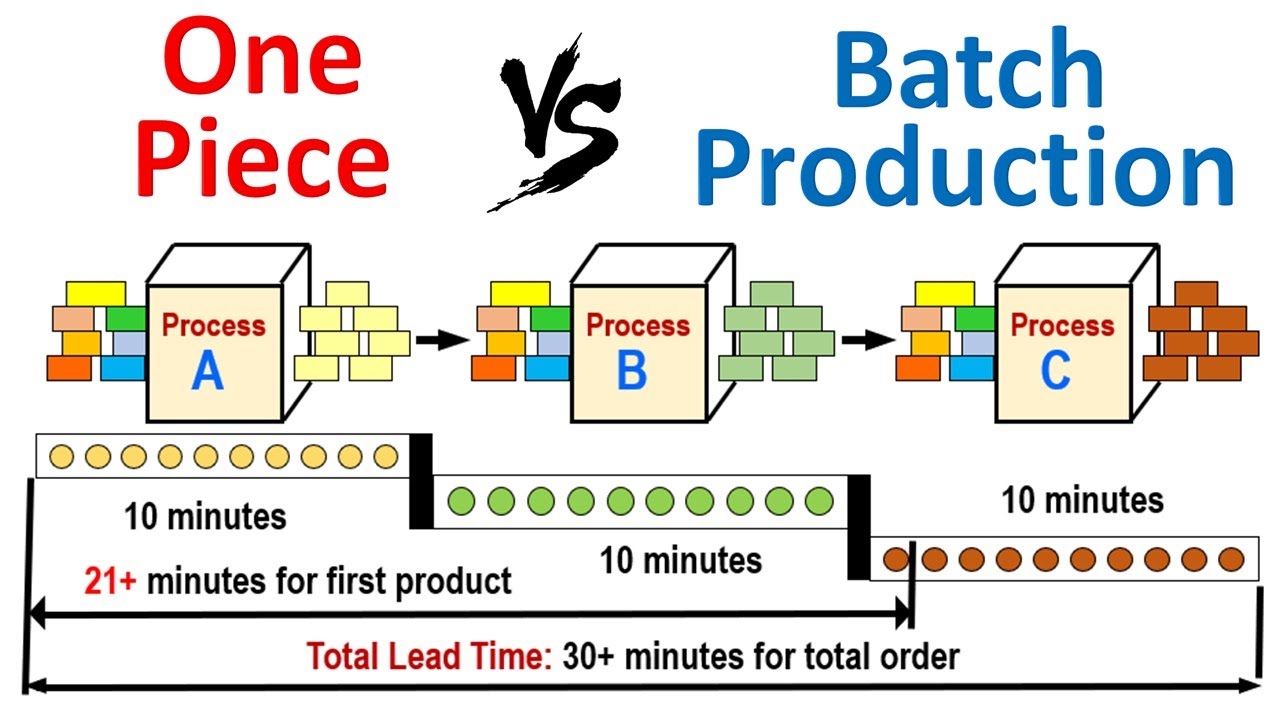
Despite the recent economic revival, the US Manufacturing sector is still a key contributor of the national economy. It supports 12.8million jobs, accounts for one percent of private-sector work, and employs more people than the average American. However, it has seen its share in the national output decline since the Great Recession. And its employment rate has fallen to just 12 percent. Manufacturing has been experiencing structural problems including productivity and trade deficits. Although these issues are slowly being addressed, it is not clear what the long-term impact of these issues will be. Although the US manufacturing sector appears to be in a positive place, it is up to the United States to decide if it should rebound.
Manufacturing is a capital-intensive business. This sector is evolving as new technologies are developed. To increase their productivity and improve the skills of their employees, firms are investing in new technologies. They also develop a workforce of future workers. Manufacturers are also investing in the upskilling of their current workforce. These investments will help to increase their market share. Firms are also working to improve their supply chains in order to prevent future disruptions.
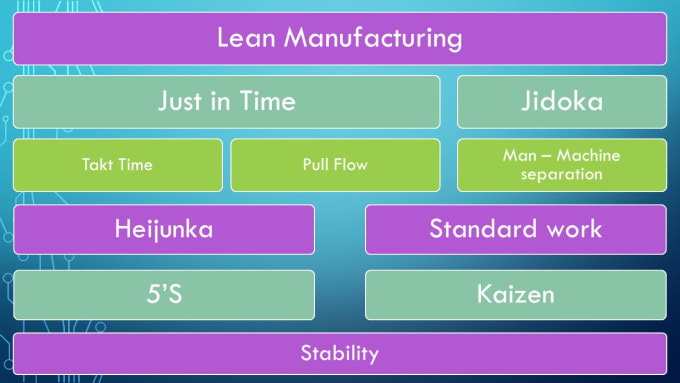
Manufacturers are confronting increasing costs due to supply chain problems. These challenges can be addressed by the US by strengthening its innovation system. The US will need avoid tariff wars from countries that want to import to the US and will need to maintain open-trade policies to keep its manufacturer competitive.
The United States has an international presence that has increased over the past century. As a result, the United States has a large share of the world's oil and gas demand. It is, however, at risk of losing the title of world's largest manufacturing economy. Because of its low level of international immigration and aging population, this is a serious threat to its position as the world's leading manufacturing economy. It is also in a strong position to be more competitive through investments in new technologies that will increase production efficiency and make the company more sustainable.
US manufacturing contributes $2.3 trillion to GDP. This figure is 20 percent of the nation’s capital investment, and 35 percent productivity growth. In Q1 2018, the manufacturing output hit a new record of $2.00 Trillion. This figure is a record in US manufacturing since the Great Recession. Manufacturing output is stronger than the recovery.
The United States has the second-largest global manufacturing presence, after China. The nation's 60 percent exports are made up of manufacturing, which accounts for a significant portion of R&D spending. However, manufacturing output declined from the fourth quarter of 2007 to the first quarter of 2009. In a few states, however, manufacturing output declined. Manufacturing is more prominent in the Eighth District states. In many of these states, manufacturing output shares have increased.
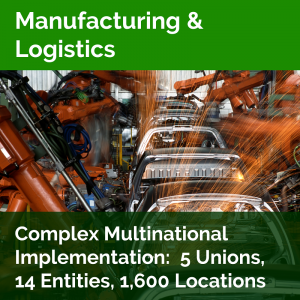
Manufacturing output was 15.2 percent below pre-pandemic levels in the fourth quarter of 2007. In the first quarter, 2009 saw a drop in manufacturing output of 6.4 percent. However, manufacturing output increased in Illinois and Indiana as well as Ohio and Michigan.
FAQ
What are manufacturing & logistics?
Manufacturing is the act of producing goods from raw materials using machines and processes. Logistics includes all aspects related to supply chain management, such as procurement, distribution planning, inventory control and transportation. As a broad term, manufacturing and logistics often refer to both the creation and delivery of products.
What are the 4 types manufacturing?
Manufacturing is the process that transforms raw materials into useful products. It involves many different activities such as designing, building, testing, packaging, shipping, selling, servicing, etc.
What is the difference between Production Planning and Scheduling?
Production Planning (PP) is the process of determining what needs to be produced at any given point in time. Forecasting and identifying production capacity are two key elements to this process.
Scheduling refers the process by which tasks are assigned dates so that they can all be completed within the given timeframe.
How can we increase manufacturing efficiency?
First, determine which factors have the greatest impact on production time. We then need to figure out how to improve these variables. If you don't know where to start, then think about which factor(s) have the biggest impact on production time. Once you have identified them, it is time to identify solutions.
Why automate your warehouse
Modern warehousing has seen automation take center stage. E-commerce has increased the demand for quicker delivery times and more efficient processes.
Warehouses need to adapt quickly to meet changing needs. To do so, they must invest heavily in technology. Automating warehouses is a great way to save money. These are some of the benefits that automation can bring to warehouses:
-
Increases throughput/productivity
-
Reduces errors
-
Improves accuracy
-
Safety Boosts
-
Eliminates bottlenecks
-
This allows companies to scale easily
-
It makes workers more efficient
-
Provides visibility into everything that happens in the warehouse
-
Enhances customer experience
-
Improves employee satisfaction
-
Reducing downtime and increasing uptime
-
You can be sure that high-quality products will arrive on time
-
Removing human error
-
It ensures compliance with regulations
Do we need to know about Manufacturing Processes before learning about Logistics?
No. No. It is important to know about the manufacturing processes in order to understand how logistics works.
Statistics
- Job #1 is delivering the ordered product according to specifications: color, size, brand, and quantity. (netsuite.com)
- According to the United Nations Industrial Development Organization (UNIDO), China is the top manufacturer worldwide by 2019 output, producing 28.7% of the total global manufacturing output, followed by the United States, Japan, Germany, and India.[52][53] (en.wikipedia.org)
- [54][55] These are the top 50 countries by the total value of manufacturing output in US dollars for its noted year according to World Bank.[56] (en.wikipedia.org)
- (2:04) MTO is a production technique wherein products are customized according to customer specifications, and production only starts after an order is received. (oracle.com)
- You can multiply the result by 100 to get the total percent of monthly overhead. (investopedia.com)
External Links
How To
How to use the Just In-Time Production Method
Just-in-time (JIT) is a method that is used to reduce costs and maximize efficiency in business processes. It allows you to get the right amount resources at the right time. This means that you only pay the amount you actually use. Frederick Taylor developed the concept while working as foreman in early 1900s. He observed how workers were paid overtime if there were delays in their work. He decided that workers would be more productive if they had enough time to complete their work before they started to work.
JIT is an acronym that means you need to plan ahead so you don’t waste your money. The entire project should be looked at from start to finish. You need to ensure you have enough resources to tackle any issues that might arise. You can anticipate problems and have enough equipment and people available to fix them. This will prevent you from spending extra money on unnecessary things.
There are many JIT methods.
-
Demand-driven: This JIT is where you place regular orders for the parts/materials that are needed for your project. This will allow you to track how much material you have left over after using it. This will let you know how long it will be to produce more.
-
Inventory-based: This is a type where you stock the materials required for your projects in advance. This allows you to predict how much you can expect to sell.
-
Project-driven: This is an approach where you set aside enough funds to cover the cost of your project. Knowing how much money you have available will help you purchase the correct amount of materials.
-
Resource-based JIT: This is the most popular form of JIT. Here you can allocate certain resources based purely on demand. You might assign more people to help with orders if there are many. If you don’t have many orders you will assign less people to the work.
-
Cost-based : This is similar in concept to resource-based. But here, you aren't concerned about how many people your company has but how much each individual costs.
-
Price-based: This is very similar to cost-based, except that instead of looking at how much each individual worker costs, you look at the overall price of the company.
-
Material-based: This is quite similar to cost-based, but instead of looking at the total cost of the company, you're concerned with how much raw materials you spend on average.
-
Time-based JIT: A variation on resource-based JIT. Instead of focusing only on how much each employee is costing, you should focus on how long it takes to complete your project.
-
Quality-based JIT: This is another variation of resource based JIT. Instead of looking at the labor costs and time it takes to make a product, think about its quality.
-
Value-based: This is one of the newest forms of JIT. You don't worry about whether the products work or if they meet customer expectations. Instead, your focus is on the value you bring to the market.
-
Stock-based: This is an inventory-based method that focuses on the actual number of items being produced at any given time. It's useful when you want maximum production and minimal inventory.
-
Just-in-time (JIT) planning: This is a combination of JIT and supply chain management. It's the process of scheduling delivery of components immediately after they are ordered. This is important as it reduces lead time and increases throughput.