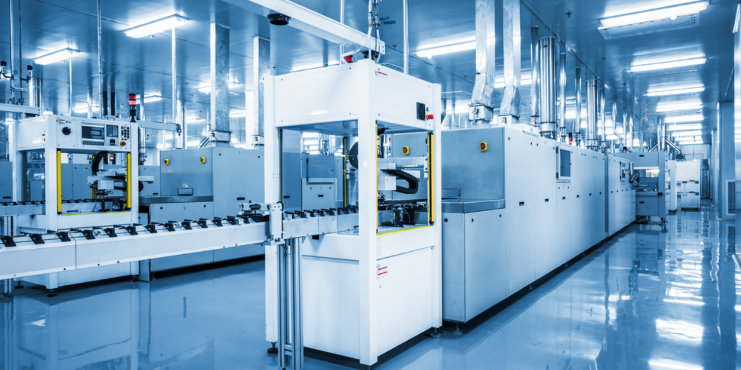
Kaizen integration into manufacturing processes can be difficult. The process is slow, requires time to procure inventory and ensure that all hands are on deck. The amount of time needed to improve the manufacturing process depends on the level of participation, the problem area, and the firm. You must follow the right implementation procedures and acquire the required resources to ensure the success of your manufacturing process improvement program. To make this strategy work, create a culture within your company that promotes continuous improvement.
Creating a company culture with a focus on improvement
According to a Gallup poll, only 32% of employees in the United States are engaged in their job. 17.2% were actively disengaged. Kaizen culture is a way to increase employee engagement. This will result in improved processes, reduced turnover, and increased innovation. Engaged employees are more likely than others to share ideas and invent, leading to greater productivity and customer satisfaction. Kaizen culture has many benefits beyond reducing waste and increasing productivity.
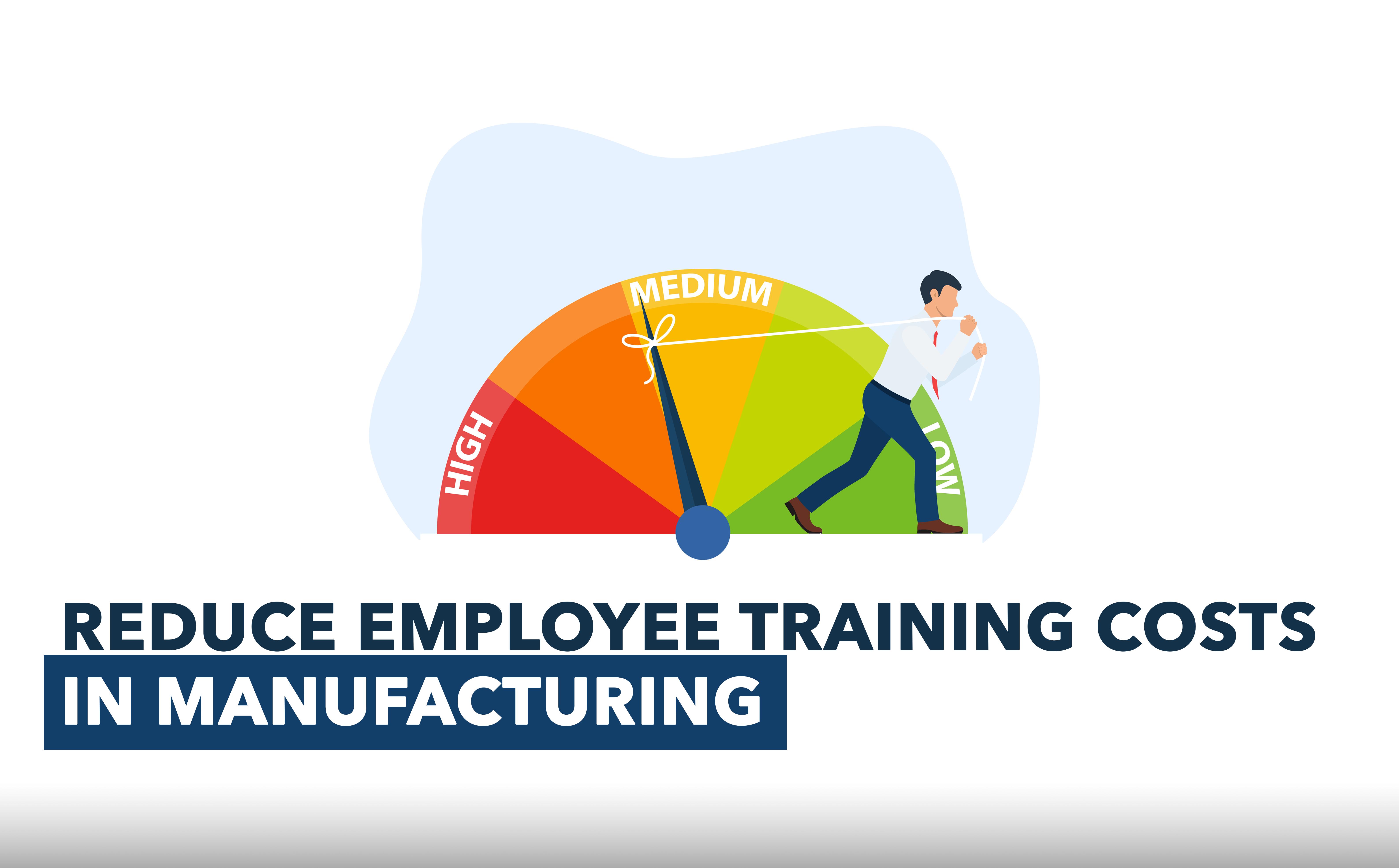
Kaizen stands for continuous improvement in all aspects of a company's business. Kaizen, which is an incremental improvement method, is better than making major, drastic changes that provide little to no benefit. Kaizen can be a method of incremental improvement that leads to reduced costs, increased productivity and better customer satisfaction. It can also improve communication and morale among employees.
There are many obstacles to implementing Kaizen in manufacturing
Although there are many benefits to implementing kaizen, there are also some drawbacks. First, implementing Kaizen in a business requires major changes to its management system. It may be difficult to reverse changes once they are made. Second, many businesses find that it is difficult to alter their work practices. This may be a barrier for kaizen.
Another problem is the fact that many manufacturers work in a "feast or framine" cycle. A machine shop will run into trouble when demand for their products drops and they can't find enough good people to hire them. In this situation, the machine shop will need to cut back on employees and close its doors. The solution is to implement kaizen or continuous improvement. This will prevent these machine shops from becoming "feast" or "famine." Implementing kaizen will increase a shop's efficiency and allow it to produce more products.
Kaizen implementation in manufacturing is a success rate
Statistics show that Kaizen implementation in the manufacturing industry is very low. Only 10% reported positive results from Kaizen implementation in their manufacturing businesses. But this does not mean that the implementation process is worthless. Implementing kaizen in lean manufacturing is a crucial component. Here are some tips to increase your manufacturing business's success rate:
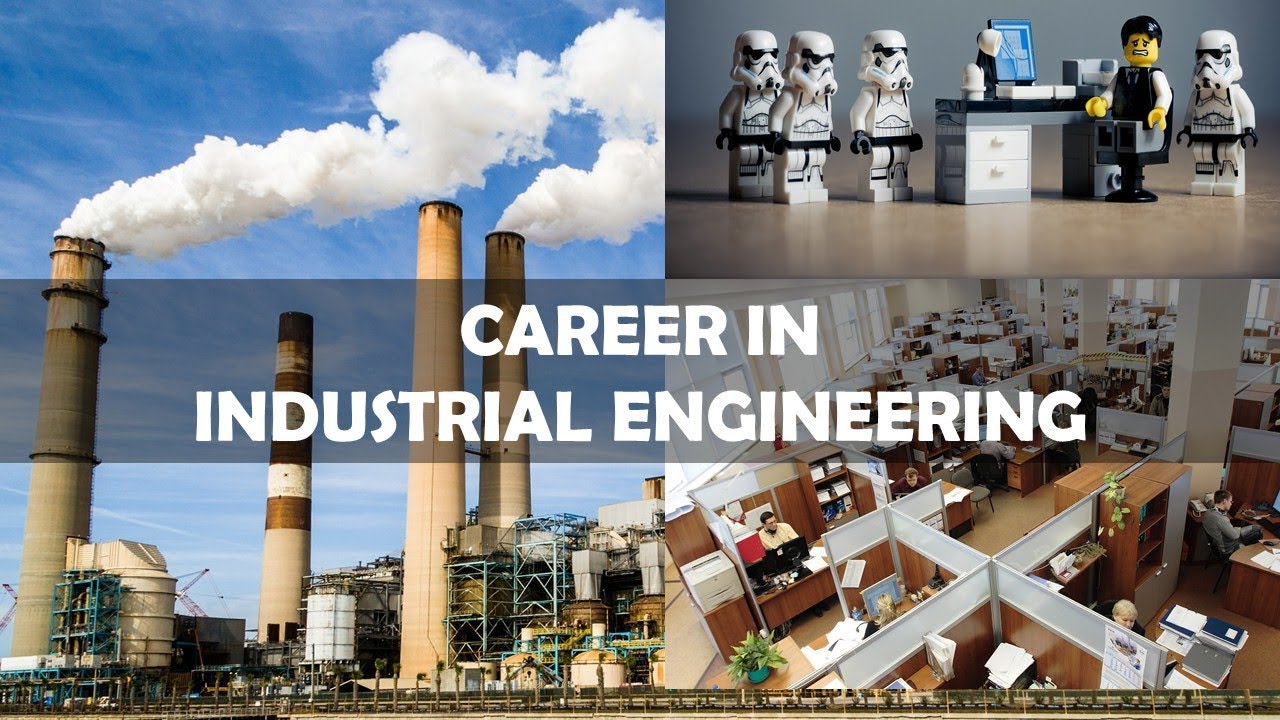
Understanding the state of the world is essential to kaizen. To identify the most important priorities, data must be collected and analyzed during the first step. Next, improvements are tested by comparing the before and after. You can also use benefit-to cost analysis to assess the impact on a particular improvement or the entire kaizen cycle. To gauge the effectiveness of the program, it is important to keep track of the results of kaizen cycle for between 60 and 90 days.
FAQ
What are the products and services of logistics?
Logistics are the activities involved in moving goods from point A to point B.
They cover all aspects of transportation, such as packing, loading, transporting and unloading.
Logisticians ensure that products reach the right destination at the right moment and under safe conditions. Logisticians help companies improve their supply chain efficiency by providing information about demand forecasts and stock levels, production schedules, as well as availability of raw materials.
They coordinate with vendors and suppliers, keep track of shipments, monitor quality standards and perform inventory and order replenishment.
Why automate your warehouse
Modern warehouses have become more dependent on automation. The rise of e-commerce has led to increased demand for faster delivery times and more efficient processes.
Warehouses need to adapt quickly to meet changing needs. They must invest heavily in technology to do this. The benefits of automating warehouses are numerous. Here are some of the reasons automation is worth your investment:
-
Increases throughput/productivity
-
Reduces errors
-
Increases accuracy
-
Safety enhancements
-
Eliminates bottlenecks
-
Allows companies scale more easily
-
Increases efficiency of workers
-
This gives you visibility into what happens in the warehouse
-
Enhances customer experience
-
Improves employee satisfaction
-
Reduces downtime and improves uptime
-
Quality products delivered on time
-
Eliminates human error
-
It helps ensure compliance with regulations
How important is automation in manufacturing?
Not only is automation important for manufacturers, but it's also vital for service providers. Automation allows them to deliver services quicker and more efficiently. It reduces human errors and improves productivity, which in turn helps them lower their costs.
What is the importance of logistics in manufacturing?
Logistics are an essential component of any business. They help you achieve great results by helping you manage all aspects of product flow, from raw materials to finished goods.
Logistics are also important in reducing costs and improving efficiency.
What are the jobs in logistics?
There are many jobs available in logistics. Here are some:
-
Warehouse workers – They load and unload pallets and trucks.
-
Transportation drivers – These drivers drive trucks and wagons to transport goods and pick up the goods.
-
Freight handlers - They sort and pack freight in warehouses.
-
Inventory managers: They are responsible for the inventory and management of warehouses.
-
Sales reps are people who sell products to customers.
-
Logistics coordinators - They organize and plan logistics operations.
-
Purchasing agents: They are responsible for purchasing goods and services to support company operations.
-
Customer service representatives are available to answer customer calls and emails.
-
Shipping clerks: They process shipping requests and issue bills.
-
Order fillers – They fill orders based upon what was ordered and shipped.
-
Quality control inspectors: They inspect outgoing and incoming products for any defects.
-
Others - There are many types of jobs in logistics such as transport supervisors and cargo specialists.
Are there ways to automate parts of manufacturing?
Yes! Yes. The Egyptians invent the wheel thousands of year ago. Robots are now used to assist us in assembly lines.
Robotics is used in many manufacturing processes today. They include:
-
Automation line robots
-
Robot welding
-
Robot painting
-
Robotics inspection
-
Robots that produce products
Manufacturing could also benefit from automation in other ways. For example, 3D printing allows us to make custom products without having to wait for weeks or months to get them manufactured.
Statistics
- According to the United Nations Industrial Development Organization (UNIDO), China is the top manufacturer worldwide by 2019 output, producing 28.7% of the total global manufacturing output, followed by the United States, Japan, Germany, and India.[52][53] (en.wikipedia.org)
- Many factories witnessed a 30% increase in output due to the shift to electric motors. (en.wikipedia.org)
- It's estimated that 10.8% of the U.S. GDP in 2020 was contributed to manufacturing. (investopedia.com)
- (2:04) MTO is a production technique wherein products are customized according to customer specifications, and production only starts after an order is received. (oracle.com)
- You can multiply the result by 100 to get the total percent of monthly overhead. (investopedia.com)
External Links
How To
How to Use the 5S to Increase Productivity In Manufacturing
5S stands for "Sort", "Set In Order", "Standardize", "Separate" and "Store". The 5S methodology was developed at Toyota Motor Corporation in 1954. It assists companies in improving their work environments and achieving higher efficiency.
The basic idea behind this method is to standardize production processes, so they become repeatable, measurable, and predictable. It means tasks like cleaning, sorting or packing, labeling, and storing are done every day. Workers can be more productive by knowing what to expect.
There are five steps to implementing 5S, including Sort, Set In Order, Standardize, Separate and Store. Each step requires a different action to increase efficiency. If you sort items, it makes them easier to find later. When you arrange items, you place them together. You then organize your inventory in groups. You can also label your containers to ensure everything is properly labeled.
Employees will need to be more critical about their work. Employees need to be able understand their motivations and discover alternative ways to do them. They must learn new skills and techniques in order to implement the 5S system.
The 5S method not only increases efficiency but also boosts morale and teamwork. They will feel motivated to strive for higher levels of efficiency once they start to see results.