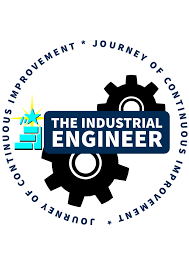
It is the process that predicts future demand for certain products or services. This is an important part of supply-chain management as it allows businesses to meet customer needs and maximize profits.
What is Demand Planning (DDP)?
To forecast demand for a product or service, data is analyzed, including sales information and inventory information. It's a complex task that may involve multiple departments.
What is the Demand Planner?
A demand planner is a member of a company's supply chain team who uses their understanding of the industry and their business acumen to predict future market trends and customer needs. The demand planner creates a plan for the company that includes optimal inventory levels, timelines for shipping, and other steps to meet the demand.
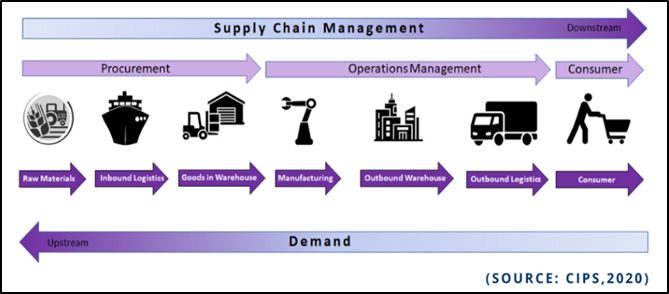
What Are the Best Tools for Demand Planning?
The most efficient demand planning tools provide full visibility of the company's supply chain. This gives demand planners the ability to track and analyze demand in real-time, ensuring they are able to make decisions as quickly as possible.
What is the best way to predict demand?
One way to predict demand is by analyzing sales data, which is often provided directly by a company's sales team. These data will help you identify any issues your sales team is having with customers. This could result in changes to your demand plan.
Another method is to use statistical analysis to determine the relationships between sales and inventory. The accuracy of demand plans can be improved by using analytics to discover these relationships.
What Are some of the most common pitfalls in Demand Planning?
Demand planning is a difficult task that requires time and effort. If your demand plan is inaccurate, a lot of things can go wrong, such as excess inventory which locks up working capital and increases inventory carrying costs. This can lead to a loss in money for the company or negatively impact its customers.
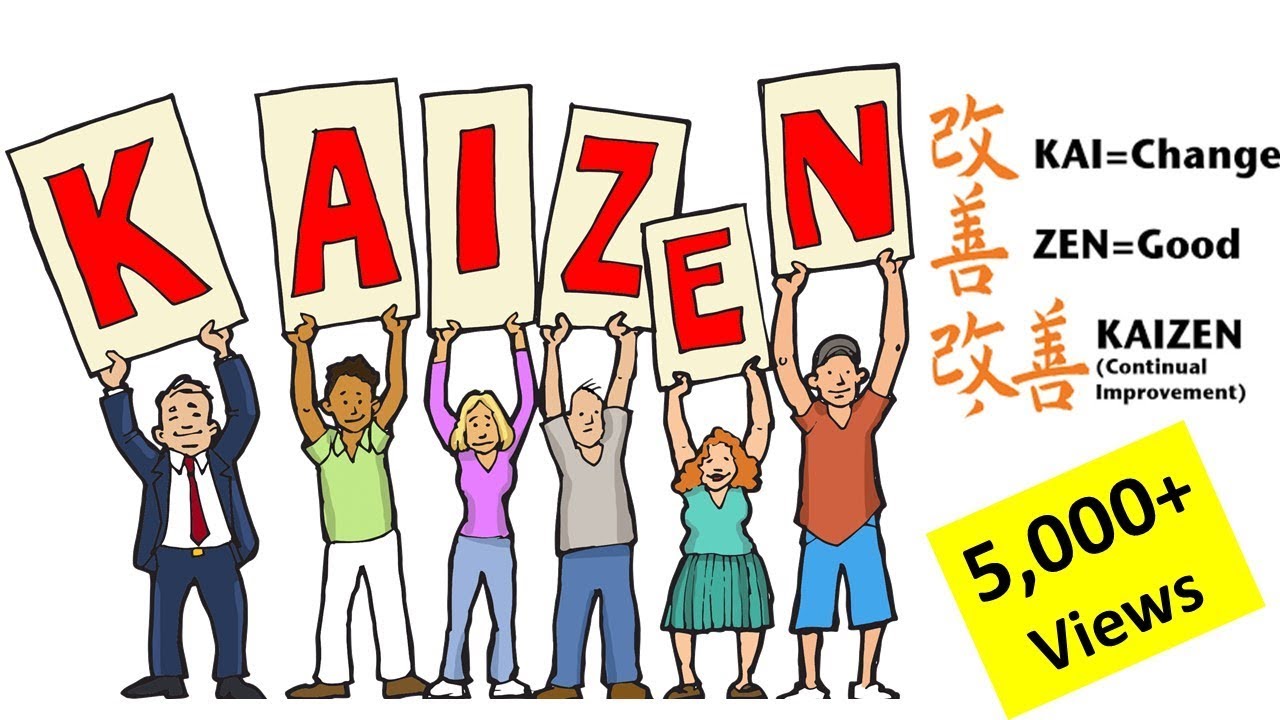
What Are Some of the Most Common Skills a Demand Planner Needs?
A demand planner should have good analytical and management abilities. They need to be able to analyze complex data sets and make sound decisions based on the results. They must also be able build consensus with others and work together.
What Are Some of the Most Valuable Skills in Demand Planning?
A great demand planner will be adept at both working with people and using technology. As they will be working closely with different teams on developing a forecasting tool, they should be able effectively communicate with them.
A demand planner must be able to analyze a variety of statistical data. They should also know how to use the Delphi method to get feedback from experts and facilitators outside the company. This method can come in handy if you only have a small amount of data but need multiple perspectives on an issue.
FAQ
How can I learn about manufacturing?
Experience is the best way for you to learn about manufacturing. You can read books, or watch instructional videos if you don't have the opportunity to do so.
What are the requirements to start a logistics business?
It takes a lot of skills and knowledge to run a successful logistics business. Good communication skills are essential to effectively communicate with your suppliers and clients. You need to understand how to analyze data and draw conclusions from it. You must be able manage stress and pressure under pressure. You need to be innovative and creative to come up with new ways to increase efficiency. To motivate and guide your team towards reaching organizational goals, you must have strong leadership skills.
It is important to be organized and efficient in order to meet tight deadlines.
What are the responsibilities of a manufacturing manager
A manufacturing manager has to ensure that all manufacturing processes work efficiently and effectively. They should also be aware of any problems within the company and act accordingly.
They must also be able to communicate with sales and marketing departments.
They must also keep up-to-date with the latest trends in their field and be able use this information to improve productivity and efficiency.
What type of jobs is there in logistics
There are many types of jobs in logistics. These are some of the jobs available in logistics:
-
Warehouse workers – They load, unload and transport pallets and trucks.
-
Transportation drivers - They drive trucks and trailers to deliver goods and carry out pick-ups.
-
Freight handlers – They sort and package freight at warehouses.
-
Inventory managers – They manage the inventory in warehouses.
-
Sales reps are people who sell products to customers.
-
Logistics coordinators: They plan and manage logistics operations.
-
Purchasing agents - They buy goods and services that are necessary for company operations.
-
Customer service representatives - Answer calls and email from customers.
-
Shippers clerks - They process shipping order and issue bills.
-
Order fillers: They fill orders based off what has been ordered and shipped.
-
Quality control inspectors (QCI) - They inspect all incoming and departing products for potential defects.
-
Others - There are many other types of jobs available in logistics, such as transportation supervisors, cargo specialists, etc.
What is the role and responsibility of a Production Planner?
Production planners ensure all aspects of the project are delivered within time and budget. A production planner ensures that the service and product meet the client's expectations.
What does warehouse refer to?
Warehouses and storage facilities are where goods are kept before being sold. It can be indoors or out. It could be one or both.
What does manufacturing mean?
Manufacturing Industries refers to businesses that manufacture products. These products are sold to consumers. These companies employ many processes to achieve this purpose, such as production and distribution, retailing, management and so on. They create goods from raw materials, using machines and various other equipment. This covers all types of manufactured goods including clothing, food, building supplies and furniture, as well as electronics, tools, machinery, vehicles and pharmaceuticals.
Statistics
- Many factories witnessed a 30% increase in output due to the shift to electric motors. (en.wikipedia.org)
- (2:04) MTO is a production technique wherein products are customized according to customer specifications, and production only starts after an order is received. (oracle.com)
- It's estimated that 10.8% of the U.S. GDP in 2020 was contributed to manufacturing. (investopedia.com)
- [54][55] These are the top 50 countries by the total value of manufacturing output in US dollars for its noted year according to World Bank.[56] (en.wikipedia.org)
- In the United States, for example, manufacturing makes up 15% of the economic output. (twi-global.com)
External Links
How To
How to Use the Just-In-Time Method in Production
Just-intime (JIT), a method used to lower costs and improve efficiency in business processes, is called just-in-time. It's a way to ensure that you get the right resources at just the right time. This means that you only pay for what you actually use. Frederick Taylor first coined this term while working in the early 1900s as a foreman. Taylor observed that overtime was paid to workers if they were late in working. He decided that workers would be more productive if they had enough time to complete their work before they started to work.
The idea behind JIT is that you should plan ahead and have everything ready so you don't waste money. It is important to look at your entire project from beginning to end and ensure that you have enough resources to handle any issues that may arise. You'll be prepared to handle any potential problems if you know in advance. This way, you won't end up paying extra money for things that weren't really necessary.
There are many JIT methods.
-
Demand-driven: This JIT is where you place regular orders for the parts/materials that are needed for your project. This will let you track the amount of material left over after you've used it. It will also allow you to predict how long it takes to produce more.
-
Inventory-based: This is a type where you stock the materials required for your projects in advance. This allows you to forecast how much you will sell.
-
Project-driven: This means that you have enough money to pay for your project. When you know how much you need, you'll purchase the appropriate amount of materials.
-
Resource-based JIT is the most widespread form. You allocate resources based on the demand. You might assign more people to help with orders if there are many. You'll have fewer orders if you have fewer.
-
Cost-based: This is similar to resource-based, except that here you're not just concerned about how many people you have but how much each person costs.
-
Price-based pricing: This is similar in concept to cost-based but instead you look at how much each worker costs, it looks at the overall company's price.
-
Material-based: This is quite similar to cost-based, but instead of looking at the total cost of the company, you're concerned with how much raw materials you spend on average.
-
Time-based JIT: This is another variant of resource-based JIT. Instead of focusing solely on the amount each employee costs, focus on how long it takes for the project to be completed.
-
Quality-based JIT: Another variation on resource-based JIT. Instead of worrying about the costs of each employee or how long it takes for something to be made, you should think about how quality your product is.
-
Value-based JIT : This is the newest type of JIT. In this case, you're not concerned with how well the products perform or whether they meet customer expectations. Instead, you are focused on adding value to the marketplace.
-
Stock-based is an inventory-based system that measures the number of items produced at any given moment. This is used to increase production and minimize inventory.
-
Just-in time (JIT), planning: This is a combination JIT/supply chain management. It refers to the process of scheduling the delivery of components as soon as they are ordered. This is important as it reduces lead time and increases throughput.