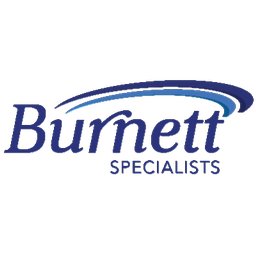
A blue collar job is generally a manual labor job. These jobs might be in the fields of agriculture, manufacturing, healthcare or hospitality. While some may require some skills, such as electricians or plumbers, others may not. Blue collar jobs often pay decent wages and offer excellent career growth.
The Fourth Industrial Revolution will transform the labor market for manual workers. This revolution includes artificial intelligence and robotics, as well as machine learning and 3D printing. Companies will need a more skilled workforce to be successful. It will also require that firms shift away from transactional relations and move towards more enduring relationships.
As a result, companies are forced to hire workers from outside of the United States. These workers may be hired in exchange for per-item wages. Other workers might be paid per the project. Blue collar jobs are on the rise, which is positive in all cases.
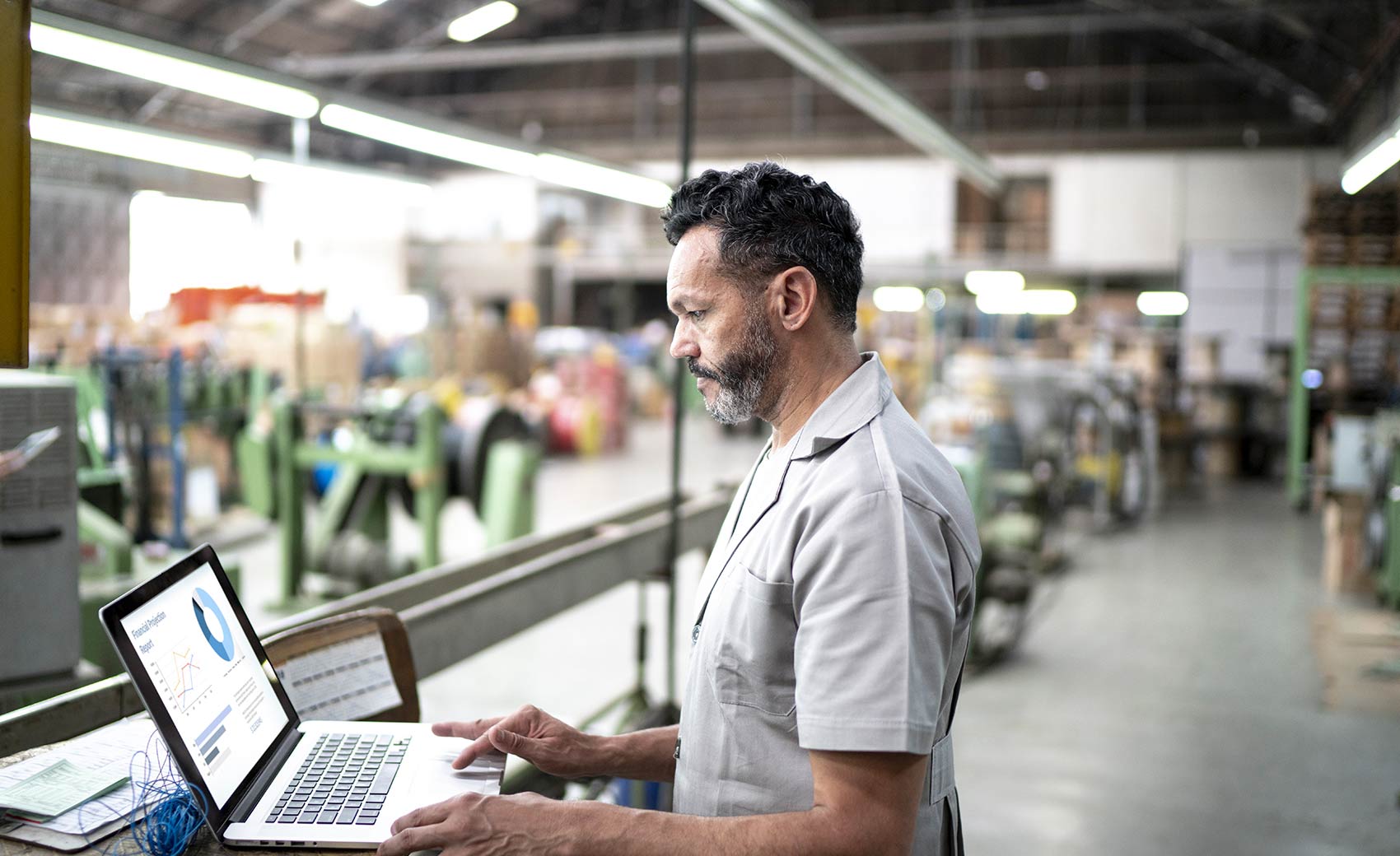
These jobs are more physically demanding than white collar jobs, but they tend to be well-paid. These jobs are an excellent source of income and many companies will invest in training their staff. Some examples of these jobs are signal and track switching repairers, nuclear power reactor operators, and electrical and electronics repairers. These jobs require only a high school diploma, while others require on-the-job training.
The availability of blue collar jobs is also higher than that of white collar positions. Blue collar workers actually make up a large part of India's workforce. India has 210 million workers in the agricultural sector, and 290 million in the non-agricultural sector. Blue collar workers are in demand at an increasing rate.
Companies are also being transformed by the Fourth Industrial Revolution in how they manage their blue-collar workers. Companies are moving away from transactional relationships to build lasting relationships, and replacing manual jobs by digital ones. Firms can build stronger relationships with their employees and increase productivity by prioritizing employee needs.
Blue collar workers are also in demand, but they face competing realities. They might be concerned about their jobs' stability, or about retirement. Regardless of these concerns, blue collar workers tend to be optimistic about their futures. Blue-collar workers are actually saving more for retirement. Additionally, blue collar jobs will likely increase in popularity as the economy improves.

These jobs are also not in danger from automation. The Association for Manufacturing Technology has found that for every job that is replaced by technology there are five new jobs. Signal and track switch repairers earned $76,210 an average salary, which was the largest increase in salaries.
Additionally, blue collar jobs have a rising number of better-paying positions. The earnings of many blue collar jobs are well above the national average, making it an ideal option for those looking for a job with good pay. In addition, many blue collar jobs require a high degree of problem-solving skills, and are more than likely to provide good career growth.
FAQ
What is the responsibility of a logistics manager?
Logistics managers make sure all goods are delivered on schedule and without damage. This is achieved by using their knowledge and experience with the products of the company. He/she should ensure that sufficient stock is available in order to meet customer demand.
What do we need to know about Manufacturing Processes in order to learn more about Logistics?
No. No. However, knowing about manufacturing processes will definitely give you a better understanding of how logistics works.
What is the job of a manufacturer manager?
Manufacturing managers must ensure that manufacturing processes are efficient, effective, and cost-effective. They should also be aware and responsive to any company problems.
They should also know how to communicate with other departments such as sales and marketing.
They must also keep up-to-date with the latest trends in their field and be able use this information to improve productivity and efficiency.
What does it take for a logistics enterprise to succeed?
It takes a lot of skills and knowledge to run a successful logistics business. To communicate effectively with clients and suppliers, you must be able to communicate well. You should be able analyse data and draw inferences. You must be able to work well under pressure and handle stressful situations. To increase efficiency and creativity, you need to be creative. Strong leadership qualities are essential to motivate your team and help them achieve their organizational goals.
It is important to be organized and efficient in order to meet tight deadlines.
What can I do to learn more about manufacturing?
Hands-on experience is the best way to learn more about manufacturing. You can read books, or watch instructional videos if you don't have the opportunity to do so.
What is production planning?
Production Planning involves developing a plan for all aspects of the production, including scheduling, budgeting, casting, crew, location, equipment, props, etc. It is important to have everything ready and planned before you start shooting. It should also contain information on achieving the best results on set. It should include information about shooting locations, casting lists, crew details, equipment requirements, and shooting schedules.
The first step in filming is to define what you want. You may have decided where to shoot or even specific locations you want to use. Once you have identified your locations and scenes it's time to begin figuring out what elements you will need for each one. You might decide you need a car, but not sure what make or model. You could look online for cars to see what options are available, and then narrow down your choices by selecting between different makes or models.
After you've found the perfect car, it's time to start thinking about adding extras. Do you need people sitting in the front seats? Maybe you need someone to move around in the back. You may want to change the interior's color from black or white. These questions will help determine the look and feel you want for your car. You can also think about the type of shots you want to get. Will you be filming close-ups or wide angles? Maybe you want to show the engine and the steering wheel. These things will help you to identify the car that you are looking for.
Once you have all the information, you are ready to create a plan. A schedule will tell you when you need to start shooting and when you need to finish. The schedule will show you when to get there, what time to leave, and when to return home. Everyone will know what they need and when. You can also make sure to book extra staff in advance if you have to hire them. There is no point in hiring someone who won't turn up because you didn't let him know.
Also, consider how many days you will be filming your schedule. Some projects can be completed in a matter of days or weeks. Others may take several days. You should consider whether you will need more than one shot per week when creating your schedule. Shooting multiple takes over the same location will increase costs and take longer to complete. It is better to be cautious and take fewer shots than you risk losing money if you are not sure if multiple takes are necessary.
Budgeting is another important aspect of production planning. You will be able to manage your resources if you have a realistic budget. It is possible to reduce the budget at any time if you experience unexpected problems. However, it is important not to overestimate the amount that you will spend. You will end up spending less money if you underestimate the cost of something.
Production planning is a complicated process. But once you understand how everything works together, it becomes much easier to plan future project.
What is the importance of automation in manufacturing?
Not only is automation important for manufacturers, but it's also vital for service providers. It allows them to offer services faster and more efficiently. In addition, it helps them reduce costs by reducing human errors and improving productivity.
Statistics
- You can multiply the result by 100 to get the total percent of monthly overhead. (investopedia.com)
- It's estimated that 10.8% of the U.S. GDP in 2020 was contributed to manufacturing. (investopedia.com)
- Job #1 is delivering the ordered product according to specifications: color, size, brand, and quantity. (netsuite.com)
- Many factories witnessed a 30% increase in output due to the shift to electric motors. (en.wikipedia.org)
- According to the United Nations Industrial Development Organization (UNIDO), China is the top manufacturer worldwide by 2019 output, producing 28.7% of the total global manufacturing output, followed by the United States, Japan, Germany, and India.[52][53] (en.wikipedia.org)
External Links
How To
Six Sigma in Manufacturing
Six Sigma is defined by "the application SPC (statistical process control) techniques to achieve continuous improvements." It was developed by Motorola's Quality Improvement Department at their plant in Tokyo, Japan, in 1986. Six Sigma's core idea is to improve the quality of processes by standardizing and eliminating defects. In recent years, many companies have adopted this method because they believe there is no such thing as perfect products or services. Six Sigma seeks to reduce variation between the mean production value. You can calculate the percentage of deviation from the norm by taking a sample of your product and comparing it to the average. If it is too large, it means that there are problems.
Understanding how variability works in your company is the first step to Six Sigma. Once you understand that, it is time to identify the sources of variation. You'll also want to determine whether these variations are random or systematic. Random variations occur when people do mistakes. Symmetrical variations are caused due to factors beyond the process. If you make widgets and some of them end up on the assembly line, then those are considered random variations. You might notice that your widgets always fall apart at the same place every time you put them together.
Once you've identified the problem areas you need to find solutions. You might need to change the way you work or completely redesign the process. To verify that the changes have worked, you need to test them again. If they don't work you need to rework them and come up a better plan.