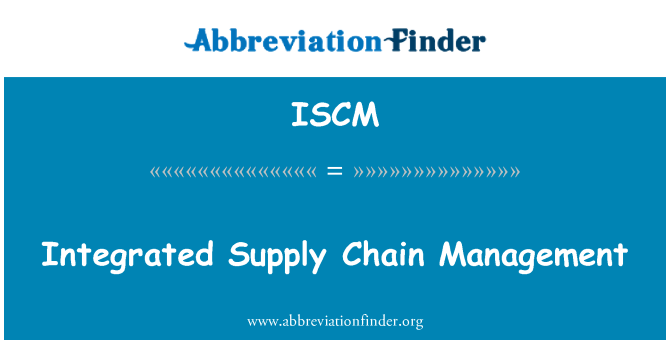
The Industrial Products & Services sector of the industrial manufacturing industry is experiencing increased global competition and a shortage in skilled workers. Combined with increased supply chain volatility, the industrial manufacturing industry faces a challenging landscape in the 2020s. To optimize growth in established markets as well as to identify growth opportunities, the Industrial Products & Services market requires a holistic culture of Innovation.
According to the Deloitte and Manufacturing Institute study, the US manufacturing workforce will experience the largest shortfall of skilled workers in history, as 2 million jobs are estimated to be unfilled over the next decade. The future of the industry is now in the hands of manufacturers. They must decide how to develop their digital capabilities and innovate. Deloitte's Industrial Manufacturing Team can help manufacturers navigate the landscape of the industry.
The fourth industrial revolution continues to disrupt manufacturing. This means that the industry must prepare its workforce for a future where there will be networking and digital transformation. The Industrial Manufacturing team is skilled at establishing innovative management models that are grounded industry-specific expertise and deep industry knowledge. It also offers a wide range digital transformation services that can be used to assist manufacturers in the digital age.
The Deloitte research is based on extensive secondary analysis of labor supply and interviews with executives of manufacturing companies of all sizes. The research also includes economic projections. The importance of diversity in the workforce is also highlighted by these findings. Half of respondents identified adaptability to company values being a key aspect of their job satisfaction. Over a third of respondents said that employees need to have a purpose to feel satisfied at their jobs. Executives also think that millennials value environmental awareness and are increasingly interested in climate change issues.
Deloitte's Oxford Economic Model predicts that the manufacturing GDP will rise at a moderate pace of 1.3 per cent in 2020. However, the study notes that this level of growth is expected to be less than half of the rate seen in the past few years. This will force companies to rethink their supply chain assurance strategies. Businesses will need to focus their efforts on other management initiatives such a greater resilience in operations. According to Deloitte research, manufacturers will probably be making decisions about work places and work practices.
Manufacturing companies need to create career pathways and build an inclusive culture to ensure they are ready for the future. Also, increasing operational resilience can improve manufacturing efficiency and decrease waste. In addition, the combination of digital technologies and lean principles can also help reduce manufacturing variability.
Deloitte released a new report on diversity in manufacturing as the US manufacturing industry continues its evolution. Deloitte's new report "Beyond Reskilling", focuses on how diversity is crucial to the future of manufacturing and highlights the benefits that a diverse workforce can bring.
FAQ
Is automation important in manufacturing?
Not only is automation important for manufacturers, but it's also vital for service providers. Automation allows them to deliver services quicker and more efficiently. It reduces human errors and improves productivity, which in turn helps them lower their costs.
What are the responsibilities of a production planner
Production planners ensure that all project aspects are completed on time, within budget and within the scope. They ensure that the product or service is of high quality and meets client requirements.
What makes a production planner different from a project manger?
The main difference between a production planner and a project manager is that a project manager is usually the person who plans and organizes the entire project, whereas a production planner is mainly involved in the planning stage of the project.
Statistics
- In 2021, an estimated 12.1 million Americans work in the manufacturing sector.6 (investopedia.com)
- [54][55] These are the top 50 countries by the total value of manufacturing output in US dollars for its noted year according to World Bank.[56] (en.wikipedia.org)
- In the United States, for example, manufacturing makes up 15% of the economic output. (twi-global.com)
- You can multiply the result by 100 to get the total percent of monthly overhead. (investopedia.com)
- Job #1 is delivering the ordered product according to specifications: color, size, brand, and quantity. (netsuite.com)
External Links
How To
How to Use the Just In Time Method in Production
Just-intime (JIT), a method used to lower costs and improve efficiency in business processes, is called just-in-time. It's the process of obtaining the right amount and timing of resources when you need them. This means that only what you use is charged to your account. The term was first coined by Frederick Taylor, who developed his theory while working as a foreman in the early 1900s. He saw how overtime was paid to workers for work that was delayed. He realized that workers should have enough time to complete their jobs before they begin work. This would help increase productivity.
The idea behind JIT is that you should plan ahead and have everything ready so you don't waste money. It is important to look at your entire project from beginning to end and ensure that you have enough resources to handle any issues that may arise. If you expect problems to arise, you will be able to provide the necessary equipment and personnel to address them. This will ensure that you don't spend more money on things that aren't necessary.
There are many types of JIT methods.
-
Demand-driven: This type of JIT allows you to order the parts/materials required for your project on a regular basis. This will let you track the amount of material left over after you've used it. This will let you know how long it will be to produce more.
-
Inventory-based: This allows you to store the materials necessary for your projects in advance. This allows one to predict how much they will sell.
-
Project-driven: This is an approach where you set aside enough funds to cover the cost of your project. Once you have an idea of how much material you will need, you can purchase the necessary materials.
-
Resource-based JIT : This is probably the most popular type of JIT. You allocate resources based on the demand. For example, if there is a lot of work coming in, you will have more people assigned to them. If you don't have many orders, you'll assign fewer people to handle the workload.
-
Cost-based: This is a similar approach to resource-based but you are not only concerned with how many people you have, but also how much each one costs.
-
Price-based: This is very similar to cost-based, except that instead of looking at how much each individual worker costs, you look at the overall price of the company.
-
Material-based: This approach is similar to cost-based. However, instead of looking at the total cost for the company, you look at how much you spend on average on raw materials.
-
Time-based JIT: A variation on resource-based JIT. Instead of focusing only on how much each employee is costing, you should focus on how long it takes to complete your project.
-
Quality-based JIT: This is another variation of resource based JIT. Instead of thinking about how much each employee costs or how long it takes to manufacture something, you think about how good the quality of your product is.
-
Value-based JIT is the newest form of JIT. This is where you don't care about how the products perform or whether they meet customers' expectations. Instead, you are focused on adding value to the marketplace.
-
Stock-based: This is an inventory-based method that focuses on the actual number of items being produced at any given time. It's used when you want to maximize production while minimizing inventory.
-
Just-in time (JIT), planning: This is a combination JIT/supply chain management. It is the process of scheduling components' delivery as soon as they have been ordered. It reduces lead times and improves throughput.