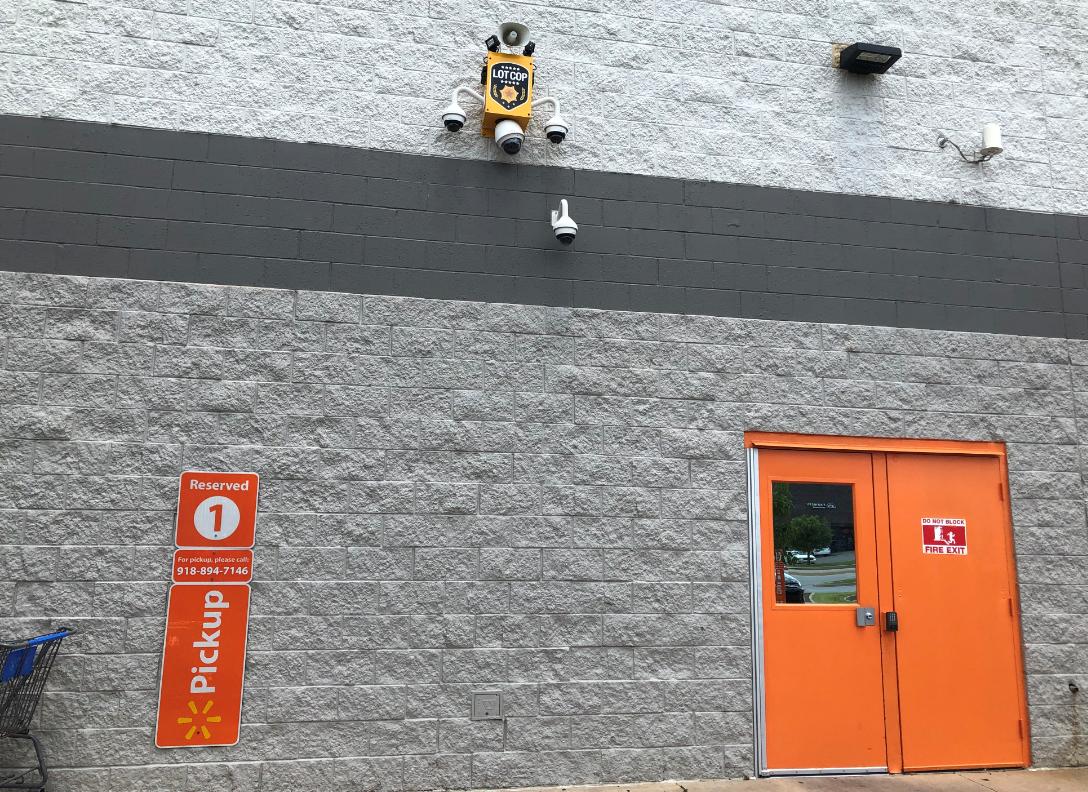
When he graduated from high school, Watts had no idea that he was going to end up as a supply chain major at Towson University. Jack Jensen - the managing director for the Moore School's Supply Chain Management program - was able sell him the program after telling him he could work on the capstone consulting project of the school.
Capstone projects, one of the most prestigious courses offered in business schools, allow students to dig into real-world supply chain issues on projects for businesses and nonprofits. According to Jensen, the Moore School has partnered with more than 150 companies in the last eight years to identify cost savings totaling more than $175 million through projects involving undergraduate students.
During their course work, students collaborate closely with faculty advisors to analyze supply chain problems using data science tools such as Lean Manufacturing and Six Sigma. Students also learn how to organize and transform data and build models.
After finishing the course, each student completes a capstone assignment in which they describe the problem, its importance for business and theory, research into the project's background, a method that is well defined, and their findings or results.
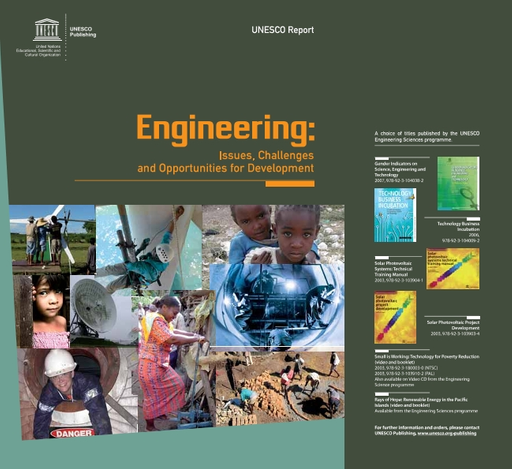
In addition to being a great opportunity to apply the knowledge and skills gained through your degree, the capstone project is a valuable learning experience and an excellent way to demonstrate your commitment to your education.
As a result, many schools offer their students the opportunity to complete a capstone project as part of their graduation requirements. These projects can be very challenging, and students often need to spend a significant amount of time and effort to complete them.
The project may be completed over the course a semester, or even longer. In general, it should take between 100-120 hours to complete.
Towson place apartment is a community of student housing located near campus. It offers studios, 1- and 2-bedroom apartments. Professionally managed by Capstone Management, residents enjoy a variety of amenities designed to meet their needs.
Millennium Hall consists of three separate buildings, each with 400 beds. The design was created in partnership between Towson and the University. The building is home to both undergraduates and graduates. The complex consists of studios as well one and two bedroom units. There is also a central mailbox and a laundry facility.
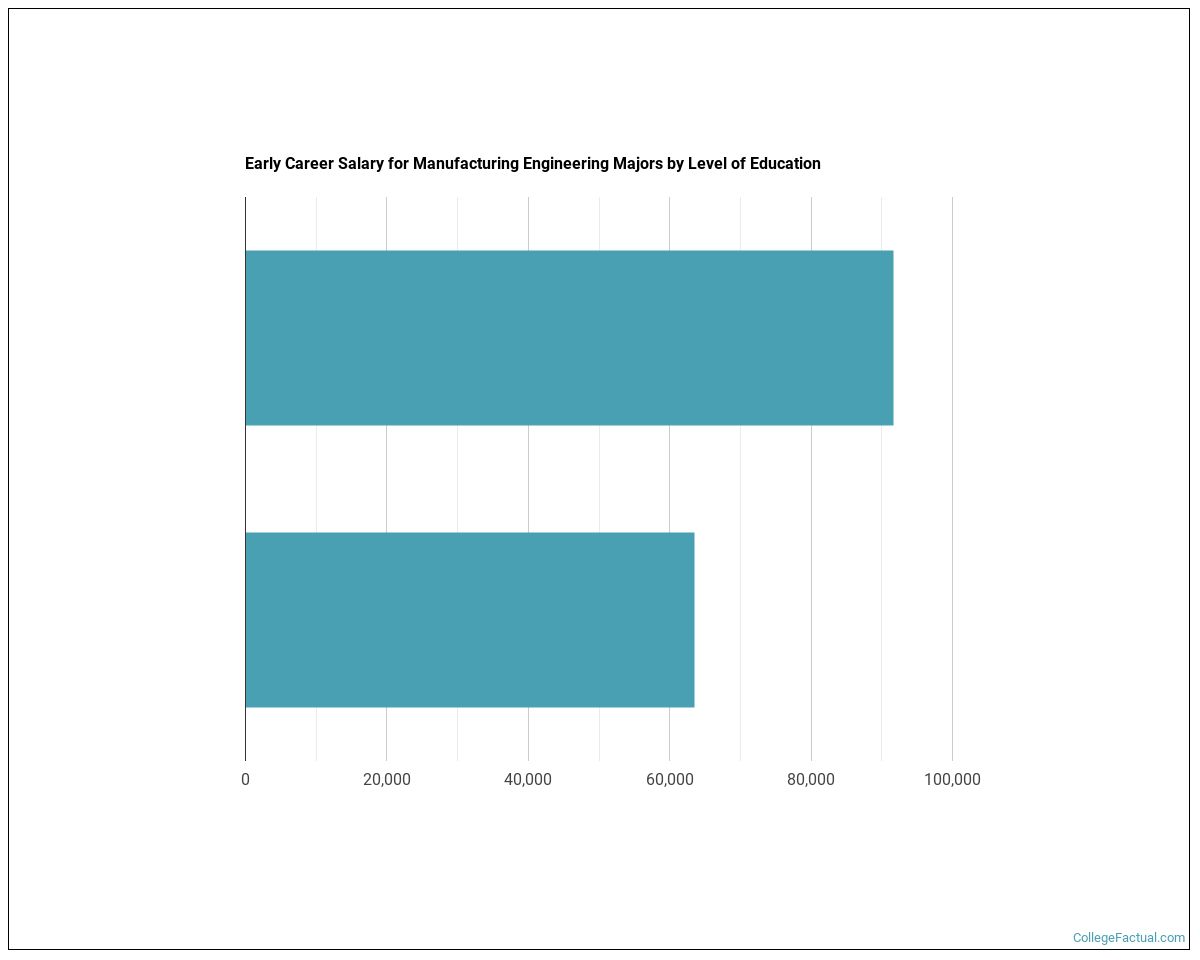
MEDCO leases Millennium Hall from TU. It owns the Paca, Tubman, and Tubman residences. Capstone Properties Inc. was hired by MEDCO for the management of day-to-day operation.
Several families have sued MEDCO, claiming breach of contract. They claim that their lease agreements are holding them hostage as TU moves to distance learning. They claim that MEDCO is refusing to release their leases and refunds, despite that they follow the guidelines of TU Housing and Residence Life's Campus Living Services and Center for Disease Control's (CDC).
The lawsuit, filed in March 2018, has not yet been resolved. Lucchi received responses from MEDCO’s Legal Council and he will continue to pursue this case.
FAQ
What makes a production planner different from a project manger?
The major difference between a Production Planner and a Project Manager is that a Project Manager is often the person responsible for organizing and planning the entire project. While a Production Planner is involved mainly in the planning stage,
What are the 4 types of manufacturing?
Manufacturing is the process by which raw materials are transformed into useful products through machines and processes. It includes many different activities like designing, building and testing, packaging, shipping and selling, as well as servicing.
What skills is required for a production planner?
A production planner must be organized, flexible, and able multitask to succeed. Communication skills are essential to ensure that you can communicate effectively with clients, colleagues, and customers.
Statistics
- [54][55] These are the top 50 countries by the total value of manufacturing output in US dollars for its noted year according to World Bank.[56] (en.wikipedia.org)
- Job #1 is delivering the ordered product according to specifications: color, size, brand, and quantity. (netsuite.com)
- In 2021, an estimated 12.1 million Americans work in the manufacturing sector.6 (investopedia.com)
- You can multiply the result by 100 to get the total percent of monthly overhead. (investopedia.com)
- According to a Statista study, U.S. businesses spent $1.63 trillion on logistics in 2019, moving goods from origin to end user through various supply chain network segments. (netsuite.com)
External Links
How To
How to Use the Just-In-Time Method in Production
Just-in time (JIT), is a process that reduces costs and increases efficiency in business operations. It's the process of obtaining the right amount and timing of resources when you need them. This means you only pay what you use. Frederick Taylor was the first to coin this term. He developed it while working as a foreman during the early 1900s. After observing how workers were paid overtime for late work, he realized that overtime was a common practice. He concluded that if workers were given enough time before they start work, productivity would increase.
The idea behind JIT is that you should plan ahead and have everything ready so you don't waste money. You should also look at the entire project from start to finish and make sure that you have sufficient resources available to deal with any problems that arise during the course of your project. You'll be prepared to handle any potential problems if you know in advance. This will ensure that you don't spend more money on things that aren't necessary.
There are several types of JIT techniques:
-
Demand-driven: This JIT is where you place regular orders for the parts/materials that are needed for your project. This will let you track the amount of material left over after you've used it. It will also allow you to predict how long it takes to produce more.
-
Inventory-based: This is a type where you stock the materials required for your projects in advance. This allows you to predict how much you can expect to sell.
-
Project-driven: This approach involves setting aside sufficient funds to cover your project's costs. When you know how much you need, you'll purchase the appropriate amount of materials.
-
Resource-based JIT: This type of JIT is most commonly used. Here you can allocate certain resources based purely on demand. For instance, if you have a lot of orders coming in, you'll assign more people to handle them. If you don’t have many orders you will assign less people to the work.
-
Cost-based : This is similar in concept to resource-based. But here, you aren't concerned about how many people your company has but how much each individual costs.
-
Price-based pricing: This is similar in concept to cost-based but instead you look at how much each worker costs, it looks at the overall company's price.
-
Material-based: This is quite similar to cost-based, but instead of looking at the total cost of the company, you're concerned with how much raw materials you spend on average.
-
Time-based JIT: This is another variant of resource-based JIT. Instead of focusing on how much each employee costs, you focus on how long it takes to complete the project.
-
Quality-based: This is yet another variation of resource-based JIT. Instead of focusing on the cost of each worker or how long it takes, think about how high quality your product is.
-
Value-based JIT: This is the latest form of JIT. In this instance, you are not concerned about the product's performance or meeting customer expectations. Instead, your goal is to add value to the market.
-
Stock-based. This method is inventory-based and focuses only on the actual production at any given point. It is used when production goals are met while inventory is kept to a minimum.
-
Just-in time (JIT), planning: This is a combination JIT/supply chain management. This refers to the scheduling of the delivery of components as soon after they are ordered. This is important as it reduces lead time and increases throughput.