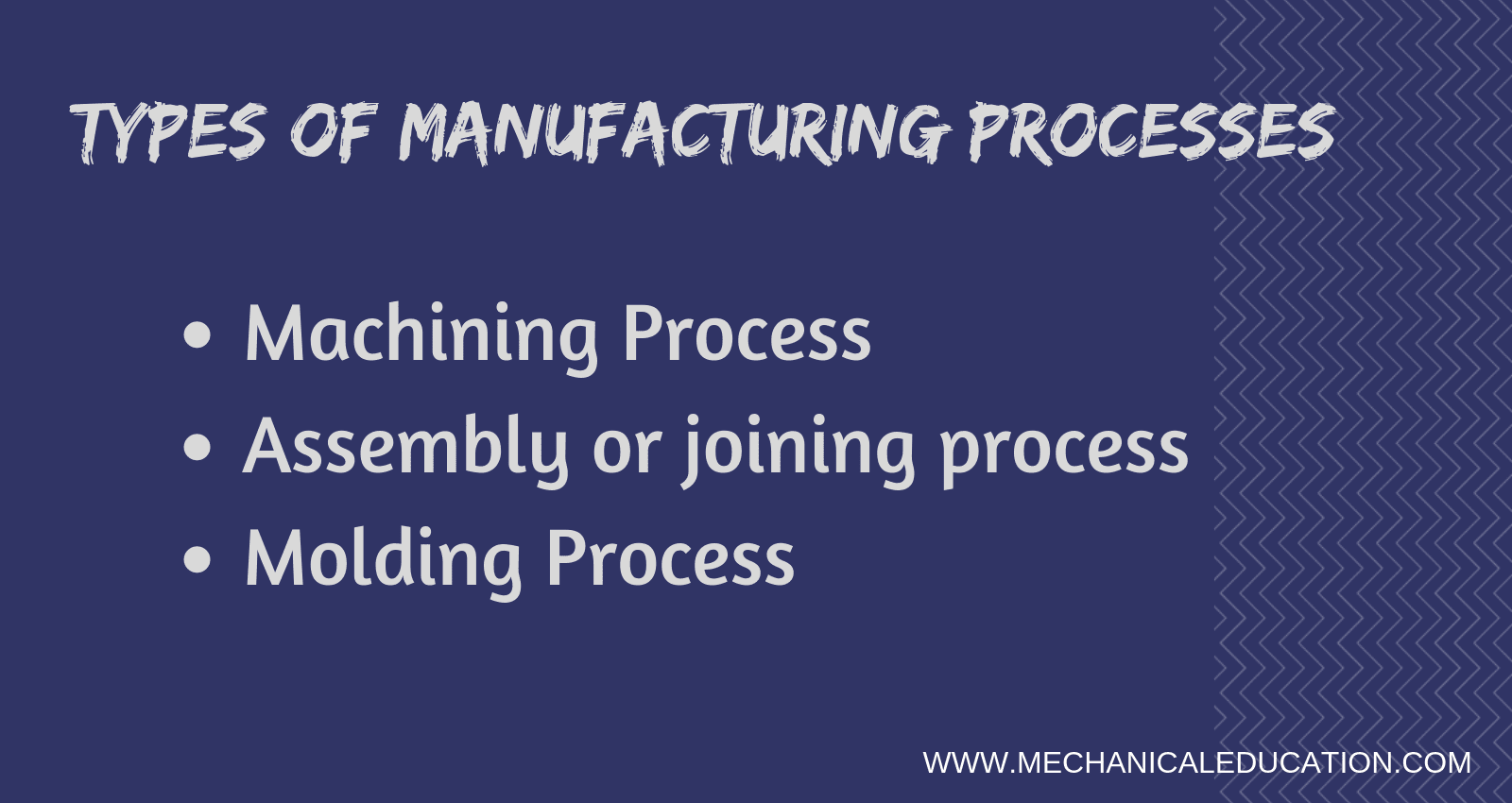
Toyota Production System was originally known as Just in Time production. It is an integrated socio-technical program that eliminates waste and improves processes. It's designed to optimize manufacturing, logistics and customer interaction. It drives continuous improvement as well as employee development. It is also the foundation for Lean Manufacturing. The Toyota Production System is used in many manufacturing facilities across the United States and internationally.
SakichiToyoda, founder of Toyota was the one who developed Toyota Production System. He examined every stage of his company's production process and removed any unneeded parts. This resulted in a 20% decrease in build time. Toyota could also produce a vehicle in half of the time as GM. However, Toyota was on the verge of bankruptcy by the early 1950s.
Taiichi Ahno, Toyota's executive, saw the supermarket shelf-stocking process in the late 1940s. He realized that using Just-in-Time methods in vehicle production could save time. He developed the Toyota Production System from 1948 to 1975 with Eiji Toyoda (the president of Toyota).
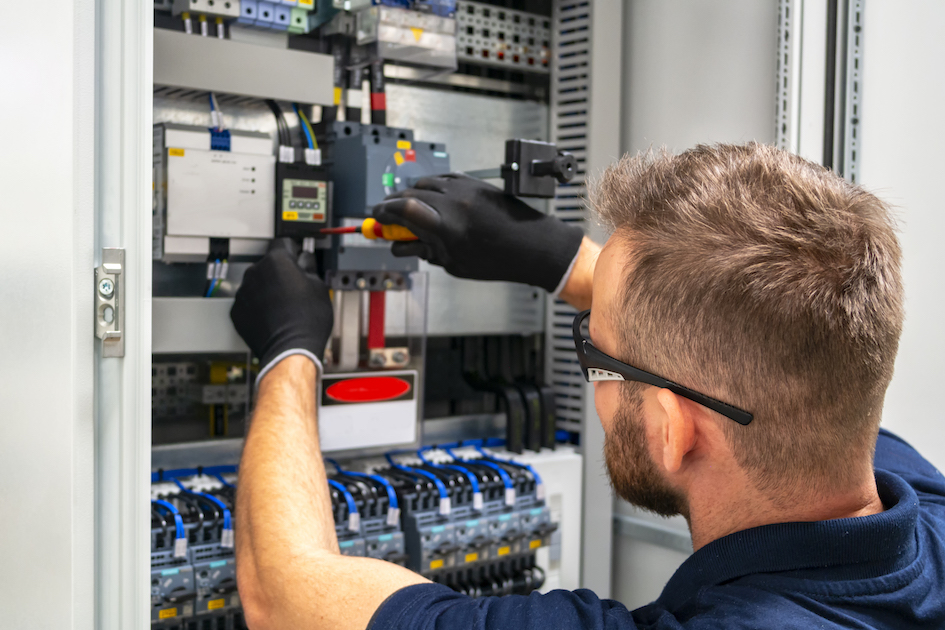
The Toyota Production System was designed to eliminate waste and inconsistency. Kaizen, the Japanese word for continuous improvement, was the underlying philosophy of the Toyota Production System. Toyota Production System continues to be improved in order to meet its customers' needs. It promotes learning and utilizes simple, but powerful, low-tech tools that combine with advanced production techniques. It also employs advanced information technology, as well as unique social/management methods.
The Toyota Production System is built on a set of six core principles. This system has been modified by many companies, including Boeing and Porsche. These companies reengineered processes to emulate Toyota's production system.
Toyota Production System includes activities for team building. These activities include weekly leader safety rounds that evaluate staff's performance with key safety initiatives. Everyone is encouraged to contribute ideas and identify opportunities for improvement. This has changed the culture of the company.
Jidoka is another concept that automates processes with a human touch. Jidoka encourages workers inspect their work and stop production if they find any problems. Jidoka also stresses the importance in building things right from the beginning, and not overlooking problems.
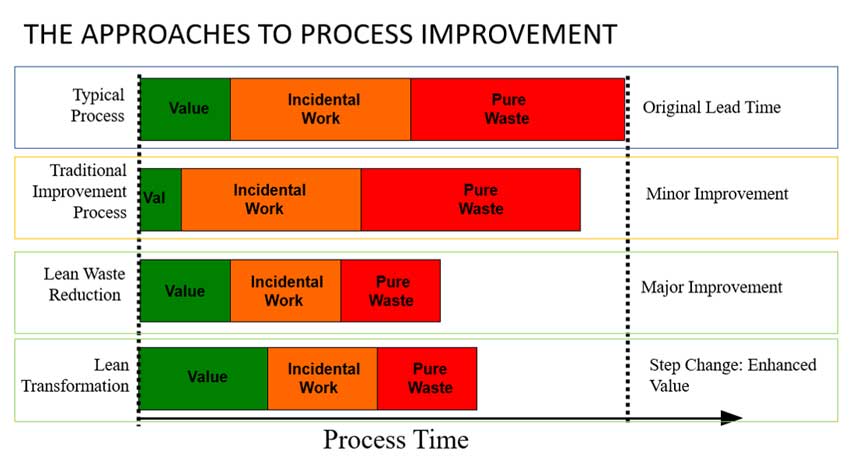
The Toyota Production System also employs visual control. It allows workers to see the instructions clearly on the factory floor. This helps workers follow instructions precisely. The company also uses poka-yoke devices to verify quality standards. These devices can also be used for identifying red rabbits.
Toyota Production System has many applications beyond manufacturing plants. It can also be applied to health care. It can also be used for improving patient satisfaction. It can also be applied to critical care and the operating room.
Using the Toyota Production System, it is possible to improve patient satisfaction and health care delivery. A case study report published in 2003 by the EPA indicates that Toyota's advances in waste reduction caught the EPA's attention. This led to a partnership with several companies, including the St. Bernard Project, which employs military veterans.
FAQ
What are manufacturing & logistics?
Manufacturing refers the process of producing goods from raw materials through machines and processes. Logistics includes all aspects related to supply chain management, such as procurement, distribution planning, inventory control and transportation. Sometimes manufacturing and logistics are combined to refer to a wider term that includes both the process of creating products as well as their delivery to customers.
What kind of jobs are there in logistics?
There are many types of jobs in logistics. Some of them are:
-
Warehouse workers: They load and unload trucks, pallets, and other cargo.
-
Transportation drivers: They drive trucks and trailers and deliver goods and make pick-ups.
-
Freight handlers: They sort and package freight in warehouses.
-
Inventory managers – They manage the inventory in warehouses.
-
Sales reps are people who sell products to customers.
-
Logistics coordinators – They plan and coordinate logistics operations.
-
Purchasing agents: They are responsible for purchasing goods and services to support company operations.
-
Customer service representatives – They answer emails and phone calls from customers.
-
Shipping clerks - They process shipping orders and issue bills.
-
Order fillers: They fill orders based off what has been ordered and shipped.
-
Quality control inspectors are responsible for inspecting incoming and outgoing products looking for defects.
-
Other - Logistics has many other job opportunities, including transportation supervisors, logistics specialists, and cargo specialists.
What is production planning?
Production Planning involves developing a plan for all aspects of the production, including scheduling, budgeting, casting, crew, location, equipment, props, etc. This document aims to ensure that everything is planned and ready when you are ready to shoot. You should also have information to ensure the best possible results on set. This includes location information, crew details, equipment specifications, and casting lists.
It is important to first outline the type of film you would like to make. You may already know where you want the film to be shot, or perhaps you have specific locations and sets you wish to use. Once you've identified the locations and scenes you want to use, you can begin to plan what elements you need for each scene. One example is if you are unsure of the exact model you want but decide that you require a car. You could look online for cars to see what options are available, and then narrow down your choices by selecting between different makes or models.
After you have selected the car you want, you can begin to think about additional features. You might need to have people in the front seats. You might also need someone to help you get around the back. Maybe you want to change the interior color from black to white? These questions can help you decide the right look for your car. Another thing you can do is think about what type of shots are desired. Do you want to film close-ups, or wider angles? Perhaps you want to show the engine or the steering wheel? These things will help you to identify the car that you are looking for.
Once you have established all the details, you can create a schedule. A schedule will tell you when you need to start shooting and when you need to finish. A schedule for each day will detail when you should arrive at the location and when you need leave. Everyone knows exactly what they should do and when. Book extra staff ahead of time if you need them. You don't want to hire someone who won't show up because he didn't know.
Also, consider how many days you will be filming your schedule. Some projects can be completed in a matter of days or weeks. Others may take several days. You should consider whether you will need more than one shot per week when creating your schedule. Multiplying takes in the same area will result both in increased costs and a longer time. If you are unsure if you need multiple takes, it is better to err on the side of caution and shoot fewer takes rather than risk wasting money.
Budget setting is another important aspect in production planning. It is important to set a realistic budget so you can work within your budget. Remember that you can always reduce the budget later on if you run into unforeseen problems. It is important to not overestimate how much you will spend. You will end up spending less money if you underestimate the cost of something.
Production planning can be a complex process. However, once you know how everything works together it will become easier to plan future projects.
Statistics
- Job #1 is delivering the ordered product according to specifications: color, size, brand, and quantity. (netsuite.com)
- In the United States, for example, manufacturing makes up 15% of the economic output. (twi-global.com)
- According to a Statista study, U.S. businesses spent $1.63 trillion on logistics in 2019, moving goods from origin to end user through various supply chain network segments. (netsuite.com)
- According to the United Nations Industrial Development Organization (UNIDO), China is the top manufacturer worldwide by 2019 output, producing 28.7% of the total global manufacturing output, followed by the United States, Japan, Germany, and India.[52][53] (en.wikipedia.org)
- You can multiply the result by 100 to get the total percent of monthly overhead. (investopedia.com)
External Links
How To
How to use the Just In-Time Production Method
Just-in-time is a way to cut costs and increase efficiency in business processes. It allows you to get the right amount resources at the right time. This means that only what you use is charged to your account. Frederick Taylor was the first to coin this term. He developed it while working as a foreman during the early 1900s. He saw how overtime was paid to workers for work that was delayed. He decided that workers would be more productive if they had enough time to complete their work before they started to work.
JIT is an acronym that means you need to plan ahead so you don’t waste your money. The entire project should be looked at from start to finish. You need to ensure you have enough resources to tackle any issues that might arise. If you expect problems to arise, you will be able to provide the necessary equipment and personnel to address them. This way, you won't end up paying extra money for things that weren't really necessary.
There are many JIT methods.
-
Demand-driven: This is a type of JIT where you order the parts/materials needed for your project regularly. This will enable you to keep track of how much material is left after you use it. This will let you know how long it will be to produce more.
-
Inventory-based: This type allows you to stock the materials needed for your projects ahead of time. This allows you to predict how much you can expect to sell.
-
Project-driven: This approach involves setting aside sufficient funds to cover your project's costs. When you know how much you need, you'll purchase the appropriate amount of materials.
-
Resource-based JIT : This is probably the most popular type of JIT. You assign certain resources based off demand. For instance, if you have a lot of orders coming in, you'll assign more people to handle them. If you don't receive many orders, then you'll assign fewer employees to handle the load.
-
Cost-based: This approach is very similar to resource-based. However, you don't just care about the number of people you have; you also need to consider how much each person will cost.
-
Price-based: This is similar to cost-based but instead of looking at individual workers' salaries, you look at the total company price.
-
Material-based: This is very similar to cost-based but instead of looking at total costs of the company you are concerned with how many raw materials you use on an average.
-
Time-based: Another variation of resource-based JIT. Instead of focusing on how much each employee costs, you focus on how long it takes to complete the project.
-
Quality-based JIT: This is another variation of resource based JIT. Instead of focusing on the cost of each worker or how long it takes, think about how high quality your product is.
-
Value-based: This is one of the newest forms of JIT. You don't worry about whether the products work or if they meet customer expectations. Instead, your goal is to add value to the market.
-
Stock-based: This inventory-based approach focuses on how many items are being produced at any one time. It's useful when you want maximum production and minimal inventory.
-
Just-intime planning (JIT), is a combination JIT/sales chain management. It is the process of scheduling components' delivery as soon as they have been ordered. This is important as it reduces lead time and increases throughput.