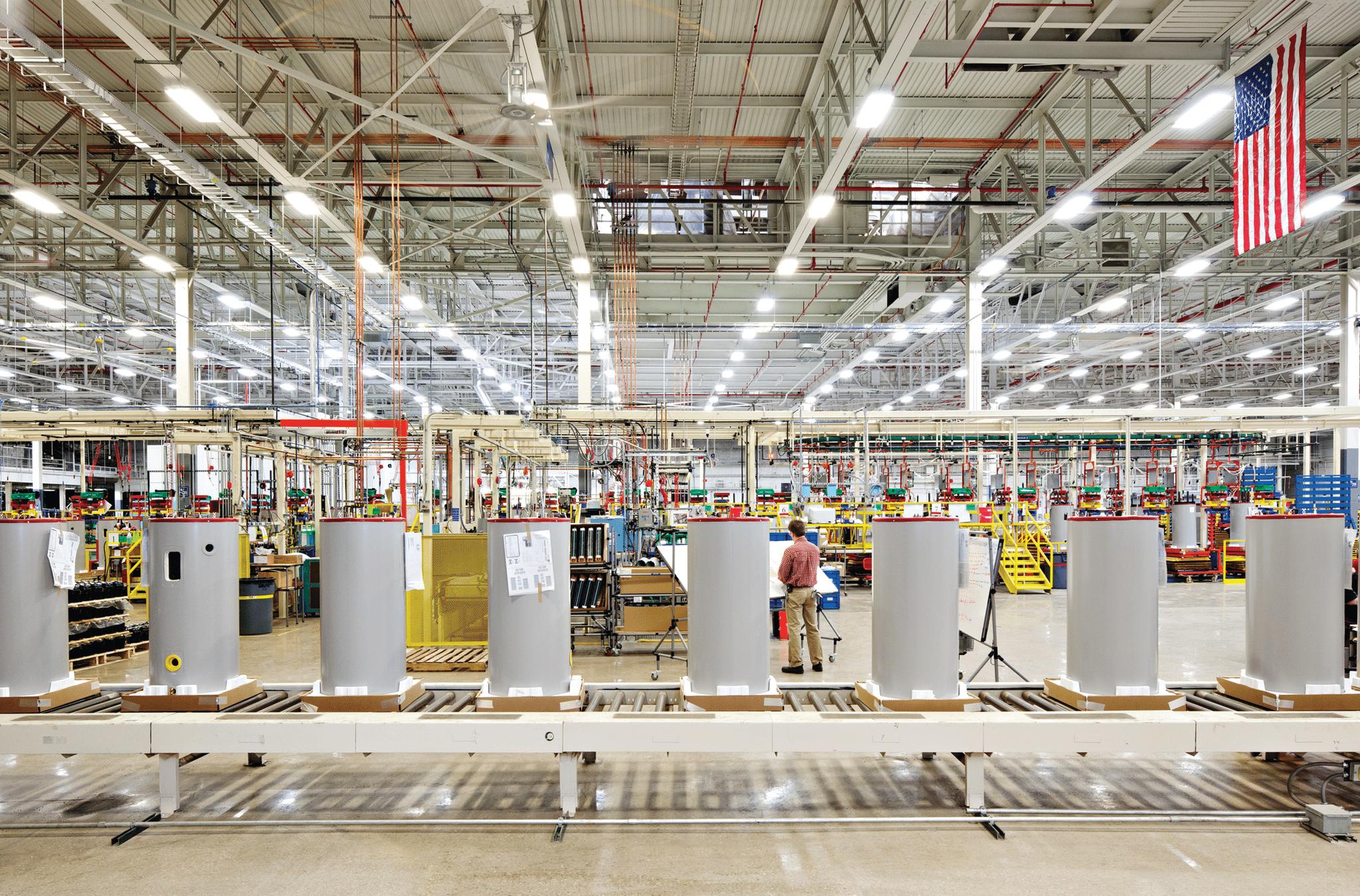
Global supply-chain management is the process of distributing goods and services within a global company's network. The principle behind this concept is to maximize profit, while minimizing waste. While this distribution method is a great option, it does have its downsides. Let's discuss some of these issues. Continue reading to discover more about global supply chain management's benefits. We'll also be discussing some of the difficulties associated with global Supply Chain Management.
Resilience
As an effective global supply chain manager, it is crucial to build a strategy that promotes resilience. Redesigning the supply chain, eliminating redundant workers, and implementing multiple sources can all help to increase the supply chain's resilience. Supply chains may appear rigid at first, but they can evolve with creativity, innovation, and constant vigilance. One inventory management software provider, Cin7, has helped its users to build resilience in their supply chains by publishing various educational materials and advice.
Information sharing
Although the role information sharing plays in global supply chains management may seem vague, it is crucial to the survival companies. This study examines how information sharing can benefit various parties in a supply chain. Information sharing offers many benefits, which may vary depending on the type of information. In general, the value of information varies depending on the parties involved. These are just a few examples of the types of information that can be beneficial to a supply chain.
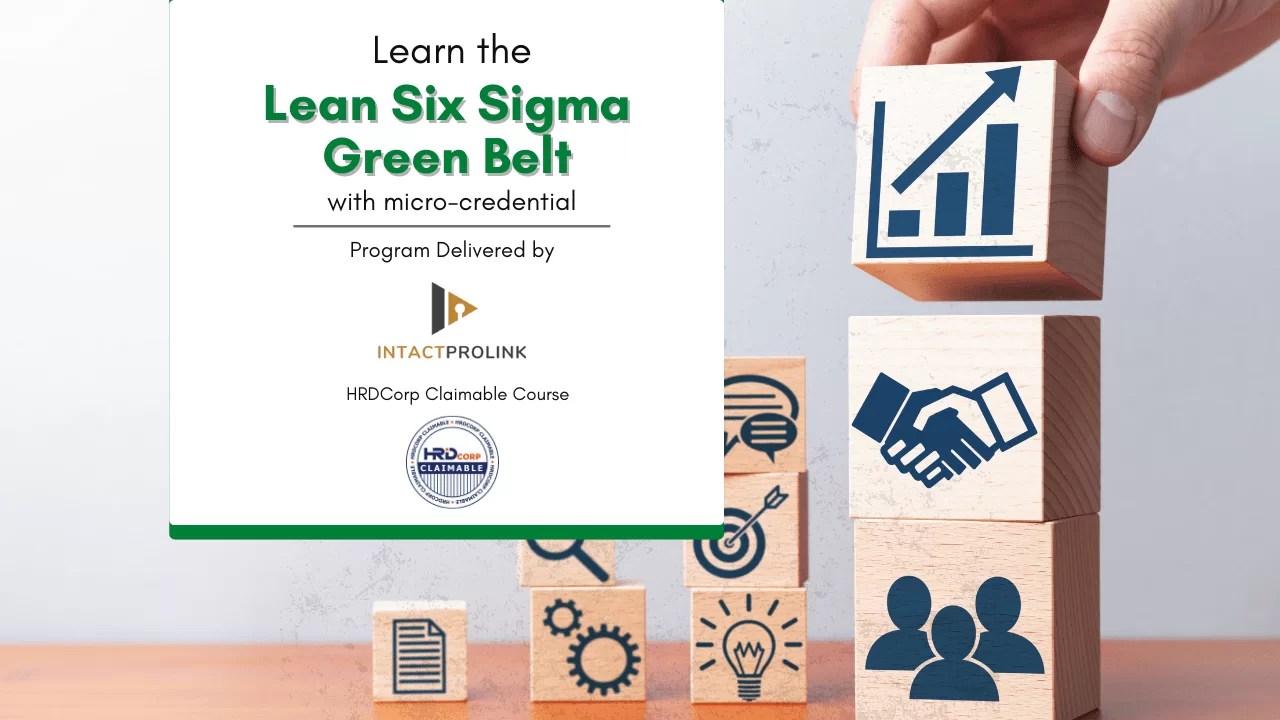
Management of quality
Quality issues are an important part of any supply chains. It is crucial for companies to ensure product quality. However it is equally important that secondary issues are addressed and supply chain risk managed. This article will address the role of quality in global supply chain management. This article will also discuss how business systems may fail to meet the challenge. Let's examine how companies can overcome these obstacles and implement quality management strategies that are more efficient.
Logistics links
As consumers' demands and preferences continue to evolve, so do the needs of the business. The global supply chain is a complex system of companies, individuals, and suppliers that work together to deliver goods at the correct time and to the right location. Logistics plays a key role in global Supply Chain Management, helping companies to reduce their costs, and improving their performance. The supply chain includes vendors, producers and warehouses as well as transportation companies, distribution centers and retailers.
Pandemic COVID-19
Global supply chain management is urgently needed due to the large-scale spread of COVID-19. Global supply chains are vital to response efforts, supplying essential supplies in a timely manner. Other issues have strained the global supply chains, such as China's ongoing lockdown and economic uncertainty. This pandemic is testing supply chain flexibility and resilience. Companies will be evaluated not only on how they respond to this crisis but also on the corporate values that they display.
Economic Impact
Global supply chain management plays a vital role in the global economy. As more manufacturers shift to JIT production (just-in time), they become increasingly dependent upon a single source of vital supplies. JIT production models do have one major problem: they leave companies open for disruptions in their supply networks. A recent survey revealed that almost half of executives intend to eliminate some Chinese production and one-third plan de-emphasize JIT manufacturing.

Opportunities for career advancement
Global supply chain managers oversee all aspects of a business's international procurement strategy. They are responsible for the management of inventory and will work closely with suppliers to ensure that high-quality products are produced. They monitor the supply chain performance and analyze the data. This role also requires a great deal of collaboration with other departments in a company. This list contains some career options. All offer career advantages.
FAQ
What does manufacturing mean?
Manufacturing Industries are companies that manufacture products. Consumers are those who purchase these products. These companies use various processes such as production, distribution, retailing, management, etc., to fulfill this purpose. They manufacture goods from raw materials using machines and other equipment. This includes all types of manufactured goods, including food items, clothing, building supplies, furniture, toys, electronics, tools, machinery, vehicles, pharmaceuticals, medical devices, chemicals, and many others.
How is a production manager different from a producer planner?
The major difference between a Production Planner and a Project Manager is that a Project Manager is often the person responsible for organizing and planning the entire project. While a Production Planner is involved mainly in the planning stage,
What does warehouse refer to?
A warehouse is a place where goods are stored until they are sold. You can have it indoors or outdoors. In some cases it could be both indoors and outdoors.
How can manufacturing reduce production bottlenecks?
Production bottlenecks can be avoided by ensuring that processes are running smoothly during the entire production process, starting with the receipt of an order and ending when the product ships.
This includes planning for capacity requirements as well as quality control measures.
Continuous improvement techniques like Six Sigma are the best way to achieve this.
Six Sigma is a management method that helps to improve quality and reduce waste.
It's all about eliminating variation and creating consistency in work.
How can we increase manufacturing efficiency?
The first step is to identify the most important factors affecting production time. Next, we must find ways to improve those factors. If you don’t know how to start, look at which factors have the greatest impact upon production time. Once you have identified them, it is time to identify solutions.
What is the difference between Production Planning and Scheduling?
Production Planning (PP), or production planning, is the process by which you determine what products are needed at any given time. Forecasting demand is one way to do this.
Scheduling involves the assignment of dates and times to tasks in order to complete them within the timeframe.
Statistics
- According to the United Nations Industrial Development Organization (UNIDO), China is the top manufacturer worldwide by 2019 output, producing 28.7% of the total global manufacturing output, followed by the United States, Japan, Germany, and India.[52][53] (en.wikipedia.org)
- It's estimated that 10.8% of the U.S. GDP in 2020 was contributed to manufacturing. (investopedia.com)
- (2:04) MTO is a production technique wherein products are customized according to customer specifications, and production only starts after an order is received. (oracle.com)
- Many factories witnessed a 30% increase in output due to the shift to electric motors. (en.wikipedia.org)
- According to a Statista study, U.S. businesses spent $1.63 trillion on logistics in 2019, moving goods from origin to end user through various supply chain network segments. (netsuite.com)
External Links
How To
How to use lean manufacturing in the production of goods
Lean manufacturing (or lean manufacturing) is a style of management that aims to increase efficiency, reduce waste and improve performance through continuous improvement. It was developed in Japan during the 1970s and 1980s by Taiichi Ohno, who received the Toyota Production System (TPS) award from TPS founder Kanji Toyoda. Michael L. Watkins published the "The Machine That Changed the World", the first book about lean manufacturing. It was published in 1990.
Lean manufacturing is often defined as a set of principles used to improve the quality, speed, and cost of products and services. It emphasizes eliminating waste and defects throughout the value stream. Lean manufacturing is called just-in-time (JIT), zero defect, total productive maintenance (TPM), or 5S. Lean manufacturing eliminates non-value-added tasks like inspection, rework, waiting.
Lean manufacturing not only improves product quality but also reduces costs. Companies can also achieve their goals faster by reducing employee turnover. Lean manufacturing is a great way to manage the entire value chain including customers, suppliers, distributors and retailers as well as employees. Lean manufacturing is widely used in many industries. Toyota's philosophy is a great example of this. It has helped to create success in automobiles as well electronics, appliances and healthcare.
Lean manufacturing includes five basic principles:
-
Define Value - Determine the value that your business brings to society. Also, identify what sets you apart from your competitors.
-
Reduce Waste – Eliminate all activities that don't add value throughout the supply chain.
-
Create Flow - Ensure work moves smoothly through the process without interruption.
-
Standardize and simplify - Make your processes as consistent as possible.
-
Building Relationships – Establish personal relationships with both external and internal stakeholders.
Lean manufacturing is not a new concept, but it has been gaining popularity over the last few years due to a renewed interest in the economy following the global financial crisis of 2008. Many businesses have adopted lean manufacturing techniques to help them become more competitive. Many economists believe lean manufacturing will play a major role in economic recovery.
Lean manufacturing is now becoming a common practice in the automotive industry, with many benefits. These include improved customer satisfaction, reduced inventory levels, lower operating costs, increased productivity, and better overall safety.
Lean manufacturing can be applied to almost every aspect of an organization. Because it makes sure that all value chains are efficient and effectively managed, Lean Manufacturing is particularly helpful for organizations.
There are three main types of lean manufacturing:
-
Just-in Time Manufacturing (JIT), also known as "pull system": This form of lean manufacturing is often referred to simply as "pull". JIT refers to a system in which components are assembled at the point of use instead of being produced ahead of time. This strategy aims to decrease lead times, increase availability of parts and reduce inventory.
-
Zero Defects Manufacturing - ZDM: ZDM focuses its efforts on making sure that no defective units leave a manufacturing facility. Repairing a part that is damaged during assembly should be done, not scrapping. This applies to finished products, which may need minor repairs before they are shipped.
-
Continuous Improvement (CI), also known as Continuous Improvement, aims at improving the efficiency of operations through continuous identification and improvement to minimize or eliminate waste. Continuous improvement refers to continuous improvement of processes as well people and tools.