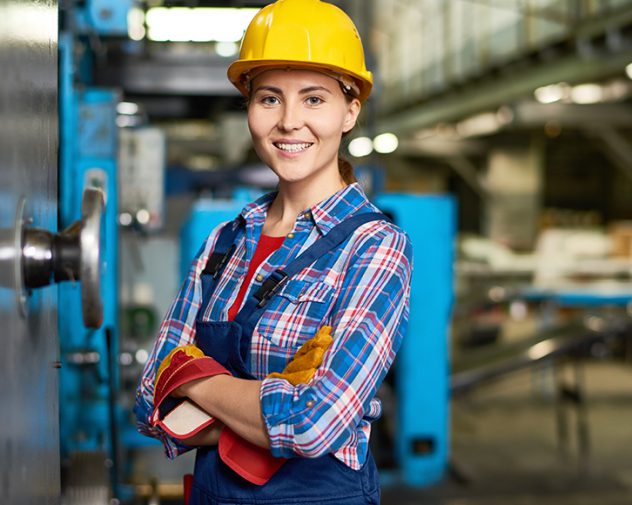
You may be interested in Estimator jobs. But, are you wondering how to get the job? This article will cover the typical role, the work environment, as well as the salary range. This article will also discuss the required skills and experience for this job. Keep reading to discover more! Here are some essential qualities that a candidate for the job of Estimator should possess. Having all of these traits will make your job as an Estimator all the more attractive.
Ideal candidate for estimator role
A great candidate for the Estimator position should be well-versed and have excellent analytical skills. The ideal candidate should be highly skilled in communication and detail-oriented. A minimum of a Bachelor's degree is required, along with 3 years experience in a related field. Candidate should be proficient in MS Office suite. Candidates should be able and able to think critically as well as work well under pressure.
A bachelor's degree in Construction or another related field is required to be an ideal candidate for the Estimator position. The candidate must be motivated and enthusiastic. The candidate must communicate with clients, be confident, and enjoy the job. They should be able to give positive impressions and present their estimates. It's important that the candidate can deliver on their promises and be accountable for meeting deadlines.
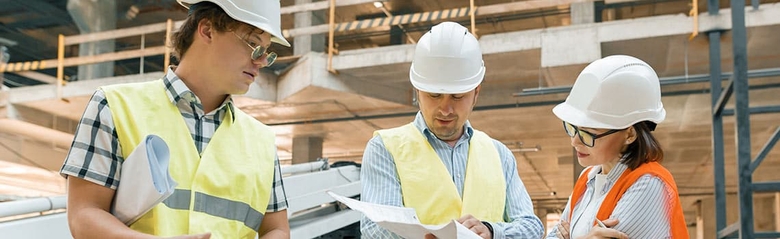
Job description
An estimator's primary role is to prepare detailed reports that can help companies grow and improve their profitability. Estimators use computer software to communicate and estimate cost and time. Estimators also prepare and present reports that include budget risks and recommendations to the client. Estimators make educated guesses regarding the project's costs. However, these workers can be very valuable to their employers. They can also contribute greatly to a company’s bottom line.
The job description for estimators should reflect the area of interest the applicant is interested in. For example, a construction estimator's job description might require a background in quantity surveying, but this knowledge is not required for all construction projects. Estimators need to have knowledge in other areas such as energy, environmental, or technology. Whether a construction company is looking for a full-time employee or a contractor, there's a suitable job description for the position.
Salary
An estimator is someone who works in construction to determine the project's costs. Estimators are responsible for many different responsibilities and may be experts in one or more areas. In order to increase the salary of an estimator, you must first find out the experience that you need. Look for companies that offer an apprenticeship program to new employees. If you have an associate's degree in estimating, you may want to consider a position there. Then, you can advance in your career to a full-time salary.
An estimator must be able to deliver valuable information and have a good understanding of building materials. This knowledge allows them to produce accurate and useful forecasts. These professionals are often required to work in high-pressure settings. Their job requires them to work together and deliver accurate information. Salary information for estimators is based upon Indeed Salaries data. These figures can be affected by the location, employer, and education of candidates.
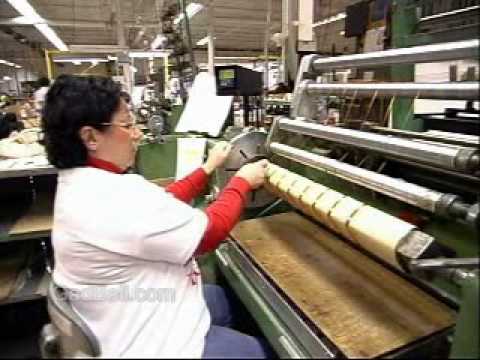
Work environment
Your primary responsibility as an estimator is to prepare competitive bids on construction projects. Your primary responsibility will be to prepare competitive bids for construction projects. You will determine the priorities of bidding, participate in pre-bid meetings and identify labor, equipment and materials requirements for each project. As part of the project management team, you will prepare change orders for different projects.
While a bachelor's degree is required for most estimator jobs, some employers will hire those with only a high school diploma. Employers will consider candidates who have an associate's or five-year college diploma, but some will not hire people with just an associate's. The most sought-after degrees are mathematics, business and management. As a construction estimator, strong numeracy skills are necessary.
FAQ
What does it mean to warehouse?
A warehouse is a place where goods are stored until they are sold. It can be indoors or out. It may also be an indoor space or an outdoor area.
What are manufacturing and logistics?
Manufacturing is the act of producing goods from raw materials using machines and processes. Logistics encompasses the management of all aspects associated with supply chain activities such as procurement, production planning, distribution and inventory control. It also includes customer service. As a broad term, manufacturing and logistics often refer to both the creation and delivery of products.
What does manufacturing mean?
Manufacturing Industries are businesses that produce products for sale. These products are sold to consumers. These companies use various processes such as production, distribution, retailing, management, etc., to fulfill this purpose. They produce goods from raw materials by using machines and other machinery. This covers all types of manufactured goods including clothing, food, building supplies and furniture, as well as electronics, tools, machinery, vehicles and pharmaceuticals.
Statistics
- In 2021, an estimated 12.1 million Americans work in the manufacturing sector.6 (investopedia.com)
- Job #1 is delivering the ordered product according to specifications: color, size, brand, and quantity. (netsuite.com)
- [54][55] These are the top 50 countries by the total value of manufacturing output in US dollars for its noted year according to World Bank.[56] (en.wikipedia.org)
- It's estimated that 10.8% of the U.S. GDP in 2020 was contributed to manufacturing. (investopedia.com)
- You can multiply the result by 100 to get the total percent of monthly overhead. (investopedia.com)
External Links
How To
Six Sigma and Manufacturing
Six Sigma refers to "the application and control of statistical processes (SPC) techniques in order to achieve continuous improvement." Motorola's Quality Improvement Department developed it at their Tokyo plant in Japan in 1986. The basic idea behind Six Sigma is to improve quality by improving processes through standardization and eliminating defects. Since there are no perfect products, or services, this approach has been adopted by many companies over the years. Six Sigma's main objective is to reduce variations from the production average. This means that you can take a sample from your product and then compare its performance to the average to find out how often the process differs from the norm. If there is a significant deviation from the norm, you will know that something needs to change.
Understanding how your business' variability is a key step towards Six Sigma implementation is the first. Once you have a good understanding of the basics, you can identify potential sources of variation. It is important to identify whether the variations are random or systemic. Random variations are caused by human errors. Systematic variations can be caused by outside factors. If you make widgets and some of them end up on the assembly line, then those are considered random variations. You might notice that your widgets always fall apart at the same place every time you put them together.
Once you have identified the problem, you can design solutions. The solution could involve changing how you do things, or redesigning your entire process. Once you have implemented the changes, it is important to test them again to ensure they work. If they don't work, you will need to go back to the drawing boards and create a new plan.