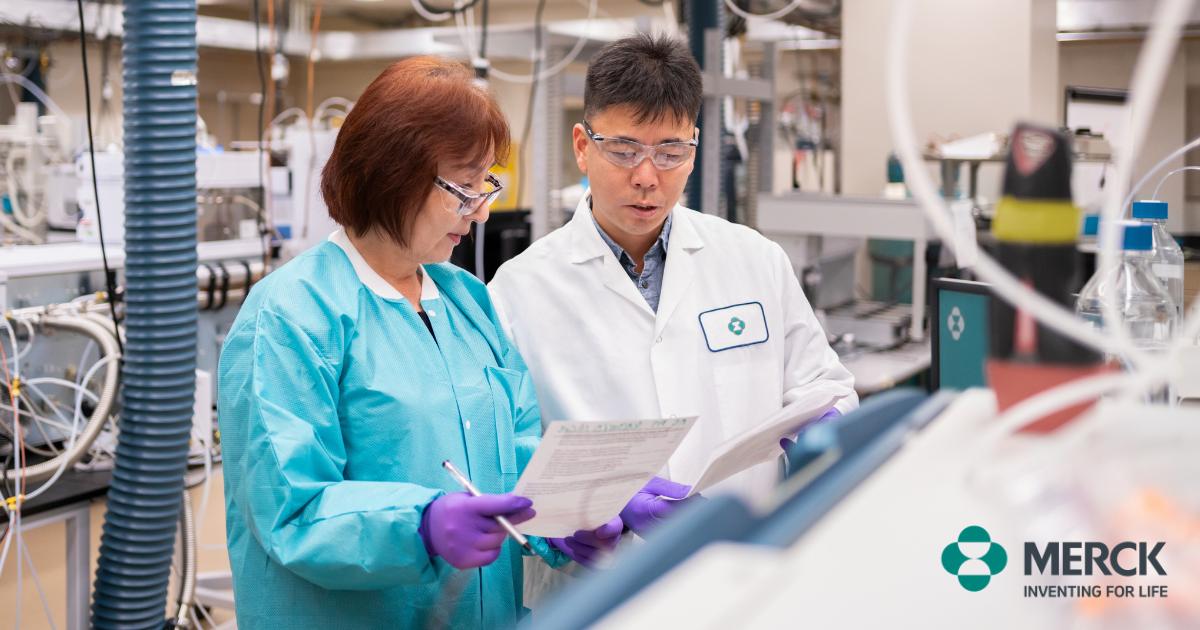
An industrial engineer is responsible for creating and implementing processes that optimize resource utilization and eliminate waste. These engineers work in various industries to design processes that benefit their companies in a variety of ways. They review production schedules, design specifications and workflows in order to make the company's processes more efficient. Additionally, industrial engineers help to improve the profitability of production processes. They also help in improving the overall quality of products and services.
Industrial engineers need to be employed
A key role for an industrial engineer is to use innovative design systems and streamline production processes in order to provide streamlined operations for natural and organic food industry. The Industrial Engineer works closely with customers to develop innovative solutions and lead dynamic projects to improve the manufacturing industry. To qualify for this job, an individual must be qualified and able to perform all essential duties satisfactorily. Industrial engineers should be familiar with AutoCAD, Pro-E and must have a good understanding of advanced product quality planning as well as the approval and approval processes for parts.
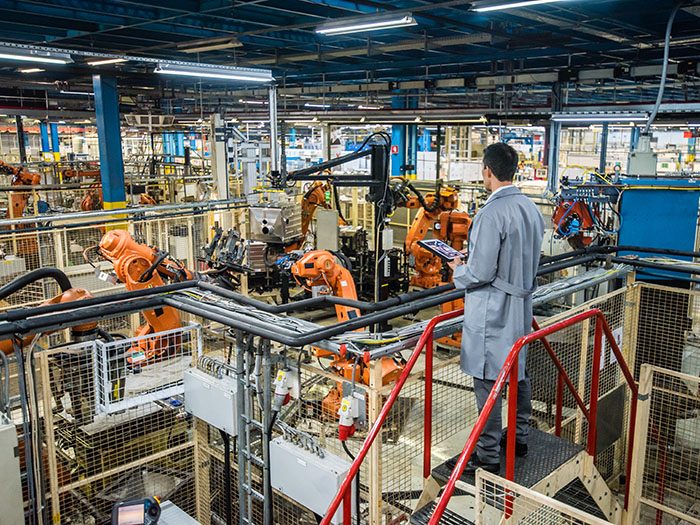
Industrial Engineers focus on the development and testing of integrated systems that maximize efficiency. This job is not limited to this. It also includes studying human work factors to increase product quality and efficiency. Other responsibilities include logistics and cost analysis as well as guest coordination. The person must also be skilled in advanced technical skills, such Microsoft Office. You will also need experience in logistics, manufacturing, and systems design. It is essential that you have the technical skills required to perform well in Orlando.
Industrial engineer's salary
Consider the salary range for Industrial & Manufacturing Engineers in Orlando, FL. Orlando is a great place to live with an average salary $80 325 per year. This is 6% lower than the national average, and 9% less than the New York average salary. Orlando has a salary range of $64,260- $96,390. The middle 67% earn $85,000 per annum, while the top 10 percent earn $102,000.
Industrial Engineers in Orlando earn between $89,700 and $114,300. The salaries for industrial engineers are like any other career. The following salary figures are for Industrial Engineers with five to ten years' experience. However, those with more experience can expect to earn almost twice the salary as those without. But, pay scales can vary between industrial engineers.
Responsibilities and responsibilities of an industrial engineer
This role will require you to identify the most effective processes and strategies for improving them. It is your responsibility to develop and implement flexible, efficient and effective processes that meet customer requirements and goals. You will be responsible for a wide range of tasks including process improvement, capacity planning and reporting. The Industrial Engineer will also need to assist with cross-functional improvement efforts by carrying out observations and time studies.
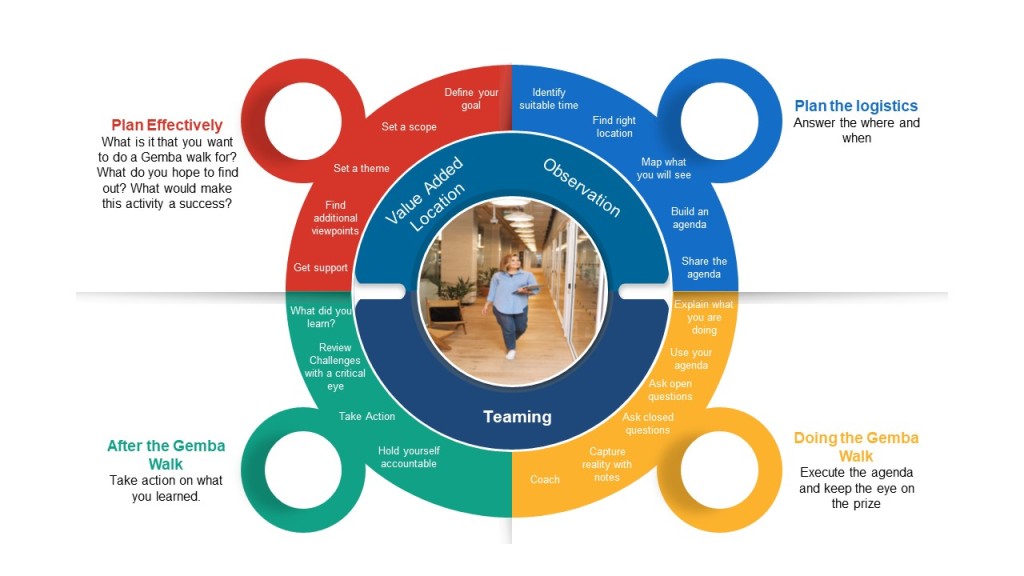
This job requires you to have excellent communication skills and experience as an engineer, as well a solid understanding of statistical analysis. The industrial engineers work closely with the management to create design standards and manage moderately complicated industrial engineering projects. They will analyse data and produce statistical reports to improve quality, process flow, and standard times. They will coordinate key research and produce key metrics reports.
FAQ
What do we need to know about Manufacturing Processes in order to learn more about Logistics?
No. You don't have to know about manufacturing processes before learning about logistics. Understanding the manufacturing process will allow you to better understand logistics.
What is the difference between manufacturing and logistics
Manufacturing is the process of creating goods from raw materials by using machines and processes. Logistics covers all aspects involved in managing supply chains, including procurement and production planning. Logistics and manufacturing are often referred to as one thing. It encompasses both the creation of products and their delivery to customers.
What is the importance of automation in manufacturing?
Not only are service providers and manufacturers important, but so is automation. It allows them to offer services faster and more efficiently. It reduces human errors and improves productivity, which in turn helps them lower their costs.
Can some manufacturing processes be automated?
Yes! Automation has been around since ancient times. The Egyptians discovered the wheel thousands and years ago. Nowadays, we use robots for assembly lines.
There are many applications for robotics in manufacturing today. These include:
-
Automation line robots
-
Robot welding
-
Robot painting
-
Robotics inspection
-
Robots create products
Manufacturing could also benefit from automation in other ways. 3D printing is a way to make custom products quickly and without waiting weeks or months for them to be manufactured.
What are the responsibilities of a production planner
Production planners make sure that every aspect of the project is delivered on-time, within budget, and within schedule. They also ensure the quality of the product and service meets the client's requirements.
What skills does a production planner need?
Production planners must be flexible, organized, and able handle multiple tasks. Also, you must be able and willing to communicate with clients and coworkers.
What does it take for a logistics enterprise to succeed?
To be a successful businessman in logistics, you will need many skills and knowledge. You must have good communication skills to interact effectively with your clients and suppliers. You need to understand how to analyze data and draw conclusions from it. You need to be able work under pressure and manage stressful situations. To increase efficiency and creativity, you need to be creative. You need to have strong leadership qualities to motivate team members and direct them towards achieving organizational goals.
To meet tight deadlines, you must also be efficient and organized.
Statistics
- According to the United Nations Industrial Development Organization (UNIDO), China is the top manufacturer worldwide by 2019 output, producing 28.7% of the total global manufacturing output, followed by the United States, Japan, Germany, and India.[52][53] (en.wikipedia.org)
- According to a Statista study, U.S. businesses spent $1.63 trillion on logistics in 2019, moving goods from origin to end user through various supply chain network segments. (netsuite.com)
- In the United States, for example, manufacturing makes up 15% of the economic output. (twi-global.com)
- [54][55] These are the top 50 countries by the total value of manufacturing output in US dollars for its noted year according to World Bank.[56] (en.wikipedia.org)
- Job #1 is delivering the ordered product according to specifications: color, size, brand, and quantity. (netsuite.com)
External Links
How To
How to use 5S in Manufacturing to Increase Productivity
5S stands for "Sort", "Set In Order", "Standardize", "Separate" and "Store". Toyota Motor Corporation created the 5S methodology in 1954. It helps companies achieve higher levels of efficiency by improving their work environment.
This approach aims to standardize production procedures, making them predictable, repeatable, and easily measurable. This means that tasks such as cleaning, sorting, storing, packing, and labeling are performed daily. This knowledge allows workers to be more efficient in their work because they are aware of what to expect.
There are five steps to implementing 5S, including Sort, Set In Order, Standardize, Separate and Store. Each step requires a different action to increase efficiency. You can make it easy for people to find things later by sorting them. When items are ordered, they are put together. Once you have separated your inventory into groups and organized them, you will store these groups in easily accessible containers. Finally, label all containers correctly.
This requires employees to critically evaluate how they work. Employees need to be able understand their motivations and discover alternative ways to do them. They must learn new skills and techniques in order to implement the 5S system.
The 5S method increases efficiency and morale among employees. Once they start to notice improvements, they are motivated to keep working towards their goal of increasing efficiency.