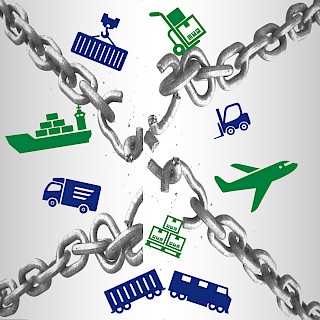
Industrial Engineering Managers are an integral part of any team, regardless of whether it is for a new or regular project. They are responsible for directing staff and improving production output. This includes coordinating the layout and design of the factory floor and overseeing the implementation of processes and procedures. Additionally, they offer technical knowledge and expertise that can be used to aid in the development of new products or processes.
Industrial engineering managers are responsible for maintaining and developing efficient manufacturing processes. This requires a working knowledge of robotics and automation. They must also monitor and maintain industrial processes and ensure that they comply with safety and health standards. They also oversee the use of raw material and consumables. They also do studies to optimize workflow and maximize space usage. The manager oversees all work projects, including reductions in cycle time, cost reductions and improvement of processes. They are also responsible for managing preventative maintenance plans.
The manager works in collaboration with other teams to develop new processes, improve efficiency, and streamline operations. The manager also supervises the renovation and installation of equipment. As part of the project management process, the manager communicates technical information to non-technical stakeholders. Additionally, the manager ensures that resources are available to teams and makes site visits at suppliers' facilities. He or she is a champion for members of the team and ensures they adhere to quality standards.
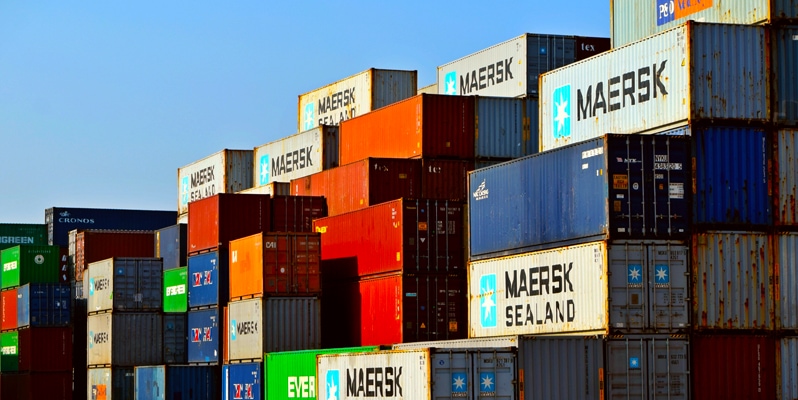
Industrial Engineering Managers are expected to be highly motivated, creative, and able to solve problems. They must be able climb and walk for up to 12 hours per day, as well as be able handle extreme temperatures. They must also be able communicate with all levels of employees.
An engineering degree or related field is required for Industrial Engineering Managers. They must also have at least five years experience in this field. Employers prefer candidates who have completed postgraduate studies. They may also need to have specific skills, such as project management or logistics.
Industrial Engineering Managers oversee the design and development of new products and processes. They have a strong background in problem-solving and quality improvement. They enjoy working in a team. Managers are more successful when they are able to encourage employee growth.
Industrial Engineers have the ability to streamline operations and reduce costs. They are skilled in manufacturing processes and can meet deadlines. They also have experience with recruiting, human resources, logistics, and vendor / supplier relations. They are skilled in setting goals, managing procedures, and creating budgets. They can also prepare strategies to improve the efficiency of engineering projects.
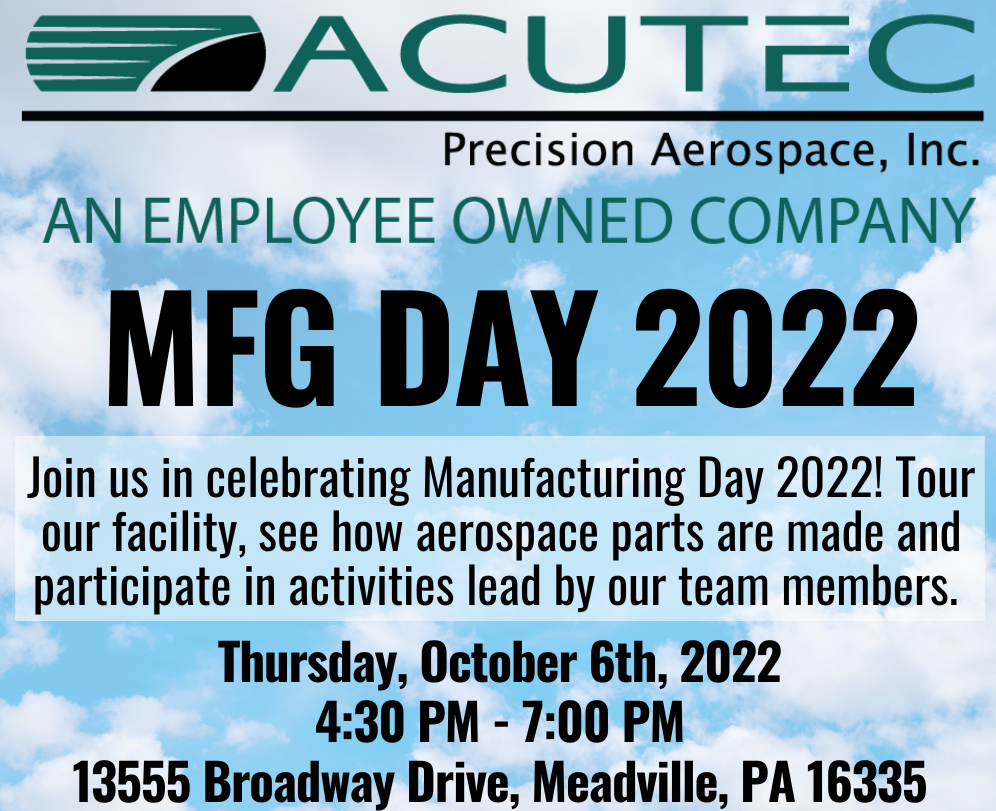
The industrial engineering manager may be responsible for the design and execution of new manufacturing procedures or operating equipment. They must develop plans for new equipment and operating methods using existing standards and guidelines. They are also responsible for overseeing the implementation and monitoring of waste elimination plans. They also have to analyze the factory's labor productivity.
Industrial Engineering Managers can also contribute their expertise in developing strategies for improving productivity, developing new products, and managing human resources. They can also improve efficiency and develop new processes.
FAQ
What is production planning?
Production planning is the process of creating a plan that covers all aspects of production. This includes scheduling, budgeting and crew, location, equipment, props, and more. This document is designed to make sure everything is ready for when you're ready to shoot. This document should also include information on how to get the best result on set. This includes information on shooting times, locations, cast lists and crew details.
It is important to first outline the type of film you would like to make. You might have an idea of where you want to film, or you may have specific locations or sets in mind. Once you've identified the locations and scenes you want to use, you can begin to plan what elements you need for each scene. Perhaps you have decided that you need to buy a car but aren't sure which model. If this is the case, you might start searching online for car models and then narrow your options by selecting from different makes.
Once you have found the right vehicle, you can think about adding accessories. Do you have people who need to be seated in the front seat? Maybe you need someone to move around in the back. You may want to change the interior's color from black or white. These questions will help guide you in determining the ideal look and feel for your car. Another thing you can do is think about what type of shots are desired. Will you be filming close-ups or wide angles? Maybe you want to show the engine and the steering wheel. These things will help you to identify the car that you are looking for.
Once you have established all the details, you can create a schedule. A schedule will tell you when you need to start shooting and when you need to finish. Each day will include the time when you need to arrive at the location, when you need to leave and when you need to return home. So everyone is clear about what they need to do. If you need to hire extra staff, you can make sure you book them in advance. It's not worth paying someone to show up if you haven't told him.
When creating your schedule, you will also need to consider the number of days you need to film. Some projects may only take a couple of days, while others could last for weeks. When creating your schedule, be aware of whether you need more shots per day. Multiplying takes in the same area will result both in increased costs and a longer time. If you are unsure if you need multiple takes, it is better to err on the side of caution and shoot fewer takes rather than risk wasting money.
Budget setting is an important part of production planning. It is important to set a realistic budget so you can work within your budget. If you have to reduce your budget due to unexpected circumstances, you can always lower it later. But, don't underestimate how much money you'll spend. You'll end up with less money after paying for other things if the cost is underestimated.
Planning production is a tedious process. Once you have a good understanding of how everything works together, planning future projects becomes easy.
What is the difference between Production Planning and Scheduling?
Production Planning (PP), or production planning, is the process by which you determine what products are needed at any given time. This is done through forecasting demand and identifying production capacities.
Scheduling involves the assignment of dates and times to tasks in order to complete them within the timeframe.
What jobs are available in logistics?
There are different kinds of jobs available in logistics. Some of them are:
-
Warehouse workers - They load trucks and pallets.
-
Transport drivers - These are people who drive trucks and trailers to transport goods or perform pick-ups.
-
Freight handlers: They sort and package freight in warehouses.
-
Inventory managers – They manage the inventory in warehouses.
-
Sales representatives - They sell products.
-
Logistics coordinators - They plan and organize logistics operations.
-
Purchasing agents – They buy goods or services necessary to run a company.
-
Customer service representatives - Answer calls and email from customers.
-
Shipping clerks - They process shipping orders and issue bills.
-
Order fillers - These people fill orders based on what has been ordered.
-
Quality control inspectors are responsible for inspecting incoming and outgoing products looking for defects.
-
Other - Logistics has many other job opportunities, including transportation supervisors, logistics specialists, and cargo specialists.
What skills does a production planner need?
Being a production planner is not easy. You need to be organized and flexible. It is also important to be able communicate with colleagues and clients.
Statistics
- Many factories witnessed a 30% increase in output due to the shift to electric motors. (en.wikipedia.org)
- According to the United Nations Industrial Development Organization (UNIDO), China is the top manufacturer worldwide by 2019 output, producing 28.7% of the total global manufacturing output, followed by the United States, Japan, Germany, and India.[52][53] (en.wikipedia.org)
- You can multiply the result by 100 to get the total percent of monthly overhead. (investopedia.com)
- [54][55] These are the top 50 countries by the total value of manufacturing output in US dollars for its noted year according to World Bank.[56] (en.wikipedia.org)
- Job #1 is delivering the ordered product according to specifications: color, size, brand, and quantity. (netsuite.com)
External Links
How To
Six Sigma in Manufacturing
Six Sigma is defined by "the application SPC (statistical process control) techniques to achieve continuous improvements." Motorola's Quality Improvement Department in Tokyo, Japan developed Six Sigma in 1986. Six Sigma's core idea is to improve the quality of processes by standardizing and eliminating defects. This method has been adopted by many companies in recent years as they believe there are no perfect products or services. The main goal of Six Sigma is to reduce variation from the mean value of production. This means that you can take a sample from your product and then compare its performance to the average to find out how often the process differs from the norm. If the deviation is excessive, it's likely that something needs to be fixed.
Understanding how variability works in your company is the first step to Six Sigma. Once you have a good understanding of the basics, you can identify potential sources of variation. You'll also want to determine whether these variations are random or systematic. Random variations happen when people make errors; systematic variations are caused externally. These are, for instance, random variations that occur when widgets are made and some fall off the production line. However, if you notice that every time you assemble a widget, it always falls apart at exactly the same place, then that would be a systematic problem.
Once you've identified the problem areas you need to find solutions. This could mean changing your approach or redesigning the entire process. To verify that the changes have worked, you need to test them again. If they don't work, you will need to go back to the drawing boards and create a new plan.