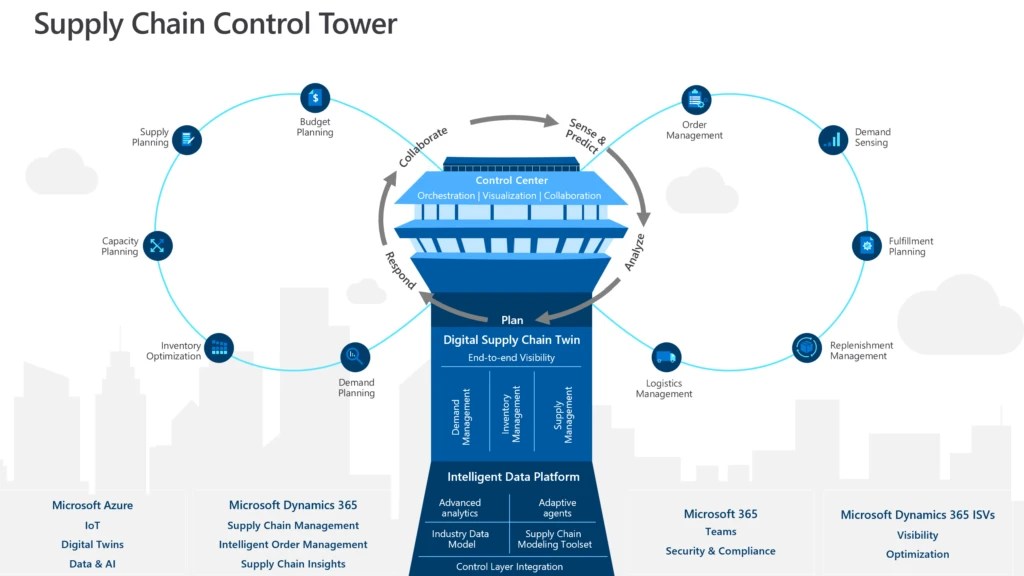
Lean system is a way of reducing waste. The belief is that each activity or process within a company must add value to a product or service provided for the customer. To achieve this, it is necessary to eliminate any activities which do not create value.
A lean management is designed to increase the performance of an organization. The system also ensures that employees are aware of the objectives and goals of their jobs.
The first step of lean system-management is to define what value is. This involves identifying what a customer wants and then creating a solution that provides that value. It is possible to achieve this by making everything, from the production process through to customer service efficient and consistent.
You can reduce costs and improve efficiency by applying lean manufacturing principles when making products. But, your staff must be on board. Without a strong commitment to the program, the results could be disastrous.
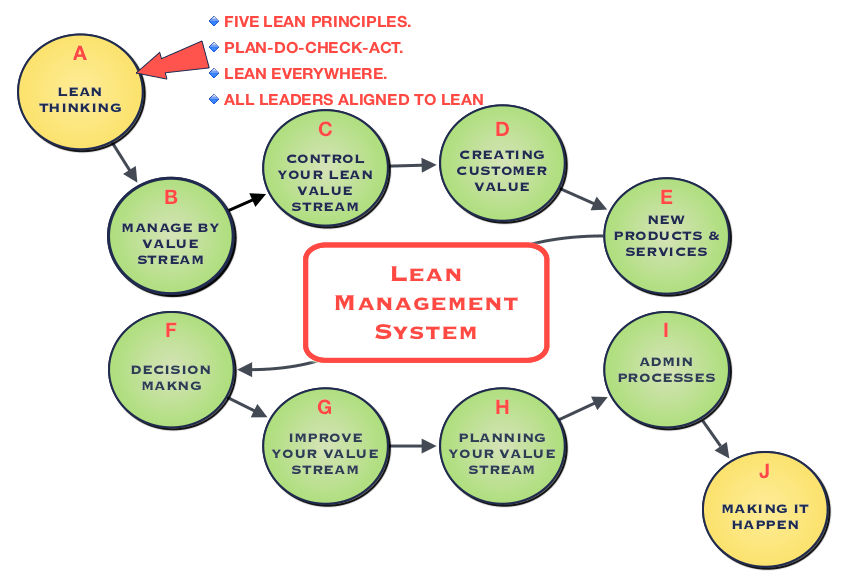
It is not enough to get the employees on board. Your organization must also have a strong supply chain. The majority of lean projects require the supply chain be retooled to work properly.
You should ensure your staff are well-trained in lean principles. This can include making sure your employees understand what waste is and why it's important to remove it from the production process.
When implementing lean principles, you should also consider the importance of teamwork. It may be hard to achieve but is an important aspect of the lean system.
Your team will be able to create better products and services, and your bottom line will increase over time. Give them the chance to meet up regularly to discuss how they can reduce waste.
A lean manager will be able to help you by ensuring all your workers are properly trained in these techniques. They can also keep your production running smoothly and efficiently, by keeping the team updated on any potential issues.
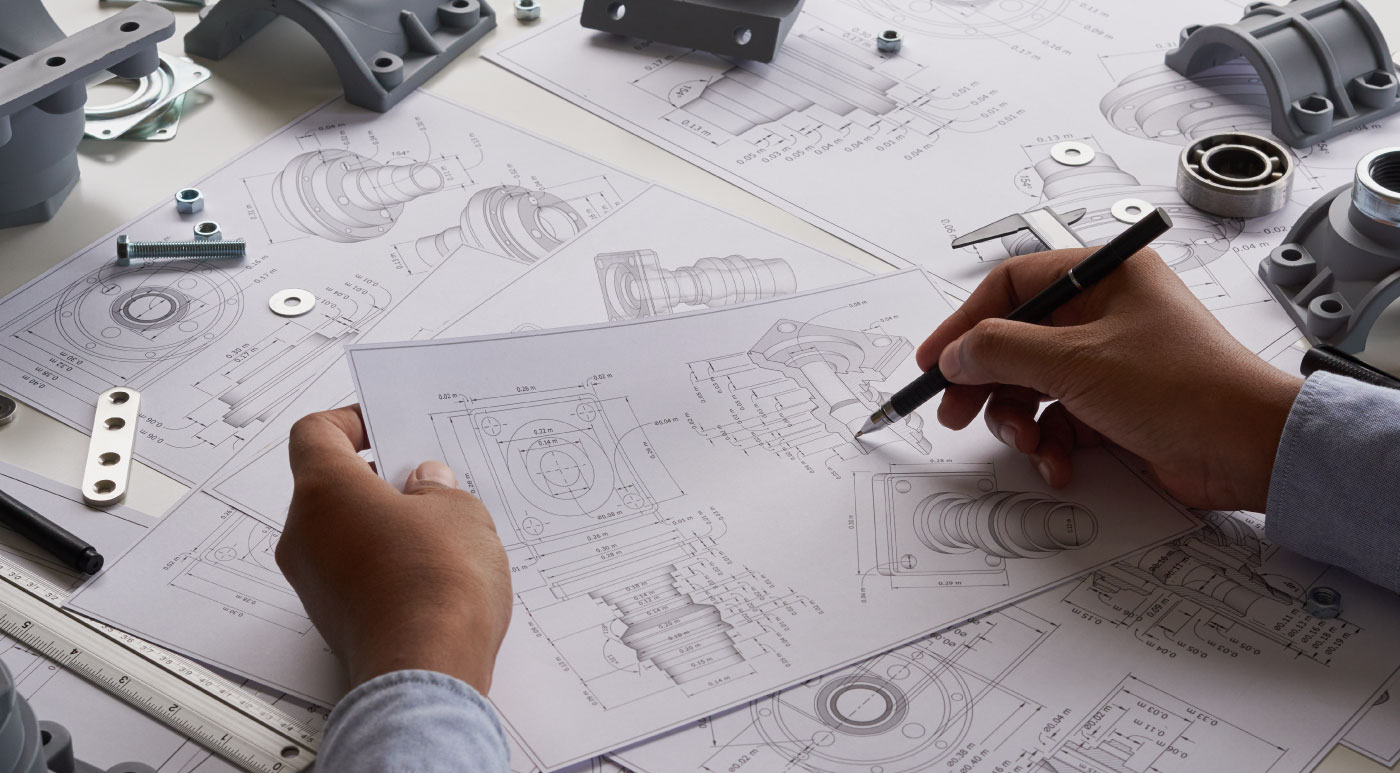
The final step of lean system implementation is to improve and monitor each procedure. It is possible to do this by monitoring the progress of every project and making sure any changes needed are implemented.
Depending on the level of your organization, you may need to hire someone to manage your lean operations. You can find people in this role by doing a search for lean management jobs or looking at job boards.
FAQ
Is there anything we should know about Manufacturing Processes prior to learning about Logistics.
No. It doesn't matter if you don't know anything about manufacturing before you learn about logistics. Understanding the manufacturing process will allow you to better understand logistics.
What is manufacturing and logistics?
Manufacturing refers to the process of making goods using raw materials and machines. Logistics includes all aspects related to supply chain management, such as procurement, distribution planning, inventory control and transportation. Manufacturing and logistics can often be grouped together to describe a larger term that covers both the creation of products, and the delivery of them to customers.
How can I learn about manufacturing?
You can learn the most about manufacturing by getting involved in it. However, if that's not possible, you can always read books or watch educational videos.
Statistics
- According to the United Nations Industrial Development Organization (UNIDO), China is the top manufacturer worldwide by 2019 output, producing 28.7% of the total global manufacturing output, followed by the United States, Japan, Germany, and India.[52][53] (en.wikipedia.org)
- It's estimated that 10.8% of the U.S. GDP in 2020 was contributed to manufacturing. (investopedia.com)
- According to a Statista study, U.S. businesses spent $1.63 trillion on logistics in 2019, moving goods from origin to end user through various supply chain network segments. (netsuite.com)
- [54][55] These are the top 50 countries by the total value of manufacturing output in US dollars for its noted year according to World Bank.[56] (en.wikipedia.org)
- In the United States, for example, manufacturing makes up 15% of the economic output. (twi-global.com)
External Links
How To
Six Sigma: How to Use it in Manufacturing
Six Sigma can be described as "the use of statistical process control (SPC), techniques to achieve continuous improvement." Motorola's Quality Improvement Department created Six Sigma at their Tokyo plant, Japan in 1986. Six Sigma is a method to improve quality through standardization and elimination of defects. Many companies have adopted this method in recent years. They believe there is no such thing a perfect product or service. Six Sigma's main objective is to reduce variations from the production average. If you take a sample and compare it with the average, you will be able to determine how much of the production process is different from the norm. If there is a significant deviation from the norm, you will know that something needs to change.
Understanding the dynamics of variability within your business is the first step in Six Sigma. Once you have this understanding, you will need to identify sources and causes of variation. Also, you will need to identify the sources of variation. Random variations occur when people do mistakes. Symmetrical variations are caused due to factors beyond the process. If you make widgets and some of them end up on the assembly line, then those are considered random variations. However, if you notice that every time you assemble a widget, it always falls apart at exactly the same place, then that would be a systematic problem.
Once you've identified where the problems lie, you'll want to design solutions to eliminate those problems. The solution could involve changing how you do things, or redesigning your entire process. Test them again once you've implemented the changes. If they don't work you need to rework them and come up a better plan.