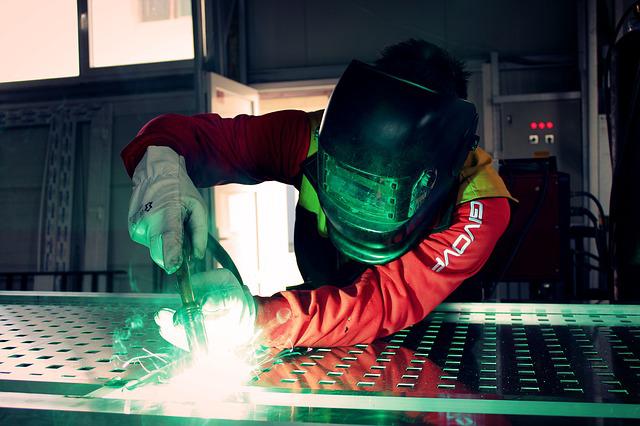
You need to consider manufacturing cost when making sure you produce a product that is financially viable. If you plan to sell wooden tabletop furniture, then you will need to purchase adhesives, wood, and other materials. To ensure that your product lasts, you need to locate a reliable supplier who can supply the highest quality raw material. You could end up with a damaged item or lost revenue if you don't use the best quality raw materials.
The best way to determine manufacturing cost is to break it up into three main categories. Each one of these costs will influence the final product price. The unit cost is a key component of manufacturing costs. It's the cost it takes to produce an item. While this number can be a good starting point, it is difficult to quantify.
When deciding the most cost-effective manufacturing method for your company, you can use either the units-per hour or unit-per–unit ratio as a guide. To illustrate, let's say you want to make 5,000 wooden table tops. You can find the average cost by subtracting the amount of time required to complete the project.
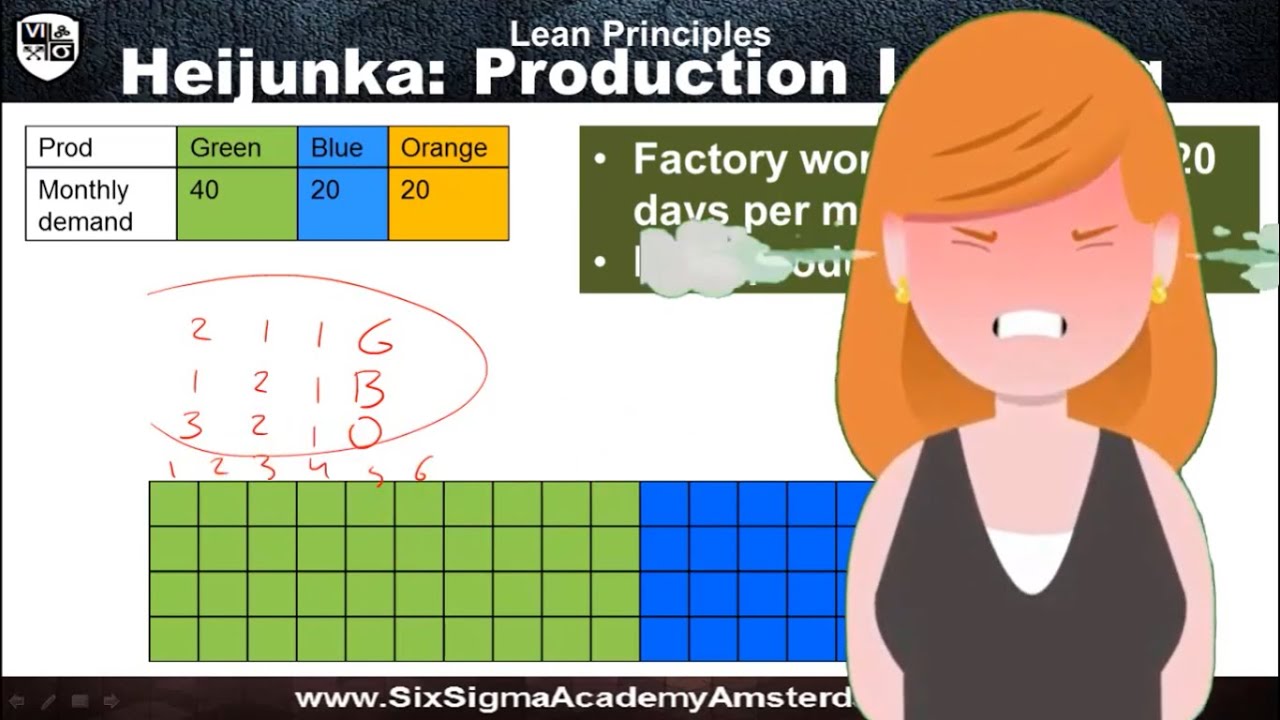
Budgeting for administrative and general expenses is essential in addition to direct labor costs and equipment manufacturing. These can include advertising costs, office supplies, rent, and sales commissions. Compliance with regulatory requirements will require you to spend substantial amounts. However, you can minimize the cost of these expenses by using online inventory control software to track production and forecast production.
Direct labor costs refer to wages that are paid to workers at a factory. They include employees who prepare the goods for manufacture. This may include sanitation staff, maintenance personnel, and bookkeepers. In general, direct labor costs about $150 an hour.
Indirect costs, which are part manufacturing, include utilities bills and equipment maintenance. To calculate the unit-per-hour you need to include the costs of preparation, assembly and delivery. The manufacturing overhead account can be used to estimate your overhead for the next fiscal year and calculate the total cost of your operations.
The manufacturing cost of a product should also be considered when calculating its manufacturing cost. Examples of these are wood, thread, and cotton. Using low quality materials can lead to an inferior final product, and if you are a food manufacturer in certain parts of the world, you'll need to test your products to make sure they are safe to eat.
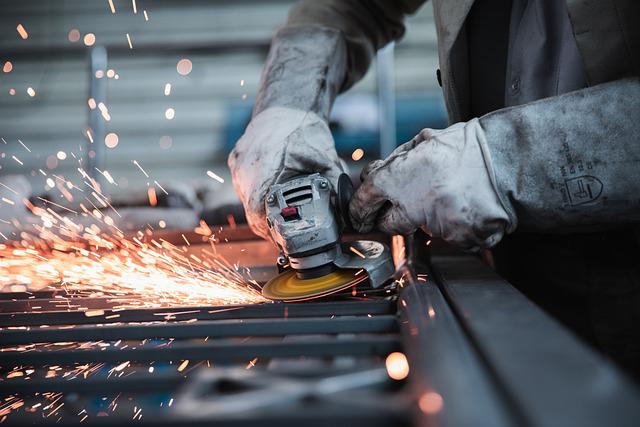
Knowing the unit-per-unit ratio and the manufacturing cost of your products will help you to figure out whether you should start producing a new product. It's also a smart idea to figure out how much you should be charging for your products, so that your business is more profitable.
FAQ
What makes a production planner different from a project manger?
The major difference between a Production Planner and a Project Manager is that a Project Manager is often the person responsible for organizing and planning the entire project. While a Production Planner is involved mainly in the planning stage,
What is the role and responsibility of a Production Planner?
Production planners ensure that all project aspects are completed on time, within budget and within the scope. They also ensure the quality of the product and service meets the client's requirements.
Why is logistics important for manufacturing?
Logistics are an essential component of any business. Logistics can help you achieve amazing results by helping to manage product flow from raw materials to finished products.
Logistics play a key role in reducing expenses and increasing efficiency.
What skills is required for a production planner?
Production planners must be flexible, organized, and able handle multiple tasks. Communication skills are essential to ensure that you can communicate effectively with clients, colleagues, and customers.
What types of jobs can you find in logistics
There are different kinds of jobs available in logistics. Some of them are:
-
Warehouse workers - They load trucks and pallets.
-
Transportation drivers – These drivers drive trucks and wagons to transport goods and pick up the goods.
-
Freight handlers are people who sort and pack freight into warehouses.
-
Inventory managers - These are responsible for overseeing the stock of goods in warehouses.
-
Sales reps - They sell products and services to customers.
-
Logistics coordinators - They plan and organize logistics operations.
-
Purchasing agents: They are responsible for purchasing goods and services to support company operations.
-
Customer service representatives - They answer calls and emails from customers.
-
Ship clerks - They issue bills and process shipping orders.
-
Order fillers - These people fill orders based on what has been ordered.
-
Quality control inspectors are responsible for inspecting incoming and outgoing products looking for defects.
-
Other - Logistics has many other job opportunities, including transportation supervisors, logistics specialists, and cargo specialists.
How can manufacturing avoid production bottlenecks
Avoiding production bottlenecks is as simple as keeping all processes running smoothly, from the time an order is received until the product ships.
This includes both planning for capacity and quality control.
Continuous improvement techniques like Six Sigma are the best way to achieve this.
Six Sigma can be used to improve the quality and decrease waste in all areas of your company.
It's all about eliminating variation and creating consistency in work.
Statistics
- Job #1 is delivering the ordered product according to specifications: color, size, brand, and quantity. (netsuite.com)
- (2:04) MTO is a production technique wherein products are customized according to customer specifications, and production only starts after an order is received. (oracle.com)
- It's estimated that 10.8% of the U.S. GDP in 2020 was contributed to manufacturing. (investopedia.com)
- [54][55] These are the top 50 countries by the total value of manufacturing output in US dollars for its noted year according to World Bank.[56] (en.wikipedia.org)
- In the United States, for example, manufacturing makes up 15% of the economic output. (twi-global.com)
External Links
How To
How to use 5S to increase Productivity in Manufacturing
5S stands for "Sort", "Set In Order", "Standardize", "Separate" and "Store". Toyota Motor Corporation was the first to develop the 5S approach in 1954. It allows companies to improve their work environment, thereby achieving greater efficiency.
The basic idea behind this method is to standardize production processes, so they become repeatable, measurable, and predictable. This means that tasks such as cleaning, sorting, storing, packing, and labeling are performed daily. Because workers know what they can expect, this helps them perform their jobs more efficiently.
Five steps are required to implement 5S: Sort, Set In Order, Standardize. Separate. Each step involves a different action which leads to increased efficiency. If you sort items, it makes them easier to find later. Once you have placed items in an ordered fashion, you will put them together. You then organize your inventory in groups. Make sure everything is correctly labeled when you label your containers.
This process requires employees to think critically about how they do their job. Employees must understand why they do certain tasks and decide if there's another way to accomplish them without relying on the old ways of doing things. They will need to develop new skills and techniques in order for the 5S system to be implemented.
The 5S Method not only improves efficiency, but it also helps employees to be more productive and happier. Once they start to notice improvements, they are motivated to keep working towards their goal of increasing efficiency.