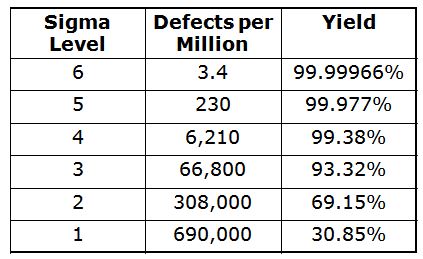
There are many manufacturing options depending on the type and purpose of the product. Manufacturing can be done either by machine or hand. Manufacturing businesses can sell their goods directly to consumers, wholesalers or retailers. You can also sell your goods online.
The materials and equipment required to manufacture a product are the first step in manufacturing. A manufacturing company can either buy raw materials from vendors or create its own. For instance, a jewelry maker may purchase ingredients for a new bracelet, then combine them with a few tools and assemble the product.
Other manufacturing processes involve the use of sophisticated tools and machinery. For example, cell phones are made out of raw materials which must be combined using sophisticated tools. The products are then shipped directly to the customer.
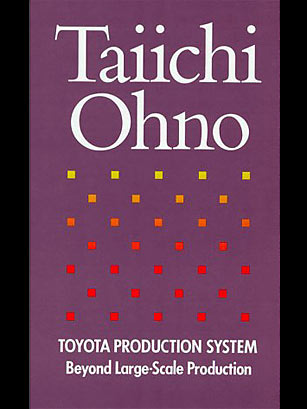
In order to produce a more advanced product, a manufacturing business may have to pay more for workers with advanced skill sets. Manufacturing is a complex and expensive business that can take several years to grow. In order to stay afloat, this type business will need to keep a reserve of cash. A manufacturing business may also need to hire employees as needed.
Manufacturing can be an exciting career option. A manufacturing business may find that the best products to sell are items that customers already have. They might also realize that they have to make more products with less waste. However, not everyone is suited for manufacturing.
Manufacturing can be challenging, especially if it isn't done well. Some manufacturing businesses may find it necessary to hire workers around the clock or have to abandon work. This could lead to higher costs and lower profits. Manufacturing also requires large investments for equipment, labor, as well as materials.
One of the most important things to know about manufacturing is that it has a very long history. It began thousands of years ago as an art form associated with traditional artifacts. Manufacturing is one of today's most important economic activities. Manufacturing helps industrializing nations expand their economies by providing goods for sale and employment opportunities.
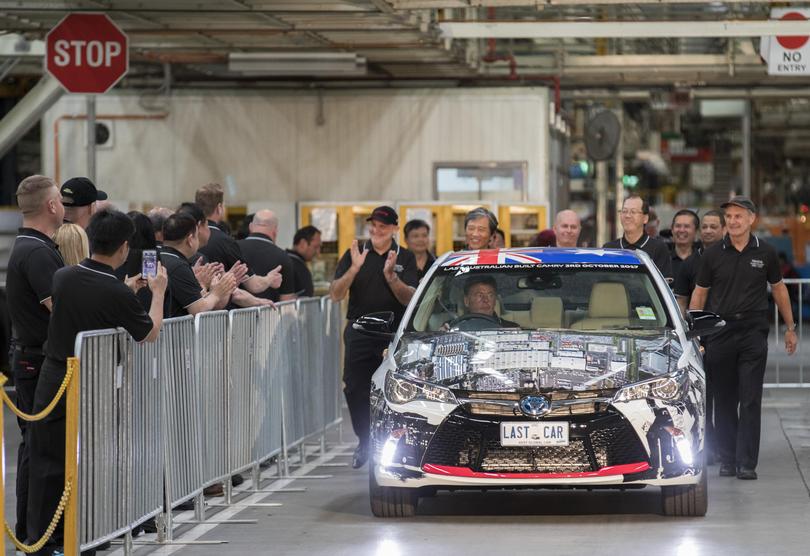
Manufacturing can be more complicated that it seems. There could be hundreds of steps. Quality control is essential during the manufacturing process. Because it ensures that the finished product meets safety standards and protects the brand identity, quality control is essential. If the manufacturer plans to sell its finished goods directly to consumers or wholesalers, this is especially important.
You can manufacture in almost any place. There are many different kinds of manufacturing, but they all fall under one of three categories: process, discrete, or make to order. Each type of manufacturing has its advantages and drawbacks. It's important to understand what each kind of manufacturing process does, and how it benefits your business.
FAQ
What makes a production planner different from a project manger?
The primary difference between a producer planner and a manager of a project is that the manager usually plans and organizes the whole project, while a production planner is only involved in the planning stage.
What does it take for a logistics enterprise to succeed?
To be a successful businessman in logistics, you will need many skills and knowledge. To communicate effectively with clients and suppliers, you must be able to communicate well. You will need to know how to interpret data and draw conclusions. You must be able and able to handle stress situations and work under pressure. You must be creative and innovative to develop new ideas to improve efficiency. You must be a strong leader to motivate others and direct them to achieve organizational goals.
You should also be organized and efficient to meet tight deadlines.
Why should you automate your warehouse?
Modern warehouses have become more dependent on automation. With the rise of ecommerce, there is a greater demand for faster delivery times as well as more efficient processes.
Warehouses should be able adapt quickly to new needs. Technology investment is necessary to enable warehouses to respond quickly to changing demands. Automation of warehouses offers many benefits. Here are some of the reasons automation is worth your investment:
-
Increases throughput/productivity
-
Reduces errors
-
Increases accuracy
-
Safety Boosts
-
Eliminates bottlenecks
-
This allows companies to scale easily
-
It makes workers more efficient
-
Gives you visibility into all that is happening in your warehouse
-
Enhances customer experience
-
Improves employee satisfaction
-
Reduces downtime and improves uptime
-
Ensures quality products are delivered on time
-
Eliminates human error
-
This helps to ensure compliance with regulations
What are the 7 Rs of logistics?
The 7R's of Logistics is an acronym for the seven basic principles of logistics management. It was developed by the International Association of Business Logisticians (IABL) and published in 2004 as part of its "Seven Principles of Logistics Management" series.
The acronym is made up of the following letters:
-
Responsible – ensure that all actions are legal and don't cause harm to anyone else.
-
Reliable – have faith in your ability and capability to keep promises.
-
Be responsible - Use resources efficiently and avoid wasting them.
-
Realistic – consider all aspects of operations, from cost-effectiveness to environmental impact.
-
Respectful - show respect and treat others fairly and fairly
-
Reliable - Find ways to save money and increase your productivity.
-
Recognizable: Provide customers with value-added service
Is it necessary to be familiar with Manufacturing Processes before we learn about Logistics.
No. No. But, being familiar with manufacturing processes will give you a better understanding about how logistics works.
Statistics
- In the United States, for example, manufacturing makes up 15% of the economic output. (twi-global.com)
- According to the United Nations Industrial Development Organization (UNIDO), China is the top manufacturer worldwide by 2019 output, producing 28.7% of the total global manufacturing output, followed by the United States, Japan, Germany, and India.[52][53] (en.wikipedia.org)
- You can multiply the result by 100 to get the total percent of monthly overhead. (investopedia.com)
- (2:04) MTO is a production technique wherein products are customized according to customer specifications, and production only starts after an order is received. (oracle.com)
- In 2021, an estimated 12.1 million Americans work in the manufacturing sector.6 (investopedia.com)
External Links
How To
Six Sigma: How to Use it in Manufacturing
Six Sigma is defined by "the application SPC (statistical process control) techniques to achieve continuous improvements." Motorola's Quality Improvement Department in Tokyo, Japan developed Six Sigma in 1986. Six Sigma's main goal is to improve process quality by standardizing processes and eliminating defects. Since there are no perfect products, or services, this approach has been adopted by many companies over the years. Six Sigma seeks to reduce variation between the mean production value. It is possible to measure the performance of your product against an average and find the percentage of time that it differs from the norm. If the deviation is excessive, it's likely that something needs to be fixed.
Understanding the dynamics of variability within your business is the first step in Six Sigma. Once you have a good understanding of the basics, you can identify potential sources of variation. You'll also want to determine whether these variations are random or systematic. Random variations are caused when people make mistakes. While systematic variations are caused outside of the process, they can occur. If you make widgets and some of them end up on the assembly line, then those are considered random variations. It would be considered a systematic problem if every widget that you build falls apart at the same location each time.
Once you have identified the problem, you can design solutions. It might mean changing the way you do business or redesigning it entirely. After implementing the new changes, you should test them again to see if they worked. If they don't work, you will need to go back to the drawing boards and create a new plan.