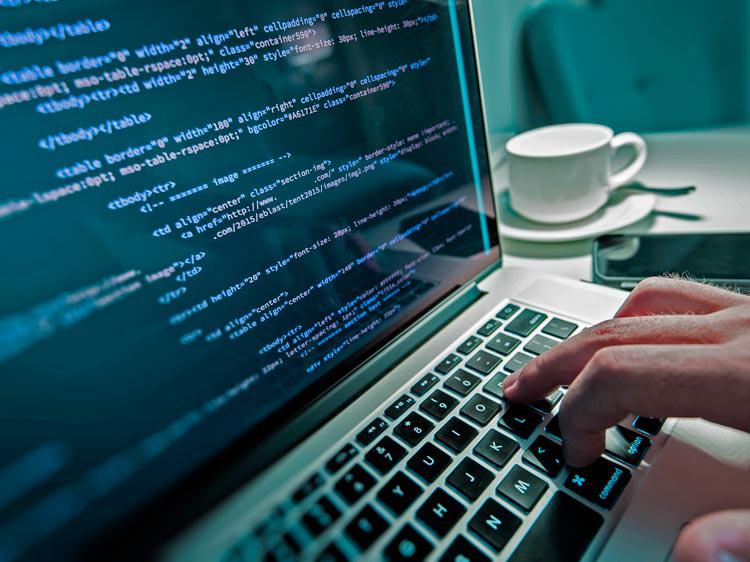
This article will cover the different types companies that are manufacturing in the U.S. The list will include industry trends as well as the costs involved in doing businesses in the U.S. Dun & Bradstreet can be a good resource for manufacturers because they collect information from a wide variety of reliable sources. This information can be used to help manufacturers assess their performance and potential growth as well as the competitive pressures. Any company looking to expand its operations will find this information invaluable.
List of American manufacturing companies
The United States comprises 50 states. This covers a large portion of North America. The northwestern region of the United States includes Alaska and Hawaii, while New York City and Washington, DC are the major cities along the Atlantic coast. Los Angeles and Chicago, two of the most important cities in America, are both known for their iconic architecture and filmmaking. There are many manufacturers in the United States. You need to be able to identify one that fits your needs.
A comprehensive list of US manufacturing companies should include contact information at all levels. The contact list can be long and include people responsible for everything from purchasing to health and safety, supply chain policies, and supply chain management. It should also include contacts for marketing and sales development, purchasing, and quality assurance. It is important not to forget that the list may have been updated.
Industry trends
As the global demand for goods increases, manufacturers are increasingly concerned about rising labor costs and raw materials. Some have chosen to reshoring while others seek to improve their ability to quickly switch production lines. With this in mind, some manufacturers are looking into automated production and other sustainable production practices. Here are some trends to keep your eye on. This article will focus on three key trends that are important for American manufacturers.
The U.S. industrial sector is a crucial indicator of the country's economic health. The economy is moving from recovery to sustained growth if there is a rebound in manufacturing. However, manufacturers face a number of challenges, including labor and raw materials, which are historically challenging. Abhijit Shahide, BofA Securities Managing Director, discusses five major trends that will drive the manufacturing industry. The manufacturing sector is becoming more resilient, in addition to technological advancements.
Cost of doing business with the U.S.
While the U.S. economy remains strong, rising costs and tariffs are clouding the business outlook. Many predict the end of the world in 2020. But no one knows when. In any case, in 2020 the cost to do business in America is likely to increase. This is good news, but it can also pose risks to newcomers.
While the cost of raw materials and labor may seem insignificant, you can't avoid the registration costs and startup costs. Your business's profitability will be affected by these costs. However, you can lower your overall costs and keep it moving forward. Look for cost-saving options if you can't reduce these expenses. Consider leasing or hiring equipment, or find more efficient ways to use your existing resources.
FAQ
How can manufacturing avoid production bottlenecks
Production bottlenecks can be avoided by ensuring that processes are running smoothly during the entire production process, starting with the receipt of an order and ending when the product ships.
This includes planning to meet capacity requirements and quality control.
Continuous improvement techniques like Six Sigma are the best way to achieve this.
Six Sigma management is a system that improves quality and reduces waste within your organization.
It's all about eliminating variation and creating consistency in work.
What are manufacturing and logistics?
Manufacturing is the process of creating goods from raw materials by using machines and processes. Logistics is the management of all aspects of supply chain activities, including procurement, production planning, distribution, warehousing, inventory control, transportation, and customer service. Logistics and manufacturing are often referred to as one thing. It encompasses both the creation of products and their delivery to customers.
What is the job of a logistics manger?
A logistics manager ensures that all goods are delivered on time and without damage. This is accomplished by using the experience and knowledge gained from working with company products. He/she should make sure that enough stock is on hand to meet the demands.
What are the 7 Rs of logistics?
The acronym 7R's for Logistics stands to represent the seven basic principles in logistics management. It was published in 2004 by the International Association of Business Logisticians as part of their "Seven Principles of Logistics Management" series.
The acronym consists of the following letters:
-
Responsible - to ensure that all actions are within the legal requirements and are not detrimental to others.
-
Reliable – have faith in your ability and capability to keep promises.
-
Be responsible - Use resources efficiently and avoid wasting them.
-
Realistic - Take into consideration all aspects of operations including cost-effectiveness, environmental impact, and other factors.
-
Respectful - Treat people fairly and equitably
-
Reliable - Find ways to save money and increase your productivity.
-
Recognizable - provide customers with value-added services.
Statistics
- Many factories witnessed a 30% increase in output due to the shift to electric motors. (en.wikipedia.org)
- In the United States, for example, manufacturing makes up 15% of the economic output. (twi-global.com)
- [54][55] These are the top 50 countries by the total value of manufacturing output in US dollars for its noted year according to World Bank.[56] (en.wikipedia.org)
- You can multiply the result by 100 to get the total percent of monthly overhead. (investopedia.com)
- (2:04) MTO is a production technique wherein products are customized according to customer specifications, and production only starts after an order is received. (oracle.com)
External Links
How To
How to Use Lean Manufacturing for the Production of Goods
Lean manufacturing is a management style that aims to increase efficiency and reduce waste through continuous improvement. It was developed by Taiichi Okono in Japan, during the 1970s & 1980s. TPS founder Kanji Takoda awarded him the Toyota Production System Award (TPS). The first book published on lean manufacturing was titled "The Machine That Changed the World" written by Michael L. Watkins and published in 1990.
Lean manufacturing, often described as a set and practice of principles, is aimed at improving the quality, speed, cost, and efficiency of products, services, and other activities. It emphasizes the elimination of defects and waste throughout the value stream. Just-in-time (JIT), zero defect (TPM), and 5S are all examples of lean manufacturing. Lean manufacturing emphasizes reducing non-value-added activities like inspection, rework and waiting.
In addition to improving product quality and reducing costs, lean manufacturing helps companies achieve their goals faster and reduces employee turnover. Lean manufacturing can be used to manage all aspects of the value chain. Customers, suppliers, distributors, retailers and employees are all included. Lean manufacturing is widely used in many industries. Toyota's philosophy is a great example of this. It has helped to create success in automobiles as well electronics, appliances and healthcare.
Five fundamental principles underlie lean manufacturing.
-
Define Value- Identify the added value your company brings to society. What makes you stand out from your competitors?
-
Reduce Waste – Eliminate all activities that don't add value throughout the supply chain.
-
Create Flow. Ensure that your work is uninterrupted and flows seamlessly.
-
Standardize and Simplify – Make processes as consistent, repeatable, and as simple as possible.
-
Build Relationships- Develop personal relationships with both internal as well as external stakeholders.
Lean manufacturing isn’t new, but it has seen a renewed interest since 2008 due to the global financial crisis. Many businesses have adopted lean manufacturing techniques to help them become more competitive. In fact, some economists believe that lean manufacturing will be an important factor in economic recovery.
Lean manufacturing is becoming a popular practice in automotive. It has many advantages. These include better customer satisfaction and lower inventory levels. They also result in lower operating costs.
Lean manufacturing can be applied to almost every aspect of an organization. Lean manufacturing is most useful in the production sector of an organisation because it ensures that each step in the value-chain is efficient and productive.
There are three types principally of lean manufacturing:
-
Just-in Time Manufacturing (JIT), also known as "pull system": This form of lean manufacturing is often referred to simply as "pull". JIT is a method in which components are assembled right at the moment of use, rather than being manufactured ahead of time. This method reduces lead times, increases availability, and decreases inventory.
-
Zero Defects Manufacturing, (ZDM): ZDM is focused on ensuring that no defective products leave the manufacturing facility. If a part needs to be fixed during the assembly line, it should be repaired rather than scrapped. This also applies to finished products that need minor repairs before being shipped.
-
Continuous Improvement (CI): CI aims to improve the efficiency of operations by continuously identifying problems and making changes in order to eliminate or minimize waste. Continuous Improvement (CI) involves continuous improvement in processes, people, tools, and infrastructure.