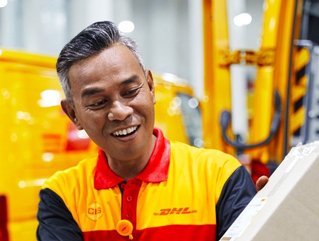
Demand management is a technique used to ensure that a company meets the demands of its customers. It is essentially bridging the gap between supply and marketing by allowing organizations to predict demand. This can be used to increase the speed and accuracy of delivery, reduce disputes over invoices, and lower the costs of running a business.
Companies that have developed a mature demand management process tend to be more responsive to market changes. This is due to the fact that they have a system in which to identify the ideal buyer, which can be used to make marketing more effective.
Demand management can help businesses plan for future demand, and improve customer satisfaction. When done correctly, it can help organizations reduce the number of invoice disputes and improve asset utilization. A solid demand management strategy is a good way to improve operational flexibility.
A project management program can improve the demand management approach. Such software allows teams to collaborate and prevent silos. Also, a change management plan can help companies course correct supply chain problems quickly.
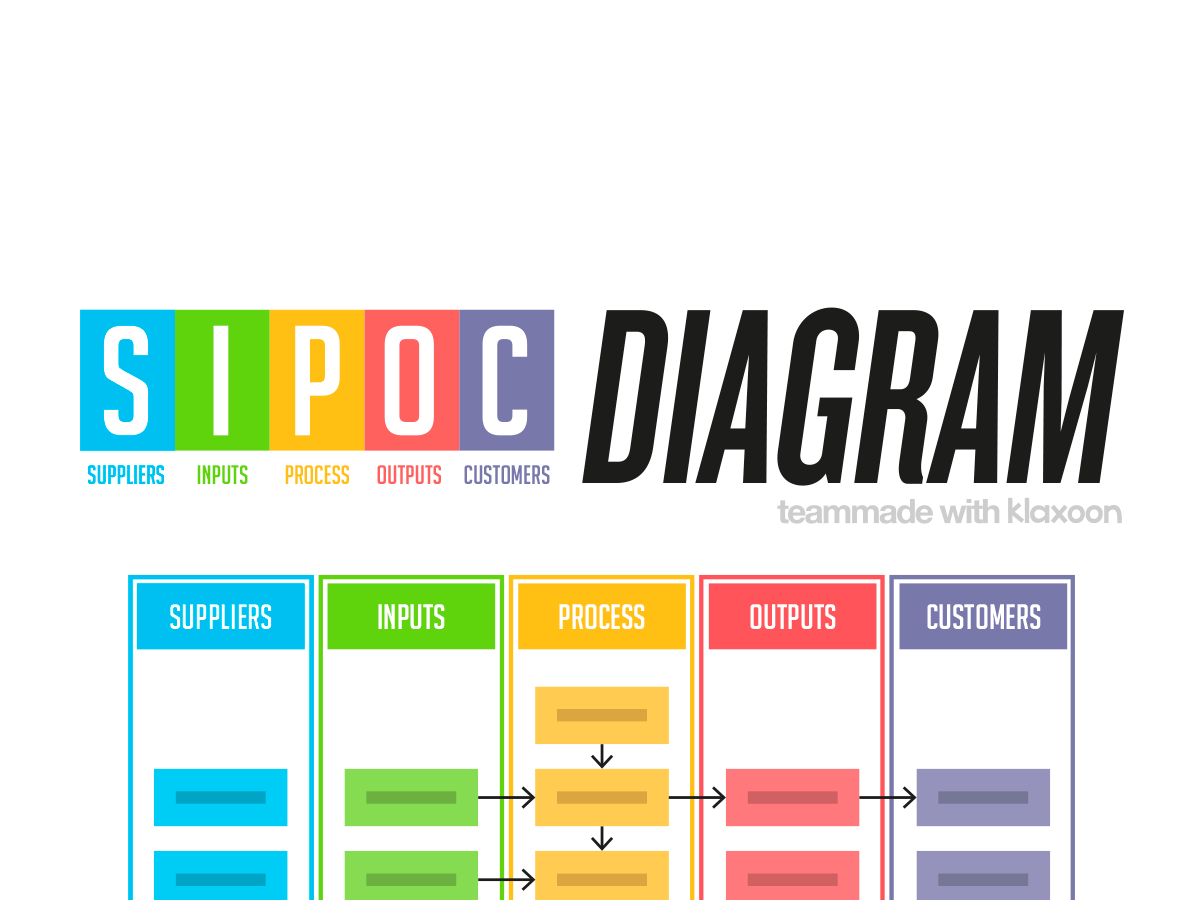
ILOG's PowerOps Suite combines manufacturing scheduling functions. Similarly, QAD and Dynasys offer applications that allow organizations to create a demand and supply plan. These applications are useful for helping organizations see the effect of changes on their supply chains. Optiant also offers ERP solutions that enable organizations to create efficient, consistent and effective order and supply management processes.
Tools such as CDC Software, Terra Technology, and Real-Time Inventory provide real-time forecasting solutions which can help reduce supply chain disruptions. Companies can also benefit from the collaborative management strategy which allows them to share information. It can include performance indicators and knowledge sharing.
It is important to take into account a few things before you start to implement a demand-management strategy. These factors will help professionals understand the process better and keep their focus on the most important elements.
Leadership buy-in is a critical factor in demand management. Demand management is a collaborative process that requires input from all levels of management. High-ranking executives and managers are responsible in ensuring everyone is on the right page. It is important that the initiative succeeds at all levels.
There are many applications available that can assist organizations in implementing a demand/supply planning. However, these key points should be kept in mind.
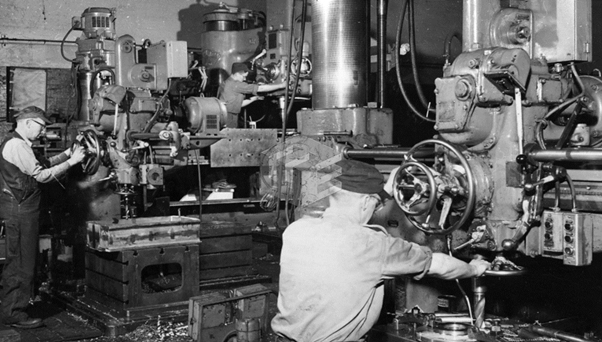
It is crucial to understand the market and identify the ideal customer. It is important that the company can effectively measure and analyze its success.
As businesses look to become more nimble, they must develop a demand management strategy that can be easily altered to accommodate change. A well-designed plan will reduce supply chain disruptions and tactical forecast errors. Demand management is also a useful tool in the development and implementation of portfolio and strategic planning.
FAQ
How can I find out more about manufacturing?
You can learn the most about manufacturing by getting involved in it. But if that is not possible you can always read books and watch educational videos.
What are the jobs in logistics?
There are many kinds of jobs available within logistics. Here are some examples:
-
Warehouse workers - They load trucks and pallets.
-
Transportation drivers - They drive trucks and trailers to deliver goods and carry out pick-ups.
-
Freight handlers – They sort and package freight at warehouses.
-
Inventory managers - These are responsible for overseeing the stock of goods in warehouses.
-
Sales representatives - They sell products.
-
Logistics coordinators – They plan and coordinate logistics operations.
-
Purchasing agents - They buy goods and services that are necessary for company operations.
-
Customer service agents - They answer phone calls and respond to emails.
-
Shippers clerks - They process shipping order and issue bills.
-
Order fillers – They fill orders based upon what was ordered and shipped.
-
Quality control inspectors – They inspect incoming and outgoing products to ensure that there are no defects.
-
Other - Logistics has many other job opportunities, including transportation supervisors, logistics specialists, and cargo specialists.
What are the 7 Rs of logistics?
The acronym 7R's for Logistics stands to represent the seven basic principles in logistics management. It was published in 2004 by the International Association of Business Logisticians as part of their "Seven Principles of Logistics Management" series.
The acronym is made up of the following letters:
-
Responsible – ensure that all actions are legal and don't cause harm to anyone else.
-
Reliable - Have confidence in your ability to fulfill all of your commitments.
-
It is reasonable to use resources efficiently and not waste them.
-
Realistic – consider all aspects of operations, from cost-effectiveness to environmental impact.
-
Respectful - show respect and treat others fairly and fairly
-
Resourceful - look for opportunities to save money and increase productivity.
-
Recognizable provides value-added products and services to customers
What is the difference in Production Planning and Scheduling, you ask?
Production Planning (PP) refers to the process of determining how much production is needed at any given moment. Forecasting and identifying production capacity are two key elements to this process.
Scheduling is the process of assigning specific dates to tasks so they can be completed within the specified timeframe.
What are the responsibilities of a production planner
Production planners ensure that all project aspects are completed on time, within budget and within the scope. They make sure that the product and services meet client expectations.
What does it mean to be a manufacturer?
Manufacturing Industries are companies that manufacture products. The people who buy these products are called consumers. These companies employ many processes to achieve this purpose, such as production and distribution, retailing, management and so on. These companies produce goods using raw materials and other equipment. This includes all types of manufactured goods, including food items, clothing, building supplies, furniture, toys, electronics, tools, machinery, vehicles, pharmaceuticals, medical devices, chemicals, and many others.
Statistics
- Job #1 is delivering the ordered product according to specifications: color, size, brand, and quantity. (netsuite.com)
- In the United States, for example, manufacturing makes up 15% of the economic output. (twi-global.com)
- According to the United Nations Industrial Development Organization (UNIDO), China is the top manufacturer worldwide by 2019 output, producing 28.7% of the total global manufacturing output, followed by the United States, Japan, Germany, and India.[52][53] (en.wikipedia.org)
- You can multiply the result by 100 to get the total percent of monthly overhead. (investopedia.com)
- It's estimated that 10.8% of the U.S. GDP in 2020 was contributed to manufacturing. (investopedia.com)
External Links
How To
How to Use lean manufacturing in the Production of Goods
Lean manufacturing is an approach to management that aims for efficiency and waste reduction. It was developed by Taiichi Okono in Japan, during the 1970s & 1980s. TPS founder Kanji Takoda awarded him the Toyota Production System Award (TPS). Michael L. Watkins published the first book on lean manufacturing in 1990.
Lean manufacturing refers to a set of principles that improve the quality, speed and costs of products and services. It emphasizes the elimination of defects and waste throughout the value stream. Lean manufacturing can be described as just-in–time (JIT), total productive maintenance, zero defect (TPM), or even 5S. Lean manufacturing seeks to eliminate non-value added activities, such as inspection, work, waiting, and rework.
Lean manufacturing is a way for companies to achieve their goals faster, improve product quality, and lower costs. Lean manufacturing has been deemed one of the best ways to manage the entire value-chain, including customers, distributors as well retailers and employees. Lean manufacturing is widely practiced in many industries around the world. For example, Toyota's philosophy underpins its success in automobiles, electronics, appliances, healthcare, chemical engineering, aerospace, paper, food, etc.
Five basic principles of Lean Manufacturing are included in lean manufacturing
-
Define Value- Identify the added value your company brings to society. What makes you stand out from your competitors?
-
Reduce waste - Get rid of any activity that does not add value to the supply chain.
-
Create Flow: Ensure that the work process flows without interruptions.
-
Standardize and simplify – Make processes as repeatable and consistent as possible.
-
Develop Relationships: Establish personal relationships both with internal and external stakeholders.
Lean manufacturing is not a new concept, but it has been gaining popularity over the last few years due to a renewed interest in the economy following the global financial crisis of 2008. To increase their competitiveness, many businesses have turned to lean manufacturing. Some economists even believe that lean manufacturing can be a key factor in economic recovery.
Lean manufacturing is becoming a popular practice in automotive. It has many advantages. These include improved customer satisfaction, reduced inventory levels, lower operating costs, increased productivity, and better overall safety.
Lean manufacturing can be applied to almost every aspect of an organization. It is especially useful for the production aspect of an organization, as it ensures that every step in the value chain is efficient and effective.
There are three types principally of lean manufacturing:
-
Just-in-Time Manufacturing (JIT): This type of lean manufacturing is commonly referred to as "pull systems." JIT stands for a system where components are assembled on the spot rather than being made in advance. This approach is designed to reduce lead times and increase the availability of components. It also reduces inventory.
-
Zero Defects Manufacturing, (ZDM): ZDM is focused on ensuring that no defective products leave the manufacturing facility. You should repair any part that needs to be repaired during an assembly line. This is also true for finished products that require minor repairs before shipping.
-
Continuous Improvement: Continuous Improvement aims to improve efficiency by continually identifying problems and making adjustments to eliminate or minimize waste. Continuous Improvement involves continuous improvement of processes.