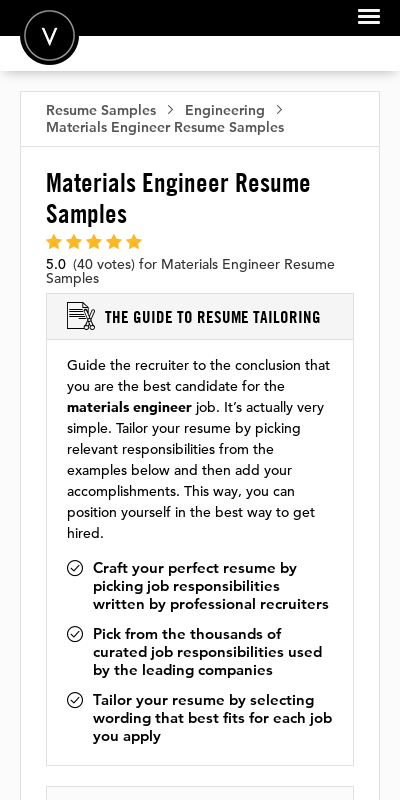
Robotics specialists are employed by both robotics suppliers as well as robot manufacturers. They are responsible for the maintenance and repair of equipment used to build and operate robotic systems. A degree is required as well as practical experience. A robotics technician salary can vary considerably depending on the level of education and experience.
Robotics technicians typically earn an associate's degree in a relevant field. This could be in electronics, mathematics or mechanical engineering. Typically, the degree will provide the student with a good background in science, mathematics, and computer programming. After the program is completed, a robotics technician will join a team of professionals to design, test, maintain, and repair robotic systems.
These systems are used in almost every aspect of our lives. Robots are used across many industries. A robot can gather information for soldiers, such as landmines, in the military. Mechatronics is an engineering discipline that combines electrical, mechanical, and computer engineering.
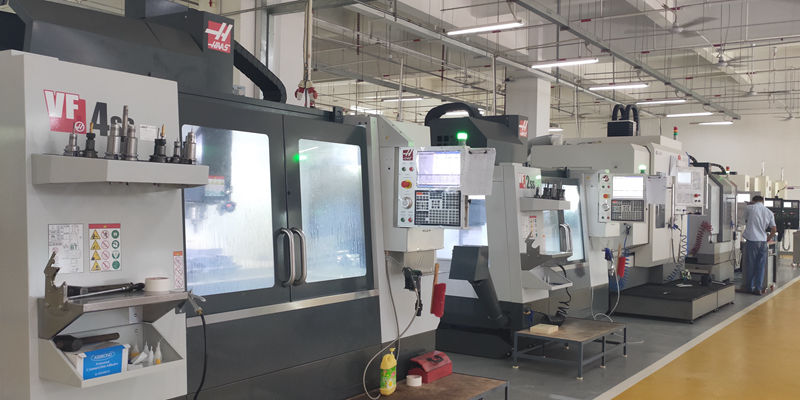
There are many colleges and universities in the United States that offer robotics technician programs. There are also opportunities for students to work directly with companies that hire robotics techs. One must be an enthusiastic problem solver and have a good understanding of math and science in order to become a successful operator. Employers generally require that applicants have a highschool diploma.
The salary for a robotics technician may not be very high, but it requires a great deal of education. A two-year associate degree in robotics technology is the norm for robotics technicians. You may be required to complete additional training, but most employers will provide on-the job training.
Depending on the industry, robotics technicians can be expected to work in shifts, primarily around the clock. Robotics technicians are responsible to program robots to do specific tasks. Operators must diagnose the root cause of malfunctioning robots and then repair them. Additionally, operators will need to work nights and weekends.
Robotics technicians typically earn between $44,175 and $84,520. Atlanta, GA is the most desirable city for Robotics Technicians. Because it offers the best quality life, this is why. The average salary for Robotics Technicians is $1,841 per paycheck.
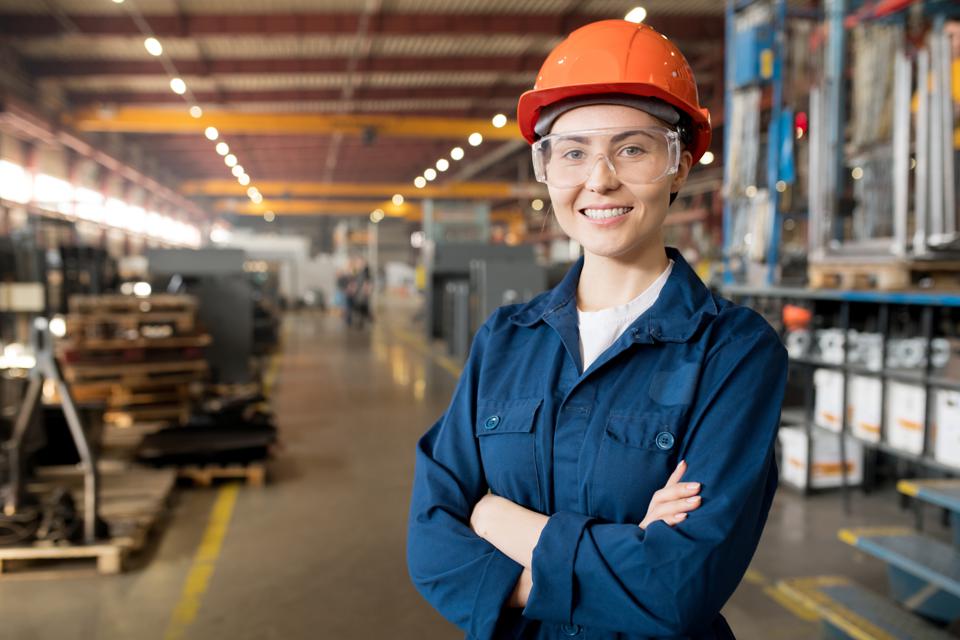
Atlanta also offers a lower tax rate for robotics technicians. In Georgia, robotics technicians pay 6% in taxes in 2018. This is more than the national average. Atlanta has a lower cost of living than many other cities. This makes it a great spot to settle.
Robotics technicians make a great choice for those looking to make a real difference in the world. Robotics technicians can earn high salaries as they are experts in their field. These people can use their skills and knowledge to make the workplace and the world safer.
FAQ
What skills are required to be a production manager?
To become a successful production planner, you need to be organized, flexible, and able to multitask. Effective communication with clients and colleagues is essential.
What are the responsibilities of a production planner
Production planners ensure that all project aspects are completed on time, within budget and within the scope. They also ensure the quality of the product and service meets the client's requirements.
How can manufacturing avoid production bottlenecks
The key to avoiding bottlenecks in production is to keep all processes running smoothly throughout the entire production cycle, from the time you receive an order until the time when the product ships.
This includes planning for both capacity requirements and quality control measures.
The best way to do this is to use continuous improvement techniques such as Six Sigma.
Six Sigma management is a system that improves quality and reduces waste within your organization.
It is focused on creating consistency and eliminating variation in your work.
Statistics
- According to the United Nations Industrial Development Organization (UNIDO), China is the top manufacturer worldwide by 2019 output, producing 28.7% of the total global manufacturing output, followed by the United States, Japan, Germany, and India.[52][53] (en.wikipedia.org)
- In 2021, an estimated 12.1 million Americans work in the manufacturing sector.6 (investopedia.com)
- Many factories witnessed a 30% increase in output due to the shift to electric motors. (en.wikipedia.org)
- According to a Statista study, U.S. businesses spent $1.63 trillion on logistics in 2019, moving goods from origin to end user through various supply chain network segments. (netsuite.com)
- It's estimated that 10.8% of the U.S. GDP in 2020 was contributed to manufacturing. (investopedia.com)
External Links
How To
How to Use lean manufacturing in the Production of Goods
Lean manufacturing (or lean manufacturing) is a style of management that aims to increase efficiency, reduce waste and improve performance through continuous improvement. It was developed in Japan during the 1970s and 1980s by Taiichi Ohno, who received the Toyota Production System (TPS) award from TPS founder Kanji Toyoda. Michael L. Watkins published the "The Machine That Changed the World", the first book about lean manufacturing. It was published in 1990.
Lean manufacturing is often described as a set if principles that help improve the quality and speed of products and services. It emphasizes the elimination of defects and waste throughout the value stream. Lean manufacturing can be described as just-in–time (JIT), total productive maintenance, zero defect (TPM), or even 5S. Lean manufacturing is about eliminating activities that do not add value, such as inspection, rework, and waiting.
Lean manufacturing not only improves product quality but also reduces costs. Companies can also achieve their goals faster by reducing employee turnover. Lean manufacturing is considered one of the most effective ways to manage the entire value chain, including suppliers, customers, distributors, retailers, and employees. Many industries worldwide use lean manufacturing. Toyota's philosophy is the foundation of its success in automotives, electronics and appliances, healthcare, chemical engineers, aerospace, paper and food, among other industries.
Lean manufacturing is based on five principles:
-
Define Value: Identify the social value of your business and what sets you apart.
-
Reduce waste - Stop any activity that isn't adding value to the supply chains.
-
Create Flow. Ensure that your work is uninterrupted and flows seamlessly.
-
Standardize & Simplify - Make processes as consistent and repeatable as possible.
-
Building Relationships – Establish personal relationships with both external and internal stakeholders.
Lean manufacturing isn’t new, but it has seen a renewed interest since 2008 due to the global financial crisis. Many businesses have adopted lean production techniques to make them more competitive. In fact, some economists believe that lean manufacturing will be an important factor in economic recovery.
Lean manufacturing has many benefits in the automotive sector. These include higher customer satisfaction, lower inventory levels, lower operating expenses, greater productivity, and improved overall safety.
Any aspect of an enterprise can benefit from Lean manufacturing. Because it makes sure that all value chains are efficient and effectively managed, Lean Manufacturing is particularly helpful for organizations.
There are three main types in lean manufacturing
-
Just-in Time Manufacturing (JIT), also known as "pull system": This form of lean manufacturing is often referred to simply as "pull". JIT is a method in which components are assembled right at the moment of use, rather than being manufactured ahead of time. This approach aims to reduce lead times, increase the availability of parts, and reduce inventory.
-
Zero Defects Manufacturing (ZDM),: ZDM is a system that ensures no defective units are left the manufacturing facility. If a part needs to be fixed during the assembly line, it should be repaired rather than scrapped. This is also true for finished products that require minor repairs before shipping.
-
Continuous Improvement: Continuous Improvement aims to improve efficiency by continually identifying problems and making adjustments to eliminate or minimize waste. Continuous Improvement (CI) involves continuous improvement in processes, people, tools, and infrastructure.