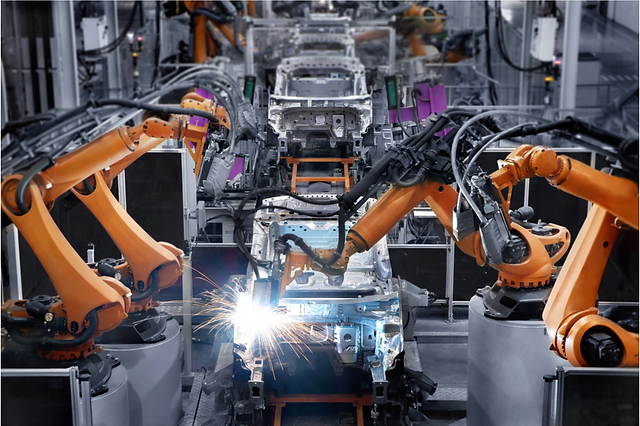
Having a good media supply chain workflow is important. As consumers become more sophisticated, companies must invest in the best technology to ensure that their content is delivered in the most efficient manner. Cloud-based platforms are a great way for you to make sure your media assets get used in the best way possible. You can also use it to facilitate processes and gain insight into your company.
To get the most from your media supply chain workflow you must understand all components. You might have quality control in place to ensure that the media files you receive are in the correct format and audio mapping. This is important to ensure that the content is being delivered in the correct way and that it is preserved correctly. A metadata framework will help you better understand what content is being provided, which can help to locate content more quickly.
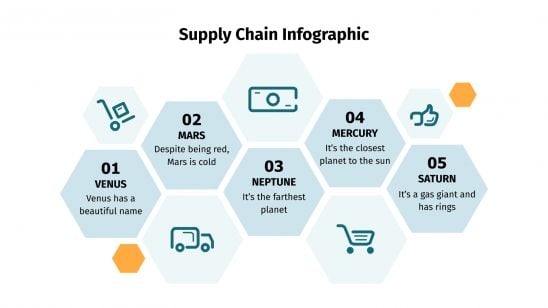
You may be able to receive content from third parties or other companies as part of your media supply chain workflow. This can cause problems as files could arrive in different formats. Also, you may have to modify the files in order to make them usable. This could include changing the format of the master files or transcoding them into smaller proxy files. This can be costly and affect the continuity of your business.
The media supply chain workflows are more complex than ever. Long gone are the days when tape was all you had to do is insert it into a machine. Video editing technology and streaming services have revolutionized the way content is created. With these technologies, you can now create multiple versions of a piece of content, ensuring that you get the highest quality. This will allow you to reduce costs and provide the highest quality content.
A deep understanding of all the involved processes is necessary to get the best from your media supply-chain workflow. You will need to be proficient in client and servers operating systems, networking, media terminology, and other relevant areas. Experience in cloud computing is also required. If you don't know how to do it, consult an IT Analyst who is experienced in this area.
Video engineers work closely together with client teams to develop a media supply-chain workflow. They are responsible of improving functionality, collaborating and delivering media to users. They also have to create requirements for new features.
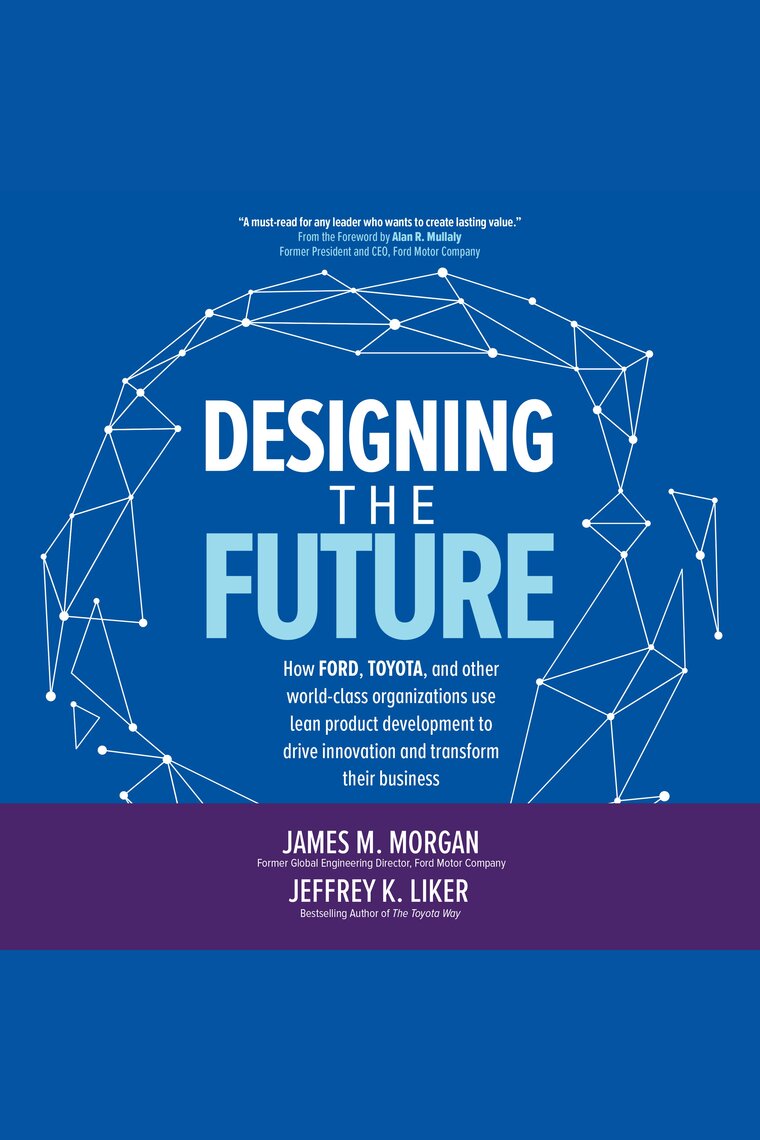
Paramount Global Media Supply Chain Platforms Operations is managed by the Director, Product. They will be working with internal and externe collaborators to develop solutions and implement them for Paramount's customers. They will review product requirements and give feedback on a regular base. They will also lead product development cycles using Agile methodology. They will communicate product requirements to the development teams and supervise the translation of those requirements into the product.
FAQ
What is the difference between Production Planning, Scheduling and Production Planning?
Production Planning (PP) is the process of determining what needs to be produced at any given point in time. Forecasting demand is one way to do this.
Scheduling refers to the process of allocating specific dates to tasks in order that they can be completed within a specified timeframe.
What is the role and responsibility of a Production Planner?
Production planners ensure that all project aspects are completed on time, within budget and within the scope. They make sure that the product and services meet client expectations.
What is the role of a logistics manager
Logistics managers make sure all goods are delivered on schedule and without damage. This is achieved by using their knowledge and experience with the products of the company. He/she should also ensure enough stock is available to meet demand.
What are the 4 types manufacturing?
Manufacturing refers to the transformation of raw materials into useful products by using machines and processes. Manufacturing involves many activities, including designing, building, testing and packaging, shipping, selling, service, and so on.
Statistics
- It's estimated that 10.8% of the U.S. GDP in 2020 was contributed to manufacturing. (investopedia.com)
- In the United States, for example, manufacturing makes up 15% of the economic output. (twi-global.com)
- Job #1 is delivering the ordered product according to specifications: color, size, brand, and quantity. (netsuite.com)
- You can multiply the result by 100 to get the total percent of monthly overhead. (investopedia.com)
- [54][55] These are the top 50 countries by the total value of manufacturing output in US dollars for its noted year according to World Bank.[56] (en.wikipedia.org)
External Links
How To
Six Sigma: How to Use it in Manufacturing
Six Sigma can be described as "the use of statistical process control (SPC), techniques to achieve continuous improvement." Motorola's Quality Improvement Department developed it at their Tokyo plant in Japan in 1986. Six Sigma's core idea is to improve the quality of processes by standardizing and eliminating defects. In recent years, many companies have adopted this method because they believe there is no such thing as perfect products or services. The main goal of Six Sigma is to reduce variation from the mean value of production. This means that if you take a sample of your product, then measure its performance against the average, you can find out what percentage of the time the process deviates from the norm. If there is a significant deviation from the norm, you will know that something needs to change.
Understanding the nature of variability in your business is the first step to Six Sigma. Once you have this understanding, you will need to identify sources and causes of variation. These variations can also be classified as random or systematic. Random variations happen when people make errors; systematic variations are caused externally. These are, for instance, random variations that occur when widgets are made and some fall off the production line. If however, you notice that each time you assemble a widget it falls apart in exactly the same spot, that is a problem.
Once you've identified the problem areas you need to find solutions. The solution could involve changing how you do things, or redesigning your entire process. You should then test the changes again after they have been implemented. If they didn't work, then you'll need to go back to the drawing board and come up with another plan.