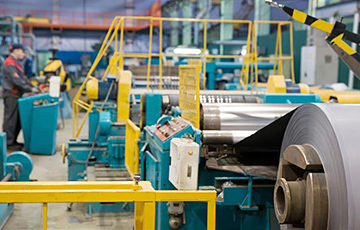
Biomedical engineering is a promising career that can improve the health of the people who choose it. These engineers are skilled in many fields including pharmaceutical manufacturing, laboratory science, and health care facilities. These engineers invent new techniques and products that aid patients.
A bachelor's degree is required to become a biomedical engineer. A solid foundation in science and math is required for biomedical engineers. They should also be able to problem solve and have strong analytical skills. They can also take internships to gain experience. Some employers may also require a master's degree.
A combination of an aging population along with advances in medical technology will lead to a greater demand for biomedical technicians in the future. Biomedical engineers are professionals who work in medical fields to create and test new technologies. Biomedical engineers can also design, build, and repair medical devices. They are available to work in healthcare facilities, research facilities and companies that sell medical equipment.
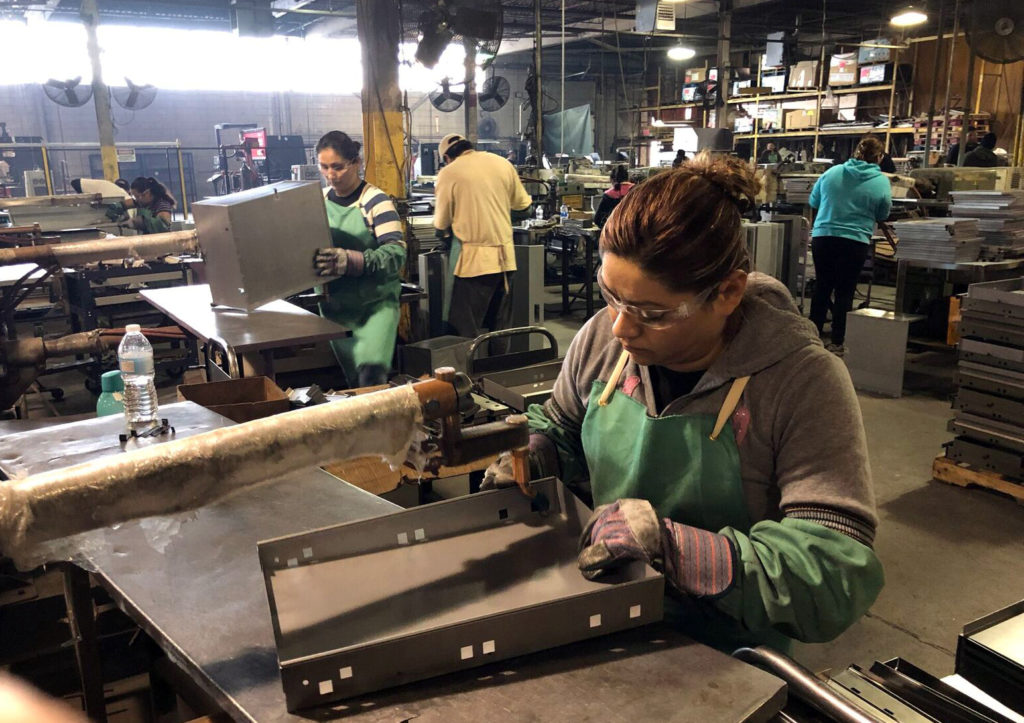
Biomedical engineers employ advanced science and math to design equipment and software for biological science problems. These engineers also use advanced math, statistics, and advanced math to create models of complex medical devices. Biomedical engineers are also responsible, in addition to developing new devices and processes for patients, for testing and approving new medication and drug therapies. Biomedical engineers are also responsible for ensuring that medical equipment works at its maximum performance.
Biomedical engineers are in high demand, as with all engineering fields. The field is expected expand faster than other engineering disciplines. The Bureau of Labor Statistics (BLS) predicts that jobs for biomedical engineers will grow by six percent between 2020 and 2030. This is significantly faster than the average rate of growth for all occupations. In 2010, biomedical engineers had around 15,700 jobs. BLS forecasts that there would be 1,400 job openings per year through 2029. These openings will be available in the healthcare and medical equipment and supply manufacturing industries as well as research services.
Internships are an opportunity to explore a career in biomedical engineering. These internships are an opportunity to see how biomedical engineers work and to gain real-life experience. It is a smart idea to study computer programming, drafting and mechanical drawing as a student. Those who have a passion for science can also choose to study physiology, human anatomy, and molecular biology.
People who wish to become a biomedical technician should prepare for this career from high school. While a bachelor’s degree in biomedical engineer is essential, many employers prefer a Master’s degree. A master's degree can expand opportunities and lead to supervisory roles in the field.
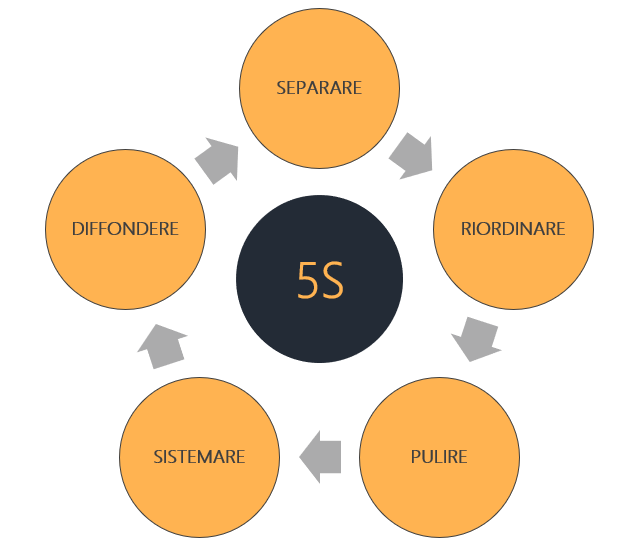
Biology, chemistry, mathematics, and physics are required for biomedical engineers. Biomedical engineering students take courses in human anatomy, molecular biology and physiology during their undergraduate years. They also do capstone projects, which combine engineering skills with problems in biological science.
FAQ
How can manufacturing avoid production bottlenecks
You can avoid bottlenecks in production by making sure that everything runs smoothly throughout the production cycle, from the moment you receive an order to the moment the product is shipped.
This includes both quality control and capacity planning.
Continuous improvement techniques like Six Sigma are the best way to achieve this.
Six Sigma is a management method that helps to improve quality and reduce waste.
It emphasizes consistency and eliminating variance in your work.
What are the responsibilities of a logistic manager?
Logistics managers make sure all goods are delivered on schedule and without damage. This is accomplished by using the experience and knowledge gained from working with company products. He/she must also ensure sufficient stock to meet the demand.
What can I do to learn more about manufacturing?
Practical experience is the best way of learning about manufacturing. You can read books, or watch instructional videos if you don't have the opportunity to do so.
What are the four types of manufacturing?
Manufacturing is the process that transforms raw materials into useful products. It involves many different activities such as designing, building, testing, packaging, shipping, selling, servicing, etc.
What are the 7 Rs of logistics.
The acronym "7R's" of Logistics stands for seven principles that underpin logistics management. It was published in 2004 by the International Association of Business Logisticians as part of their "Seven Principles of Logistics Management" series.
The following letters form the acronym:
-
Responsible - ensure that actions are in compliance with legal requirements and do not cause harm to others.
-
Reliable: Have faith in your ability or the ability to honor any promises made.
-
Use resources effectively and sparingly.
-
Realistic - Take into consideration all aspects of operations including cost-effectiveness, environmental impact, and other factors.
-
Respectful - show respect and treat others fairly and fairly
-
Be resourceful: Look for opportunities to save money or increase productivity.
-
Recognizable - Provide value-added services to customers
What is the difference between manufacturing and logistics
Manufacturing refers to the process of making goods using raw materials and machines. Logistics encompasses the management of all aspects associated with supply chain activities such as procurement, production planning, distribution and inventory control. It also includes customer service. Manufacturing and logistics are often considered together as a broader term that encompasses both the process of creating products and delivering them to customers.
What is the responsibility of a production planner?
Production planners ensure that all project aspects are completed on time, within budget and within the scope. They ensure that the product or service is of high quality and meets client requirements.
Statistics
- You can multiply the result by 100 to get the total percent of monthly overhead. (investopedia.com)
- Many factories witnessed a 30% increase in output due to the shift to electric motors. (en.wikipedia.org)
- Job #1 is delivering the ordered product according to specifications: color, size, brand, and quantity. (netsuite.com)
- In 2021, an estimated 12.1 million Americans work in the manufacturing sector.6 (investopedia.com)
- [54][55] These are the top 50 countries by the total value of manufacturing output in US dollars for its noted year according to World Bank.[56] (en.wikipedia.org)
External Links
How To
How to use lean manufacturing in the production of goods
Lean manufacturing refers to a method of managing that seeks to improve efficiency and decrease waste. It was created in Japan by Taiichi Ohno during the 1970s and 80s. He received the Toyota Production System award (TPS), from Kanji Toyoda, founder of TPS. Michael L. Watkins published the original book on lean manufacturing, "The Machine That Changed the World," in 1990.
Lean manufacturing is often described as a set if principles that help improve the quality and speed of products and services. It emphasizes the elimination and minimization of waste in the value stream. Lean manufacturing is called just-in-time (JIT), zero defect, total productive maintenance (TPM), or 5S. Lean manufacturing is about eliminating activities that do not add value, such as inspection, rework, and waiting.
Lean manufacturing not only improves product quality but also reduces costs. Companies can also achieve their goals faster by reducing employee turnover. Lean Manufacturing is one of the most efficient ways to manage the entire value chains, including suppliers and customers as well distributors and retailers. Lean manufacturing practices are widespread in many industries. Toyota's philosophy is a great example of this. It has helped to create success in automobiles as well electronics, appliances and healthcare.
Five fundamental principles underlie lean manufacturing.
-
Define Value - Identify the value your business adds to society and what makes you different from competitors.
-
Reduce waste - Get rid of any activity that does not add value to the supply chain.
-
Create Flow – Ensure that work flows smoothly throughout the process.
-
Standardize and simplify - Make your processes as consistent as possible.
-
Build Relationships - Establish personal relationships with both internal and external stakeholders.
Lean manufacturing isn’t new, but it has seen a renewed interest since 2008 due to the global financial crisis. Many businesses have adopted lean manufacturing techniques to help them become more competitive. Many economists believe lean manufacturing will play a major role in economic recovery.
With many benefits, lean manufacturing is becoming more common in the automotive industry. These benefits include increased customer satisfaction, reduced inventory levels and lower operating costs.
Any aspect of an enterprise can benefit from Lean manufacturing. However, it is particularly useful when applied to the production side of an organization because it ensures that all steps in the value chain are efficient and effective.
There are three types principally of lean manufacturing:
-
Just-in Time Manufacturing (JIT), also known as "pull system": This form of lean manufacturing is often referred to simply as "pull". JIT stands for a system where components are assembled on the spot rather than being made in advance. This approach aims to reduce lead times, increase the availability of parts, and reduce inventory.
-
Zero Defects Manufacturing (ZDM): ZDM focuses on ensuring that no defective units leave the manufacturing facility. Repairing a part that is damaged during assembly should be done, not scrapping. This applies to finished products, which may need minor repairs before they are shipped.
-
Continuous Improvement (CI): CI aims to improve the efficiency of operations by continuously identifying problems and making changes in order to eliminate or minimize waste. Continuous Improvement (CI) involves continuous improvement in processes, people, tools, and infrastructure.