They inspect all incoming and departing products for potential defects.
-
Others - There is a variety of other jobs in logistics. These include transportation supervisors and cargo specialists.
Statistics
- It's estimated that 10.8% of the U.S. GDP in 2020 was contributed to manufacturing. (investopedia.com)
- [54][55] These are the top 50 countries by the total value of manufacturing output in US dollars for its noted year according to World Bank.[56] (en.wikipedia.org)
- According to the United Nations Industrial Development Organization (UNIDO), China is the top manufacturer worldwide by 2019 output, producing 28.7% of the total global manufacturing output, followed by the United States, Japan, Germany, and India.[52][53] (en.wikipedia.org)
- In the United States, for example, manufacturing makes up 15% of the economic output. (twi-global.com)
- (2:04) MTO is a production technique wherein products are customized according to customer specifications, and production only starts after an order is received. (oracle.com)
External Links
How To
How to Use the 5S to Increase Productivity In Manufacturing
5S stands for "Sort", "Set In Order", "Standardize", "Separate" and "Store". Toyota Motor Corporation was the first to develop the 5S approach in 1954. It allows companies to improve their work environment, thereby achieving greater efficiency.
The basic idea behind this method is to standardize production processes, so they become repeatable, measurable, and predictable. Cleaning, sorting and packing are all done daily. This knowledge allows workers to be more efficient in their work because they are aware of what to expect.
There are five steps to implementing 5S, including Sort, Set In Order, Standardize, Separate and Store. Each step involves a different action which leads to increased efficiency. By sorting, for example, you make it easy to find the items later. When you arrange items, you place them together. Once you have separated your inventory into groups and organized them, you will store these groups in easily accessible containers. Finally, label all containers correctly.
Employees will need to be more critical about their work. Employees need to be able understand their motivations and discover alternative ways to do them. They will need to develop new skills and techniques in order for the 5S system to be implemented.
The 5S method increases efficiency and morale among employees. Once they start to notice improvements, they are motivated to keep working towards their goal of increasing efficiency.