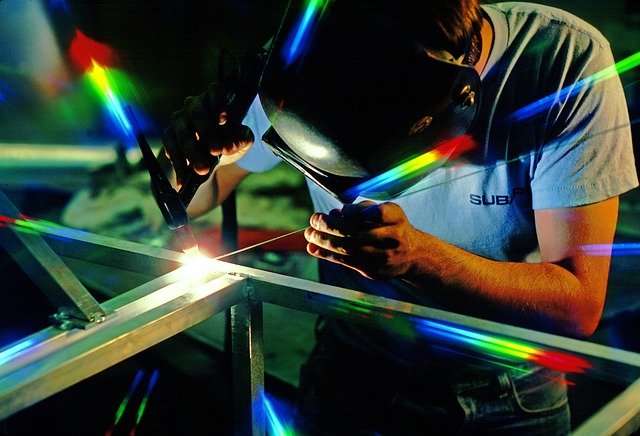
A good salary for a material engineer depends on your work location and specialization. Some of the highest paying companies include Apple, ConocoPhillips, Meta and Western Digital. FedEx and Motorola Solutions are two other excellent places for a material engineering to work.
Materials engineers need knowledge of the relationship between materials, and their processing methods. They should also be able identify the causes of failures. Aside from being able to explain engineering concepts and ideas to non-engineers, they also need to be able to do so. They are responsible for developing and implementing cost-efficient operations strategies. They may also need to communicate with suppliers and other professionals. Sometimes, they may be required to travel to foreign countries in order to collect samples for testing. In some cases, they may work more than 40 hours a week.
Materials engineers might also be eligible for advanced degrees. They may be eligible for a PhD. They may also be qualified to teach and work in research. Senior material engineers may have more managerial responsibilities. They might also have the opportunity for innovative research.
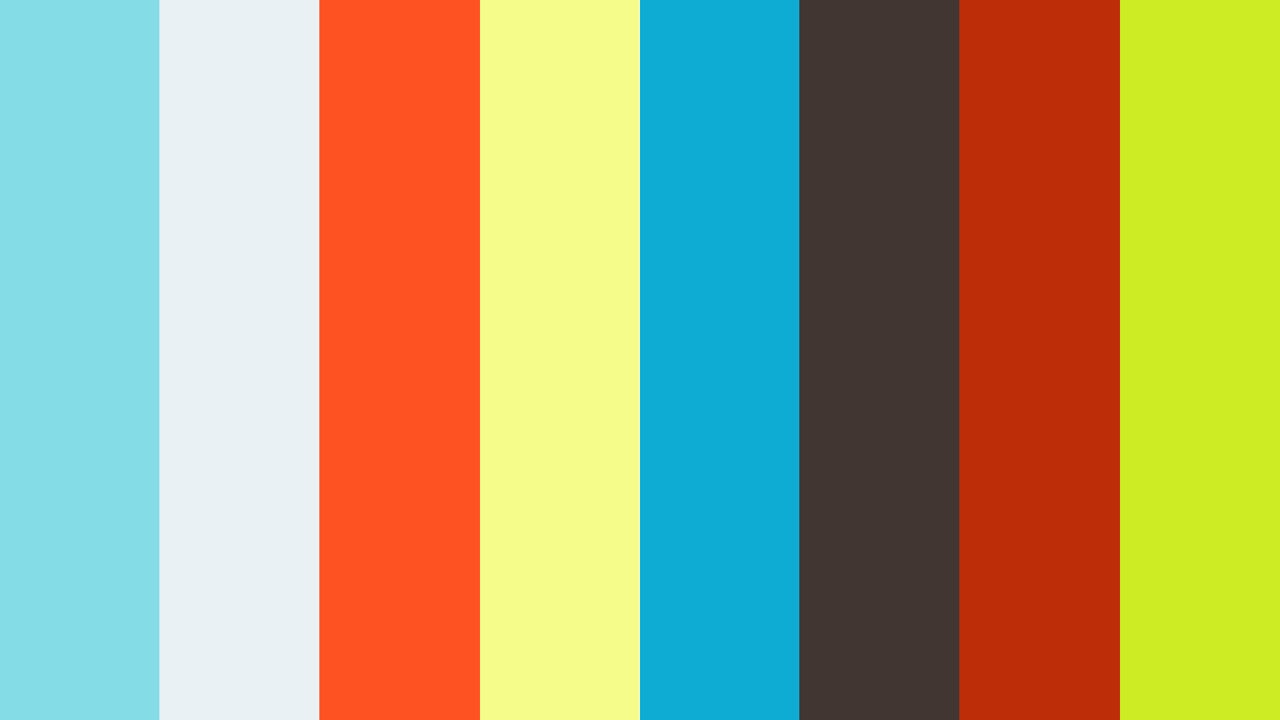
Materials engineers may work in manufacturing plants or offices, and may also travel to worksites to collect samples for testing. The field is very competitive and it is important that you stay up to date with industry innovations and trends. Aside from that, they might need to build relationships with clients. They can provide green practices to product engineers and help them improve their products. A strong reputation may result.
Materials engineers could also work in laboratories. Advanced math topics may be used for troubleshooting and design. They might need to communicate engineering concepts clearly. They may also be required travel to other countries in order to obtain samples or observe the manufacturing process.
Companies such as FedEx or Apple hire materials engineers. They may also be employed by companies that manufacture metals and other materials, such as Raytheon Technologies. This field is extremely competitive and it may prove difficult to land a job at these companies. It is also possible to become a material engineer through engineering consulting firms. Aside from being able to keep up with their industry, they might also be able to start their own business.
They may also have to work long hours as materials engineers. They may be required to travel to sites in order to test materials or observe the manufacturing process. If they are working in a factory, they may be expected to work 40-hour days. As a result, they may need to have a strong work ethic.
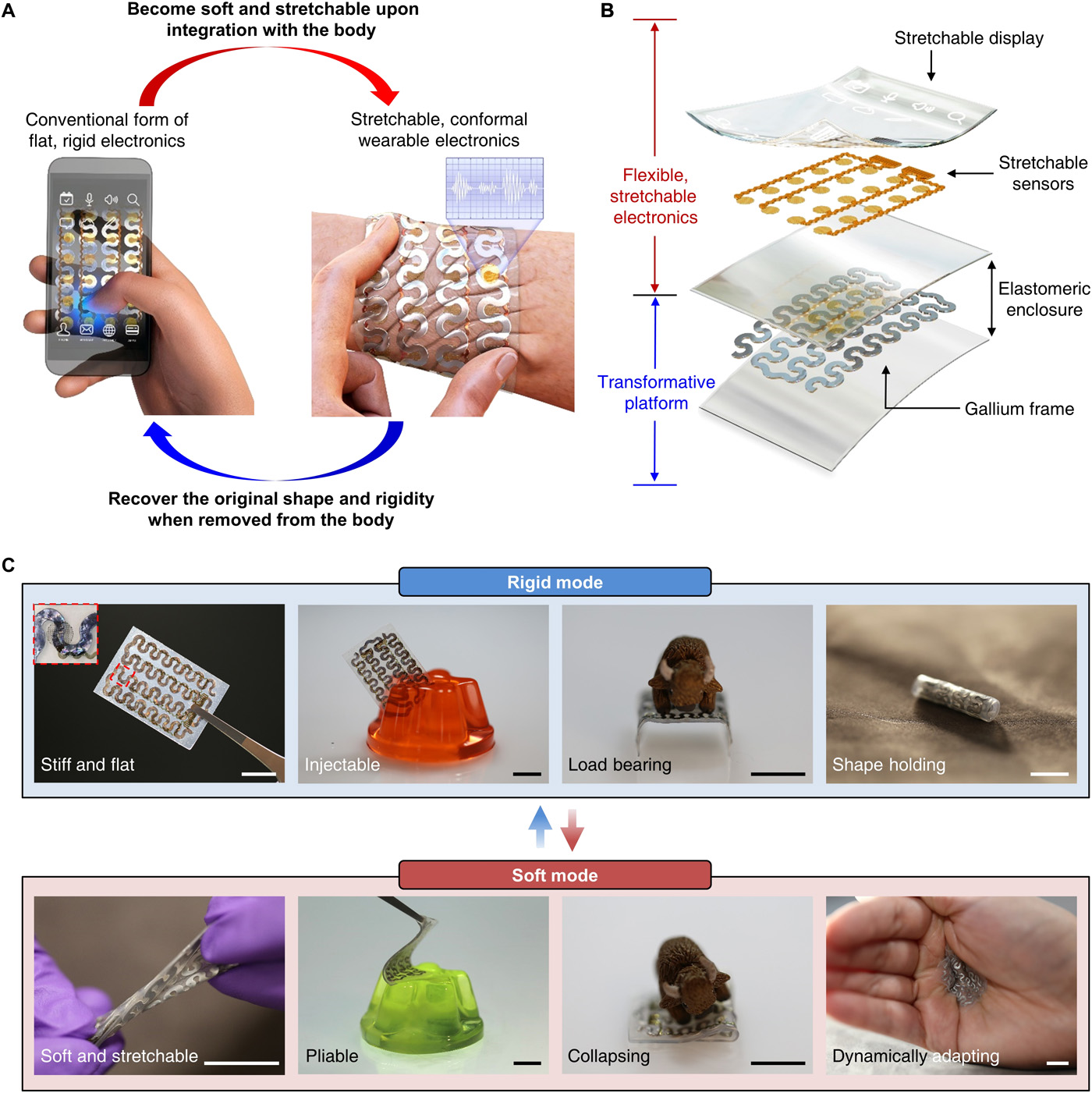
As a result, material engineers may need to work with a team. They might need to communicate with clients and other professionals as well as with suppliers. In addition, they may be responsible for ensuring that budgets are met and that deadlines are met.
FAQ
What is the job of a manufacturer manager?
A manufacturing manager must ensure that all manufacturing processes are efficient and effective. They must also be alert to any potential problems and take appropriate action.
They should also be able and comfortable communicating with other departments like sales and marketing.
They should be up to date on the latest trends and be able apply this knowledge to increase productivity and efficiency.
Do we need to know about Manufacturing Processes before learning about Logistics?
No. No. Knowing about manufacturing processes will help you understand how logistics works.
Why is logistics so important in manufacturing?
Logistics are an integral part any business. They help you achieve great results by helping you manage all aspects of product flow, from raw materials to finished goods.
Logistics play a key role in reducing expenses and increasing efficiency.
Statistics
- (2:04) MTO is a production technique wherein products are customized according to customer specifications, and production only starts after an order is received. (oracle.com)
- According to the United Nations Industrial Development Organization (UNIDO), China is the top manufacturer worldwide by 2019 output, producing 28.7% of the total global manufacturing output, followed by the United States, Japan, Germany, and India.[52][53] (en.wikipedia.org)
- [54][55] These are the top 50 countries by the total value of manufacturing output in US dollars for its noted year according to World Bank.[56] (en.wikipedia.org)
- In 2021, an estimated 12.1 million Americans work in the manufacturing sector.6 (investopedia.com)
- Many factories witnessed a 30% increase in output due to the shift to electric motors. (en.wikipedia.org)
External Links
How To
How to use Lean Manufacturing in the production of goods
Lean manufacturing is a management system that aims at increasing efficiency and reducing waste. It was developed in Japan during the 1970s and 1980s by Taiichi Ohno, who received the Toyota Production System (TPS) award from TPS founder Kanji Toyoda. The first book published on lean manufacturing was titled "The Machine That Changed the World" written by Michael L. Watkins and published in 1990.
Lean manufacturing refers to a set of principles that improve the quality, speed and costs of products and services. It is about eliminating defects and waste from all stages of the value stream. Just-in-time (JIT), zero defect (TPM), and 5S are all examples of lean manufacturing. Lean manufacturing focuses on eliminating non-value-added activities such as rework, inspection, and waiting.
Lean manufacturing not only improves product quality but also reduces costs. Companies can also achieve their goals faster by reducing employee turnover. Lean manufacturing can be used to manage all aspects of the value chain. Customers, suppliers, distributors, retailers and employees are all included. Lean manufacturing practices are widespread in many industries. For example, Toyota's philosophy underpins its success in automobiles, electronics, appliances, healthcare, chemical engineering, aerospace, paper, food, etc.
Five principles are the basis of lean manufacturing:
-
Define Value - Determine the value that your business brings to society. Also, identify what sets you apart from your competitors.
-
Reduce waste - Get rid of any activity that does not add value to the supply chain.
-
Create Flow - Ensure work moves smoothly through the process without interruption.
-
Standardize and Simplify – Make processes as consistent, repeatable, and as simple as possible.
-
Build Relationships - Establish personal relationships with both internal and external stakeholders.
Although lean manufacturing isn't a new concept in business, it has gained popularity due to renewed interest in the economy after the 2008 global financial crisis. Many businesses are now using lean manufacturing to improve their competitiveness. In fact, some economists believe that lean manufacturing will be an important factor in economic recovery.
With many benefits, lean manufacturing is becoming more common in the automotive industry. These benefits include increased customer satisfaction, reduced inventory levels and lower operating costs.
Lean manufacturing can be applied to almost every aspect of an organization. Lean manufacturing is most useful in the production sector of an organisation because it ensures that each step in the value-chain is efficient and productive.
There are three types of lean manufacturing.
-
Just-in Time Manufacturing (JIT), also known as "pull system": This form of lean manufacturing is often referred to simply as "pull". JIT means that components are assembled at the time of use and not manufactured in advance. This approach is designed to reduce lead times and increase the availability of components. It also reduces inventory.
-
Zero Defects Manufacturing - ZDM: ZDM focuses its efforts on making sure that no defective units leave a manufacturing facility. You should repair any part that needs to be repaired during an assembly line. This is true even for finished products that only require minor repairs prior to shipping.
-
Continuous Improvement (CI),: Continuous improvement aims improve the efficiency and effectiveness of operations by continuously identifying issues and making changes to reduce waste. Continuous Improvement involves continuous improvement of processes.