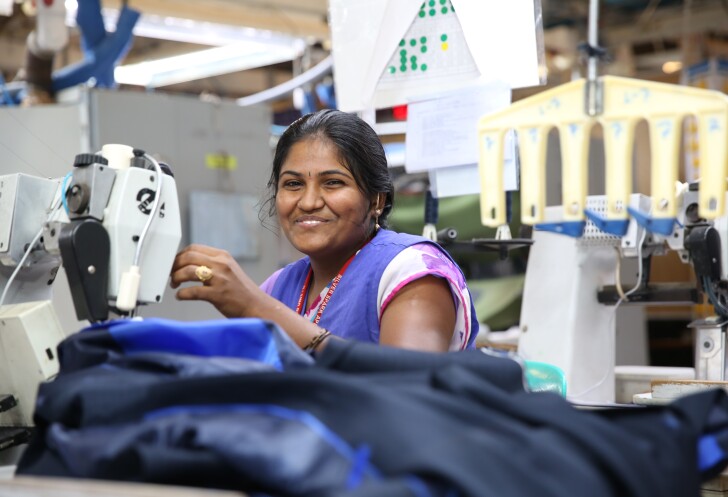
While value stream mapping is a way to improve your manufacturing process, it's not always easy. It involves mapping product families and products. Your team will need training and may even need a value stream manager to help them. Leadership should also support the implementation of your strategy. Larger companies usually have their own value stream manager who oversees the mapping process. While smaller businesses can work without a VSM manager for their mapping process, it can be advantageous to show leadership the improvement opportunities.
Lean Six Sigma
Value Stream Mapping in Lean Six Sigma will allow you to document the flow information from customers to suppliers. The first thing to put on your value stream map is your customer. Start at the shipping point and work your way upstream. Include a box with a customer's data, which will tell you how often a product must be produced in order to meet the demand. You will also need to know your Takt time. This is how long it takes to produce a product, and how that compares to the product's cycle. A bottleneck is when Takt time exceeds the cycle time.
Value Stream Maps help companies identify waste at all stages of their operations. Value stream mapping allows you to identify non-value added activities and analyze the flow data. This can help you identify potential threats and opportunities for your business. It can help you identify bottlenecks in your business and pinpoint areas where you can make improvements to make it more efficient. Value Stream Mapping is a great tool for improving information flow. It can help you implement Lean Six Sigma and increase your bottom line.
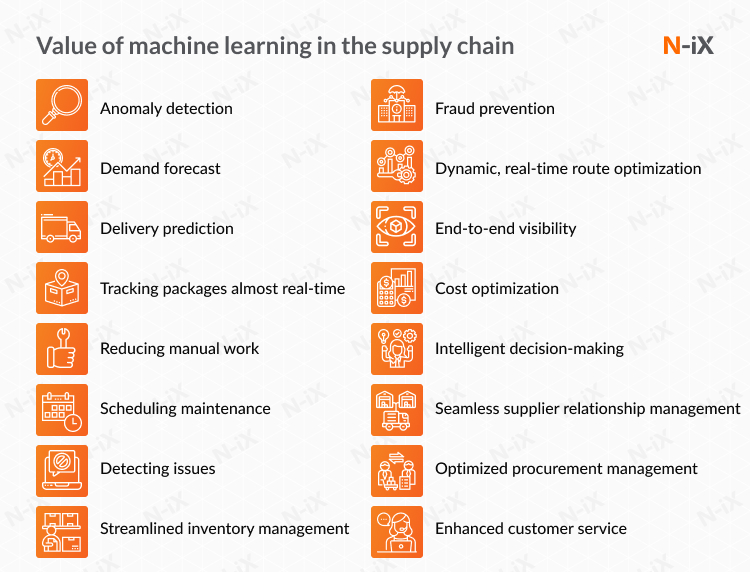
Lean Healthcare
Value stream mapping is a tool used to improve synchronization of activities in the medical field. It helps identify areas for improvement and identifies implementation strategies. For example, a map can depict a patient's flow from the moment they arrive in the hospital, to the time they leave after treatment. These flow paths can be used to visualize the entire process and help identify value-added and waste-generating actions.
The authors suggest that you define the terms used in VSM in Lean Healthcare in order to improve its effectiveness. They also recommend establishing appropriate indicators and sharing examples of success and failure. These indicators can be used to replicate the results and adapt them to specific situations. Positive outcomes are more likely to be achieved by using lean methods in the healthcare sector. The authors recommend that healthcare professionals agree on a common definition for value stream mapping to ensure that this methodology is widely used.
Lean Manufacturing
In order to begin value stream mapping, you need input from key stakeholders. The team should include all people responsible to fulfill customer needs. They should also include the people who perform tasks or activities that are critical to the flow of information and materials. By gathering input from these key stakeholders, value stream mapping can help identify waste, and ultimately improve efficiency. The scope of the value streaming mapping process must be defined.
Next, you will need to choose the product/process that needs improvement and then train the team in value stream modeling. The mapping process begins by identifying the customer's needs. This includes all information received, as well as the communication and decision-making processes. Value stream mapping helps to reduce waste and improve customer satisfaction. Lean manufacturing can provide a viable, sustainable solution that addresses the unique challenges faced by any company by identifying and eliminating those elements.
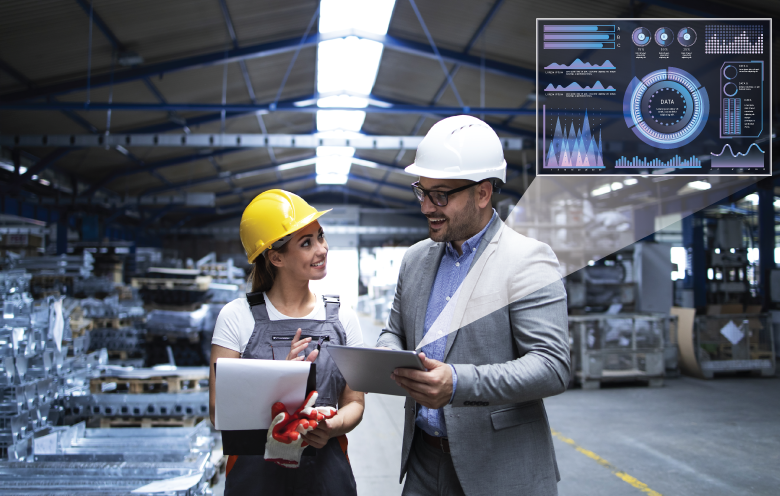
Future state value stream mapping
Future state value stream maps are a powerful tool for identifying waste. This type of mapping helps to identify the causes and eliminate them. Future state ideas will be marked with the same symbols used in current state mapping. Takt Time is a key concept in future state value stream mapping. It allows you to allocate resources effectively and to identify areas of waste. Your company can also use the future state value stream map as a powerful tool.
Once you've determined where problems are and how they relate to the future state, it's time to map the steps you need to take to get there. As teams complete projects and achieve the target value, a future state map can serve as a constant reference point. It is important to update your future stream mapping of state value every six to twelve mois to ensure that you are able to monitor your progress. It is important to update the future statemap as new projects and changes are implemented.
FAQ
What is the difference between manufacturing and logistics
Manufacturing is the act of producing goods from raw materials using machines and processes. Logistics includes all aspects related to supply chain management, such as procurement, distribution planning, inventory control and transportation. Manufacturing and logistics are often considered together as a broader term that encompasses both the process of creating products and delivering them to customers.
What are the essential elements of running a logistics firm?
You need to have a lot of knowledge and skills to manage a successful logistic business. For clients and suppliers to be successful, you need to have excellent communication skills. You must be able analyze data and draw out conclusions. You must be able to work well under pressure and handle stressful situations. To increase efficiency and creativity, you need to be creative. Strong leadership qualities are essential to motivate your team and help them achieve their organizational goals.
It is also important to be efficient and well organized in order meet deadlines.
What makes a production planner different from a project manger?
The major difference between a Production Planner and a Project Manager is that a Project Manager is often the person responsible for organizing and planning the entire project. While a Production Planner is involved mainly in the planning stage,
Why is logistics important in manufacturing
Logistics are an integral part any business. They help you achieve great results by helping you manage all aspects of product flow, from raw materials to finished goods.
Logistics play a key role in reducing expenses and increasing efficiency.
What does manufacturing mean?
Manufacturing Industries are companies that manufacture products. Consumers are people who purchase these goods. These companies use a variety processes such as distribution, retailing and management to accomplish their purpose. These companies produce goods using raw materials and other equipment. This covers all types of manufactured goods including clothing, food, building supplies and furniture, as well as electronics, tools, machinery, vehicles and pharmaceuticals.
What is the difference between Production Planning, Scheduling and Production Planning?
Production Planning (PP), also known as forecasting and identifying production capacities, is the process that determines what product needs to be produced at any particular time. This is accomplished by forecasting the demand and identifying production resources.
Scheduling refers the process by which tasks are assigned dates so that they can all be completed within the given timeframe.
Statistics
- In 2021, an estimated 12.1 million Americans work in the manufacturing sector.6 (investopedia.com)
- Job #1 is delivering the ordered product according to specifications: color, size, brand, and quantity. (netsuite.com)
- You can multiply the result by 100 to get the total percent of monthly overhead. (investopedia.com)
- It's estimated that 10.8% of the U.S. GDP in 2020 was contributed to manufacturing. (investopedia.com)
- According to the United Nations Industrial Development Organization (UNIDO), China is the top manufacturer worldwide by 2019 output, producing 28.7% of the total global manufacturing output, followed by the United States, Japan, Germany, and India.[52][53] (en.wikipedia.org)
External Links
How To
How to Use lean manufacturing in the Production of Goods
Lean manufacturing is a management style that aims to increase efficiency and reduce waste through continuous improvement. It was first developed in Japan in the 1970s/80s by Taiichi Ahno, who was awarded the Toyota Production System (TPS), award from KanjiToyoda, the founder of TPS. Michael L. Watkins published the "The Machine That Changed the World", the first book about lean manufacturing. It was published in 1990.
Lean manufacturing, often described as a set and practice of principles, is aimed at improving the quality, speed, cost, and efficiency of products, services, and other activities. It emphasizes eliminating waste and defects throughout the value stream. Lean manufacturing is called just-in-time (JIT), zero defect, total productive maintenance (TPM), or 5S. Lean manufacturing eliminates non-value-added tasks like inspection, rework, waiting.
Lean manufacturing not only improves product quality but also reduces costs. Companies can also achieve their goals faster by reducing employee turnover. Lean manufacturing is a great way to manage the entire value chain including customers, suppliers, distributors and retailers as well as employees. Many industries worldwide use lean manufacturing. Toyota's philosophy is a great example of this. It has helped to create success in automobiles as well electronics, appliances and healthcare.
Lean manufacturing includes five basic principles:
-
Define Value- Identify the added value your company brings to society. What makes you stand out from your competitors?
-
Reduce Waste - Eliminate any activity that doesn't add value along the supply chain.
-
Create Flow - Make sure work runs smoothly without interruptions.
-
Standardize and Simplify – Make processes as consistent, repeatable, and as simple as possible.
-
Build Relationships- Develop personal relationships with both internal as well as external stakeholders.
Although lean manufacturing has always been around, it is gaining popularity in recent years because of a renewed interest for the economy after 2008's global financial crisis. Many businesses have adopted lean production techniques to make them more competitive. Many economists believe lean manufacturing will play a major role in economic recovery.
Lean manufacturing is becoming a popular practice in automotive. It has many advantages. These include improved customer satisfaction, reduced inventory levels, lower operating costs, increased productivity, and better overall safety.
The principles of lean manufacturing can be applied in almost any area of an organization. This is because it ensures efficiency and effectiveness in all stages of the value chain.
There are three types principally of lean manufacturing:
-
Just-in-Time Manufacturing (JIT): This type of lean manufacturing is commonly referred to as "pull systems." JIT is a method in which components are assembled right at the moment of use, rather than being manufactured ahead of time. This strategy aims to decrease lead times, increase availability of parts and reduce inventory.
-
Zero Defects Manufacturing (ZDM): ZDM focuses on ensuring that no defective units leave the manufacturing facility. If a part is required to be repaired on the assembly line, it should not be scrapped. This also applies to finished products that need minor repairs before being shipped.
-
Continuous Improvement (CI), also known as Continuous Improvement, aims at improving the efficiency of operations through continuous identification and improvement to minimize or eliminate waste. Continuous Improvement involves continuous improvement of processes.