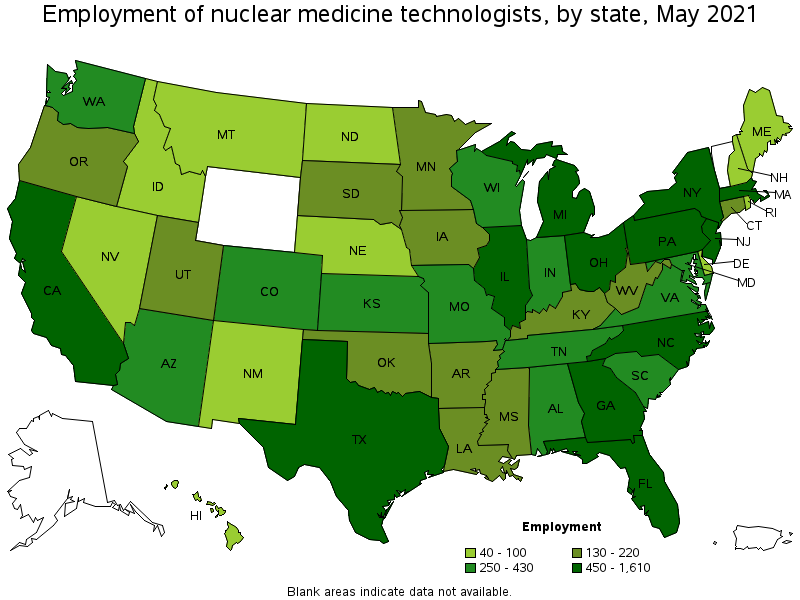
Train engineers not only have a decent income, but they also enjoy many other perks. The average train engineer salary is greater than the average person's lifetime earnings. The demand for railroad transportation positions is expected to rise by around one percent. The train engineer salary can fluctuate depending on your experience and location. Some train engineers earn well over $100,000 a year after years in the industry.
It is not an easy job to be a train engineer. First, you must complete federal licensure. After you get your license, you'll need to get some experience before you can go on to work on your own. You'll need to pass the certification exam. Usually, this includes an eye test and a vision test. You will be eligible to work for federal railroads or other transportation agencies if you pass.
Train engineers may be away from their homes for long periods of time. You might work nights or weekends. There may be times when your schedule is irregular. For example, working in the morning or on holidays. You may also be exposed for different weather types. Some cases may require you to drive electric trains. This can be challenging.
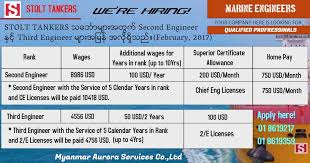
A test to assess your mechanical ability will also be required. General requirements for locomotive engineers include good eyesight, hand-eye coordination, and the ability to operate controls and follow a plan. Some cases may involve driving freight trains. In these cases, you may need to work late nights or even weekends.
Depending on your location, you may have to work in the dark, or you may have to be on call twenty-four hours a day. As long as you are able to perform the job well, it is a great way for you to make money. Train engineers get the highest salaries from large rail companies. Although they offer their own training programs for engineers, you can still get certified through a school of trades if your goal is to work for smaller railroads.
Additionally, you'll need to have a solid high school diploma as well as a clean criminal record. Although it's not required, having a degree in train engineering can help you get noticed by employers. You can also attend a trade school or community college and earn certification that will allow you to take a job as a train engineer.
The average salary for a train engineer is $5,254 per monthly. You can expect a salary that is based on your job, experience, and location. Train engineers typically earn $75,000 to $186,000 annually, according to most companies. There are many ways to get a better salary than the average, and you can even find a job that pays more. You should also keep your eyes open for job openings.
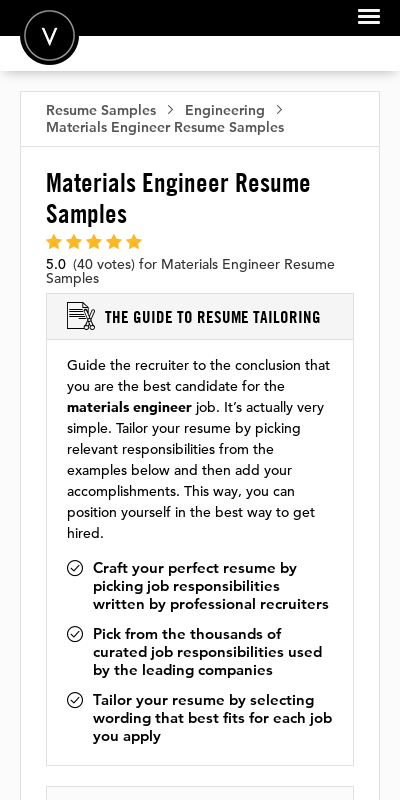
An advanced degree might also be beneficial for your pay. Some locomotive engineers may go on as train trainers or railroad schedulers. Many train engineers also find that they enjoy their jobs and will keep doing it for a long period of time.
FAQ
What are the 7 Rs of logistics management?
The acronym 7R's for Logistics stands to represent the seven basic principles in logistics management. It was developed and published by the International Association of Business Logisticians in 2004 as part of the "Seven Principles of Logistics Management".
The acronym consists of the following letters:
-
Responsible - ensure that actions are in compliance with legal requirements and do not cause harm to others.
-
Reliable: Have faith in your ability or the ability to honor any promises made.
-
Use resources effectively and sparingly.
-
Realistic - Consider all aspects of operations, including environmental impact and cost effectiveness.
-
Respectful - Treat people fairly and equitably
-
Be resourceful: Look for opportunities to save money or increase productivity.
-
Recognizable provides value-added products and services to customers
What is the difference between Production Planning and Scheduling?
Production Planning (PP) refers to the process of determining how much production is needed at any given moment. This is done through forecasting demand and identifying production capacities.
Scheduling is the process that assigns dates to tasks so they can get completed within a given timeframe.
What does manufacturing mean?
Manufacturing Industries are companies that manufacture products. Consumers are people who purchase these goods. This is accomplished by using a variety of processes, including production, distribution and retailing. They make goods from raw materials with machines and other equipment. This covers all types of manufactured goods including clothing, food, building supplies and furniture, as well as electronics, tools, machinery, vehicles and pharmaceuticals.
How does a production planner differ from a project manager?
The major difference between a Production Planner and a Project Manager is that a Project Manager is often the person responsible for organizing and planning the entire project. While a Production Planner is involved mainly in the planning stage,
What are the requirements to start a logistics business?
You need to have a lot of knowledge and skills to manage a successful logistic business. Good communication skills are essential to effectively communicate with your suppliers and clients. You need to understand how to analyze data and draw conclusions from it. You must be able to work well under pressure and handle stressful situations. In order to innovate and create new ways to improve efficiency, creativity is essential. Strong leadership qualities are essential to motivate your team and help them achieve their organizational goals.
You should also be organized and efficient to meet tight deadlines.
What does warehouse refer to?
A warehouse, or storage facility, is where goods are stored prior to being sold. It can be an outdoor or indoor area. It may also be an indoor space or an outdoor area.
Statistics
- You can multiply the result by 100 to get the total percent of monthly overhead. (investopedia.com)
- Job #1 is delivering the ordered product according to specifications: color, size, brand, and quantity. (netsuite.com)
- According to a Statista study, U.S. businesses spent $1.63 trillion on logistics in 2019, moving goods from origin to end user through various supply chain network segments. (netsuite.com)
- In 2021, an estimated 12.1 million Americans work in the manufacturing sector.6 (investopedia.com)
- According to the United Nations Industrial Development Organization (UNIDO), China is the top manufacturer worldwide by 2019 output, producing 28.7% of the total global manufacturing output, followed by the United States, Japan, Germany, and India.[52][53] (en.wikipedia.org)
External Links
How To
Six Sigma in Manufacturing:
Six Sigma is defined by "the application SPC (statistical process control) techniques to achieve continuous improvements." It was developed by Motorola's Quality Improvement Department at their plant in Tokyo, Japan, in 1986. The basic idea behind Six Sigma is to improve quality by improving processes through standardization and eliminating defects. In recent years, many companies have adopted this method because they believe there is no such thing as perfect products or services. Six Sigma's primary goal is to reduce variation from the average value of production. You can calculate the percentage of deviation from the norm by taking a sample of your product and comparing it to the average. If you notice a large deviation, then it is time to fix it.
Understanding the dynamics of variability within your business is the first step in Six Sigma. Once you understand this, you can then identify the causes of variation. It is important to identify whether the variations are random or systemic. Random variations are caused by human errors. Systematic variations can be caused by outside factors. You could consider random variations if some widgets fall off the assembly lines. If however, you notice that each time you assemble a widget it falls apart in exactly the same spot, that is a problem.
Once you've identified where the problems lie, you'll want to design solutions to eliminate those problems. That solution might involve changing the way you do things or redesigning the process altogether. To verify that the changes have worked, you need to test them again. If they fail, you can go back to the drawing board to come up with a different plan.