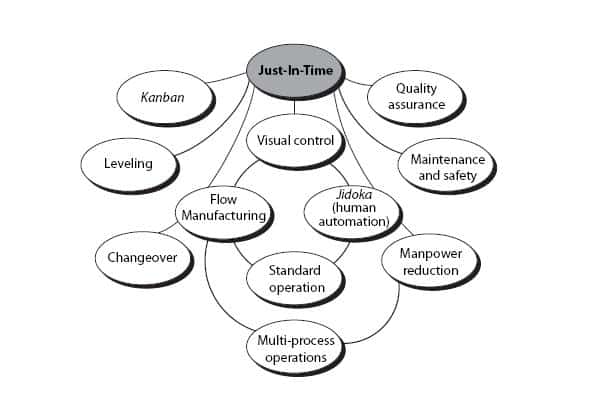
Supply chain risk management, regardless of how small or large your business is, is vital to maintaining a strong operation. There are many possible risks, from the small to the large. Protect your company from loss with a well-planned plan.
Data sharing is one of the most critical aspects of a supply-chain continuity plan. If your organization is dependent on a single supplier it can lead to supplier disputes and vendor failures. You will be more likely to avoid supply interruptions if your company is part-of a multisupplier group. You may be able to find an alternative supplier.
If your company has multiple contractors, there is a greater chance of vendor fraud, duplicate billing and improper related party billing. A risk assessment methodology can be used to mitigate these risks. It can include a complete assessment of your suppliers and partners as well as other tier one components.
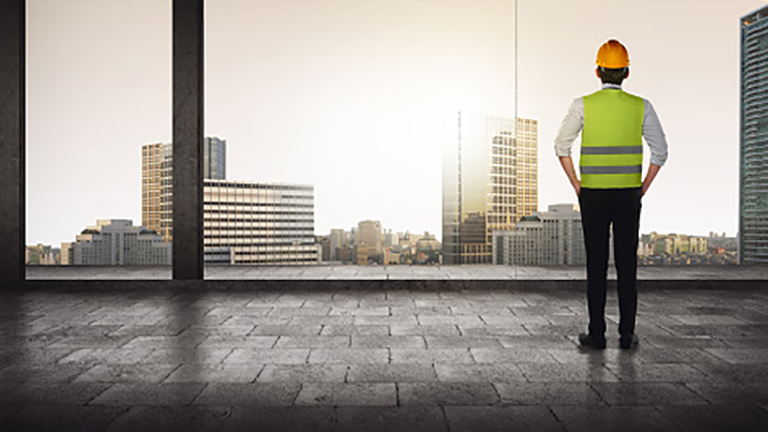
When developing a good supply chain risk management program, you should first identify the important elements of a good supply chain, then quantify and measure them, and then devise an action plan. These items should be combined with a few additional. A proactive monitoring system is crucial. It is important that your executives have access to real-time, accurate information regarding supply chain risk. You can make better decisions and react quickly by monitoring supply risk in real-time.
While you are assessing your risks and quantifying them, it is crucial to keep in view that your supply chain's ability to withstand disruption is a function if governance. You must also consider the roles of stakeholders. A properly scorecarded supplier system could have saved the pharmacy from a bankruptcy.
A well-planned plan is essential for minimizing supply chain crises. But it can be difficult to put together the right contingency plans. Many companies fail to plan enough contingency strategies for each risk they manage. This should start with the greatest possible impact.
The PPPR (preventive preparation, response, and recovery) is a standard worldwide for supply chain risk management. It is a solid approach that will improve your ability to react to supply-chain disruptions and can be used with other strategies to protect you organization from them. Using a PPPR as a guide can help you make the right decisions and stay ahead of your competition in today's marketplace.
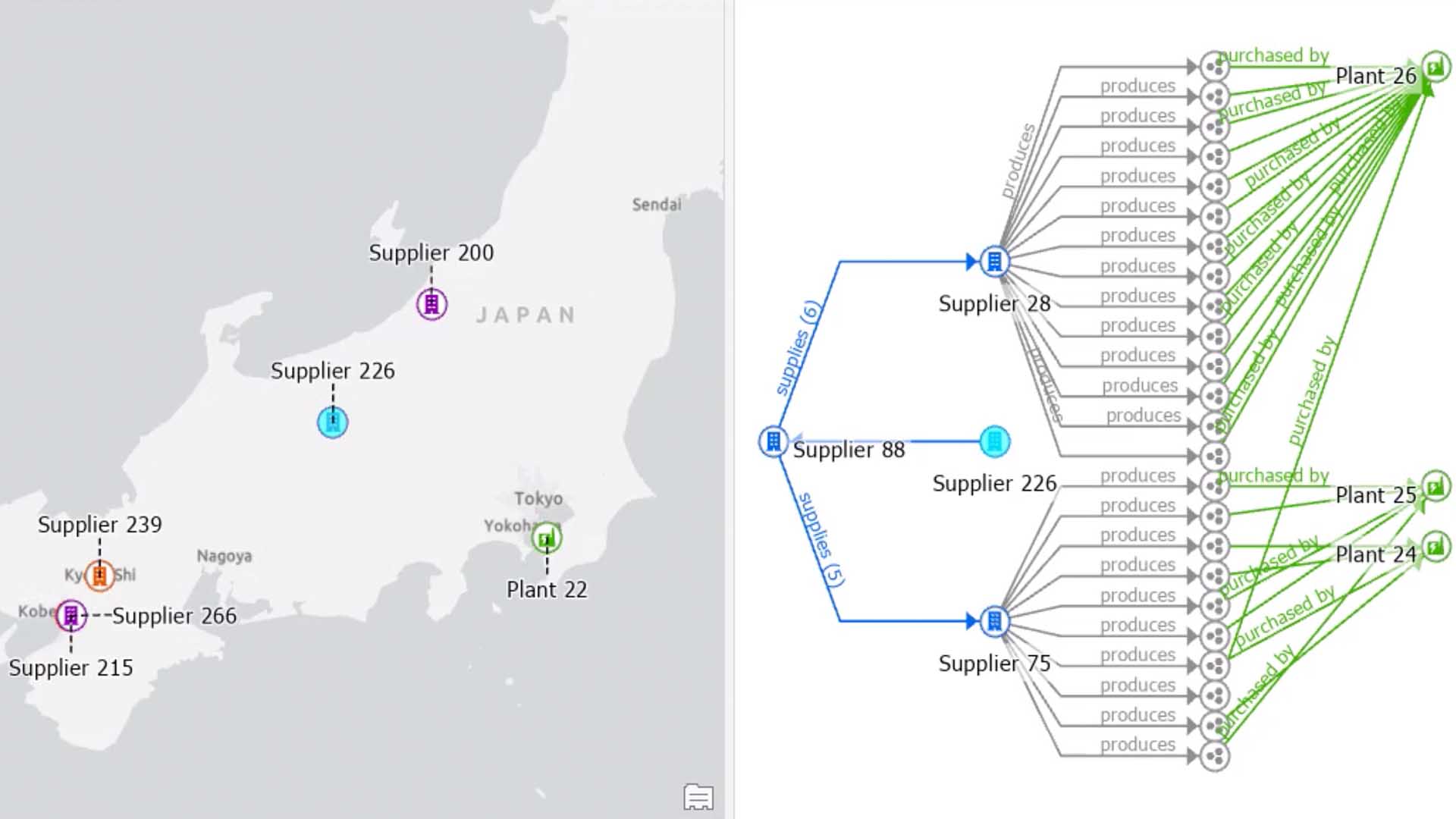
It is possible to get the right information from your suppliers to help you understand their history and offer. This can inform your decision-making, whether you are looking to expand your sourcing efforts or you are just fine-tuning your current processes. You can provide the right risk premiums to your insurers by having reliable data.
FAQ
Is automation necessary in manufacturing?
Automation is essential for both manufacturers and service providers. It allows them provide faster and more efficient services. It reduces human errors and improves productivity, which in turn helps them lower their costs.
How can manufacturing reduce production bottlenecks?
You can avoid bottlenecks in production by making sure that everything runs smoothly throughout the production cycle, from the moment you receive an order to the moment the product is shipped.
This includes planning to meet capacity requirements and quality control.
Continuous improvement techniques such Six Sigma can help you achieve this.
Six Sigma is a management method that helps to improve quality and reduce waste.
It focuses on eliminating variation and creating consistency in your work.
Why is logistics important in manufacturing
Logistics is an integral part of every business. They are essential to any business's success.
Logistics also play a major role in reducing costs and increasing efficiency.
Statistics
- In the United States, for example, manufacturing makes up 15% of the economic output. (twi-global.com)
- (2:04) MTO is a production technique wherein products are customized according to customer specifications, and production only starts after an order is received. (oracle.com)
- It's estimated that 10.8% of the U.S. GDP in 2020 was contributed to manufacturing. (investopedia.com)
- Job #1 is delivering the ordered product according to specifications: color, size, brand, and quantity. (netsuite.com)
- According to a Statista study, U.S. businesses spent $1.63 trillion on logistics in 2019, moving goods from origin to end user through various supply chain network segments. (netsuite.com)
External Links
How To
How to Use lean manufacturing in the Production of Goods
Lean manufacturing refers to a method of managing that seeks to improve efficiency and decrease waste. It was developed in Japan between 1970 and 1980 by Taiichi Ohno. TPS founder Kanji Tyoda gave him the Toyota Production System, or TPS award. Michael L. Watkins published the first book on lean manufacturing in 1990.
Lean manufacturing is often described as a set if principles that help improve the quality and speed of products and services. It emphasizes reducing defects and eliminating waste throughout the value chain. Lean manufacturing is called just-in-time (JIT), zero defect, total productive maintenance (TPM), or 5S. Lean manufacturing eliminates non-value-added tasks like inspection, rework, waiting.
Lean manufacturing is a way for companies to achieve their goals faster, improve product quality, and lower costs. Lean manufacturing has been deemed one of the best ways to manage the entire value-chain, including customers, distributors as well retailers and employees. Lean manufacturing practices are widespread in many industries. Toyota's philosophy is the foundation of its success in automotives, electronics and appliances, healthcare, chemical engineers, aerospace, paper and food, among other industries.
Five principles are the basis of lean manufacturing:
-
Define Value: Identify the social value of your business and what sets you apart.
-
Reduce waste - Get rid of any activity that does not add value to the supply chain.
-
Create Flow. Ensure that your work is uninterrupted and flows seamlessly.
-
Standardize and Simplify – Make processes as consistent, repeatable, and as simple as possible.
-
Develop Relationships: Establish personal relationships both with internal and external stakeholders.
Lean manufacturing, although not new, has seen renewed interest in the economic sector since 2008. Many businesses have adopted lean manufacturing techniques to help them become more competitive. According to some economists, lean manufacturing could be a significant factor in the economic recovery.
Lean manufacturing is becoming a popular practice in automotive. It has many advantages. These include higher customer satisfaction, lower inventory levels, lower operating expenses, greater productivity, and improved overall safety.
The principles of lean manufacturing can be applied in almost any area of an organization. Because it makes sure that all value chains are efficient and effectively managed, Lean Manufacturing is particularly helpful for organizations.
There are three main types in lean manufacturing
-
Just-in Time Manufacturing, (JIT): This kind of lean manufacturing is also commonly known as "pull-systems." JIT is a method in which components are assembled right at the moment of use, rather than being manufactured ahead of time. This strategy aims to decrease lead times, increase availability of parts and reduce inventory.
-
Zero Defects Manufacturing, (ZDM): ZDM is focused on ensuring that no defective products leave the manufacturing facility. If a part is required to be repaired on the assembly line, it should not be scrapped. This applies to finished goods that may require minor repairs before shipment.
-
Continuous Improvement (CI: Continuous improvement aims to increase the efficiency of operations by constantly identifying and making improvements to reduce or eliminate waste. It involves continuous improvement of processes, people, and tools.