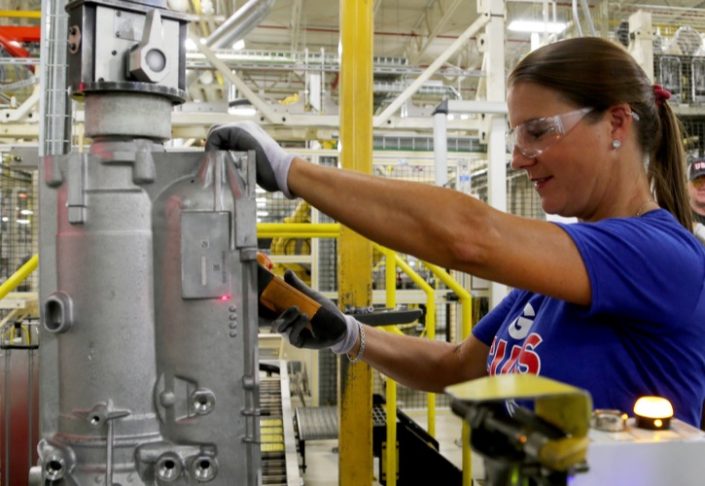
An industrial engineer uses engineering and testing to improve products. Industrial engineers use shake tables to test products at different temperatures, humidity, vibrations, and in product development. Failure data can then be used to improve manufacturing procedures and engineering. Simple changes such a mold-resistant paint can improve the quality of a product and extend its service life. Even the smallest of changes can increase a product’s service life, such as lock-washed positioning.
Job description
It is important to carefully craft your job description if industrial engineers are something you want to pursue. It is the people who are able to combine technical expertise and human intelligence that make industrial engineers the most successful. A well-written job description will help you attract top candidates. You can get some inspiration for a job description by checking out engineering job listings on Monster. An opening paragraph should introduce the company and its benefits to applicants. Whether you're looking to join a world-renowned brand, an innovative start-up, or a fast-paced young company with an open, creative atmosphere, sell your employer as a good place to work.
In addition to having excellent technical skills, industrial engineers also need exceptional communication skills. Industrial processes involve multiple departments and people, so an industrial engineer needs to know how to interact with them all. He or she must also know how to persuade employees and management that his or her proposed approaches will improve efficiency. The best relationship management results in higher productivity. An industrial engineer job description does not require only technical skills.
Education requirements
A bachelor's degree in industrial engineer is necessary to hold a job as an industrial engineer. This position requires extensive math and analytical skills. An industrial engineer must have exceptional communication skills to share their findings with others. Additionally, industrial engineers must be able and willing to create processes and designs that are cost-effective and reduce labor. This field can also be achieved through education. These are some essential requirements for this role.
An industrial engineer must have a college diploma. However, they also need to be able to communicate and interact well with others. To effectively communicate with business leaders as well as employees, industrial engineers must have strong communication skills and analytical abilities. This occupation requires exceptional problem-solving and leadership skills. Also, industrial engineers need to have high levels of technical proficiency and mechanical aptitude.
Options for a career
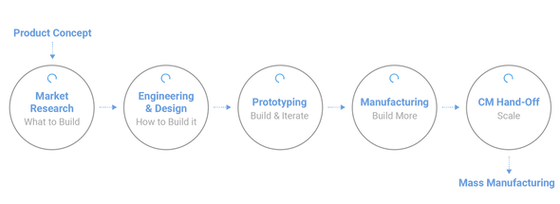
If you're interested in industrial engineering, you have many career options. While most industrial engineers start their career in manufacturing, hospitals and government agencies are other options. There are many other possible jobs for industrial engineers, including in the food and retail trades, education agencies, professional trade associations, computer service centers, and in the IT industry. There are many options for industrial engineers. Here's a list of some of the best. Read on to find out more about the various career opportunities available to you.
An industrial engineer can be focused on efficiency and effectiveness. Their job requires them to balance several factors such as time, number of workers needed, available technology, and actions workers must take. They need to be mindful of worker safety and environmental concerns. Many industrial engineers also work in supply chain management and quality assurance. This field is vital because industries constantly seek ways to reduce costs and increase productivity. They can also be used to help companies develop new product ideas and improve work flow.
Salary
The average industrial engineer salary in 2004 was $87,513 US Dollars. This figure is expected to rise to $114,146 by 2020. However, salaries vary greatly depending on what industry they are in. The salaries of people who work in high-growth industries are more likely to be raised. Bonus figures for Industrial Engineers change frequently and are often moderate. Most bonus recipients are involved in the revenue generation cycle. A degree in industrial engineering is required to get the best salary for this job.
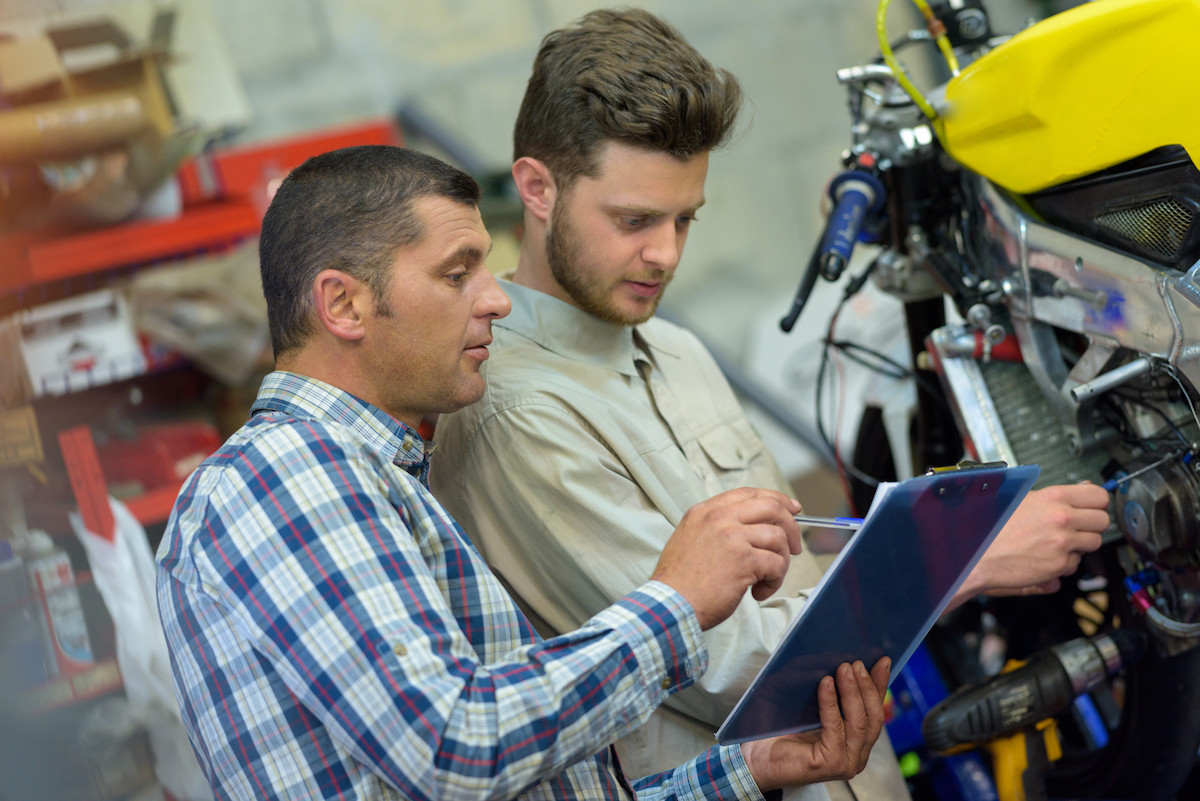
Bachelor's degrees are required for industrial engineers to be successful. Some employers, however, prefer PhDs. The average salary for an industrial engineer in the United States is $56,000 to $121,000. However, this number can fluctuate greatly. Industrial engineers can work in offices, but many jobs require extra time and protective clothing. This makes it necessary to be flexible.
FAQ
What is the difference between Production Planning, Scheduling and Production Planning?
Production Planning (PP), is the process of deciding what production needs to take place at any given time. Forecasting and identifying production capacity are two key elements to this process.
Scheduling refers to the process of allocating specific dates to tasks in order that they can be completed within a specified timeframe.
What does "warehouse" mean?
Warehouses and storage facilities are where goods are kept before being sold. It can be either an indoor or outdoor space. It could be one or both.
How can I learn about manufacturing?
Experience is the best way for you to learn about manufacturing. But if that is not possible you can always read books and watch educational videos.
Why should you automate your warehouse?
Modern warehouses have become more dependent on automation. Increased demand for efficient and faster delivery has resulted in a rise in e-commerce.
Warehouses need to adapt quickly to meet changing needs. Technology is essential for warehouses to be able to adapt quickly to changing needs. Automation of warehouses offers many benefits. Here are some of the reasons automation is worth your investment:
-
Increases throughput/productivity
-
Reduces errors
-
Improves accuracy
-
Safety increases
-
Eliminates bottlenecks
-
This allows companies to scale easily
-
Workers are more productive
-
Provides visibility into everything that happens in the warehouse
-
Enhances customer experience
-
Improves employee satisfaction
-
Minimizes downtime and increases uptime
-
Quality products delivered on time
-
Eliminates human error
-
Assure compliance with regulations
What makes a production planner different from a project manger?
The difference between a product planner and project manager is that a planer is typically the one who organizes and plans the entire project. A production planner, however, is mostly involved in the planning stages.
What types of jobs can you find in logistics
Logistics can offer many different jobs. Some of them are:
-
Warehouse workers – They load and unload pallets and trucks.
-
Transportation drivers - They drive trucks and trailers to deliver goods and carry out pick-ups.
-
Freight handlers: They sort and package freight in warehouses.
-
Inventory managers – These people oversee inventory at warehouses.
-
Sales representatives - They sell products to customers.
-
Logistics coordinators - They plan and organize logistics operations.
-
Purchasing agents - They purchase goods and services needed for company operations.
-
Customer service agents - They answer phone calls and respond to emails.
-
Ship clerks - They issue bills and process shipping orders.
-
Order fillers - They fill orders based on what is ordered and shipped.
-
Quality control inspectors – They inspect incoming and outgoing products to ensure that there are no defects.
-
Others - There are many types of jobs in logistics such as transport supervisors and cargo specialists.
Can certain manufacturing steps be automated?
Yes! Yes. Automation has been around since ancient time. The Egyptians invent the wheel thousands of year ago. We now use robots to help us with assembly lines.
Robotics is used in many manufacturing processes today. These include:
-
Line robots
-
Robot welding
-
Robot painting
-
Robotics inspection
-
Robots that produce products
Automation could also be used to improve manufacturing. 3D printing is a way to make custom products quickly and without waiting weeks or months for them to be manufactured.
Statistics
- [54][55] These are the top 50 countries by the total value of manufacturing output in US dollars for its noted year according to World Bank.[56] (en.wikipedia.org)
- Job #1 is delivering the ordered product according to specifications: color, size, brand, and quantity. (netsuite.com)
- It's estimated that 10.8% of the U.S. GDP in 2020 was contributed to manufacturing. (investopedia.com)
- (2:04) MTO is a production technique wherein products are customized according to customer specifications, and production only starts after an order is received. (oracle.com)
- According to the United Nations Industrial Development Organization (UNIDO), China is the top manufacturer worldwide by 2019 output, producing 28.7% of the total global manufacturing output, followed by the United States, Japan, Germany, and India.[52][53] (en.wikipedia.org)
External Links
How To
How to Use Just-In-Time Production
Just-intime (JIT), a method used to lower costs and improve efficiency in business processes, is called just-in-time. It's the process of obtaining the right amount and timing of resources when you need them. This means you only pay what you use. Frederick Taylor developed the concept while working as foreman in early 1900s. Taylor observed that overtime was paid to workers if they were late in working. He decided to ensure workers have enough time to do their jobs before starting work to improve productivity.
JIT is a way to plan ahead and make sure you don't waste any money. It is important to look at your entire project from beginning to end and ensure that you have enough resources to handle any issues that may arise. You can anticipate problems and have enough equipment and people available to fix them. This will prevent you from spending extra money on unnecessary things.
There are many JIT methods.
-
Demand-driven: This JIT is where you place regular orders for the parts/materials that are needed for your project. This will allow to track how much material has been used up. It will also allow you to predict how long it takes to produce more.
-
Inventory-based : You can stock the materials you need in advance. This allows you to forecast how much you will sell.
-
Project-driven: This method allows you to set aside enough funds for your project. If you know the amount you require, you can buy the materials you need.
-
Resource-based: This is the most common form of JIT. Here, you allocate certain resources based on demand. You will, for example, assign more staff to deal with large orders. If you don’t have many orders you will assign less people to the work.
-
Cost-based: This is a similar approach to resource-based but you are not only concerned with how many people you have, but also how much each one costs.
-
Price-based: This is similar to cost-based but instead of looking at individual workers' salaries, you look at the total company price.
-
Material-based is an alternative to cost-based. Instead of looking at the total cost in the company, this method focuses on the average amount of raw materials that you consume.
-
Time-based JIT is another form of resource-based JIT. Instead of focusing on how much each employee costs, you focus on how long it takes to complete the project.
-
Quality-based JIT - This is another form of resource-based JIT. Instead of thinking about the cost of each employee or the time it takes to produce something, you focus on how good your product quality.
-
Value-based JIT : This is the newest type of JIT. You don't worry about whether the products work or if they meet customer expectations. Instead, you focus on the added value that you provide to your market.
-
Stock-based: This stock-based method focuses on the actual quantity of products being made at any given time. This is used to increase production and minimize inventory.
-
Just-in-time (JIT) planning: This is a combination of JIT and supply chain management. This refers to the scheduling of the delivery of components as soon after they are ordered. It reduces lead times and improves throughput.